1. SiC 性能優異,材料升級勢在必行
SiC 是第三代寬禁帶半導體材料,在禁帶寬度、擊穿場強、電子飽和漂移速度等 物理特性上較 Si 更有優勢,制備的 SiC 器件如二極管、晶體管和功率模塊具有 更優異的電氣特性,能夠克服硅基無法滿足高功率、高壓、高頻、高溫等應用要 求的缺陷,也是能夠超越摩爾定律的突破路徑之一,因此被廣泛應用于新能源領 域(光伏、儲能、充電樁、電動車等)。
1.1.什么是 SiC
半導體材料按被研究和規模化應用的時間先后順序通常分為三代。第一代:20 世紀 40 年代,硅(Si)、鍺(Ge)開始應用,硅的自然儲量大、制 備工藝簡單,是當前產量最大、應用最廣的半導體材料,應用于集成電路,涉及 工業、商業、交通、醫療、軍事等人類生產生活的各個環節,但在高頻高功率器 件和光電子器件應用上存在較大瓶頸。第二代:20 世紀 60 年代,砷化鎵(GaAs)、磷化銦(InP)在光電子、微電子、 射頻領域被用以制作高速高頻、大功率以及發光電子器件,能夠應用于衛星通信、 移動通信、光通信、GPS 導航等。由于 GaAs、InP 材料資源稀缺、價格昂貴、 有毒性、污染環境,使得第二代半導體材料的應用具有一定的局限性。第三代:20 世紀 80 年代,碳化硅(SiC)、氮化鎵(GaN)、金剛石(C)等為 代表的寬禁帶(Eg>2.3eV)半導體迅速發展,具有擊穿電場高、熱導率高、電子飽和速率高、抗輻射能力強等優勢,滿足高電壓、高頻率場景,應用于高電壓 功率器件、5G 射頻器件等領域。
與 Si 材料相比,SiC 主要優勢在于:1)SiC 具有 3 倍于 Si 的禁帶寬度,能減少漏電并提高耐受溫度。2)SiC 具有 10 倍于 Si 擊穿場強,能提高電流密度、工作頻率、耐壓容量并減 低導通損耗,更適合高壓應用。3)SiC 具有 2 倍于 Si 的電子飽和漂移速度,所以可工作頻率更高。4)SiC 具有 3 倍于 Si 的熱導率,散熱性能更好,能夠支持高功率密度并降低散 熱要求,使得器件更輕量化。因此,SiC 材料具有明顯的材料性能優勢,能滿足現代電子對高溫、高功率、高 壓、高頻、抗輻射等惡劣條件要求,適用于 5G 射頻器件和高電壓功率器件,滿足新能源領域(光伏、儲能、充電樁、電動車等)對于輕量化、高能效、高驅動 力等要求。
1.2.我們為什么要用 SiC 做器件
SiC 器件包括二極管、晶體管和功率模塊。2001 年英飛凌最先發布 SiC JBS 產 品;2008 年 Semisouth 發布了第一款常關型的 SiC JFET 器件;2010 年 ROHM 公司首先量產 SiC MOSFET 產品;2011 年 Cree 公司開始銷售 SiC MOSFET 產品,2015 年 ROHM 繼續優化推出了溝槽柵 MOSFET。目前, SiC SBD 二極管和 MOSFET 晶體管目前應用最廣泛、產業化成熟度最高,SiC IGBT 和 GTO 等器件由于技術難度更大,仍處于研發階段,距離產業化有較大 的差距。
SiC 器件因其材料特性表現優越電氣性能:1)導通、開關/恢復損耗更低:寬帶隙使得 SiC 器件漏電流更少,并且在相同耐壓條件下,SiC 器件的導通電阻約為硅基器件的 1/200,因此導通損耗更低;Si FRD 和 Si MOSFET 從正向偏置切換到反向偏置的瞬間會產生極大的瞬態 電流,過渡到反向偏置狀態會產生很大損耗。而 SiC SBD 和 SiC MOSFET 是 多數載流子器件,反向恢復時只會流過結電容放電程度的較小電流。并且,該瞬態電流幾乎不受溫度和正向電流的影響,無論在何種環境條件下都可以實現穩定 快速(小于 20ns)的反向恢復。根據 ROHM,SiC MOSFET+SBD 的模組可 以將開通損耗(Eon)減小 34%,因此恢復損耗低;SiC 器件在關斷過程中不存在電流拖尾現象,根據 ROHM , SiC MOSFET+SBD 的模組可以將關斷損耗(Eoff)減小 88%,因此開關損耗更低。
2)器件得以小型化:SiC 禁帶寬度決定了它能夠以更高的摻雜濃度、更薄的膜厚漂移層制作出 600V 以上的高壓功率器件(對于相同耐壓的產品、同樣的導通電阻,芯片尺寸更小);SiC 飽和電子漂移速率高,所以 SiC 器件能實現更高的工作頻率和更高的功率 密度,因頻率的提升減少了電感、變壓器等外圍組件體積,從而降低了組成系統 后的體積及其他組件成本。SiC 帶隙寬并且導熱率顯著,不僅在高溫條件下也能穩定工作,器件散熱更容易, 因此對散熱系統要求更低。
3)SiC 器件熱穩定:SiC SBD 與 Si FRD 開啟電壓都小于 1V,但 SiC SBD 的溫度依存性與 Si FRD 不同:溫度越高,導通阻抗就會增加,VF 值會變大,不易發生熱失控,提升系 統的安全性和可靠性。同等溫度條件下,IF=10A 時 SiC 與硅二極管正向導通電 壓比對,SiC 肖特基二極管的導通壓降為 1.5V,硅快速恢復二極管的導通壓降 為 1.7V,SiC 材料性能好于硅材料。此外,Si MOSFET 的漂移層電阻在溫升 100℃時會變為原來 2 倍,但 SiC MOSFET 的漂移層電阻占比小,其他電阻如溝道電阻在高溫時會稍微下降,n+ 基板的電阻幾乎沒有溫度依存性,因此在高溫條件下導通電阻也不容易升高。
超越摩爾定律,新材料是突破路徑之一。硅基器件逼近物理極限,摩爾定律接近 效能極限。SiC 器件作為功率器件材料端的技術迭代產品出現,能夠克服硅基無 法滿足高功率、高壓、高頻、高溫等應用要求的缺陷。
2. 多領域需求驅動,SiC 市場規模可達 62.97 億美元
2021-27 年全球 SiC 功率器件市場規模 CAGR 為 34%。SiC 器件被廣泛用于 新能源汽車、光伏發電、軌道交通、智能電網、國防軍工等領域。Yole 數據顯 示,全球 SiC 功率器件市場規模將由 2021 年的 10.9 億美元增長至 2027 年的 62.97 億美元,2021-27 年 CAGR+34%。此外,根據 CASA Research 統 計,2020 年國內 SiC、GaN 電力電子器件市場規模約為 46.8 億元,較上年同 比增長 90%,占分立器件的比例為 1.6%。并且預計未來五年 SiC、GaN 將以 45%的年復合增長率增至近 300 億元。
根據 Yole,新能源汽車、光伏儲能是 SiC 市場增長的主要驅動力。1)全球新能源汽車 SiC 功率器件市場規模 2019 年為 2.3 億美元,占比為 41.6%, 2021 年 6.8 億,占比為 62.8%,預計至 2027 年增加至 49.9 億美元,占比提 升至 79.2%,2021-27 年 CAGR 為 39.2%。2)光伏儲能是 SiC 功率器件第二大應用市場,2021 年該全球市場規模為 1.5 億美元,預計至 2027 年增加至 4.6 億美元,2021-27 年 CAGR 為 20.0%。據 CASA 預測,2021-26 年中國第三代半導體電力電子市場將保持 40%年均 增速,到 2026 年市場規模有望達 500 億元。其中,車用第三代半導體市場將從 40.5 億元增長至 267.3 億元;充電樁用第三代半導體市場從 0.54 億元增長至 24.9 億元;光伏用第三代半導體市場從 5 億元增長至 20 億元。
2.1.新能源車是 SiC 器件應用的最大驅動力,或迎替代機遇
2.1.1. 角度一:SiC 電驅系統搶先上車,體積、損耗有效下降
