傳統的功率模塊基本結構分層圖來說說其構成:
可見,我們前面聊的很多的半導體芯片,只是功率模塊中的一部分,除此之外還包括其他的成分。而這些成分的選擇和搭配,再結合半導體芯片的特性,將決定功率模塊的整體性能。
?功率半導體芯片:如IGBT、FRD、MOSFET等等,傳統Si基和新興的第三代半導體SiC等,它們的特性受制于其本身的設計,同時也需要看于其搭配的封裝材料和技術;
?絕緣襯底:主要是由陶瓷或硅化合物構成的絕緣層,其上覆蓋金、銀和銅等構成的金屬層;
?底板:一般由銅、銅合金、碳基強化混合物、碳化硅鋁等構成;
?互連材料:一般分為鉛焊錫和無鉛焊錫兩類,當然也包含銀燒結、固液互擴散連接等新興技術;
?功率互連主要使用的是鋁線鍵合,還包括壓接式連接和功率端子連接;
功率模塊的每一層之間都是緊密相關的,它們具有不同的電氣、機械及熱性能,設計時需要考慮彼此之間的配合,同時也可以根據不同的應用場景產生不同的搭配組合。所以很多半導體模塊的廠家會根據不同的應用需求來選擇不同的材料。
功率模塊封裝材料的選擇一般會考慮下面幾點:
★熱特性
★電氣特性
★機械特性
★化學特性
★成本
★技術成熟度
其中,熱性能是其最主要的因素。功率模塊的選型和使用過程中考慮得最多的也是熱,以及失效的最主要的因素也是熱,所以熱特性是功率模塊選擇的主要考慮因素。
熱應力:在溫度循環和熱疲勞測試中,加熱過程中各層材料的熱膨脹系數不同,將導致熱應力的產生,如果超過某層材料的機械強度限制,將會產生失效;
熱導率:功率模塊在使用過程中,半導體芯片將會產生大量的熱損耗,需要通過基板和底板等進行有效地傳輸散熱,以保證芯片的結溫能夠控制在合適的范圍之內。一般來說,較低的芯片結溫能夠延長模塊的可靠性,結溫沒上升9℃,模塊的失效概率將會增加一倍。所以,功率模塊的設計,除了半導體芯片,其他組成也是一個需要精心選擇和設計的重點。
接下來我們將分別介紹功率模塊各層的材料。
絕緣襯底主要是作為半導體芯片的底座,同時會在絕緣襯底上沉積導電材料、絕緣材料和阻性材料,還能形成無源的元器件。作為功率模塊機械支撐的結構,需要能夠耐受不同的工作環境,并且需要有足夠的熱導率將芯片等產生的熱量快速傳遞出去。并且,一些后續的工藝,如薄膜,綁定,間距等等,需要絕緣襯底能夠擁有一個較為合理的平整度。
功率模塊的襯底選擇標準
電氣特性
高體電阻率:>1012Ω/cm
高介電強度:>200V/mil (1mil=0.0254mm)
低介電常數:<15
熱特性
高導熱率:有效熱傳導>30W/m·K
與半導體芯片的熱膨脹系數較為匹配:般選擇在
2~6×10-6/℃
高耐溫:一般能夠滿足后續加工工藝的最大溫度
機械特性
高抗拉強度:>200MPa
高抗彎強度:>200MPa
硬度較合理
機械可加工性:易于磨削、拋光、切削和鉆孔等
可金屬化:適用于較為常見的金屬化技術,如薄膜和厚膜工藝、電鍍銅等等,這段我們下篇聊
化學特性
耐酸、堿及其他工藝溶液的腐蝕
低吸水率、空隙小
無毒性
不會等離子化
密度
低密度:機械沖擊能夠最小化
成熟度
技術較為成熟
