制作氧化局限面射型雷射與蝕刻空氣柱狀結構一樣都需要先將磊晶片進行蝕刻,以便暴露出側向蝕刻表面(etched sidewall)提供增益波導或折射率波導效果,同時靠近活性層的高鋁含量砷化鋁鎵層也才能與高溫水蒸氣進行氧化反應。制作砷化鎵以及其他材料光電元件時定義元件形貌或個別元件之間的電性隔絕的蝕刻制程稱為mesa etching’mesa在西班牙語中指桌子,或者像桌子一樣的平頂高原,四周有河水侵蝕或因地質活動陷落造成的陡峭懸崖,通常出現在早期移民以西班牙裔為主的美國西南地區例如大峽谷等知名景點,下圖5-10即為美國猶他州峽谷地國家公園的mesa景觀。
進行mesa etching通常有兩種選擇,早期選用酸性溶液進行化學濕式蝕刻(chemicalwet etching),通常用來蝕刻砷化鎵相關材料的蝕刻液為硫酸或磷酸混合雙氧水及水稀釋后的溶液,磊晶層表面會有光阻定義不易被酸性溶液侵蝕的SiO2作為蝕刻保護層,在浸泡蝕刻溶液特定時間后,未受保護的區域就會被溶液蝕刻掉,留下未受蝕刻的區域供后續制作元件所需。采用化學濕式蝕刻通常會遭遇到一個嚴重的問題,由于化學反應速率與構成磊晶層的材料在不同晶格方向有顯著差異,因此經常在與磊晶面平行方向造成非等向性蝕刻(anisotropic etching),讓原本設計為圓形或者方形的圖案在蝕刻后變成接近圓角方形。同時在垂直磊晶面方向因為等向性蝕刻而造成底切(undercut)現象,讓蝕刻側壁呈現大幅度的傾斜,且剩余未被蝕刻的尺寸小于原先設計,這兩個現象都會造成蝕刻結果與光罩設計的元件圖案不一致的結果,造成后續制程例如金屬化對準的問題。
由于濕式蝕刻之蝕刻選擇比與垂直方向非等向性較差,因此通常無法達到蝕刻側壁垂直的制程需求,如圖5-13所示,從蝕刻后所拍攝的掃瞄式電子顯微鏡(SEM)照片可以觀察到,蝕刻后的mesa邊緣呈現平緩的坡度,而非原本所期望的垂直蝕刻側面,這個結果對于后續氧化制程后要觀察氧化深度造成相當大的困擾,同時要蒸鍍金屬上電極也可能造成短路現象,甚至在后續光阻曝光顯影步驟就會出現問題,因此有必要改采蝕刻選擇性與非等向性較優異的干式蝕刻法。
后來面射型雷射蝕刻制程較常采用的技術轉變為干式蝕刻,通常采用活性離子蝕刻(Reactive Ion Etching, RIE)[20]或感應耦合電漿活性離子蝕刻(Inductively Coupled Plasma-Reactive Ion Etching, ICP-RIE)。典型的RIE蝕刻設備示意圖如下圖5-14所示。
RIE蝕刻設備腔體中一般壓力約為數毫托耳(mTorr)至數百毫托耳,借由射頻電源提供能量將蝕刻反應氣體游離呈電漿狀態,這些電漿具有高度化學活性可以和被蝕刻的牛導體、金屬或介電質材料產生化學反應并形成氣態生成物最后被真空幫浦移除,一般放置樣品的載臺會另外施加偏壓形成電場引導電漿態反應物朝向被蝕刻樣品加速,因此這些電獎粒子通常也會具有動能并因而撞擊被蝕刻物表面,形成非等向性物理性蝕刻,與化學性蝕刻相輔相成,一般均能獲得比傳統化學溶液濕式蝕刻更加垂直的蝕刻側面,同時底切現象也可以顯著改善。利用感應耦合線圈可以進一步提高電漿密度,而且通常ICP-RIE反應腔體壓力較傳統RIE更低,因此粒子的平均自由徑(mean free path)較長,有利于帶電粒子(通常是電子)被加速到較高能量撞擊氣體分子產生電漿的機率,因此采用ICP-RIE進行蝕刻通常可以獲得更快的蝕刻速率和蝕刻選擇比,典型的ICP-RIE蝕刻設備示意圖如下圖5-15所示。
