成立于1945年的美國的ISA學會(以前稱為美國儀表學會,后來改名為國際自動化學會,簡稱都是ISA)正在開展慶祝成立75周年的各種活動。其中有一項是回顧75年來工業自動化技術的發展。
Automation.com的主編Bill Lydon撰文列舉了20項對自動化發展堪稱里程碑的技術創新和發明,其中有半導體和摩爾定律、可編程邏輯控制器PLC、分布式控制系統(DCS)架構、個人計算機(PC)、人機界面(HMI)、微軟的Windows操作系統、歷史數據庫、開放工業網絡、ISA-88批量控制標準、ISA-95企業控制系統集成標準、IEEE 802.15.4無線短程網規范促進無線傳感器的發展、機器視覺和圖像識別、ISA-95 企業控制系統集成標準B2MML、電子游戲技術、OPC UA、機器學習、工業4.0創議、數字孿生、云和邊緣計算,以及協作機器人。
與此同時還遴選了20個75年來對自動化的發展起了舉足輕重作用,堪稱自動化巨頭的人物,對他們的貢獻作了簡述。他們是:晶體管發明家Walter Brattain 和William Shockley;微處理器創新者Federico Faggin;氣-液相色譜分析技術發明人A.T. James和 J.P. Martin;PLC之父Dick(Richard) Morley;自適應控制之父Karl Astrom,;流程建模的先行者、AspenTech的創建人Larry Evans;Wonderware的創始人 Dennis Morin;工業歷史數據庫之父Patrick Kennedy;Tom Fisher,ISA-88的倡導者;Lynn Craig,ISA-88的倡導者、并深度介入ISA-88和ISA-95;Dennis Brandl,ISA-95的倡導者;IBM PC的實驗室主任BillLowe,對IBM PC問世起了巨大作用;工業通信協議的先驅John Berra,他是三個制造通信協議HART、FF和OPC的主要開發者,Emerson Process Management的總裁和Emerson執行副總裁;Charlie Cutler,他對先進過程控制APC進行再定義,成功開發商品化的多變量控制器,動態矩陣控制Dynamic Matrix Control(DMC)和實時優化Real-time Optimization(RTO);Odo Struger,他是PLC的命名者,同時在IEC 61131-3PLC編程語言標準編制過程中擔任領導角色;Ed Hurd 為商品化DCS的誕生發揮巨大作用,功不可沒。這里這里略去幾個ISA的創建者和組織者。
下面簡述這些堪稱里程碑的自動化技術。
半導體和摩爾定律
從大型計算機到嵌入控制器和傳感器內的處理器,如此巨大的計算技術的進展,全都植根于晶體管的發明。在1947年,貝爾實驗室的John Bardeen和Walter Brattain因此為人類的科學技術進步做出了史無前例的貢獻。無可辯駁的是,晶體管的發明是集成電路和微處理器開發成功的基礎。甚至今天運算能力最強的處理器芯片也是按其中封裝了多少晶體管的數量來測度的。 一直到1953年才有商品化的第一個低價的小信號PNP結鍺晶體管問世,型號是CK722,每只價格7.6美元。到1954年Texas Instruments 和另外一家公司合作開發了第一臺商品化的晶體管收音機Regency TR-1,那時標價為$49.95美元(大約相當于2019年的$476 )。 采用晶體管的工業用電子控制器大約在1950年誕生,此前氣動控制器從上世紀的20和30年代開始應用于工業現場,幾十年一直這樣在用著,直到晶體管出現后才發生很大的變化。 固態電子器件的成本實際上就是以低成本呈現更多功能和更多應用的歷史。這可以用經過時間檢驗的摩爾定律予以表達。仙童半導體的聯合創始人和曾任Intel CEO的Gordon Moore,在1965年的論文中首次定義集成電路中元件的數量每年要翻一番,而且這一增長率將延續到下一個十年。摩爾定律連續地推動計算技術的發展,這些被商用設備和工業設備的復雜和小型化所證實。由于高性能的電子器件和處理器的不斷進展,使得更小的體積和更低的價格成為可能,這才造就了物聯網IoT得以實現和普遍應用。
可編程邏輯控制器PLC