材料供應能夠滿足
成本盡可能低,(說性價比高更為合適,畢竟不同的應用所能容許的成本高低不同)
目前幾種適用于功率半導體器件應用的絕緣襯底材料有下面幾種:
?陶瓷材料(3種):Al2O3(96%,99%)、AlN、BeO
?硅基襯底:Si3N4
其中屬氧化鋁較為常見,不過在功率半導體芯片等框架確定時,一些供應商會通過改變模塊中的其他成分,來達到要求,所以AlN和Si3N4也算常見。下面,我們來聊聊這幾種絕緣襯底材料的優劣。
一、氧化鋁(Al2O3)
優勢:
是絕緣襯底最為常用的材料,工藝相對較為成熟;成本較低;性能能夠滿足我們上述的要求;
劣勢:
導熱系數較低,熱膨脹系數(6.0~7.2×10-6/℃)與半導體芯片(Si基的一般為2.8×10-6/℃)的熱膨脹系數不算太匹配;高介電常數;抗酸性腐蝕性能一般;
所以,氧化鋁適用于中、低功率器件;適合高壓和低成本器件;適用于密封封裝;99%的氧化鋁性價比更高一些。
二、氮化鋁(AlN)
優勢:
熱導率高,約為Al2O3的6倍,較為適合大功率半導體器件的應用;AlN的熱膨脹系數為4.6×10-6/℃,較為匹配芯片;性能同樣滿足我們上述的要求;
劣勢:
是一種較新的材料,但與氧化鋁和氧化鈹相比工藝還不算成熟;在其表面直接敷銅的難度較大,易發生熱疲勞失效;成本約為氧化鋁的4倍;并且在較高溫度和較大濕度下可能會分解為水合氧化鋁;
適合大功率半導體器件的理想襯底之一,由于其機械斷裂強度一般,應用時需要合金屬底板配合使用。
三、氧化鈹(BeO)
優勢:
極其優異的熱導率,約為Al2O3的8倍;同樣適合大功率半導體器件的應用;工藝成熟;
劣勢:
無論是固態粉末還是氣態都是有毒性的;熱膨脹系數相對較大,約為7.0×10-6/℃;機械強度較差,只有Al2O3的60%左右;成本是氧化鋁的5倍;
有毒性大大限制了這種材料的使用。
四、氮化硅(Si3N4)
優勢:
熱膨脹系數約為3.0×10-6/℃,與半導體芯片較為接近;機械性能優越:是Al2O3和AlN的2倍以上,是BeO的3倍;熱導率高,是Al2O3的2.5倍;適合大功率半導體的應用;高溫強度高,抗熱震性優良;
劣勢:
技術相對還沒有那么成熟,所以供應商也相對有限;不適合酸性環境下的應用;成本是Al2O3的2~2.5倍;
對于大功率半導體器件的應用來說,Si3N4應該是目前最優的襯底材料,CTE和熱導率較為優勢,可靠性也較高。
以上4種絕緣襯底,最常見的氧化鋁,最不常見的氧化鈹,以及較為優異的碳化硅,很多廠家都在針對不同的應用來搭配不同的絕緣襯底,這一點能夠在芯片技術發展的同時,間接地更大效率地發揮已有芯片的性能。
幾種常用的金屬化技術:
?薄膜
?厚膜
?電鍍銅
?直接敷銅
?活化釬焊覆銅
?硬釬焊敷銅
絕緣襯底表面金屬化要求:
熱特性:
高熱導率(>200W/K·m)
與絕緣襯底的熱膨脹系數相匹配
高抗熱疲勞性(溫度循環相關)
高熱穩定性(即耐高溫性)
電氣特性:
載流能力強
低電阻率(一般而言,通過金屬鍍膜的電壓降要小于芯片集射極之間飽和壓降的1/10)
機械特性:
與絕緣襯底的高附著力