由于進行蝕刻后通常會接著進行高溫選擇性氧化制程,元件表面需要有保護層以免表面氧化造成后續金屬電極制作問題,因此通常會在蝕刻制程進行前鍍上SiO2或SiNx作為蝕刻阻擋層同時也可以在氧化制程中保護元件表面。一般會利用電漿輔助化學氣相沉積(plasma enhanced chemical vapor deposition, PECVD)成長較致密的SiNx以做為蝕刻與后續濕式氧化的表面保護層,典型的鍍膜參數包含溫度控制在300°C,反應腔體壓力500mTorr,微波功率20W,氮氣流量600 scem(standard cubic centimeter per minute,溫度273K一大氣壓下每分鐘流量1立方公分),氨氣流量15 sccm,矽甲烷SiN4(5%)/ N2流量挫制在400 scom。所需的SiNx厚度取決于RIE或ICP-RIE設備與使用之蝕刻反應氣體對于做為蝕刻光罩的SiNx與砷化鎵/砷化鋁鎵DBR之間的蝕刻選擇比,蝕刻選擇比愈高表示SiNx不需要太厚就可以承受下方砷化鎵/砷化鋁鎵DBR被蝕刻到活性層深度的時間:相反的,蝕刻選擇比愈低,則SiNx的厚度就必須愈厚,才能夠應付長時間的蝕刻而不至于尚未達到所需蝕刻深度時上方的蝕刻阻擋層已經消耗殆盡。因此要蝕刻頂部發光(top emission)氧化局限面射型雷射結構時,以850nm發光波長為例,通常需要蝕刻超過4微米深度才能到達活性層,如果所使用的RIE設備對于SiNx和AIGaAS/GaAs材料蝕刻選擇比為1:4,那么用來作為蝕刻阻擋層的SiNx厚度至少要1微米,考量到還需剩下足夠厚度的SiNx作為選擇性氧化制程的表面保護層,實際需要鍍上的SiNx至少應該要1.3微米。若要制作長波長1.3微米的面射型雷射,由于每一層的DBR厚度隨著發光波長等比例增加,因此蝕刻深度至少6微米,要直接一次蝕刻6微米到活性層,則需大約2微米厚度的SiNx做為蝕刻阻擋層。這時候具有較高蝕刻速率與蝕刻選擇比的ICP-RIE必要性就突顯出來了。
成長完成SiNx蝕刻保護層后,就進行標準黃光制程以定義蝕刻圖案,在光阻硬烤后利用活性離子蝕刻設備先蝕刻SiNx,將光罩圖案轉移到SiNx蝕刻保護層上。典型的SiNx蝕刻條件為氬氣(Ar)流量5sccm,SF620sccm,氦氣(He)流量5sccm,壓力50 mTorr,微波功率75W,自偏壓(self-bias)106.7伏特;蝕刻0.8微米SiNx約需時6分30秒,蝕刻2微米SiNx約需時16分鐘,蝕刻速率控制在每分鐘0.125微米/分左右,同時利用蝕刻終點監測(end-point detector)監測蝕刻深度,以確保后續欲蝕刻之砷化鎵材料表面己確實暴露出來。
待SiNx保護層完成蝕刻后,以丙酮加熱去除殘余光阻,隨即以活性離子蝕刻設備進行砷化鎵/砷化鋁鎵分布布拉格反射器之蝕刻制程。典型的AIGaAs/GaAs蝕刻參數為氫氣流量80sccm,氯氣(Cl2)流量2 sccm,氦氣流量15 sccm,壓力10 mTorr,微波功率100W,自偏壓120 Volt,蝕刻1.3微米氧化局限面射型雷射時,為確保緊鄰活性層的高鋁含量氧化層確實暴露出來,蝕刻深度至少需達到6微米,蝕刻時間約為11分鐘;若要制作850nm氧化局限面射型雷射時,蝕刻深度約為4微米,因此蝕刻時間約僅需7分30秒。
