以特斯拉Model 3為代表的眾多電動(dòng)汽車量產(chǎn)車型成功應(yīng)用SiC MOSFET芯片,表明SiC MOSFET在性能、可靠性和綜合成本層面已得到產(chǎn)業(yè)界的認(rèn)可。基于大量的設(shè)計(jì)優(yōu)化和可靠性驗(yàn)證工作,瑞能半導(dǎo)體于2021年推出SiC MOSFET產(chǎn)品,不僅一如既往的追求高可靠性,同時(shí)也擁有業(yè)內(nèi)領(lǐng)先的高性能和競(jìng)爭(zhēng)力。
作者:瑞能半導(dǎo)體科技股份有限公司 崔京京
引言
近年內(nèi),碳化硅功率器件已逐漸成為高壓、高頻及高效率應(yīng)用場(chǎng)合需求的首選。性能、可靠性和成本是決定功率器件商業(yè)化進(jìn)程的三個(gè)重要維度,此三者一般互為矛盾關(guān)系。但回顧SiC MOSFET器件的技術(shù)發(fā)展歷程可以發(fā)現(xiàn),通過(guò)優(yōu)化制造工藝和器件設(shè)計(jì),不僅帶來(lái)性能和可靠性的提升,也降低了單顆芯片成本,技術(shù)發(fā)展成為推動(dòng)SiC MOSFET商業(yè)化進(jìn)程的重要源動(dòng)力。
自2011年商業(yè)化產(chǎn)品推出以來(lái),SiC MOSFET目前已完成三次技術(shù)迭代,圖1為三代SiC MOSFET的主要技術(shù)特點(diǎn)。圖中的比導(dǎo)通電阻值(Ron,sp)是評(píng)價(jià)單極型功率器件性能的重要指標(biāo),其物理意義為器件導(dǎo)通電阻乘以芯片有源區(qū)(有效導(dǎo)通區(qū)域)面積,數(shù)值越小表示技術(shù)水平越高,即相同導(dǎo)通電阻值產(chǎn)品所需的芯片面積越小。可以看到,基于工藝的進(jìn)步和設(shè)計(jì)的優(yōu)化,SiC MOSFET性能逐代提升,單位導(dǎo)通電阻值需要的芯片面積越來(lái)越小。
圖1:三代SiC MOSFET產(chǎn)品主要技術(shù)特點(diǎn)
新制造工藝開發(fā)
1. 柵氧氮化工藝
相比同為第三代半導(dǎo)體的GaN材料,SiC具有和Si一樣能與O2反應(yīng)生成理想介質(zhì)層SiO2的天然優(yōu)勢(shì),但是SiC中C原子的存在使得其MOS結(jié)構(gòu)的柵氧界面(SiO2/SiC)比傳統(tǒng)的Si基柵氧界面(SiO2/Si)高近三個(gè)數(shù)量級(jí)的界面態(tài)密度,導(dǎo)致SiC MOS結(jié)構(gòu)的溝道遷移率遠(yuǎn)遠(yuǎn)低于Si MOS結(jié)構(gòu),溝道電阻成為SiC MOSFET的主要電阻。
經(jīng)過(guò)多年研究,通過(guò)在氧化工藝后加入氮化工藝(NO或N2O退火工藝),溝道遷移率由10cm2/(V·s)以下增加到20cm2/(V·s)左右,溝道電阻減少50%以上,界面陷阱引起的閾值電壓漂移問(wèn)題也得到改善。SiC柵氧氮化工藝的成功開發(fā)同時(shí)顯著提升了SiC MOSFET的器件性能和產(chǎn)品可靠性,是SiC MOSFET產(chǎn)品走向成熟商業(yè)化的基礎(chǔ)。
2.溝道自對(duì)準(zhǔn)工藝
