一、管道安裝
管道安裝除應符合一般規定外,尚應符合各系統的專門規定。
1、一般規定
1.1 管道安裝一般應在與之連接的設備及元件安裝完畢,有關土建工程施工完畢并檢查合格后進行。
1.2 管道敷設位置應便于裝拆、檢修,且不妨礙生產人員的行走,以及機電設備的運轉、維護和檢修。
1.3 管子外壁與相鄰管道之管件邊緣的距離應不小于10mm。
1.4 同排管道的法欄或活接頭應相間錯開100mm以上。
1.5 穿墻管道的接頭位置宜距墻面0.8m以上。
1.6 機體上的管道應盡量貼近機體,但不得妨礙機器動作。
1.7 管道支架安裝應符合下列規定:
(1)現場制作的支架,其下料切割和螺栓孔的加工均宜采用機械方法。
(2) 管道直管部分的支架間距一般應符合下表的規定,彎曲部分應在起彎點附近增設支架。
(3)不銹鋼管道與支架之間應墊入不銹鋼、不含氯離子的塑料或橡膠墊片,防止不銹鋼與碳素鋼直接接觸。
1.8 管子不得直接焊接在支架上。
1.9 管子與設備連接不應使設備承受附加外力,并在連接時不得使贓物進入設備及元件內。
1.10 管道密封件必須按設計規定的材質和規格使用。
1.11 管道連接時,不得采用強力對口、加熱管子、加偏心墊或多層墊等方法來消除接口端面的空隙、偏差、錯口或不同心等缺陷。
1.12 不銹鋼管道安裝時,不得用鐵質工具敲擊。
1.13 軟管的安裝應符合下列規定:
(1)應避免急彎:外徑大于30mm的軟管,其最小彎曲半徑應不小于管外徑的7倍。
(2)與管接頭的連接處應有一段直線過度部分,其長度應不小于管子外徑的6倍。
(3)在靜止及隨機移動時,均不得有扭轉變形現象。
(4)當長度過長或承受急劇振動的情況時,宜用夾子夾牢,但在高壓下使用的軟管應盡量少用夾子。
(5)當自重會引起過分變形時,必須有適當的支托或按其下垂位置安裝。
(6)長度除滿足彎曲半徑和移動行程外,上應有4%左右的余量。
(7)相互間及同他物不得摩擦;離熱源進時,必須有隔熱措施。
1.14 管道安裝間斷期間,敞開的管口處應加封閉。
1.15 管道坐標位置、標高的安裝極限偏差均為±10mm;水平度或鉛垂度公差為2/1000。
1.16 同一平面上排管的管外壁間距及高低宜一致。
2、專門規定
2.1 液壓泵和液壓馬達的泄露油管應少高于液壓泵和液壓馬達本體的高度。
2.2 雙缸同步回路中兩液壓缸管道應對稱敷設。
2.3 長度超過5m的氣動支管路,宜順氣體流動方向向下傾斜10/1000以上的斜度。
2.4 氣動系統管道的支管宜從主管的頂部引出。
2.5 潤滑油系統的回油管道應向油箱方向向下傾斜12.5/1000~25/1000的斜度。潤滑油粘度高時,回油管斜度取大值;潤滑油粘度低時,回油管斜度取小值。
2.6 油霧系統管道應順油霧方向向上傾斜5/1000以上的斜度,且不得有存水彎。
2.7 潤滑脂系統的潤滑管路(給油器或分配器至潤滑點間的管道)在安裝前應充滿潤滑脂,管內不得留有空隙。
2.8潤滑管路充脂后應及時安裝,不得再在其上焊接或用火烤;管子在切割或加工螺紋后,必須除去管口有切削的潤滑脂,并補充潔凈的潤滑脂。
2.9 雙線式潤滑脂系統的主管與給油器及壓力操縱閥連接后,應使系統中所有給油器的指示桿及壓力操縱閥的觸桿在同一潤滑周期內同時伸出或同時縮入。
二、管道酸洗、沖洗、吹掃和涂漆規程
1、管道酸洗
1.1 一般規定;
(1)液壓、潤滑管道除銹應采用酸洗法。
(2)管道酸洗應在管道配置完畢且已具備沖洗條件后進行。
(3)酸洗時管道的螺紋和密封應有防酸蝕措施;金屬密封墊不應裝入管道中酸洗。
(4)涂有油漆的管子,酸洗前應用脫漆劑將油漆除凈。
(5) 酸洗液的濃度和各成分的比例應根據管道的銹蝕程度和酸洗用水的水質確定。