SiC 功率器件做電驅,電力損耗有效下降。新能源汽車系統架構中涉及到功率半 導體應用的組件包括:電機驅動系統、車載充電系統(OBC)、電源轉換系統(車 載 DC/DC)和非車載充電樁。其中電驅是 SiC 功率器件最主要的應用部位,行 業內也都率先在電驅采用 SiC 器件。根據美國能源部對純電動車Nissan-Leaf的能耗分析,電驅能量損耗約為16%, 其中功率器件占其中的 40%,因此,電控里功率器件能量損耗約占整車的 6.4%。若使用 SiC 器件,通過導通/開關等維度,總損耗相比硅器件下降 70%,全車總 損耗下降約 4.48%,也相當于相同的電池容量下行駛里程提升比例。據汽車之家拆分,動力電池占純電動汽車總成本的 40%-50%,假設某中高端電 動車價格為 20 萬元,電池成本約 8-10 萬元,如以 SiC 方案提升里程 5%計算, 相同性能的產品條件下,僅電池系統就為總成本節省 4000-5000 元。
采用 SiC 可減小電力電子系統體積、減少能量損失。SiC 模塊可以在實現 50kHz 以上的高頻驅動(傳統 IGBT 模塊無法實現),推動電感等被動器件的小型化。另外,IGBT 模塊存在開關損耗引起的發熱問題,只能按照額定電流的一半進行 使用,而 SiC 模塊開關損耗較小,即使在高頻驅動時也無需進行大幅的電流降 額,散熱系統要求也相對較低,同樣減小了 SiC 器件的體積。采用 SiC 模塊可 以加速高集成、高密度三合一電驅的推進,實現系統性體積的縮小,進而帶來風 阻(占驅動損耗的 1/3)的減小,促進能量損耗進一步降低。
使用 SiC 并未增加整車成本。雖然 SiC 器件成本高于硅基器件,但使用 SiC 器 件可以降低系統體積、降低電池損耗、提升續航里程,從而促進整車成本的降低。據 Wolfspeed(Cree)測算,在新能源汽車使用 SiC 逆變器,可以提升 5%-10% 的續航,節省 400-800 美元的電池成本,與新增 200 美元的 SiC 器件成本抵 消后,還能實現 200-600 美元的單車成本節約,未來,隨著 SiC 規模化量產之 后,成本有望逐步降低,將為整車成本創造更大空間。
SiC 在城市工況、電池容量大、電壓低的方向上能夠提升更大系統效率。一方面, 電池基礎容量越大,可以提升的絕對里程數就越多;鋰電池成本越高,可以節省 的單位電池成本越大。另一方面,在固定電池電壓后,電池功率近似跟輸出電流能力成正比,輸出電流能力近似跟芯片的使用數量成正比,功率約高則相應使用 SiC 器件越多,替換成本越高。此外,越是處于頻繁開關/頻繁剎車加油的低速工況下,獲得的效率優勢就更高, 所以在城市工況中運行,使用 SiC 器件帶來的效率提升的優勢更加明顯。2018 年特斯拉在其 Model3 車型首次將 Si IGBT 換成了封裝尺寸更小的 SiC 模塊, 使開關損耗降低了 75%,系統效率提高了 5%,續航里程提升 5-10%。
2.1.2. 角度二:電動汽車架構向高壓過渡,成為 SiC 上車催化劑
補能時間長是新能源汽車的最大痛點。如今車企推出的電動汽車續航多在 500km 上下,甚至高達 700km,和普通燃油車續航里程接近,續航已不再是最 大負累。但是電動車還是面臨里程焦慮的問題,主要原因還是燃油車加油時間僅 為 15 分鐘,而電動車快充至少需要 60 分鐘,在高峰期充電排隊等候時間亦進 一步拉長。
續航越高、充電效率越高,電動車在通勤中耗時與燃油車約接近。根據《Enabling Fast Charging:A Technology Gap Assessment》做的一項實驗:在 525 英 里(1 英里=1.6 公里)的旅程中,普通燃油車只需要加油一次,總耗時 8 小時 23 分鐘;而續航 300 英里 400KW 的直充電動車單次充電僅需 23 分鐘,旅途 總計耗時 8 小時 31 分鐘,整體耗時不輸燃油車。
根據 P=UI,提升充電效率的方向有二,提升電壓最佳。根據發熱量公式 Q=IRt, 提升電流模式充電過程會產生大量熱量,對汽車散熱系統和熱管理有更高的要求。在用大電流充電時,還會導致極化現象出現、電池內部化學反應不充分,對于電 池的傷害較大。此外,大電流模式的應用場景有限制,目前大電流模式僅在 10%- 20%SOC 進行最大功率充電,在其他區間充電效率也有明顯下降。而提升電壓 模式除了減少能耗、提高續航里程外,還有減少重量、節省空間等優點,是目前 廠商普遍采用的模式。
相同功率下高電壓比大電流更優。華為分別測算了高電壓 800V/250A,大電流 400V/500A,相較基準 400V/250A 的電池系統成本和整車成本變化,高電壓 架構下整車成本的上升不足 2%,比大電流方案更優。根據戴姆勒奔馳研究,在 800V 高壓平臺采用 SiC 模塊較硅基 IGBT 模塊整車低了 7.6%的能耗,相比中 低壓能耗降低更多。
越來越多汽車廠商布局 800V 平臺。受限于硅基 IGBT 功率元器件的耐壓能力, 之前電動車高壓系統普遍采用的是 400V 電壓平臺。如今,高壓快充路線受到越 來越多主機廠的青睞,先是保時捷 TaycanTurboS、小鵬,隨后現代、起亞等國 際巨頭,比亞迪、長城、廣汽等國內主機廠也相繼推出或計劃推出 800V 平臺, 高壓快充體驗將會成為電動車市場差異化體驗的重要標準。未來,隨著市場對續 航里程、充電速度要求的提高,電動車電壓有望升至 800V-1000V。
高壓架構未來向中小車型滲透。根據車型劃分,可將乘用車劃分為 A00、A0、 A、B、C 級車等多個級別。根據各車企官網數據,A 級以下微型或小型車型普 遍采用低壓系統,而在 B 級/C 級中大型車型中,高壓平臺逐漸普及。長期看快 充對于中小車型亦是剛需,800V 架構升級具備長期趨勢。
高電壓平臺需要各部件耐高壓、耐高溫,將導致 SiC 器件的替代需求顯著增長。高壓平臺看起來只是升高了整車的電壓,但對于技術的開發和應用,卻是“牽一 發而動全身”的系統工程。1)電機電控:800V 平臺要求下,硅基 IGBT 的開關/導通損耗將大幅升高,而 SiC 器件在耐壓、開關頻率、損耗等多個維度表現優異,因此電機控制器需要采 用 SiC MOSFET 代替硅基 IGBT。2)車載 OBC:主流功率從 3.6kW、6.6kW 升級到 11kW、22kW,并向雙向 逆變升級。雙向 OBC 不僅可將 AC 轉化為 DC 為電池充電,同時也可將電池的DC 轉化為 AC 對外進行功率輸出,需要使用 SiC 器件。3)DC/DC:直流快充樁原本輸出電壓等級為 400V,可直接給動力電池充電, 但車系統平臺升級為 800V 后需要額外的升壓產品使電壓能夠上升到 800V,配 合 OBC 給動力電池進行直流快充。此外,DC/DC 轉換器還可將高電池電壓轉 換為低電壓,為動力轉向系統、空調以及其他輔助設備提供所需的電力,同樣需 要耐高壓材質的 SiC 器件。4)空調壓縮機:由電動機驅動,為系統提供主動制冷/熱的動力,在汽車熱管理 系統中處于重要地位,隨著動力源向更高電壓切換,SiC 器件有很大的優勢。