即使經(jīng)過(guò)氮化工藝,進(jìn)一步減少SiC MOSFET溝道電阻仍然是設(shè)計(jì)者的工作目標(biāo),減少溝道長(zhǎng)度是實(shí)現(xiàn)此目標(biāo)的重要手段。但由于無(wú)法像傳統(tǒng)Si MOS結(jié)構(gòu)一樣通過(guò)雙重?cái)U(kuò)散工藝形成溝道,SiC MOS結(jié)構(gòu)只能通過(guò)***的二次套刻形成溝道,因此溝道長(zhǎng)度受制于***的套刻精度以及偏差的控制,根據(jù)當(dāng)前功率半導(dǎo)體產(chǎn)線的實(shí)際工藝能力,這意味著溝道長(zhǎng)度往往大于0.8微米。圖2展現(xiàn)了不同溝道長(zhǎng)度對(duì)1200V SiC MOSFET導(dǎo)通性能的影響,0.4微米是理想的溝道長(zhǎng)度設(shè)計(jì),但是當(dāng)溝道長(zhǎng)度等于0.8微米時(shí),器件導(dǎo)通電阻將增加約50%。
圖2:1200V SiC MOSFET溝道長(zhǎng)度 vs. 比導(dǎo)通電阻值
經(jīng)過(guò)大量試驗(yàn)摸索,幾種針對(duì)碳化硅的溝道自對(duì)準(zhǔn)工藝開發(fā)完成,即使在現(xiàn)有的***能力下也可實(shí)現(xiàn)0.8微米以下的溝道長(zhǎng)度,SiC MOSFET比導(dǎo)通電阻值因此得到進(jìn)一步顯著降低。圖3說(shuō)明了瑞能SiC MOSFET由于采用溝道自對(duì)準(zhǔn)工藝帶來(lái)的性能優(yōu)勢(shì)。與柵氧界面氮化工藝一樣,碳化硅溝道自對(duì)準(zhǔn)工藝的應(yīng)用并未明顯增加工藝制造成本,但都顯著改善了器件的性能,極大提高了SiC MOSFET產(chǎn)品的競(jìng)爭(zhēng)力。
圖3:采用溝道自對(duì)準(zhǔn)工藝(Self-Aligned)與非自對(duì)準(zhǔn)工藝(Non-Self-Aligned)產(chǎn)品性能對(duì)比
芯片設(shè)計(jì)優(yōu)化
1.元胞尺寸縮小
對(duì)于平面型SiC MOSFET,減小元胞尺寸(Cell Pitch)是提升器件導(dǎo)通能力的主要方法。圖4為平面柵MOSFET結(jié)構(gòu)的關(guān)鍵設(shè)計(jì)參數(shù),其中JFET區(qū)寬度(WJFET)和源極接觸區(qū)寬度(LP++LNC)是主要的設(shè)計(jì)優(yōu)化對(duì)象。JFET區(qū)寬度越大,該區(qū)域“夾斷”電流的JFET電阻越小,但中間位置柵極氧化層承受的電場(chǎng)強(qiáng)度越大。所以從減小元胞尺寸和提升氧化層可靠性兩個(gè)方面來(lái)考量,都需要盡量減小JFET區(qū)寬度。然而JFET區(qū)寬度減小會(huì)增加JFET電阻,當(dāng)JFET區(qū)寬度小于臨界值時(shí),JFET電阻以及總導(dǎo)通電阻會(huì)顯著增加。
圖4:平面柵MOSFET結(jié)構(gòu)關(guān)鍵設(shè)計(jì)參數(shù)(半元胞)
如圖5所示,通過(guò)設(shè)計(jì)額外的JFET區(qū)N型離子注入工藝或高濃度外延工藝形成電流擴(kuò)展層(CSL),JFET區(qū)寬度可進(jìn)一步減小20%以上,器件比導(dǎo)通電阻值降低了15%,同時(shí)還可減小JFET區(qū)中間位置柵極氧化層承受的電場(chǎng)強(qiáng)度,電流擴(kuò)展層成為縮小元胞尺寸并提升SiC MOSFET性能的關(guān)鍵設(shè)計(jì)。
圖5:JFET區(qū)寬度與器件性能及可靠性的關(guān)系. (a) 無(wú)CSL設(shè)計(jì), (b) 有CSL設(shè)計(jì)
源極區(qū)寬度(LP++LNC)的設(shè)計(jì)主要取決于N+區(qū)和P+區(qū)的歐姆接觸電阻率,即意味著芯片設(shè)計(jì)需要基于實(shí)際的工藝能力。如只有當(dāng)N型歐姆接觸電阻率低于1E-4mOhm·cm2時(shí),才可以設(shè)計(jì)低于0.6微米的N+源極區(qū)接觸寬度而不增加器件導(dǎo)通電阻。