1970年誕生的第一臺PLC在通用汽車GM投用,對金屬切割、鉆孔、材料處理和裝配等環節進行控制。世界上首次推出的PLC的成功表現為兩個方面:一是用計算機來解析過去用繼電器實現的邏輯控制;二是采用梯形圖邏輯編程,使原來的電氣工程技術人員能在自己原有的技術基礎上采用計算機編程。 在PLC出現之前需要用大量的繼電器組成控制系統,既占據很大的空間,其可靠性又依賴于機電繼電器的可靠程度;一旦要對控制系統重新配置,不得不耗費許多時間重新接線。當時Richard Morley是Bedford公司的工程師,他率先創立了最初的設計,然后與他的團隊研制了工廠自動化和和連續處理應用的固態的順序邏輯解算器,這是第一臺實際可運用的可編程邏輯控制器,被命名為Modicon 084,因為這是Bedford公司第84個項目。1969年11月在得知GM公司的要求后,他們向公司的液壓部門展示了Modicon 084,獲得GM的青睞。 梯形圖邏輯編程極受電氣工程技術人員歡迎,其優點是不言而喻的。 這種由Bedford公司開發的梯形圖邏輯編程中相關的符號,來源于電氣工程中描述順序操作功能,這使廣大的電氣工程師和電工能以非常容易理解的方式對計算機進行編程。其發明人Morley在《Manufacturing System》1992年4月刊撰寫題為“梯形圖邏輯正在逐漸衰弱嗎?”論文中指出:“梯形圖邏輯作為一種控制語言第一次用在硅器件搭建的控制器上,大約在1969年,在Bedford Associates公司。為了支持這個控制語言構建了由三個部分組成的硬件平臺,即一臺雙端口的存儲器、一臺邏輯解算器和一臺通用計算機。早期在Modicon公司我們用了退化形式的梯形圖表達。這個語言最大的優點能被世界上所有從業的電氣工程人員理解。之后梯形圖擴展為多個節點,還附加了一些功能。梯形圖邏輯的功能性和PLC的適用性迅速在所有的工業中大量采用。” PLC在控制工業中廣泛運用,關鍵在于它對系統進行編程的能力。電磁繼電器構成的控制盤不具備同等的能力,一旦控制方案改變,必須對繼電器盤重新接線。而PLC面對控制方案的改變既方便又快速,同時體積也小許多。 在2007年ISA展會上有一個主題為《標準化會扼殺創新嗎?》的圓桌會議上,許多自動化系統的供應商都抵制具有互操作性的開放系統。對應當時會上的抵制,Morley發聲問道:什么工業需要開放系統?難道我們要放棄追求,重回以前專用的老路嗎?這振聾發聵的問話扭轉了會上的氣氛。現在13年過去了,開放系統正在變為現實。Morley作為ISA持有這種前向思維的自動化行業的輿論家和思想家,對推動工業自動化的發展起了巨大的作用。這一情節來自當時參加會議的一個年青工程師深情的回憶。
分布式控制系統(DCS)的架構
1975年Honeywell TDC 2000問世,開創了商品化DCS的歷程。這是世界第一臺采用微處理器執行流程直接數字控制的裝置,而且作為一個核心組成部分參與了整個系統的配置。在分布式控制器、工作站和其它計算部件之間用數字通信構成一個完整系統的架構,這在當時確實是革命性的創舉。在TDC 2000之前,基于計算機的流程控制系統主要用于數據采集和報警系統,而控制則由氣動回路控制器和獨立的電子PID控制器承當。 在70年代的中期日本橫河公司也將稱為Centum的分布式系統投入市場。橫河的Centum和Honeywell的TDC 2000都采用用小型監控計算機執行對若干個基于微處理器的多回路控制器進行監控的概念,而操作站采用按鈕和陰極射線管CRT的顯示器,替代以前的顯示報警盤(annunciator panel)。控制器之間的相互連接通過數據高速通道(data highway)傳輸來自不同節點和工作站的數據信息。高速通道或總線作為信號的通道,使控制器可以盡可能地靠近流程和裝置,使控制回路更緊湊,還降低了接線成本。 商品化的DCS的誕生,建立在從上世紀60年代開始的運用計算機技術對流程工業進行數字控制的探索的基礎上。那時主要是采用直接數字控制的概念,用小型計算機嘗試進行多回路的PID控制。之后開始考慮下一代的控制系統的綜合,也就是設計其架構。當時在Honeywell的工業自動化和控制部門工作的Ed.Hurd接受了第72號任務,擔任架構設計,兩年之后這一團隊導致了了TDC 2000成功推出。