適合鍵合
適合焊接等工藝
與絕緣襯底相兼容
與現有工藝設備相兼容
化學特性:
易于刻蝕成形(幾種技術中,厚膜不作此要求)
不和工藝過程中的溶劑反應
無毒性
抗腐蝕性良好
化學惰性
成本:
滿足要求的情況下盡可能低(這點毋庸置疑)
薄膜技術
薄膜一般是通過在襯底的整個表面進行濺射或者物理氣相沉積的方式形成,薄膜層經過灌封材料、曝光、蝕刻等獲得設計的樣式。常用薄膜金屬材料有:金、銀、銅和鋁。
與厚膜技術相比,薄膜技術能夠實現更精準的定位和更細小的間距,所以非常適合高頻、高密度的應用。薄膜層和絕緣襯底的結合力較強,并且具有優異的抗熱疲勞老化的能力,同時鍵合能力也較優于厚膜技術;但從成本來看,薄膜技術比厚膜要貴上個5倍左右,同時多層薄膜結構難度較大。
通常薄膜層的厚度為2.5um,甚至可以更薄,載流能力在幾到幾十安培。
厚膜技術
厚膜一般是通過絲網印刷的方式將特別配置的焊錫膏印制在襯底上,然后進行干燥,最后通過高溫下燒結成形。焊錫膏可以用來制作導體、電阻、電容、電感等等無源元器件,厚膜一般有三種類別:聚合物厚膜、金屬陶瓷厚膜和耐火材料厚膜,厚度介于0.5~2mil之間。
①聚合物厚膜
采用高分子樹脂混合導電、阻性或者絕緣的顆粒,在85~300℃的溫度下進行固化,固化溫度一般為120~165℃。這種金屬化的成本較低,但是被限制在低溫下使用。
②金屬陶瓷厚膜
這是最常用的金屬化厚膜,,適用于陶瓷和硅基襯底,包含以下幾組成分:
①活性成分:有助于厚膜的成形;
②黏結成分:提供和襯底之間的黏結力;
③有機黏結劑:為絲網印刷提供足夠的流動性;
④溶劑或者稀釋劑:調整黏度用。
此混合材料的成形溫度介于850~1000℃,厚膜與襯底的附著力較優,但是抗熱疲勞能行較差,最大載流能力在幾安培左右。
③耐火厚膜
這是一種能夠承受高溫的特殊金屬陶瓷厚膜,通常在1500~1600℃的還原氣氛中進行熱處理,膜和襯底之間的附著力很強并且抗熱疲勞強度很高,常用的耐火厚膜材料為鎢和鉬,載流能力被限制在1~2A。
金屬化敷銅技術
相對于薄膜和厚膜技術而言,沒有了金屬化厚度的限制,有幾個優點:
★增加金屬化層的厚度;
★提高了金屬化層的載流能力;
★提高了熱導率;
值得注意的是,隨著金屬化層厚度的增加,熱膨脹系數和絕緣襯底的匹配程度將越來越差,在較大的熱失配時將產生顯著的殘余的熱應力,甚至會導致微小裂紋。
金屬化敷銅技術的四種方法:
電鍍銅;
直接敷銅;
活化釬焊覆銅;
常規硬釬焊敷銅;
銅鍍層還需要解決結合難度高和化學性較為活潑的問題,一般會通過添加過渡層來提高結合力,并在銅表面增加鎳或者金來作為保護層。
電鍍銅
該方法是通過電鍍技術在絕緣襯底表面電鍍一定厚度的銅,首先需要通過厚膜或者薄膜工藝在襯底表面沉積一層金屬膜,通過用鉬或著錳作薄膜材料,用銅作厚膜材料??梢杂没瘜W鍍的方式將一層薄銅預鍍在厚膜層或者薄膜層表面,再利用電鍍技術繼續沉積銅層,最后可以將銅鍍層在氮氣中進行高溫處理,以獲得較好的結合力和抗熱疲勞能力。
電鍍層一般介于5~8mil,可通過光刻獲得精細電路圖案。如果再增加鍍層厚度,光刻圖案精度會下降,但是載流能力能到50A左右。