2.溝槽柵結(jié)構(gòu)
對(duì)于Si IGBT或者Si MOSFET,溝槽柵結(jié)構(gòu)的設(shè)計(jì)相比于平面柵結(jié)構(gòu)具有明顯的性能優(yōu)勢(shì),但是對(duì)于SiC MOSFET來(lái)說(shuō),目前這種優(yōu)勢(shì)不再顯著。根據(jù)高斯定理,SiC MOSFET中柵極SiO2表面承受的電場(chǎng)強(qiáng)度約是其對(duì)應(yīng)的SiC表面電場(chǎng)強(qiáng)度的2.5倍,由于碳化硅材料以高臨界擊穿電場(chǎng)強(qiáng)度著稱(約為硅材料的10倍),所以SiC MOSFET中柵極SiO2承受的電場(chǎng)強(qiáng)度極高,比Si MOSFET/IGBT中柵極SiO2承受的電場(chǎng)強(qiáng)度高一個(gè)數(shù)量級(jí)。因此,SiC MOSFET 柵極氧化層的可靠性面臨嚴(yán)重的挑戰(zhàn)。溝槽柵SiC MOSFET設(shè)計(jì)中的柵氧可靠性問(wèn)題更加嚴(yán)重,因?yàn)榻咏?0°的溝槽柵拐角進(jìn)一步加劇了電力線的集中,此處的柵氧層極易被擊穿。
解決柵極氧化層可靠性問(wèn)題是目前所有的溝槽柵SiC MOSFET結(jié)構(gòu)設(shè)計(jì)必須首先解決的問(wèn)題,已有技術(shù)路線是設(shè)計(jì)額外的JFET區(qū),通過(guò)其耗盡區(qū)的“夾斷”來(lái)屏蔽保護(hù)中間的柵極氧化層,減少溝槽柵拐角位置氧化層承受的電應(yīng)力,但這同時(shí)也引入了很大的JFET電阻,導(dǎo)通電阻因此顯著增加。
圖6比較了瑞能平面型SiC MOSFET以及兩款市場(chǎng)上主流的平面型和溝槽型SiC MOSFET的主要性能,通過(guò)比較可以發(fā)現(xiàn),現(xiàn)階段的溝槽型SiC MOSFET與高性能的平面型SiC MOSFET相比,性能優(yōu)勢(shì)并不明顯。反而平面型SiC MOSFET由于具備天然的可靠性優(yōu)勢(shì),更容易被市場(chǎng)認(rèn)可。當(dāng)然,如果未來(lái)柵極介質(zhì)層的可靠性問(wèn)題得到徹底解決,更緊湊的溝槽型SiC MOSFET仍然具有巨大的發(fā)展?jié)摿Α?/p>
圖6:市場(chǎng)主流平面型&溝槽型1200V SiC MOSFET性能對(duì)比(25℃)SiC MOSFET
可靠性優(yōu)化
可靠性問(wèn)題一直是業(yè)內(nèi)關(guān)注的焦點(diǎn),但隨著柵氧工藝的日益成熟,時(shí)間相關(guān)的介電擊穿、閾值電壓漂移等問(wèn)題都得到了顯著改善,SiC MOSFET可靠性也早已達(dá)到車規(guī)級(jí)應(yīng)用標(biāo)準(zhǔn),自2017年Model 3量產(chǎn)以來(lái),SiC MOSFET已在幾十萬(wàn)輛電動(dòng)汽車主驅(qū)上安全使用了4年時(shí)間。
瑞能在產(chǎn)品設(shè)計(jì)之初就將可靠性放在首位,最新推出的碳化硅MOSFET系列產(chǎn)品,通過(guò)采用平面柵結(jié)構(gòu)、高閾值電壓、高阻斷電壓以及高柵氧層耐壓能力的設(shè)計(jì),確保了器件在長(zhǎng)期的動(dòng)靜態(tài)工況中具有更強(qiáng)的魯棒性。圖7為瑞能SiC MOSFET WNSCM80120R產(chǎn)品在HTRB(175℃)各個(gè)試驗(yàn)階段的BVDSS數(shù)據(jù),其BV數(shù)據(jù)在1000H試驗(yàn)中未發(fā)生任何漂移。得益于大量的工藝和設(shè)計(jì)優(yōu)化工作,使得器件性能上有足夠多的設(shè)計(jì)裕量,確保產(chǎn)品高可靠性的同時(shí)仍然擁有高性能表現(xiàn)。