實現大功率快充的高壓系統架構共有三類,全系高壓快充有望成為主流架構。1)全系高壓,即800V 電池+800V 電機電控+800V OBC、DC/DC、PDU+800V 空調、PTC。全系高壓的優勢是能量轉化率高,但是短期成本較高,但長期來看, 產業鏈成熟以及規模效應具備之后,整車成本下降。2)部分高壓,即 800V 電池+400V 電機、電控+400V OBC、DC/DC、 PDU+400V 空調、PTC。部分高壓的優勢是基本沿用現有架構,僅升級動力電 池,車端改造費用較小,短期有較大實用性,但是能量轉化率沒有全系高壓高。3)全部低壓架構,即 400V 電池(充電串聯 800V,放電并聯 400V)+400V 電機、電控+400V OBC、DC/DC、PDU+400V 空調、PTC。其優勢是短期成 本最低,但是對充電效率提升有限。
高壓將進一步加速主驅、OBC 和 DC/DC 的 SiC 滲透率提升。以 22kW 800V 雙向 OBC 為例,從 Si 轉到 SiC 設計,因從一個三電頻降到兩電頻開關拓撲, DC 端器件數量從 16 顆到降到了 8 顆器件,驅動電路、pcb 板面積也減半,同 時提高了運行效率,替換具有顯著優勢。根據 CASA 預測,SiC 功率器件滲透 率將在電機逆變器及 DC/DC 器件中持續增長。
2.1.3. 角度三:充電樁向大功率方向發展,SiC 器件滲透率進一步提升
中國公共充電樁快速增長,總量占比超過全球半數。IEA 數據顯示,2021 年全 球共公共充電樁保有量為 176 萬個,其中有 120 萬個為低速充電樁(功率≤ 22kW),56 萬個為高速充電樁(功率>22kW)。根據各國已宣布的氣候承諾方 案,預測 2022-30 年全球年均建設 100 萬/50 萬個低速/高速充電樁,2030 年全球將擁有 1000 萬/550 萬個低速/高速充電樁。2021 年底中國擁有 115 萬個公共充電樁,占全球 65%。根據中國電動汽車充 電基礎設施促進聯盟發布的最新數據,2022 年 1-9 月新增公共充電樁 48.9 萬 臺,充電配套設施建設逐步完善。
我國有望于 2025 年在城市和城際重點區域實現 2-3C 公共充電樁的初步覆蓋。根據《中國電動車充電基礎設施發展戰略與路線圖研究(2021-2035)》,我國將 于 2025 年實現 2-3C 的充電樁在重點區域的城市和城際公共充電設施的初步 覆蓋;于 2030 年實現 3C 及以上公共快充網絡在城鄉區域與高速公路的基本覆 蓋;于 2035 年實現 3C 及以上快充在各應用場景下的全面覆蓋。
充電樁向大功率方向發展。《交通運輸部關于推動交通運輸領域新型基礎建設的 指導意見》中明確要在高速公路服務區建設超級快充、大功率充電汽車充電設施。據 EVICPA 統計,2016-20 年中國新增直流樁的平均功率從 70kW 提升至 131kW,在新增直流樁中 150kW 的比例從 9%增至 28%;從用戶使用習慣的 角度來看,99.3%用戶在公用場站充電選擇快充樁,87%用戶選擇 120kW 及以 上的大功率充電樁。國家電網是國內最大的充電樁公開招標企業,2022 年招標 的充電樁中,功率為 160kW、240kW 和 480kW 的占比分別為 53%、3%和 16%,160kW 超越 80kW 成為主力招標功率。
更高功率、更多數量的超充站布局。截至 2022 年 6 月,特斯拉在中國大陸已建 立 1200 多座超級充電站,8700 多個超級充電樁,其 V3 充電樁功率為 250kW, 未來還將推出峰值充電功率 350kW 的 V4 充電樁;小鵬汽車 22 年 8 月發布峰 值充電功率為 400kW 的 S4 超快充樁,計劃到 23 年新增超過 500 座以上、到 25 年累計建設 2000 座超快充站。此外,2022 年 7 月中國主導發起的 ChaoJi 直流充電接口標準在 IEC 全票通過,有望促進超級充電基礎設施加速布局。
大功率充電樁帶動 SiC 滲透率不斷提升。對于充電樁而言,采用 SiC 模塊可將 充電模塊功率提高至 60KW 以上,而采用 MOSFET/IGBT 單管的設計還是在 15-30kW 水平。同時,和硅基功率器件相比,SiC 功率器件可以大幅降低模塊 數量。因此,SiC 的小體積優勢在城市大功率充電站、充電樁的應用場景中具有 獨特優勢。
充電樁運營商從減少損耗率和儲能對雙向電流需求兩方面,也傾向使用 SiC。(1)對特來電、星星充電為首的公共充電樁運營商而言,從國家電網買電,到 給新能源車主充電的過程中,存在約 2%的損耗,通過使用 SiC 能夠將損耗降低 到 0.5%,則運營成本能顯著降低,加快回收投資。(2)隨著局部地區充電站數量增多、密度變大的情況,為了平抑對電網的沖擊, 需要配套儲能系統,在夜間進行儲能,充電高峰期間通過儲能電站和電網一同為 充電站供電,實現削峰填谷。充電與儲能環節的電流方向變化,而 IGBT 只能單 向流通,使用 SiC 是唯一選擇。
市場上主要由交流樁和直流樁兩種充電樁類型構成。交流樁因為其技術成熟成本 較低,可接入 220V 居民用電而成為公共充電樁的主流,但其充電效率低,耗時 長,主要適用于家用領域,目前大多仍使用硅基功率器件,隨著 SiC 功率器件成 本降低,未來交流充電樁中 SiC 功率器件的滲透率將進一步提升。直流充電樁充電速度較快,但技術復雜且成本高昂,因此早期推廣速度不如交流 充電樁;但對于公共充電樁來說,提升充電效率是用戶的關注核心。根據 IEA 統 計,全球 22kW 以上的快充樁占比從 2015 年的 14.4%,上升至 2021 年的 31.8%,公共充電樁中直流樁的滲透率持續提升。據中國充電聯盟發布的數據顯 示,截止 2022 年 9 月我國 163.6 萬臺公共充電樁中,交流樁達到 93.1 萬臺, 而直流樁為 70.4 萬臺,直流樁占比 43.1%。直流充電樁技術的未來研發市場十 分廣闊,SiC 功率器件需求量進一步增加。
2.1.4. 車用 SiC 解決方案市場規模可達 240 億元人民幣
由于 SiC 器件在新能源車用領域的優勢,隨著 SiC 在新能源車領域的應用,SiC 成本的降低,各大廠商紛紛布局 SiC,未來 SiC 在車用領域滲透率會越來越高。
SiC 新能源汽車市場規模:根據 EV-Volumes 最新數據,全球 2022H1 新能源 汽車銷量達 430 萬輛,同比+62%,新能源汽車滲透率提升至 11.3%。預計到 2025年全球新能源汽車銷量有望接近 2000萬輛,滲透率有望突破 20%,2021- 25 年復合增長率有望達 30%以上。我們假設車規 SiC 電驅模塊價值量約為 3000-4000 元,加之 OBC、DC/DC 等部件使用,整車的 SiC 器件價值量約為 4500 元。中壓車和低壓車會部分采用 SiC 器件,通過對不同電壓新能源車滲透率的計算,我們預計全球車用 SiC 器件 市場規模有望在 2025 年達到 240 億元以上。
2.2. SiC 賦能光伏發電,市場規模有望增長至百億元
政策驅動光伏國產化進程加速,新增裝機量持續提升。光伏逆變器是可以將光伏 (PV)太陽能板產生的可變直流電壓轉換為市電頻率交流電(AC)的逆變器, 可以反饋回商用輸電系統,或是供離網的電網使用。根據中國光伏行業協會 (CPIA)數據,2021 年全球光伏新增裝機規模有望達到 170GW,創歷史新高,各國光伏新增裝機數據亮眼,其中中國新增裝機規模 54.88GW,同比增長 13.9%。未來在光伏發電成本持續下降和全球綠色復蘇等有利因素的推動下,全球光伏市 場將快速增長,預計“十四五”期間,全球光伏年均新增裝機超過 220GW,我 國光伏年均新增裝機或將超過 75GW。