利用傳統活性離子蝕刻所形成之蝕刻結果如下圖5-16所示:
在蝕刻完整結構的氧化局限面射型雷射時,由于蝕刻深度相對較深,所需的蝕刻時間也因此延長,早期實驗發現SiNx蝕刻保護層在蝕刻時側壁(sidewall)若不垂直,則容易造成砷化鎵/砷化鋁鎵分布布拉格反射器之蝕刻側壁形成兩段式轉折,可能會對后續選擇性氧化制程及元件壽命造成不良影響,兩段式的蝕刻側面如下圖5-17所示:
研判造成該現象可能的原因如圖5-18所示,一開始SiNx蝕刻保護層側面稍微呈現不垂直的傾斜角度,如下圖5-18(a)所示,在經過一段時間活性離子蝕刻后,SiNx厚度也會逐漸變薄,而原本不完全垂直的邊緣側面也會因為被蝕刻而變的較為傾斜,如圖5-18(b)所示。虛線表示原本的SiNx剖面形狀,此時下方分布布拉格反射器的蝕刻側面還能維持垂直狀態:但是隨著SiNx邊緣愈來愈薄,漸漸的圖案周圍也被蝕刻干凈無法再對下方的砷化鎵/砷化鋁鎵材料提供保護,因此被蝕刻區域的面積就隨之稍微擴大,而活性離子在向下蝕刻砷化鎵/砷化鋁鎵材料時也同時繼續蝕刻SiNx保護層,漸漸的DBR就形成了兩段式的蝕刻側面,而上方一段由于主要是因為SiNx圖案邊緣減薄所造成,因此也會較為傾斜,不像下方那么垂直,這一點也可以由圖5-17中觀察到。
為避免形成兩段式蝕刻側面,可行的解決方法有兩種,其一為干式活性離子蝕刻之后再輔以磷酸一雙氧水或硫酸一雙氧水之蝕刻溶液稍微浸泡進行濕式蝕刻以去除不平整的蝕刻側面,第二個方法為嚴格控制SiNx蝕刻保護層的蝕刻雙程,務必要求一開始蝕刻保護層的蝕刻側面就非常垂直平整,如此即可避免因邊綠減薄效應而造成兩段式蝕刻側壁的不良結果,也因此雖然氫氟酸或其稀釋溶液Buffered oxide etch(BOE)普遍被用來蝕刻SiO2或SiNx,但是因為濕式蝕刻溶液造成等向性蝕刻的undercut會造成圖案邊緣不垂直,所以不適合用在面射型雷射蝕刻保護層上。
若是所使用的RIE蝕刻設備受限于可選用的蝕刻氣體及制程參數無法進一步改善SiNx對AIGaAs/GaAs材料的蝕刻選擇比及蝕刻速率,另一個選擇為改采SiO2作為蝕刻保護層,同時改用感應耦合電漿活性離子蝕刻(ICP-RIE)設備來改善干式蝕刻制程。利用感應耦合電漿活性離子蝕刻可以在更低壓的環境下進行干式蝕刻制程,粒子的平均自由徑(mean free path)較長,有利于帶電粒子(通常是電子)被加速到較高能量撞擊氣體分子產生電漿的機率,因而獲得較快的蝕刻速率,并且可以維持較佳的蝕刻選擇比。如此一來作為蝕刻保護層的介電質材料(SiO2)就無需成長較厚的厚度,通常采用ICP-RIE進行面射型雷射蝕刻制程僅需0.4微米厚度的SiO2即足夠抵擋ICP-RIE進行面射型雷射分布布拉格反射器蝕刻至5微米以上深度,同時蝕刻時間也大幅縮短為兩分鐘以內。此外為了確保SiO2的蝕刻側壁維持垂直平整,避免上述因邊緣減薄效應而造成兩段式蝕刻側壁的不良結果,原本利用BOE化學濕式蝕刻的制程最好也改用ICP-RIE進行干式蝕刻。RIE觸刻SiO2條件為壓力100mTorr,RF功率為100W,蝕刻氣體為CF4及O2,流量分別為40 sccm與5 sccm。加入氧氣有助于清除反應殘余物,避免沉積在蝕刻表面造成不平坦的蝕刻結果。蝕刻完成后去除光阻之SiO2保護層經由SEM觀察結果如下圖5-19所示。