直接敷銅
直接敷銅時利用高溫下實現銅和陶瓷的緊密直連,銅和陶瓷界面之間不需要任何的焊劑或者催化劑。銅和陶瓷在氮氣中被加熱到1070℃左右(略低于銅的熔點),此時銅氧化物薄膜可以形成共熔晶體潤濕連接界面,冷卻后實現銅和陶瓷的緊密連接。
此方法金屬銅層厚度介于8~20mil,同樣可以通過光刻來獲得設計的電路圖案,但是精度不會太高。
直接敷銅用于功率模塊封裝的優點:
?銅和陶瓷的連接體表現為一個具有均勻熱膨脹系數的整體,其熱膨脹系數更接近于陶瓷。
?選用的銅材料純度較高,無氧且導電能力強,選用合適的線寬和厚度,金屬層能夠獲得很低的電阻,載流能力可以到100A以上。
?較大的銅層厚度保證了功率芯片的熱傳導。
AlN和Si3N4絕緣襯底則必須先進行一定的工藝處理,因為直接敷銅首先需要一層氧化膜,相對較為繁瑣,下面的更適合這兩種襯底。
活化釬焊覆銅
活化釬焊覆銅技術采用焊料合金在銅和陶瓷之間形成黏合層。釬焊通常以黏結的形式實現,大多使用絲網印刷技術,得到的鈦釬焊層具有優良的附著力和熱循環能力。
活化釬焊覆銅已經廣泛應用于AlN和Si3N4絕緣襯底,而相對于直接覆銅,其優點如下:
?更強的黏合力;
?更強的載流能力;
?更高的熱疲勞強度。
常規硬釬焊敷銅
與上述的活化釬焊較為相似,但是硬釬焊技術必須在真空條件下進行。首先在襯底上濺射一層薄銀層,并以黏結的方式將銀合金焊料粘在搞薄膜上,最后將銅箔覆蓋在上面。將整體加熱到焊料合金的熔點進行制造,釬焊后的頂層可以通過光刻得到想要的圖案。
除了電鍍銅技術之外,后三者比較適合大功率半導體的金屬化工藝。
底板作為絕緣沉底的機械支撐,一是吸收功率器件內部產生的熱量,二來要將熱量傳遞出去,必須具有較高的熱導率才能有效地傳遞熱量。并且需要具有較低的表面粗糙度,能與絕緣襯底緊密接觸,否則由于粗糙度造成的空隙會形成熱點,降低可靠性。另外底板還需要具有一定的形變能力,可以與散熱器等熱沉緊密接觸。
底板選擇標準
首先為了與絕緣襯底相匹配,需要與絕緣襯底的熱特性、機械特性、化學特性等相匹配,除此之外:
01
熱特性
熱導率(W/m·K)——高于150W/m·K
熱膨脹系數——與絕緣襯底相匹配
02
機械特性
高抗拉強度——高于200MPa
高抗彎強度
易于塑形
表面粗糙度低——低于2um
03
化學特性
不與處理溶劑發生反應
低吸水率
低毒性
04
成本
始終是不可不考慮的一點
目前半強化的高導電無氧銅是底板的首選材料,而大多數高性能襯底采用的則是復合材料,通過控制復合材料的合金成分、粉末顆粒大小合成分組成來控制底板的性能。目前最先進的復合材料多數是聚合物、金屬和碳釬維強化或者顆粒強化,或兩者皆有;纖維強化復合材料是各向異性的,顆粒強化復合材料是各向同性的。
幾乎所以絕緣襯底材料都會選擇鋁層或者銅層作為接觸部分,這兩種材料都需要通過表面鎳或者鎳/金層來提高可焊性,同時起到免受腐蝕的作用。
可作為底板的材料:
銅、鋁、銅/鉬/銅、碳化硅鋁、銅/鎢基、銅/鉬基、銅/石墨基、銅/金剛石基、鋁/石墨基