SiC 賦能光伏發電,轉換率提升顯著。光伏系統是 SiC 器件除了汽車領域外的 重要應用領域之一。根據天科合達招股說明書,使用 SiC MOS 或 Si MOS 與 SiC SBD 結合的功率模塊的光伏逆變器,轉換效率可以從 96%提升至 99%, 能效損耗降低 50%以上,設備循環壽命提升 50 倍,從而縮小系統體積、增加功 率密度、延長使用壽命。SiC 還可以通過降低無源元件的故障率、減少散熱器尺 寸、減少占地面積和節省安裝成本等方式間接節約成本。
海外布局較早,國內 SiC 企業也逐漸將產品導入到光伏市場。在海外,英飛凌、 富士電機等全球知名廠商早在 2012 年起開始布局、開發、量產應用 SiC 器件的 光伏逆變器產品。三安、瞻芯、泰科天潤等企業都已經與國內主流的光伏逆變器 生產企業進行合作,逐步擴大產能繼續帶動國產 SiC 器件的應用。
光伏逆變器市場規模有望增長至百億元。CPIA 預測到 2025 年,樂觀情景下全 球光伏新增裝機量有望超 330GW。受益于光伏裝機量上升,逆變器市場需求將 大幅增長,我們測算 2025 年全球 SiC 光伏逆變器新增市場有望增長至 108.90 億元。
2.3.應用場景多點開花,滲透率逐步提升
1)軌道交通
SiC 特性滿足軌交發展需求,節能提升符合“雙碳”大趨勢。SiC 高溫高頻耐高 壓的特性可滿足軌道交通大功率和節能需求,因此軌道交通中牽引變流器、輔助 變流器、主輔一體變流器、電力電子變壓器、電源充電機尤其有使用 SiC 器件的 需求。以牽引變流器為例,作為機車大功率交流傳動系統的核心設備,使用 SiC 器件能 提高牽引變流器裝置效率,從而滿足軌道交通大容量、輕量化和節能型牽引變流 裝置的應用需求,并提升系統的整體效能。根據中國城市軌道交通協會統計的數 據,使用 SiC 牽引逆變器可以節省至少 10%以上的電能耗,如果我國全面采用 SiC,以 2019 年全國軌交總電能耗為例,可節省 15.26 億度電,相當于北京一 年的軌交電能耗。
2)智能電網
未來智能電網將大量采用電力電子裝置來實現新能源接入,功率半導體器件是核 心元件,傳統硅基功率半導體器件的發展已接近其物理極限,新一代 SiC 功率器 件的優異性能可以滿足未來智能電網對高效率,高性能的需求,采用 SiC MOSFET 可以大幅度減小功率損耗,特別是器件的通態損耗,相比于采用硅基 MOSFET 的電力電子變換器,采用 SiC 功率器件損耗可以減少 60%以上,未來隨著智能電網產業的升級,SiC 功率器件替代硅基半導體器件或將成為必然。
3)其他
由于 SiC 器件工作頻率和效率較高、耐溫性較強等特性,其對功率轉換(即整流 或者逆變)模塊中電容電感等被動元件以及散熱片的要求大大降低,預期使用 SiC 器件可對整個工作模塊產生優化,從而滿足當前器件小型化和效率提升要求。預期未來在 PFC 電源、不間斷電源(UPS)、電機驅動器、風能發電以及鐵路 運輸等領域,SiC 應用場景可持續擴大。
3. 技術升級成本下降,SiC 落地拐點漸行漸近
SiC 產業鏈可以分為襯底材料制備、外延生長、芯片設計、器件制造和應用。SiC 晶體生長后經過切割、研磨、拋光、清洗等工序加工形成 SiC 襯底;在符合質量 要求的襯底材料上生長出新的半導體晶層作為外延,是影響元件的基本性能;最 后配合電路設計、封裝形成功率器件,應用于下游市場。襯底在 SiC 器件制造中占據核心地位。SiC 成本分布較硅基不同,據 Telescope Magazine 數據,傳統硅晶圓中襯底部分占比前道工序平均成本結構的 7%,晶 圓制造設備及工藝占比最高達 50%。由于 SiC 晶體生長速度緩慢且制造難度大, 據前瞻產業研究和 CASA Research 在 2020 年發布的數據,襯底和外延在 SiC 功率器件成本結構中占比分別為 47%和 23%,二者合計占比 70%,是 SiC 器件的核心。
產業呈現美、歐、日三足鼎立格局。玩家紛紛布局 SiC 業務,海外企業如 Wolfspeed、ROHM、ST 等具有先發優勢,在產業鏈的多個環節具備較強的產 業優勢;國產企業也正在加速入局積極追趕,目前已初步實現了全產業鏈自主可 控。
3.1.襯底是影響滲透率提升的關鍵,高成長高壁壘
SiC 襯底可分為半絕緣型和導電型兩種,由于 SiC 襯底制備晶體溫度要求嚴格、 良率低、時間長,導致成本居高不下,價格是硅基襯底的 4-5 倍。行業通過尺寸 大化、提高切割良率等方式正逐步縮小與硅基產品的價差。當前以 Wolfspeed 為龍頭的歐美日企業在 SiC 襯底市場占據多數份額,在上游供給緊缺的情況下, 國際巨頭正加緊完善產業布局,主要的措施包括了擴大產能,與上游襯底廠商鎖 定訂單,收購襯底廠商等,全球也迎來了對 SiC 襯底的擴產、收購潮。國內專注 做 SiC 襯底且規模較大的企業主要為天岳先進、天科合達、河北同光及山西爍 科,競爭優勢有望持續擴大。
3.1.1. SiC 襯底制備困難導致高成本,6 英寸晶片成為市場主流
SiC 襯底分為半絕緣型和導電型。半絕緣型 SiC 襯底指電阻率高于 105Ω·cm 的 SiC,主要用于生長 GaN 外延層制作射頻器件;導電型 SiC 襯底指電阻率在 15-30mΩ·cm 的 SiC,主要用于生長 SiC 外延層制造耐高溫、耐高壓的功率 器件。導電型 SiC 襯底可通過 N 和 Al 作為摻雜劑實現 N 型和 P 型導電性,目 前產品以 N 型為主(氮氣摻雜)。因下游新能源汽車、光伏等應用領域需求處于 高速增長階段,SiC 導電型襯底未來將占據 SiC 市場主導地位。
各施其能,各盡其長,兩種襯底未來前景廣闊。根據 Yole 數據,隨著 5G 基站 建設和雷達下游市場對射頻器件的大量需求,半絕緣型 SiC 襯底市場規模有望 取得較快增長。應用半絕緣型 SiC 襯底的氮化鎵射頻器件全球市場規模有望在 2026 年達到 24 億美元,復合增長率為 18%。而受益新能源市場發展,全球應 用導電型 SiC 襯底的 SiC 功率器件市場規模 2027 年有望達到 62.97 億美元, 復合增長率為 34%。下游應用市場的高速發展將帶動上游襯底市場規模的快速 增長,導電型襯底市場潛力高于半絕緣型襯底。
SiC 襯底生產流程與硅基類似,晶體為流程核心:1) 原料合成&晶體生長。將高純硅粉和高純碳粉按一定配比混合,在 2000℃ 以上的高溫下反應合成 SiC 顆粒。經過破碎、清洗等工序,制得滿足晶體生長要 求的高純度 SiC 微粉原料。并以高純度 SiC 微粉為原料,使用晶體生長爐生長 SiC 晶體。2) 晶錠加工&切割。將制得的 SiC 晶錠使用 X 射線單晶定向儀進行定向后磨 平、滾磨,加工成標準直徑尺寸的 SiC 晶體。使用多線切割設備,將 SiC 晶體 切割成厚度不超過 1mm 的薄片。3) 晶片研磨&拋光。通過不同顆粒粒徑的金剛石研磨液將晶片研磨到所需的平 整度和粗糙度,并利用機械拋光和化學機械拋光方法得到表面無損傷的 SiC 拋 光片。4) 晶片檢測。使用光學顯微鏡、X 射線衍射儀、原子力顯微鏡、非接觸電阻率 測試儀、表面平整度測試儀、表面缺陷綜合測試儀等儀器設備,檢測 SiC 晶片的 微管密度、結晶質量、表面粗糙度、電阻率、翹曲度、彎曲度、厚度變化、表面 劃痕等各項參數指標,據此判定晶片的質量等級。5) 晶片清洗。以清洗藥劑和純水對 SiC 拋光片進行清洗處理,去除拋光片上殘 留的拋光液等表面污物,再通過超高純氮氣和甩干機將晶片吹干、甩干將晶片在 超凈室封裝在潔凈片盒內形成可供下游即開即用的 SiC 晶片。