美國工業自動化界認為Hurd在促成DCS的架構上功不可沒。1976年在美國休斯敦的ISA展會上第一次展出了前所未有的DCS架構的產品。TDC 2000一經面世就大受歡迎,在5年內Honeywell的工業自動化和控制部門的產值由500萬美元發展到5億美元,翻了100倍。 此時在大洋彼岸的中國掀起了翻天覆地的變化,開始了改革開放的步伐。在1980年上海的第一屆多國儀器儀表展覽會上TDC 2000現身,引起無數中國的工業自動化從業者一片驚嘆聲。展覽會后這一臺展品被上海煉油廠買下,由上海工業自動化儀表研究所和上海煉油廠技術人員組成的團隊,成功將這臺DCS裝置運用到石油催化裂化工段,成為國內流程工業運用DCS的第一個里程碑。
人機界面(HMI)
人機界面的發展始于1975年Honeywell的TDC 2000誕生之時,從那時起操作員控制臺的發展步伐發生了顯著的改變。在流程工業中人機界面邁入了基于CRT顯示器的時代,操作人員可以在屏幕上讀取有關的流程變量,觀察變量隨時間的變化曲線,還允許他們發展一種圖像識別的方法來分析當前的操作運行狀態。不過那時的操作員控制臺是專用的,價格不菲。直到1985年以后,隨著個人計算機和DOS操作系統的逐漸普及,出現了第三方的圖形圖像軟件,涌現了一些以開發圖形顯示的新公司,其中包括Intellution、Iconics和USDATA。1987年Wonderware公司推出了世界第一個基于微軟Windows的HMI軟件包InTouch,增加了一些附加的性能和對IT技術和業務系統的開放接口。這可以說是人機界面的第三個里程碑。 Dennis Morin在1987年創建Wonderware公司,主導開發在Windows操作系統環境下的人機界面軟件InTouch,目標是讓操作人員能夠方便而有效率地監控操作過程。這一產品的推出標志著微軟的工業軟件革命,為第三方的開發者開啟了工業和流程控制系統的架構的轉向。在2003年InTouch雜志將Morin列為工業自動化的發展歷史上最有影響的50人中的一員。據他回憶,開發這種類型的軟件的靈感來自一個1980年早期的視頻游戲,游戲中允許玩家可用數字方法構建彈子游戲。
微軟的Windows
1985年問世的微軟Windows操作系統對工業自動化產生意義深遠的影響。Wonderware首創將InTouch軟件運行在Windows操作系統的環境下,引領了所有的工業自動化供應商,隨后都一致的采用了這一人機界面的解決方案。甚至在發展的初期,流程工業并不看好這一方案,認為并不適合流程工業的要求,但這一趨勢還是以優秀的性價比淘汰了DCS原有的專用操作員控制臺。 國內在90年代前后在當時的機械部儀表局籌措下,花大力氣自主開發國內的大型DCS,恰好處在這一人機界面的轉型期,這對此后DCS的開發產生重大影響。由于沒能抓住技術發展趨勢,仍然抱著專用操作員控制臺不放,最后沒能取得完整的成果。這不能不說是相當大的遺憾。由此反證了Windows操作系統對工業自動化的深遠影響。 Windows操作系統豐富的操作環境造就了大量的開發者在很寬泛的應用范圍中開發了大量的軟件,包括數據庫、數據分析、先進控制、制造執行系統MES、批量過程管理、制造跟蹤,以及歷史數據庫等等。 為了制造和生產取得更統一協調的結構,Windows操作系統在實時工廠運營與IT和業務系統之間架起了溝通的橋梁。這一平臺允許使用者運用標準的IT工具來提升分析制造數據,并使業務系統可以無縫地共享生產制造的信息。Windows操作系統為開發OPC提供了平臺,顯著簡化了工業網絡和設備界面的驅動程序。
歷史數據庫
按時間序列存放歷史數據在科學和工程上取得了大量有價值的應用,隨著歷史數據庫在PC機上也能付諸使用,促使這類數據庫在控制和自動化領域廣泛運用。OSIsoft原來是一個石油系統的公司,它推出了工廠信息系統,這就是大名鼎鼎簡稱PI的歷史數據庫系統。Patrick Kennedy在1980年創建這個公司,稱他為歷史數據庫之父也不為過。如今歷史數據庫在許多類型的制造業和流程工業成為一種改善生產率、提高效率和收益的重要工具。自動化工程師、運行操作人員和業務人員以許多不同的應用方式使用歷史數據庫。立于隨時間對連續數值的變化進行分析,并對過程控制加以改善的基本原理,如今歷史數據庫已經嵌入到控制器中以及云端的服務器中。 Kennedy是一個專業的化工控制系統的注冊工程師,享有連續重整催化控制系統的專利。多年的現場經驗使他深刻認識到,流程變量的歷史數據分析工具對改善流程的操作運行和提高收得率、降低原材料和能源的消耗有著重要的作用,萌發了開發歷史數據庫的靈感。多年的堅持使他終于獲得巨大成功。
