濕法蝕刻
蝕刻的歷史方法是使用濕法蝕刻劑的浸泡技術。該程序類似于前氧化清潔沖洗干燥過程和沉浸顯影。晶圓被浸入蝕刻劑罐中一段時間,轉移到沖洗站去除酸,然后轉移到最終沖洗和旋轉干燥步驟。濕法蝕刻用于特征尺寸大于3微米的器件。在該水平以下,需要控制和精度,需要干法蝕刻技術。
蝕刻均勻性和過程控制通過向浸泡罐中添加加熱器和攪拌裝置(如攪拌器或超聲波和兆聲波)來增強。
濕法蝕刻劑的選擇基于它們均勻去除頂層而不攻擊(良好的選擇性)下層材料的能力。
蝕刻時間的變化是一個過程參數,受到溫度變化的影響,因為船和晶圓在罐中達到溫度平衡,以及晶圓轉移到沖洗罐時的持續蝕刻作用。通常,該過程設置為與均勻蝕刻和高生產力兼容的最短時間。最長時間限制在光刻膠繼續附著在晶圓表面的時間。
蝕刻目標和問題
蝕刻過程中圖像轉移的精確性取決于幾個過程因素。它們包括不完全蝕刻、過度蝕刻、底切和各向同性或各向異性蝕刻側壁。
不完全蝕刻
不完全蝕刻是部分頂層留在圖案孔中或表面上的情況(下圖所示)。不完全蝕刻的原因包括縮短的蝕刻時間、存在減緩蝕刻的表面層或導致晶圓較厚部分不完全蝕刻的不均勻表面層。如果使用濕法化學蝕刻,較低的溫度或弱蝕刻溶液會導致不完全蝕刻。如果使用干法等離子體蝕刻,錯誤的氣體混合物或操作不當的系統也會產生同樣的效果。
過度蝕刻和底切
不完全蝕刻的相反情況是過度蝕刻。在任何蝕刻過程中,總是有一定程度的過度蝕刻計劃。這允許表面層厚度變化。計劃的過度蝕刻還允許蝕刻穿透頂層表面的任何慢蝕刻層。
理想的蝕刻在層中留下垂直側壁(下圖所示)。產生這種理想結果的蝕刻技術被稱為各向異性。然而,蝕刻劑實際上在所有方向上都去除材料。這種現象稱為各向同性蝕刻。蝕刻作用在層的頂部進行,直到到達層底部。結果是斜側壁。這種作用也稱為底切(下圖所示),因為表面層在光刻膠邊緣下方被侵蝕。蝕刻步驟的一個持續目標是將底切控制在可接受的水平。電路布局設計師在規劃電路時會考慮底切。相鄰圖案必須相隔一定距離,以防止短路。必須在設計圖案時計算底切量。各向異性蝕刻在等離子體蝕刻中可用,是先進電路的首選。減少底切允許更密集的電路。
嚴重的底切(或過度蝕刻)發生在蝕刻時間太長、蝕刻溫度過高或蝕刻混合物太強時。底切也出現在光刻膠與晶圓表面之間的附著力很弱時。這是一個持續的擔憂,脫水、底漆、軟烤和硬烤步驟的目的是防止這種故障。光刻膠在蝕刻孔邊緣的附著力失敗可能導致嚴重底切。如果附著力非常差,光刻膠可能會從晶圓表面抬起,導致災難性的底切。
-
晶圓
+關注
關注
52文章
4973瀏覽量
128208 -
蝕刻
+關注
關注
9文章
419瀏覽量
15489
原文標題:半導體工藝之從顯影到最終檢查(六)
文章出處:【微信號:FindRF,微信公眾號:FindRF】歡迎添加關注!文章轉載請注明出處。
發布評論請先 登錄
相關推薦
使用n型GaSb襯底優化干法和濕法蝕刻工藝
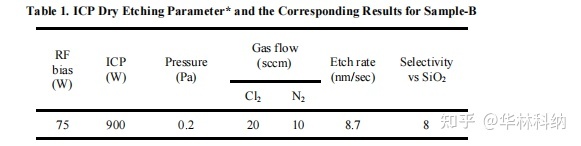
硅濕法蝕刻中的表面活性劑
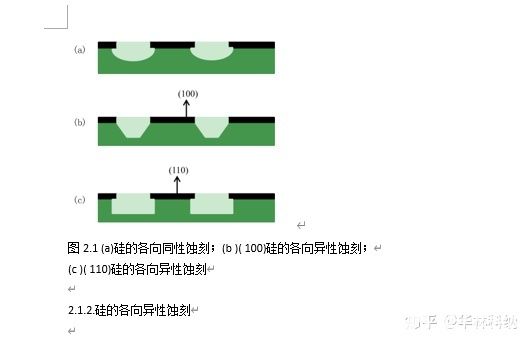
濕法蝕刻工藝的原理
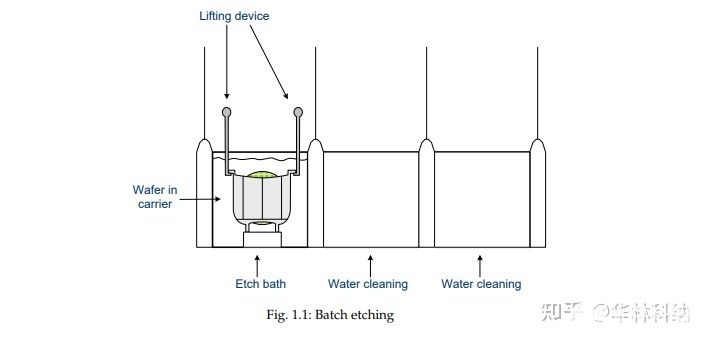
濕法蝕刻工藝
《炬豐科技-半導體工藝》GaN、ZnO和SiC的濕法化學蝕刻
關于濕法蝕刻工藝對銅及其合金蝕刻劑的評述
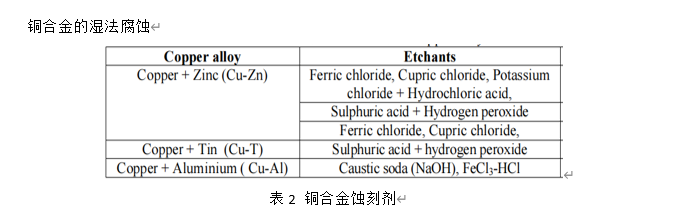
濕法蝕刻與干法蝕刻有什么不同
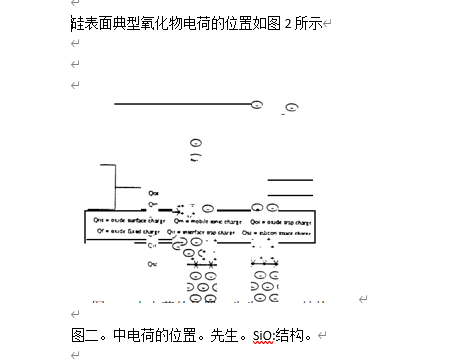
評論