物理氣相傳輸法是制備 SiC 襯底最常用的方法。目前 SiC 晶體生長包括物理氣 相傳輸法(PVT)、高溫化學氣相沉積法(HT-CVD)、液相法(LPE)三種。1)PVT 法將高純 SiC 微粉和籽晶分別置于單晶生長爐內圓柱狀密閉的石墨坩 堝下部和頂部,用中頻感應線圈將坩堝加熱至 2000℃以上并控制籽晶處溫度略 低于下部微粉,SiC 微粉在溫度梯度下升華形成硅原子、SiC2 分子、Si2C 分子等不同氣相組分的反應氣體,并在籽晶上結晶形成圓柱狀 SiC 晶錠,生長速率一 般為 0.2-0.4mm/h 左右。2)HT-CVD 法是 SiH4、C2H4、C3H8 等反應氣體和載氣從底部通入向上輸 運,到達放置在頂端的籽晶夾具處,在 18000-2300℃加熱區域內部完全分解 并發生反應形成硅和 SiC 團簇,這些團簇升華并在籽晶上生長。然后,殘余氣體 從反應室頂部排出,生長速率一般為 0.3-1mm/h 左右。3)LPE 法以 1800℃熔融硅作為溶劑、以坩堝內壁的石墨作為溶質,構成碳飽 和的硅熔體。SiC 籽晶粘結在石墨棒底端。由于固液界面相對于熔體內部溫度較 低,從而使籽晶附近的熔體處于過飽和狀態,SiC 沿襯底的晶體結構沉析出來成 長為晶體,每小時 0.5-2mm/h 左右。因設備價格低、溫度場調節靈活等優勢,PVT 法是目前技術成熟度最高、應用最 廣泛的方法。而氣態的高純碳源和硅源比高純 SiC 粉末更容易獲得,并且由于氣 態源幾乎沒有雜質,HT-CVD 法更容易生長出高純半絕緣(HPSI)半導體,通 過控制通入的氮或者硼的流量,就可以控制 SiC 晶體的摻雜和導電強弱。液相法 由于生長過程處于穩定的液相中,沒有螺旋位錯、邊緣位錯、堆垛層錯等缺陷, 生長晶體因尺寸較小目前僅用于實驗室生長,但卻是另一種重要的方向和未來發 展的儲備。
SiC 襯底制備難度大導致其價格居高不下。對比傳統硅材,SiC 襯底制備具有晶 體溫度要求嚴格、良率低、時間長等特點,導致成本價格居高不下,是硅基襯底 的 4-5 倍。1)溫場控制困難:Si 晶棒生長只需 1500℃,而 SiC 晶棒需要在 2000℃以上 高溫下進行生長,并且 SiC 同質異構體有 250 多種,但用于制作功率器件的主 要是 4H-SiC 單晶結構,如果不做精確控制,將會得到其他晶體結構。此外,坩 堝內的溫度梯度決定了 SiC 升華傳輸的速率、以及氣態原子在晶體界面上排列 生長方式,進而影響晶體生長速度和結晶質量,因此需要形成系統性的溫場控制 技術。與 Si 材料相比,SiC 生產的差別還在如高溫離子注入、高溫氧化、高溫 激活等高溫工藝上,以及這些高溫工藝所需求的硬掩模工藝等。2)晶體生長緩慢:Si 晶棒生長速度可達 30~150mm/h,生產 1-3m 的硅晶棒 僅需約 1 天的時間;而 SiC 晶棒以 PVT 法為例,生長速度約為 0.2-0.4mm/h, 7 天才能生長不到 3-6cm,長晶速度不到硅材料的百分之一,產能極為受限。3)良品參數要求高、良率低:SiC 襯底的核心參數包括微管密度、位錯密度、 電阻率、翹曲度、表面粗糙度等,在密閉高溫腔體內進行原子有序排列并完成晶 體生長,同時控制參數指標,是復雜的系統工程。4)材料硬度大、脆性高,切割耗時長、磨損高:SiC 莫氏硬度達 9.25 僅次于金 剛石,這導致其切割、研磨、拋光的加工難度顯著增加,將一個 3cm 厚的晶錠 切割 35-40 片大致需要花費 120 小時。另外,由于 SiC 脆性高,晶片加工磨損 也會更多,產出比只有 60%左右。
SiC 襯底成本可以通過做大尺寸、降低切割損耗和提高良率等方式下降。1)大尺寸 SiC 襯底是重要發展方向。SiC 襯底主要有 2 英寸(50mm)、3 英寸(75mm)、4 英寸(100mm)、6 英 寸(150mm)、8 英寸(200mm)英寸等規格。據 wolfspeed,從 6 英寸到 8 英寸,單片襯底可切割芯片數量由 488 增至 845 個,邊緣浪費由 14%減至 7%。因此隨著襯底的尺寸越大,邊緣的浪費就越小、制備的芯片數量增多,促進單位 芯片成本的降低。因此,大尺寸是 SiC 襯底制備技術的重要發展方向。
國際 SiC 商業化襯底以 6 英寸為主,逐步向 8 英寸過渡。在半絕緣型 SiC 襯底 市場主流產品規格為 4 英寸;在導電型 SiC 襯底市場主流產品規格為 6 英寸。行業領先者 Wolfspeed、II-VI、ST、Onsemi、Soitec、ROHM 等已成功研發 8 英寸產品,國際龍頭企業已陸續開始投資建設 8 英寸 SiC 晶片生產線,預計 5 年內 8 英寸全面商用。國內 SiC 商業化襯底以 4 英寸為主,逐步向 6 英寸過渡。國內企業起步較晚, 研發進度稍慢,但也完成了 6 英寸襯底的布局,與國外差距不斷縮小。2020 年 山西爍科晶體 SiC 襯底項目投產,同時天科合達、河北同光晶體、南砂晶圓等幾 大襯底生產商均在擴張 6 英寸襯底產能。
2)提高材料使用效率:提高襯底切割良率。由于 SiC 的莫氏硬度為 9.5,硬度與金剛石接近,只能用金 剛石材料進行切割,切割難度大,切割過程中易碎,保證切割過程穩定獲得低翹 曲度的晶片是技術難點之一,可以通過激光切割或其他技術手段減少當前線切割 工藝的損耗。例如英飛凌收購的 Siltectra 使用的一種冷切割技術基于激光的技 術采用化學物理過程,利用熱應力產生一種力,該力沿著所需的平面以極高的精 度分裂材料,并且幾乎不產生割縫損失。可使得原材料損耗從傳統 75%減至 50%, 減少耗材成本,同時能夠使單片晶圓產出的芯片數量翻倍。
國內大族激光已生產出 SiC 晶錠激光切片機、SiC 超薄晶圓激光切片機設備,運 用的 QCB 技術可在原來傳統線切割的基礎上大幅提升產能,以切割 2cm 厚度 的晶錠,分別產出最終厚度 350um、175um 和 100um 的晶圓為例,產能提升 幅度分別為 40%、120%和 270%,目前設備正處于量產驗證階段。
3)減少損耗、良率提升促 SiC 成本下降。目前主流商用的 PVT 法晶體缺陷控 制難度大導致襯底良率低,各廠商通過技術投入研發逐年提升 SiC 襯底良率。例 如天岳先進設計不同尺寸 SiC 單晶生長爐,對坩堝、保溫進行了設計,實現了均 勻熱場結構,提升晶體質量和良率,其 SiC 襯底良率近年來保持在 70%以上。Wolfspeed 的 8 英寸 SiC 襯底良率在經過化學機械拋光(CMP)后預期良率在 95%之上,因此擁有產品定價權。隨著襯底廠商完成低缺陷密度單晶生長工藝及 厚單晶生長工藝研發后,襯底單位面積價格將會快速的下降。
2027 年 SiC 襯底市場規模將達到 33 億美元。隨著 5G 市場對 SiC 基氮化鎵器 件需求的增長,以及新能源領域對功率半導體的旺盛需求,將帶動 SiC 襯底的市 場規模逐步擴張。結合 wolfspeed 的經營情況,到 2027 年全球 SiC 襯底材料 市場規模預計將達到約 33 億美元。
3.1.2. SiC 襯底呈美、歐、日三足鼎立格局
國外企業市占率高,美國 Wolfspeed 全球獨大。由于芯片制造企業對 SiC 襯底 的選用極為慎重,美國 Wolfspeed(Cree)布局較早,良率和產能規模都在全 球處于領先的地位,其市場份額約為 45%呈現一家獨大的競爭格局。按地域分, 美國占據全球約 58%的市場份額。歐洲和日本的 SiC 企業占據了剩余的大部分 份額。國內企業的市占率約為 8%,主要有天科合達、天岳先進等。
