摘要
表面處理和預清洗在半導體工業中的重要性是眾所周知的。為了確保良好的薄膜粘附性和金屬半導體觸點的低電阻,某些溶劑或等離子體清洗以及酸或堿處理對于去除有機殘留物和表面氧化物至關重要。已知多種蝕刻劑對于去除天然GaAs氧化物是有效的。然而,在特定的加工步驟中使用什么處理,以及需要什么濃度和加工時間來獲得有效的結果,在工業中幾乎沒有標準化。此外,與制備特定蝕刻化學物質相關的成本和所涉及的化學物質的有效壽命以前沒有被仔細研究過。這篇合作論文將回顧幾個大規模制造組織中濕法氧化物去除蝕刻的一般實踐,并研究這些實踐的有效性。
介紹
作為制造過程的一部分,所有半導體制造場所都使用酸、堿、溶劑和等離子清洗來去除氧化物、抗浮渣或GaAs和相關外延化合物。例如,圖案化光致抗蝕劑開口可能需要等離子體清潔以去除顯影步驟后殘留的殘余抗蝕劑,并且這之后經常是氧化物去除以確保蒸發膜的良好粘附。類似地,可能需要表面清潔來為下一層光刻或電介質沉積準備晶片表面。在濕法處理的情況下,化學制劑可以作為通風柜中的浴液獲得,或者從晶片軌道或其他自動化單晶片處理工具中分配。工程部門有責任決定使用什么樣的浴缸,使用什么樣的濃度,以及有效的浴缸壽命應該是多少。本文提供了這些選擇的示例,并討論了這些加工步驟在美國一些主要制造工廠中的使用情況。
用于去除氧化物的氯化氫溶液
鹽酸的稀釋物經常被用作在薄膜沉積之前去除表面氧化物的試劑。最廣泛使用的氯化氫起始濃度通常稱為37%氯化氫,更準確地說,是指11至12的氯化氫標準溶液,包裝上有標簽,標明36至38%氯化氫。全濃度37%鹽酸很少用于晶圓清洗,1:1鹽酸:DIW (18%鹽酸)或1:5鹽酸:DIW (6%鹽酸)更常見。盡管許多工廠通過稀釋率來表示水浴濃度,但如果不同地點的起始氯化氫濃度不一致,這就有可能造成混淆。Skyworks的蝕刻槽儲存的鹽酸起始濃度從18%到36%不等。在本節中,將以氯化氫百分比而不是稀釋率來描述濃度。
去除氧化物的其他化學物質
NH4OH的稀溶液也被用于各種加工步驟中的表面預清潔。它們最常用于光刻步驟和氮化物沉積之前,在某些情況下,在金屬化之前。在某些情況下,使用NH4OH進行表面清潔優于HF和HCl。HF可以攻擊PR-GaAs界面,HCl會攻擊任何暴露的鎳。在環球通信半導體,1:50稀釋的NH4OH(29%):DIW通常用于表面預清潔。清洗過程在室溫下使用3060毫升的浴液浸泡530秒,然后進行DIW漂洗和甩干。每個浴液在使用前5分鐘內混合,最多25分鐘只使用一次。成本低于20美元/加侖,每個晶圓大約需要0.01美元的化學清洗。從預清洗到后續處理的時間限制在15-60分鐘,以防止氧化物再生長。
砷化鎵氧化物的XPS研究
圖2顯示了在有意氧化但未接受濕氧化物去除處理的對照樣品上獲得的Ga 3d和As 3d結合能譜的高分辨率掃描的測量數據。光譜可以模擬為以不同結合能為中心的兩個或多個正態分布的總和,代表不同的含鎵和砷的化合物。圖2說明了如何將Ga 3d光譜建模為代表Ga2O3和GaAs的兩個分布之和,而將砷3d光譜建模為代表As2O5、As2O3和GaAs的三個分布。將代表每種化合物的模擬分布面積與鎵或砷光譜的總面積進行比較,以確定每種化合物的相對濃度。
僅使用DIW漂洗作為預清潔的GaAs晶片的濕法蝕刻底切用作比較不同化學清潔的氧化物去除的基線。對于GaAs-辛克斯粘合,用鹽酸和NH4OH清洗的晶片具有與基準晶片相似的底切。用氫氟酸清洗的晶片具有改進的粘附性,與其他預清洗方法相比,濕蝕刻底切減少了約25%。這種粘附力的提高很可能是由于除了氧化物去除之外的HF暴露的另一個影響。每種清潔化學品的兩種稀釋度之間沒有顯著差異。對于GaAs-珀羅附著力,所有化學清洗產生的附著力比基線晶片差。最后,如果每個清潔條件之間存在差異,則需要更多數據,因為每個條件的底切變化太大。
結論
晶圓制造商采用幾種不同的常用化學物質來蝕刻GaAs氧化物,評估每種方法的療效。就氧化物厚度而言,每種化學方法獲得的結果大致相同。對于氯化氫的情況,發現濃度或浴壽命對蝕刻后剩余氧化物厚度的依賴性很小或沒有依賴性。使用不同化學物質蝕刻的樣品的XPS分析證實,每種化學物質都產生相似的最終表面組成和殘余氧化物厚度。通過測量不同氧化物去除處理后沉積的SiN和光致抗蝕劑掩模的GaAs濕法蝕刻底切來評估蝕刻化學對薄膜粘附到GaAs的影響。當使用SiN蝕刻掩模時,發現了底切對氧化物去除化學的一些依賴性,而光致抗蝕劑掩模的結果是不確定的。在使用200個晶片的過程中,沒有觀察到鹽酸和NH4OH浴的消耗或負載效應。
審核編輯:符乾江
-
芯片
+關注
關注
456文章
50950瀏覽量
424758 -
集成電路
+關注
關注
5389文章
11574瀏覽量
362331
發布評論請先 登錄
相關推薦
晶圓的環吸方案相比其他吸附方案,對于測量晶圓 BOW/WARP 的影響
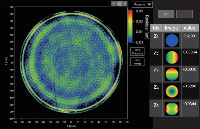
改善晶圓出刀TTV異常的加工方法有哪些?
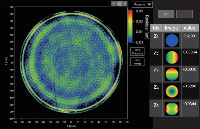
如何測量晶圓表面金屬離子的濃度

評論