在完成良好的SiO2蝕刻保護層制程后,就可以繼續進行下方分布布拉格反射器之蝕刻。傳統采用活性離子蝕刻設備若缺少BCl3蝕刻氣體,懂采用氯氣Cl2的話對于DBR的主要成分材料砷化鎵/砷化鋁鎵與蝕刻保護層SiNx的蝕刻選擇比較差。若采用ICP-RIE搭配蝕刻效果較佳之BCl3或SiCl4作為主要化學性蝕刻氣體,將可獲得較佳之蝕刻選擇比。典型的ICP-RIE蝕刻GaAS/AIGaAs制程參數為壓力3mTorr,氮氣(N2)流量5sccm,氫氣(Ar)流量10sccm,BCl3流量25sccm。在一開始嘗試ICP-RIE制程條件時,分別將感應耦合電漿功率(ICP power)固定在700W,調整射頻(RF)功率分別為60W、90W、120W和150W,并利用原子力顯微鏡3D-AFM觀察蝕刻表面平坦度,發現在射頻功率為150W時具有最平整的蝕刻結果,如下圖5-21所示:
隨后將RF功率固定為150W,改變感應耦合電漿功率從100W到700W之間進行調整,并將蝕刻后樣品經由原子力顯微鏡觀察蝕刻表面平整度,由結果可以發現,感應耦合電漿功率在700w時,蝕刻樣品具有最平坦之表面,如下圖5-22所示。新式ICP-RIE在壓力1帕(Pa)下可以獲得較干整蝕刻表面,搭配不同的氣體流量參數包括氯氣(Cl2)2 sccm,氬氣(Ar)10sccm,以及四氯化矽(SiCl4)4sccm,基板承載盤溫度控制在110°C,ICP功率設定為200W,RIE功率為10w,同樣可以獲得優異的DBR蝕刻結果。上述的蝕刻制程中所探用的ICP-RIE感應耦合電漿功率及射頻功率之條件,配合腔體壓力及反應氣體、流量等參數,均視所采用的制程設備與樣品尺寸而異,若要進行量產蝕刻制程時需考慮負載效應(loading effect)補償因為待蝕刻物面積增加導致相同反應氣體流量不足以達到小尺寸樣品測試時相同的蝕刻速率與深度。
采用SiO2作為蝕刻保護層,并利用感應耦合電漿活性離子蝕刻法,搭配具高選擇比SiCl4或BCl3蝕刻氣體及制程參數,蝕刻后之面射型雷射元件SEM照片如圖5-23所示,獲得平整垂直的蝕刻側壁有利后續選擇性氧化結果的觀察。
下表5-1列出面射型雷射制程中常見材料干式蝕刻常用的氣體,但是實際應用時并不僅限于這些氣體,通常蝕刻矽相關材料會使用含氟的氣體,蝕刻含鋁材料會使用氯氣及其化合物,其他常使用的惰性氣體如氬氣Ar大多借助其物理性蝕刻能力,而氮氣、氧氣、氫氣、氦氣多作為蝕刻輔助氣體,有的可以提供蝕刻側壁保護,有的可以幫助蝕刻反應生成物盡快被移除(例如氧氣),而氦氣通常被用來冷卻承載盤面的蝕刻樣品。
-
雷射
+關注
關注
0文章
23瀏覽量
10257 -
SiO2
+關注
關注
0文章
22瀏覽量
8538
原文標題:蝕刻
文章出處:【微信號:Semi Connect,微信公眾號:Semi Connect】歡迎添加關注!文章轉載請注明出處。
發布評論請先 登錄
相關推薦
全新的半導體基礎知識
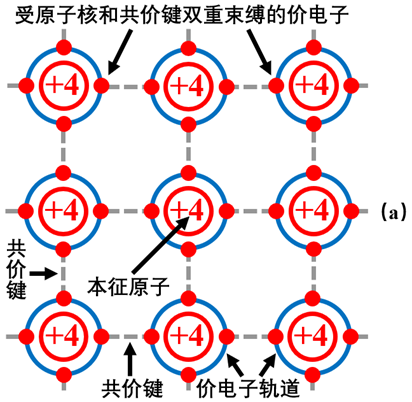
評論