按類型分,Wolfspeed市占率在導電型和半絕緣型襯底領域中亦最高。根據Yole 數據,全球半絕緣型 SiC 襯底市場中,2020 年 Wolfspeed(Cree)、II-VI、 天岳先進市占率總計高達 98%,形成三足鼎立的態勢。全球導電型 SiC 襯底市 場中,2018 年美國 Wolfspeed(Cree)市占率為 62%,遙遙領先于其他廠商, II-VI 和 ROHM 份額分別為 16%和 12%,三家合計占比高達 90%;陶氏、昭和 電工、ST(Norstel)等廠商分配剩余 10%的份額,國內廠商天科合達和天岳先 進占比分別為 1.7%和 0.5%,相對較低。
3.2.外延是提高 SiC 器件性能及可靠性的關鍵
SiC 外延材料生長技術成熟,壁壘相對較低,由于外延市場處于產業鏈中間環節, 襯底/器件廠商具備一定外延能力,因而市場規模以及玩家數量相對較小。主要 系國外 SiC 設備昂貴且交期慢,行業由 Wolfspeed 和昭和電工雙寡頭壟斷。國 內主要玩家為東莞天域、瀚天天成和南京百識,隨著國產 SiC 外延設備突破, 未來該環節利潤會逐步回歸正常水平。
SiC 外延工藝是提高 SiC 器件性能及可靠性的關鍵。SiC 外延是指在襯底的上 表面生長一層與襯底同質的單晶材料 4H-SiC。外延層可減小晶體生長和加工中 引入的缺陷帶來的影響,使 SiC 表面晶格排列整齊,形貌較襯底大幅優化。在此 基礎上制造的功率器件,器件性能和可靠性將顯著提升。SiC 外延材料生長方法與晶體生長方法相近。主要有升華外延(PVT)、液相外 延(LPE)、分子束外延(MBE)和化學氣相淀積(CVD)。化學氣相淀積是 SiC 外延生長中最常用的方法,其生長機理是以高純氫氣或者氬氣作為載氣,將反應 源氣體(如 SiH4、C3H8 等)帶入淀積室化學反應后生成 SiC 分子并沉積在襯 底上,生長出晶體取向與襯底相同的 SiC 單晶外延層。常用設備為熱壁式水平外 延爐,典型生長溫度范圍為 1500~1650℃,生長速率 5~30μm/h。
在中、低壓應用領域,SiC 外延的技術相對是比較成熟的。基本上可以滿足低中 壓的 SBD、JBS、MOS 等器件的需求,例如一個 1200 伏器件應用的 10μm 的外延片,它的厚度、摻雜濃度都非常優秀,而且表面缺陷可以達到 0.5 平方以 下。然而在高壓領域外延的技術發展相對比較滯后。展示的應用于 2 萬伏的器件 上的 200μm 的一個 SiC 外延材料,它的摻雜濃度均勻性、厚度和濃度都比低 壓的要差很多。
SiC 外延生長技術的不斷發展。經過幾十年的不斷發展完善,行業通過臺階控制 外延法、TCS 法等改進生長工藝,提升生長速率、保障晶型穩定。以行業龍頭企 業道康寧(Dow Corning)為例,該公司生長的 6 英寸 4H-SiC 同質外延材料 厚度均勻性小于 2%,摻雜濃度均勻性小于 3%,表面粗糙度小于 0.4nm。
SiC 外延市場由 Wolfspeed 和昭和電工雙寡頭壟斷。SiC 外延廠商從商業模式 來看,可分為中國的大陸的 EpiWorld、東莞天域以及臺灣的嘉晶電子這類純外 延廠商;業內龍頭 Wolfspeed 這樣垂直一體化,能夠提供襯底、外延、器件的 公司;日本昭和電工這樣 SiC 單晶和外延制備的上游原材料廠商。由于外延市場處于產業鏈中間環節,通常器件廠商具備一定外延能力,因而市場 規模以及玩家數量相對較小。據 Yole 數據,2020 年 SiC 導電型外延片市場中 Wolfspeed 和昭和電工市占率分別為 51.4%和 43.1%。Wolfspeed 在外延產 能 和 質 量 在 全 球 范 圍 內 均 處 于 領 先 地 位 , 昭 和 電 工 在 外 延 質 量 方 面 和 Wolfspeed 處在同一水平,產能方面略遜于 Wolfspeed。國內廠商東莞天域及 瀚天天成同屬第二梯隊,均計劃向 8 英寸方向布局,在外延片產能與質量方面不 及國際一線廠商 Wolfspeed 與昭和電工。南京百識因體量較小,行動較慢,遜 于東莞天域及瀚天天成。
3.3. SiC 芯片技術成熟和價格改善,封裝工藝同步跟進
芯片方面,目前 SiC SBD 出貨最大,SiC MOSFET 接力 SiC 二極管有望成為市場 增長點。Yole 預測到 2027 年全球 SiC MOSFET 占 80%的市場規模(約 50.38 億美元)。由于各環節良率提升、多企業布局促價格競爭、終端需求開始放量攤薄生 產固定成本,SiC 器件與 Si 器件價差縮小,預計 2023-25 年可達到合理性價比。封裝方面,從傳統 HPD 升級到 AMB,材料、工藝方面升級,由傳統器件廠商 ST、 英飛凌占主導地位,國內如斯達、三安、士蘭微、中車等企業也在陸續研發驗證。
3.3.1. SiC MOSFET 成為市場增長點,多因素推動 SiC 器件價格下降
中高壓二極管產品逐年增多。Mouser 數據顯示,2021 年共有 828 款 SiC SBD 產品在售,較 2020 年新增約 30 款,中高壓商業化產品逐年增多。其中,80% 以上的產品耐壓范圍集中在 650V 和 1200V;1700V 的 SiC SBD 產品達到 31 款,與 2020 年相比新增 10 款;3300V SiC SBD 產品約 6 款,單芯片導通電 流最高達 90A(Microchip,3300V/90A)。
實際應用中的需求促使 IGBT+FRD 的組合成為標配,SiC MOSFET 未來有望 替代該組合。受結構限制,IGBT 的內部沒有寄生二極管,電感突然斷電所釋放 的電容易燒壞回路中的 IGBT,若有快恢復續流二極管,其電就會通過續流二極 管回路放電,不至于燒壞 IGBT,因此 IGBT 廠家就索性在 ce 之間再加上快速恢 復二極管。目前,對于大電流的功率模塊,由 Si 的 IGBT 和 FRD 組合而成的 IGBT 模塊已得到廣泛應用。SiC MOSFET 高溫、高壓特性使其能夠更好的應用于大功率設備,在 600V 以 上具有較強優勢,最高可應用于 6500V 高壓,相較于傳統的 Si-IGBT 體積縮 小了 50%,效率提升了 2%,器件的使用壽命得到延長,并且在相同功率下損耗 小,散熱需求低,在電流密度、工作頻率、可靠性、漏電流等性能指標方面優勢 明顯。實際使用中,通過優化 SiC MOSFET 器件結構和布局,可以提升 SiC 體二極管通流能力,不需要額外并聯二極管,有效降低系統成本、減小體積。
200V SiC MOSFET 新品增多, 國際企業加速布局汽車領域 SiC MOSFET。根據 Mouser 數據,2022 年上半年 12 家主流廠商推出的 179 款 SiC 晶體管新 產品中,SiC MOSFET 占比較大。其中,1200V 的新品推出速度明顯加快, 2022 年上半年,II-VI、PI、KEC 等分別推出車規級 SiC MOSEFT,電壓集中 在 1200V、1700V。國際領先廠商 GeneSiC、英飛凌、ROHM、Wolfspeed 的 1200V 以上的新產品均已經超過一半。
高壓 SiC 模塊產品增多。2022 年上半年,Wolfspeed、TDSC(東芝電子元件 及存儲裝置株式會社)、英飛凌、三菱電機等國際廠商推出新款高壓 SiC 功率模 塊,產品額定電壓多在 1200V、1700V;并在積極推進與標準 IGBT 兼容,模 塊目標解決更小尺寸、更好擴展性和更高功率密度。