其中只有銅/鉬/銅層壓板是大顆粒復合材料,其余都是微顆粒復合材料。
考慮到化學反應的影響,所有材料的表面都會鍍鎳層,能夠保證良好的焊料潤濕性、低吸水性和對處理溶劑的耐腐蝕性。
各種底板的一些劣勢:
Cu/Mo/Cu:成本高、密度高、難以機械加工、存在分層的可能性;
Cu/Mo:成本高、密度高、機械加工困難;
Cu/W:成本高、密度高
AlSiC復合材料
碳化硅鋁復合材料是片狀或者近凈成形的材料,是目前出了銅底板之外較常遇到的底板材料。近凈成形工藝可以使得導熱片底面變形,可增大底板與冷卻系液之間的導熱面積,利于散熱,并能夠在批量生產中減少加工需求。
大部分近凈成形復合材料制造步驟大致如下:
①加工準備:多孔顆粒碳化硅通過注射成型得到多孔AlC半成品,能夠具有底板需要的幾何特征,包括腔、孔以及表面紋理等等。如果預處理溫度較為合適,還可以在絕緣襯底上進行制造。
②滲透:將多孔半成品插入尺寸和底板成品相同的模具中,在真空和高壓的條件下,熔融狀態的耐火鋁滲透到多孔半成品中,可以形成多種鋁硅合金以得到所需性能。
③后續加工:在底板頂端采用火焰噴涂銅層來加強和絕緣地板的焊接能力。
所以AlSiC的劣勢是機械加工難度大,過程控制較為嚴格。
而隨著材料技術的不斷發展,摻雜石墨纖維的復合材料在大功率器件的應用將有著良好前景,同時還需要看未來功率模塊的發展速度,否則石墨纖維復合材料的發展再快也不會在功率模塊中得到應用,所以希望是乘風破浪,不久的將來我們能夠看到越來越多的具有新材料的功率模塊。
半導體技術的進步使得芯片的尺寸得以不斷縮小,倒逼著封裝技術的發展和進步,也由此產生了各種各樣的封裝形式。當前功率器件的設計和發展具有低電感、高散熱和高絕緣能力的屬性特征,器件封裝上呈現出模塊化、多功能化和體積緊湊化的發展趨勢。為實現封裝器件低電感設計,器件封裝結構更加緊湊,而芯片電壓等級和封裝模塊的功率密度持續提高,給封裝絕緣和器件散熱帶來挑戰。在有限的封裝空間內,如何把芯片的耗散熱及時高效的釋放到外界環境中以降低芯片結溫及器件內部各封裝材料的工作溫度,已成為當前功率器件封裝設計階段需要考慮的重要問題之一。
-
MOSFET
+關注
關注
147文章
7234瀏覽量
213979 -
IGBT
+關注
關注
1268文章
3830瀏覽量
249699 -
材料
+關注
關注
3文章
1254瀏覽量
27380 -
功率器件
+關注
關注
41文章
1794瀏覽量
90563
發布評論請先 登錄
相關推薦
耐高溫絕緣陶瓷涂層IGBT/MOSFET應用 | 全球領先技術工藝材料
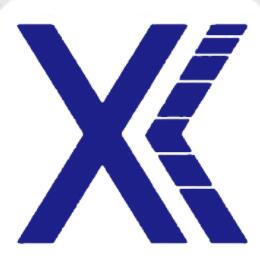
DOH新材料工藝封裝技術解決功率器件散熱問題
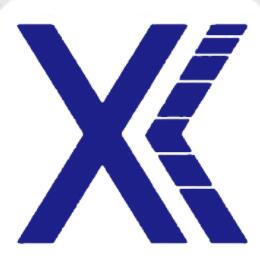
IGBT芯片/單管/模塊/器件的區別
igbt模塊與mos的區別有哪些
影響IGBT功率模塊散熱的因素
功率器件IGBT及國內外IGBT企業
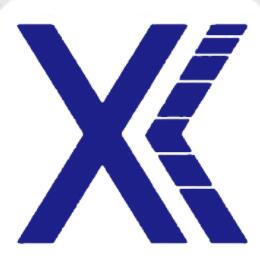
評論