(6)管道酸洗用水必須干凈;不銹鋼管道酸洗用水的氯離子含量不得大于25ppm;酸洗后若用壓縮空氣噴油保護,則所用壓縮空氣必須干燥、潔凈。(7)管道酸洗應根據銹蝕程度、酸液濃度和溫度,掌握好酸洗時間,不得造成過酸洗。
(8)管道酸洗復位后,應盡快進行循環沖洗,否則應每周通油循環2~3次。
1.2 槽式酸洗
(1)采用槽式酸洗法進行酸洗時,一般應按以下工序進行:脫脂→水沖洗→酸洗→水沖洗→中和→鈍化→水沖洗→干燥→噴涂防銹油(劑)→封口。(2)有來回彎的管道進入酸洗液時,必須使管內全部空氣逸出。
(3)將管道放入酸槽時,宜使小管在上,大管在下。
1.3 循環酸洗
(1)采用循環酸洗法進行酸洗時,一般應按以下工序進行:水試漏→脫脂→水沖洗→酸洗→水沖洗→中和→鈍化→水沖洗→干燥→涂銹油(劑)。
(2)循環酸洗回路管道長度應根據管道大小確定,一般不宜超過300m。回路的構成必須使每根管道的內壁全部接觸酸液。
(3)回路管道最高部位應設置排氣點,最低部位應設置排空點;回路中的死點宜處于水平位置,如若朝下,則須在酸洗各工序交替時,松開死點接頭,排凈死點內上一工序留存的液體。
(4)酸洗回路通入中和液,應使出口溶液不呈酸性為止。溶液的酸堿性可用pH值試紙檢查。
1.4 酸洗質量檢查
(1)酸洗后管內壁應無附著異物。
(2)用鹽酸、硝酸和硫酸酸洗后,管內壁應呈灰白色;用磷酸酸洗后,管內壁應呈灰黑色。
2、管道沖洗
2.1一般規定
(1)液壓、潤滑系統管道在酸洗合格后必須進行沖洗;沖洗一般以循環方式進行。
(2)液壓系統管道在安裝位置上組成循環沖洗回路時,必須將液壓缸、液壓馬達以及蓄能器與沖洗回路分開;伺服閥和比例閥必須用沖洗板代替。
(3)潤滑系統管道在安裝位置上構成循環沖洗回路時,應使潤滑點與沖洗回路分開。
(4)作臨時連接用的鋼管道,在接入沖洗回路前也應酸洗合格。
(5)自備的沖洗泵、油箱、濾油器等應適用于所用的沖洗油(液)。
(6)沖洗回路的構成應使每一管段全部管內壁接觸沖洗油(液);若干個并聯的沖洗回路,各回路管道大小應相近;沖洗回路中的死角管段,應另成回路沖洗。
(7)沖洗過程中宜采用變換沖洗方向及振動管路等辦法加強沖洗效果。
(8)沖洗回路中如有節流閥和減壓閥,則應將其調整到最大開口度。
(9)沖洗油(液)加入油箱時,應經過濾,過濾精度不宜低于系統的過濾精度。
(10)油箱在加入沖洗油(液)前應作檢查,內部不得有任何肉眼可見的污染物。
(11)系統沖洗合格后,必須將沖洗油(液)排除干凈,但以工作介質進行沖洗時,若沖洗后沖洗油(液)的各項品質指標仍在要求范圍之內時,可以留用。
(12)管道沖洗完畢后若要拆卸接頭,則須立即用潔凈的塑料布封口;管道如需焊接處理,則該管道必須重新進行酸洗和沖洗。
2.2 沖洗油(液)和沖洗參數的確定
2.2.1 沖洗油(液)應按下列規定選用:
(1)沖洗油(液)應與系統設備、元件及管道密封件相容;
(2)沖洗油(液)應與系統工作介質相容;
(3)沖洗油(液)的粘度宜低。
2.2.2 沖洗油(液)的沖洗流速應使油(液)流呈紊流狀態,且應盡可能高。在管壁光滑的管道中形成紊流的最小流速V(m/s)可按下式計算:
V=0.2v/d
式中:v—沖洗油(液)的運動粘度,mm2/s; d—沖洗管道的內徑,cm。
2.2.3 沖洗泵的最小額定流量Q(1/min)可按下式計算:
Q=6VA
式中:V—沖洗回路中較大管道內的油(液)流為紊流的流速,m/s;A—沖洗管道橫截面積,cm2。
注:管道串聯沖洗時,A為其中最大管子的橫截面積;管道并聯沖洗時,A為并聯管子的橫截面積。
2.2.4 沖洗使用自備油箱時,自備油箱的容積Q1(m3)可用下式計算:
Q1=5Q2
式中:Q2—沖洗回路管道容積,m3。
2.2.5 沖洗用濾油器精度應不低于系統的過濾精度;沖洗用濾油器的過濾面積宜大(特別是用液壓液沖洗時)。
2.2.6 沖洗油(液)的溫度:用高水基液壓液沖洗時,沖洗液溫度不宜超過50℃;用液壓油沖洗時,沖洗油溫度不宜超過60℃。 在不超過上述溫度下,沖洗油(液)的溫度宜高。
2.3 沖洗檢驗
(1)液壓系統中的伺服系統和帶比例閥的控制系統以及靜壓軸承的靜壓供油系統,管道沖洗后的清潔度應用顆粒計數法檢測。液壓伺服系統的清潔度應不低于15/12級;帶比例閥的液壓控制系統以及靜壓軸承的靜壓供油系統的清潔度應不低于17/14級。
(2)液壓傳動系統、動靜壓軸承的靜壓供油系統、潤滑油系統和潤滑油脂系統可用顆粒計數法或目測法檢測。采用顆粒計數法檢測時,應不低于20/17級;采用目測法檢測時,連續過濾1小時后在濾油器上應無肉眼可見的固體污染物。
(3)采用顆粒計數法檢測時,樣液應在沖洗回路的最后一根管道上抽取;取樣應連續進行2~3次,以平均值為沖洗結果。
(4)采用顆粒計數法檢測時,應選用顯微鏡顆粒計數法或自動顆粒計數器計數法等經校正公認的顆粒計數法;油(液)樣應嚴格按照規定的程序抽取;取樣容器必須清潔,不致時油(液)樣失真。(5)采用目測法檢測時,在回路開始沖洗后的15~30分鐘內應開始檢查濾油器,此后可隨污染物的減少相應延長檢查的間隔時間,直至沖洗合格。
(6)系統沖洗完畢應填寫系統沖洗記錄。
3、管道吹掃
3.1 氣動系統管道安裝完畢后應用干燥的壓縮空氣進行吹掃。
3.2 吹掃宜分段進行,先吹掃主干管,再吹掃支管。
3.3 各種閥門和輔助元件不得投入吹掃,氣缸和氣馬達的接口必須封閉。
3.4 吹掃后的清潔度在排氣口用白布或涂有白漆的靶板檢查,如5分鐘內其上無鐵銹、灰塵及其他贓物即為合格。
3.5 管道吹掃完畢后應填寫管道吹掃記錄。
4、管道涂漆:
4.1 管道涂防銹漆前應除凈管外壁的鐵銹、焊渣、油垢及水分等。
4.2 管道涂面漆一般應在試壓合格后進行,如須在試壓前涂面漆,則應將焊縫部位留出,待試壓完畢后補涂。
4.3 使用的涂料應有合格證明書,過期變質的涂料不得使用。
4.4 管道涂漆的顏色和油料品種應按設計規定采用。
4.5 涂漆施工宜在5~40℃的環境溫度下進行,漆后一般自然干燥,未干燥前要防凍、防雨。
4.6 涂層的質量應符合下列要求:
(1)涂層完整,無損壞和漏涂;
(2)漆膜附著牢固,無剝落、皺紋、氣泡、針孔等;
(3)涂層均勻,厚度符合設計要求。
審核編輯 :李倩
-
管道
+關注
關注
3文章
145瀏覽量
17994 -
機電設備
+關注
關注
0文章
39瀏覽量
13900
原文標題:經驗 | 管道安裝及管道酸洗、沖洗、吹掃和涂漆規程一文搞定!
文章出處:【微信號:gh_acae488c81aa,微信公眾號:定華儀表學堂】歡迎添加關注!文章轉載請注明出處。
發布評論請先 登錄
相關推薦
超大口徑管道測徑儀 激光與光電測量的原理是怎樣的?
國內常見的石油管道外徑測量方法?
聲波定位技術在地下管道中如何應用
消防管道壓力流量監控方案
管道風速傳感器安裝要求標準
管道風速傳感器的安裝在管道的前端還是后端
管道風速傳感器的工作原理是什么
基于DOE的管道爬行機器人輕量化研究
運營商的本分,就是專業做好管道
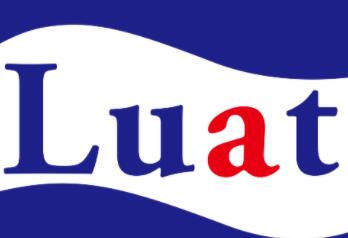
紅外熱成像技術在管道泄漏檢測中的應用

ATA-M4功率放大器在充粘液管道損傷檢測中的應用
linux管道概述
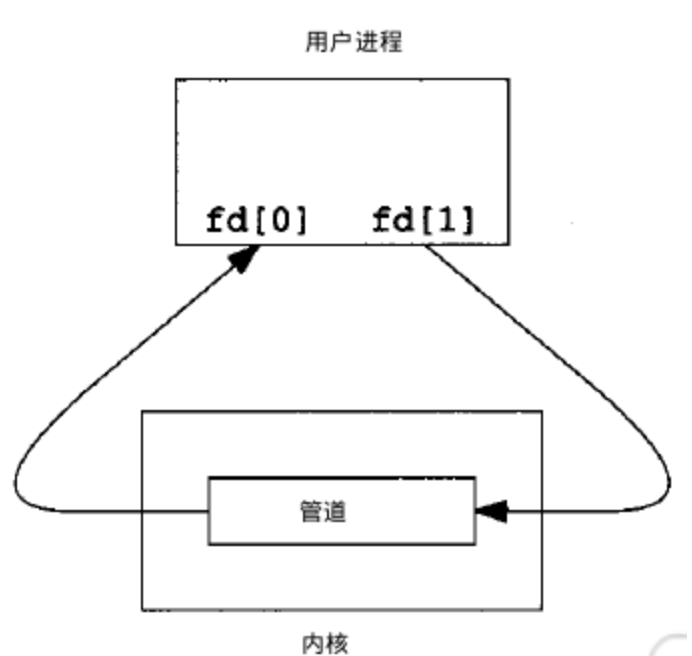
評論