多種因素推動 SiC 器件價格下降。第一,上游襯底產能持續釋放,供貨能力提 升,量產技術趨于穩定,良品率提升,器件制造成本降低;第二,規格由 4 英寸 轉向 6 英寸、制造技術進一步提升,單片晶圓產芯片量大幅提升,成本大幅下降;第三,隨著更多量產企業加入,競爭加劇,導致價格進一步下降。第四,SiC MOSFET 產品較硅基產品 DieSize 更小,未來 Wafer Cost 下降情況下將進一 步推動 SiC 技術產業化。第五,主流豪華電動車品牌中全 SiC 逆變器預計從 2022-23 年量產,終端需求逐步釋放將提升廠商產能利用率,攤薄 SiC 器件生 產成本。
供應鏈緊缺情況緩解,單種器件價格呈下降趨勢。2022 上半年,供應鏈緊缺得 到緩解,供不應求的情況好轉,根據材料深一度,SiC MOSFET 產品價格回落 至 2020 年底水平,650V、900V、1200V、1700V 的產品均價分別為 1.88 元 /A、2.94 元/A、2.88 元/A、5.78 元/A;較 2021 年底分別下降了-7.13%、 56.49%、-7.25%、-5.33%。SiC、GaN 器件與 Si 器件價差縮小,價差收窄長期趨勢不改。據 Mouser, 2022 年上半年,650V SiC、GaN 功率晶體管均價分別為 1.88 元/A、2.78 元 /A,與 650V 的 Si IGBT(0.36 元/A)的價差縮小到 7.8 倍、5.3 倍,較上年底 縮小了 69%、42%。隨著 SiC、GaN 資源持續投入,技術產品不斷改良及各家 廠商大力推進,SiC、GaN 材料、芯片、器件、模組均有大量新增產能,成本顯 著下滑,SiC、GaN 產品價格進一步下降,價差收窄長期趨勢不改。
SiC 器件預計 2023-25 年可達到合理性價比。根據 CASA 的跟蹤,SiC 產品 價格近幾年來快速下降,較 2017 年下降了 50%以上,而主流產品與 Si 產品的 價差也在持續縮小,已經基本達到 4 倍以內,部分產品已經縮小至 2 倍,已經達 到了甜蜜點。加上考慮系統成本(包括周邊的散熱、基板等成本)和能耗等因素, SiC 模組已經有一定競爭力。
3.3.2. 模塊及單管雙路線同時存在,模塊亟需新的封裝材料和工藝
電機控制器中硅基 IGBT 上車方案可以分為模塊和單管并聯兩種,兩者主要的 區別是封裝形式的不同:(1)電控廠商外采 IGBT 模塊(斯達半導、時代電氣提供),然后集成電機、變速器做“三合一/多合一”方案上車,典型廠商如“央騰”。目前 IGBT 模塊仍然 是主要的應用路線,在國內主要造車新勢力以及部分自主品牌中滲透率較高。(2)單管并聯技術主要使用 MOS 管,主要應用在低速電動車如 60~72V 或者 是 96V 等電壓平臺系統。而涉及高電壓、大電流平臺 IGBT 單管并聯方案主要 的使用者包括特斯拉和英搏爾。中長期內 IGBT 模塊和單管并聯兩種方案仍將并存,IGBT 單管并聯方案主要應 用在 A00、A0 車型上;IGBT 模塊方案將廣泛應用在 A 級別車型上。單管并聯 方案具有低成本、設計開發周期短的特性,因此主要用在 A00、A0 車型上,主 要電控供應商為英搏爾、陽光電源和奧斯偉爾;模塊方案產品線相比 10 年前豐 富程度更高,因為 IGBT 芯片經過了模塊制造商的篩選,參數一致性更好,有更 高的安全性與可靠性,因此 IGBT 模塊方案在 A 級以上車型中搭載的場景更多。
SiC MOS 在主驅上車預計和 IGBT 方式類似,模塊及單管并聯同時存在:國外特斯拉 model3 主逆變器選用 SiC MOS 單管并聯方案。特斯拉的 Model3 是第一個應用碳化硅(SiC)功率元器件的電動車型,供應商選用來自 ST 的 650v SiC MOSFET。Tesla 的 TPAK(TeslaPack)用在主驅逆變器電力模塊上共 24 顆,采用單管并聯方式排布,拆開封裝每顆 TPAK 有 2 個 SiC 裸晶(Die), 共 48 顆 SiC MOSFET。
國內碳化硅供應商更多采用模塊技術路線作為電控中功率模塊解決方案。2021 年 12 月,基本半導體位于無錫市新吳區的汽車級碳化硅功率模塊制造基地正式 通線運行,首批碳化硅模塊產品成功下線。上汽大眾與臻驅科技共同開發 SiC 功 率模塊及電控搭載“三合一”電橋亮相大眾 IVET 創新技術論壇,這款搭載臻驅 科技碳化硅電控的“三合一”電驅動系統可提升 ID4X 車型至少 4.5%的續航里 程。
現 SiC 封裝技術大多沿用硅基器件封裝方式,基于傳統封裝結構,碳化硅模塊 封裝主要會帶來以下兩方面問題:1)引線鍵合,復雜內部互聯結構會產生較大的寄生電容/電感。SiC 器件由于具 有高頻特性、柵極電荷低、開關速度塊等因素,在開關過程中電壓/電流隨時間的 變化率會變得很大(dv/dt;di/dt)。因此極易產生電壓過沖和振蕩現象,造成器 件電壓應力以及電磁干擾問題。2)高工作電壓以及電流下的器件散熱問題。SiC 器件可以在更高的溫度下工作, 但在相同功率等級下,SiC 功率模塊較 Si 在體積上大幅降低,因此 SiC 器件對 散熱的要求更高。如果工作溫度過高會引起器件性能下降,不同封裝材料熱膨脹 系數失配,進而出現可靠性問題。這意味功率模塊需要更多地依賴封裝工藝和散 熱材料來進行散熱。當前傳統的封裝工藝達到了應用極限,亟需新的封裝工藝和材料進行替代。
未來 SiC 模塊封裝有以下演進趨勢:
1)在互聯、燒結技術方面
內部互聯技術將從鋁線鍵合/超聲焊接將改用銅線方式形式,芯片/襯板燒結方式 將采用銀燒結技術代替傳統 pb/Sn 合金焊。銀燒結工藝燒結體具有優異的導電性、導熱性、高粘接強度和高穩定性等特點。用該工藝燒結的納米銀燒模塊可長期工作在高溫環境;另外銀燒結工藝會在芯片 燒結層形成可靠的機械連接和電連接,半導體模塊的熱阻和內阻均會降低,提升 模塊性能及可靠性。銀燒結技術可使模塊使用壽命提高 5-10 倍,燒結層厚度較 焊接層厚度薄 60-70%,熱傳導率提升 3 倍。
2)在材料方面
襯板從氧化鋁升級到氮化硅、氮化鋁、AMB 厚銅襯板,塑封取代傳統灌膠。傳統的 HPD 使用氧化鋁材料,優點在于價格便宜、供應量充足,缺點在于散熱 能力較差。新型基材主要是氮化硅、氮化鋁材料、AMB 厚銅襯板。氮化鋁一般 用于工業領域,氮化硅常用于汽車領域,AMB 厚銅襯板用在車載 SiC 領域。對于模塊的散熱結構來說,襯板的選擇尤為重要,目前主流的功率半導體模塊封 裝主要還是用 DBC(直接鍵合銅)陶瓷基板, AMB 的熱導率比 DBC 氧化鋁 高 3 倍,且機械強度及機械性能更好。隨著碳化硅功率模塊的應用逐漸成熟, AMB 有望逐漸成為電子模塊封裝的新趨勢。此外,塑封模塊相較于 hybridpack 模塊的優勢具有低雜散電感、高可靠等特性。
3.4.專用設備研發和產業化加速
SiC 產業鏈主要區別在長晶以及外延環節,加工設備切割/研磨/拋光都是通用設 備,因此國產替代重點主要集中在 SiC 長晶設備以及 SiC 外延設備。SiC 長晶 爐方面,因長晶難點不在設備本身而是在工藝,大部分 SiC 襯底公司選擇自研 SiC 長晶設備,也有一些廠商作為第三方單獨供應 SiC 長晶設備,如北方華創、 晶升裝備、晶盛機電實現量產突破,國產單價 60-110 萬。SiC 外延爐方面,壁 壘更多來自于設備資本開支及對設備的工藝控制,目前外延設備供不應求。ASM 預計 2021-25 年對 SiC 外延設備的需求將以超過 25% 的 CAGR 增長。國內 北方華創、晶盛機電、恒普股份、納設智能、中微公司、中電科 46 等,正在研 發布局該領域,產品單價 800-1000 萬。