圖7:瑞能1200V SiC MOSFET產(chǎn)品可靠性表現(xiàn)
驅(qū)動(dòng)優(yōu)化
現(xiàn)階段SiC MOSFET的主要替代對(duì)象是Si IGBT和Si MOSFET器件,傳統(tǒng)驅(qū)動(dòng)電壓一般為+15V或+12V左右。如前文所述,由于SiC MOSFET的溝道遷移率相對(duì)較低,需要通過(guò)增加柵極驅(qū)動(dòng)電壓來(lái)增強(qiáng)溝道的通流能力,因此目前市場(chǎng)上大部分SiC MOSFET產(chǎn)品一般需要+20V的驅(qū)動(dòng)工作電壓。瑞能1200V SiC MOSFET可以在+18V驅(qū)動(dòng)電壓下高效工作,而即將推出的瑞能1700V1000mOhm SiC MOSFET則可以使用+15V作為驅(qū)動(dòng)工作電壓,實(shí)現(xiàn)與傳統(tǒng)驅(qū)動(dòng)電路的完美兼容。
圖8:瑞能1700V1000mOhm SiC MOSFET輸出特性
小結(jié)
SiC MOSFET技術(shù)的不斷發(fā)展,不僅帶來(lái)產(chǎn)品性能和可靠性的提升,也促進(jìn)了芯片成本的降低,市場(chǎng)規(guī)模因此而快速增加。瑞能半導(dǎo)體始終堅(jiān)持技術(shù)推動(dòng)產(chǎn)品競(jìng)爭(zhēng)力,為客戶提供高性能高可靠性的SiC MOSFET產(chǎn)品。
原文標(biāo)題:高性能高可靠性SiC MOSFET的關(guān)鍵設(shè)計(jì)與優(yōu)化
文章出處:【微信公眾號(hào):瑞能半導(dǎo)體】歡迎添加關(guān)注!文章轉(zhuǎn)載請(qǐng)注明出處。
審核編輯:湯梓紅
-
芯片
+關(guān)注
關(guān)注
459文章
51715瀏覽量
430847 -
MOSFET
+關(guān)注
關(guān)注
148文章
7690瀏覽量
216057 -
SiC
+關(guān)注
關(guān)注
30文章
3028瀏覽量
63665
原文標(biāo)題:高性能高可靠性SiC MOSFET的關(guān)鍵設(shè)計(jì)與優(yōu)化
文章出處:【微信號(hào):weensemi,微信公眾號(hào):瑞能半導(dǎo)體】歡迎添加關(guān)注!文章轉(zhuǎn)載請(qǐng)注明出處。
發(fā)布評(píng)論請(qǐng)先 登錄
相關(guān)推薦
如何測(cè)試SiC MOSFET柵氧可靠性
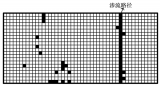
什么是MOSFET柵極氧化層?如何測(cè)試SiC碳化硅MOSFET的柵氧可靠性?
SiC-SBD關(guān)于可靠性試驗(yàn)
SiC-MOSFET的可靠性
【PCB】什么是高可靠性?
什么是高可靠性?
為什么華秋要做高可靠性?
SiC MOSFET FIT率和柵極氧化物可靠性的關(guān)系
碳化硅SiC MOSFET:低導(dǎo)通電阻和高可靠性的肖特基勢(shì)壘二極管
英飛凌推出1200V SiC MOSFET 將提高可靠性和降低系統(tǒng)成本
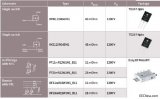
ROHM SiC-MOSFET的可靠性試驗(yàn)
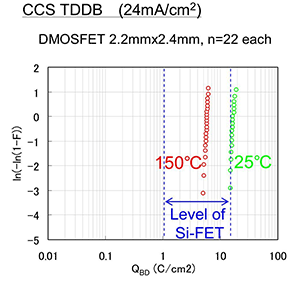
SiC-MOSFET的可靠性
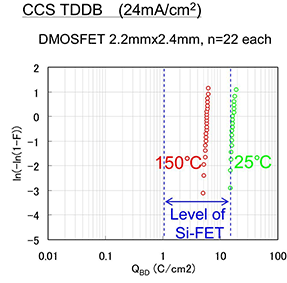
評(píng)論