3.4.1. SiC 長晶設備:北方華創及晶升裝備占據國內 77%市場份額
SiC 長晶爐與傳統硅基設備相比原理具有相通性,但 SiC 襯底生長工藝難度更 高;為了保證工藝一致性,大部分 SiC 襯底公司選擇自研 SiC 長晶設備。SiC 長晶環節主要采用 PVT(物理氣相傳輸)的技術路線,溫度高、不可實施監控, 且長晶難點不在設備本身而是在工藝。因此基本每家襯底廠商工藝不一樣,也是 各家的核心 know-how,襯底制造企業往往會選擇自研“設備+工藝”模式效率 會更高。1)天科合達:選擇自研 SiC 長晶設備(沈陽設有分公司),長晶設備大部分自產 自銷;2)天岳先進:選擇自研長晶設備并找北方華創代工,但天岳先進擁有長晶爐的知識產權。國內采用自研/自產 SiC 長晶設備的碳化硅廠商還包括晶盛機電、河北同光、山 西爍科等。上述碳化硅廠商自研/自產晶體生長設備主要用于其自身碳化硅襯底 的生產制造,不存在大批量對外銷售設備的情形。
國內碳化硅單晶爐設備供應商目前可分為三個梯隊:第一梯隊,晶升裝備及北方華創為國內碳化硅單晶爐主要供應商,具備國內領先 的碳化硅單晶爐產業技術能力,產品已大批量交付多家國內下游碳化硅材料主流 廠商。第二梯隊,寧波恒普真空科技股份有限公司已實現向下游碳化硅廠商的小批量交 付,沈陽中科漢達科技有限公司主要根據自產/自研設備碳化硅廠商的設計及技 術要求,配套生產供應碳化硅單晶爐主要部件。第三梯隊,國內其他碳化硅單晶爐廠商包括連城數控、哈爾濱科友半導體產業裝 備與技術研究院有限公司、山東力冠微電子裝備有限公司、廈門天三半導體有限 公司、上海漢虹精密機械有限公司、蘇州優晶光電科技有限公司、磐石創新(江 蘇)電子裝備有限公司及江蘇卓遠半導體有限公司等,其中多數設備廠商處于樣 機開發及驗證階段,未實現設備批量供應。
北方華創及晶升裝備目前約占國內 SiC 長晶爐市場份額 77%。國內對外采購晶 體生長設備的主要碳化硅廠商包括天岳先進、三安光電、東尼電子及中電化合物 半導體有限公司,其主要向晶升裝備及北方華創采購碳化硅晶體生長設備。根據 北方華創公開披露資料,北方華創碳化硅單晶硅爐已累計出貨千余臺,預計 2022 年銷售 480 臺至 500 臺。晶升裝備因進入 SiC 長晶設備時間相對較晚,故晶升 裝備碳化硅單晶爐累計銷售數量及市場占有率低于北方華創。根據國內主要碳化硅廠商公開披露的現有產能、晶體生長設備主要供應商信息、 主要客戶設備數量、已供應設備數量等信息進行測算。北方華創主要向天岳先進 供應長晶設備,預計占國內碳化硅廠商采購份額的比重為 50%以上;晶升裝備 SiC 長晶爐市場占有率約為 27.47%-29.01%。
未來 2-5 年國內 SiC 長晶設備市場規模約為 36.38-88.94 億元。隨著下游器 件/模塊應用的放量,我國本土企業也積極投入碳化硅襯底國產化的進程中。天岳 先進、三安光電、露笑科技、東尼電子等上市公司公司,天科合達、比亞迪半導 體、河北同光等擬上市公司,均規劃在 2022-25 年間擴張 SiC 襯底產能,襯底 尺寸以 4 英寸、6 英寸為主,少數包括 8 英寸產線。參考晶升裝備公告中的假 設,以單臺碳化硅單晶爐產量為 375 或 500 片/年進行測算,假設每臺單價為 60 萬元-110 萬元(含稅),預計未來 2 至 5 年內,國內主要外購 SiC 長晶設備市 場需求約為 36.38-88.94 億元。
3.4.2. 碳化硅外延設備:被海外四大企業壟斷,瓶頸突破需重視
與襯底環節所需“設備+長晶工藝”的 know-how 不同,SiC 外延技術成熟度 相對較高,該環節的更多壁壘來自于設備資本開支及對設備的工藝控制,目前全 球主要有四家 CVD 設備玩家,其 SiC 外延設備具有各自的優勢:1)Axitron 的外延設備生長能力最強(10*100mm&6*150mm),因此其產能 相對更大。2)LPE 的外延設備的生長速率最高(>90um/h)。3)日企 TEL 的外延設備為雙腔體結構,有助于提高產量。4)nuflare 的旋轉速率更高,每分鐘可達 1000 轉,因此均勻性更強,同時他的 氣流方向可以避免一些顆粒物的產生,減少顆粒物落到片子上的概率。
目前整個碳化硅產業鏈的瓶頸在外延環節。近兩年資本市場更關注價值量更高的 SiC 襯底環節和以及上車最快的模塊環節,卻疏忽了外延的環節。目前外延環節 成為整個 SiC 產業鏈產業化的瓶頸,主要問題在于以下兩點:1)外延設備供不應求。到目前為止,主要6寸外延設備集中在國外 4 家廠商手 中,他們的產能有限且交期極長,而國內 SiC 外延設備廠商的產品還需驗證。現 在國內主要有兩大 SiC 外延廠,一個是廈門的瀚天天成,還有一個是東莞的天域 半導體。2022 年上半年的二者的外延設備數量在 20 多臺,到年底可以超過 30 臺左右。2)外延爐在驗證過程中還主要面臨幾大問題:a)主要零配件能否滿足供給;b) 本身設備的穩定性、操作方便性;c)生產出來的外延片能否滿足市場需求。預計未來 5 年全球 SiC 外延設備增速為 25%:2022 年 7 月,ASM International N.V.(ASM)宣布收購位于意大利的碳化硅(SiC)和硅外延設備制造商 LPE S.p.A.的所有流通股。ASM 內部預計從 2021-25 年,對 SiC 外延設備的需求 將以超過 25%的復合年增長率增長。國內做 SiC 外延設備廠商有北方華創、晶 盛機電、恒普股份等,目前也在逐步進入到客戶驗證階段。
審核編輯 :李倩
-
新能源
+關注
關注
26文章
5586瀏覽量
107775 -
半導體材料
+關注
關注
11文章
548瀏覽量
29633 -
SiC
+關注
關注
29文章
2869瀏覽量
62816 -
碳化硅
+關注
關注
25文章
2799瀏覽量
49176
原文標題:SiC全產業鏈拆解,新能源行業下一代浪潮之基(上)
文章出處:【微信號:dldzjsyyy,微信公眾號:電力電子技術與應用】歡迎添加關注!文章轉載請注明出處。
發布評論請先 登錄
相關推薦
SiC MOSFET的性能優勢
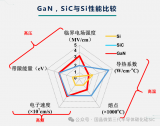
納米銀燒結技術:SiC半橋模塊的性能飛躍
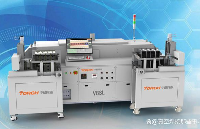
碳化硅SiC制造工藝詳解 碳化硅SiC與傳統半導體對比
碳化硅SiC在電子器件中的應用
碳化硅SiC材料應用 碳化硅SiC的優勢與性能
SiC MOSFET和SiC SBD的區別
什么是SiC功率器件?它有哪些應用?
SiC功率器件性能和可靠性的提升
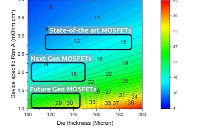
清純半導體與悉智科技攜手,共推SiC車載應用新篇章
全球掀起8英寸SiC投資熱潮,半導體產業迎來新一輪技術升級
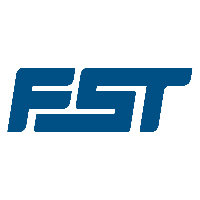
微型逆變器性能躍升:SiC器件的關鍵作用
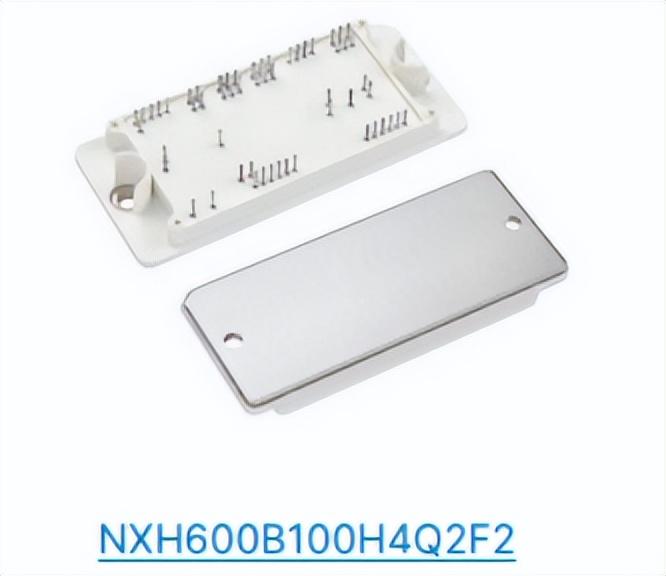
SemiQ 1200V SiC MOSFET Module說明介紹
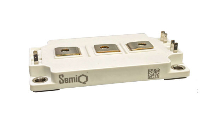
評論