開放工業網絡 將傳感器、控制系統和執行器連接在一起的開放型工業網絡,大大簡化了控制和自動化的應用。這標志著由不同供應商提供的設備和傳感器可以通過公用的通信接口構成工業控制系統時代的開始。隨著電子技術和通信技術的不斷進步,開放工業通信網絡也可以采用商業化技術,徹底擺脫了沿著專有化的道路緩慢前行。 從1979年開始Modbus首次打破堅冰,在RS 485標準的基礎上提升通信能力,將多個制造商的設備連成多播網絡。標準定義了用于多點串行通信系統發送端和接收端的電特性,使得各種設備諸如PLC、傳感器、儀表、PID控制器、電機驅動器和其它相關的設備都可以連接起來。直到今日Modbus仍在離散制造業、流程工業中有一定的應用。 從1980年到1990年出現了一系列的現場總線標準,主要有DeviceNet、Profibus、SERCOS、ASi(執行器傳感器接口)、FF(基金會現場總線)和HART(高速通信可尋址遠程傳感器)等。HART通信協議是其中唯一的在數字信號上疊加了模擬信號DC 4-20mA的數字、模擬混合的協議,其最著名的特點就是在一對雙絞線的傳輸線上共享了儀表的電流回路和數字通信信號。 在開發開放工業網絡的過程中不得不提到Emerson的執行副總裁John Berra,他在2002年獲得ISA頒發的終生成就獎,以表彰他長期專注儀表、系統和自動化社群,并作出重要貢獻。他在開發三個重要的工業制造通信協議HART、FF和OPC中發揮了很大作用。 無線短程網標準IEEE802.15.4開啟了無線傳感器網絡的發展 IEEE 802.15.4 低數據率無線短程網(low-rate wireless personal area networks ,LR-WPANs)標準和隨后開發的商用芯片,成為包括ISA 100a 和WirelessHART 在內的工業無線傳感器的標準。IEEE 802.15.4 是定義LR-WPAN操作運行的技術標準。2003年IEEE 802.15工作組開發了這一標準,并持續對不住進行維護。 ISA 100.11a (IEC 62734)無線網絡技術標準由ISA所開發,重點是針對流程控制和相關應用的工業自動化無線系統,即用于現場級的設備,2009年ISA自動化標準符合研究所成立了ISA 100無線符合研究部門,擁有“ISA 100符合”認證體系,為確保基于ISA 100產品真正符合標準,這是一個獨立的第三方的測試機構。WirelessHART(IEC 62591)是基于HART的無線傳感器聯網技術,專為流程工業的現場設備的要求所定義。WirelessHART 的一個目標是與現有的與HART兼容的系統和組態工具反向兼容,以達到將新的無線網絡與現存的HART儀表集成的目的。 由中國科學院沈陽自動化研究所為主開發的WIA-PA無線傳感器網絡技術,已被批準為中國國家標準(GB/T 26790.1-2011)和IEC國際標準(IEC 62601)。比較遺憾的是產業推廣不夠,應用面還不夠廣。
機器視覺和圖像識別
隨著價格的下降,加之得益于軟件技術(尤其是圖像識別)的進展而功能和性能更加完善,促使機器視覺系統的應用一直在增長。恰當組態和編程的視覺系統消除了人工的誤差、提高了生產能力、質量和效益。視覺系統變得具有高度智能,同時在控制自動化系統中靈活應用傳感器,擴大了實時控制的輸入范圍。視覺系統已應用于質量檢查、零件識別、機器人制導、工件輸送流動的機器控制等等。 剛開始應用時,常常是將一臺PC機與攝像頭相連接,由PC機完成圖像識別。如今都是將一臺采用IEC 61131-3標準編程的PLC和一臺具有圖像識別功能的機器視覺攝像頭集成,并直接裝在機械設備上。這都是因為計算機SoC芯片和小型化的視頻攝像芯片的急劇發展的結果。
ISA-88批量控制標準
ISA-88系列標準是專門針對廣泛應用于流程工業中的批量控制系統的設計和規范,在全世界持續地采用的結果證明,標準對提高生產率發揮了顯著的作用。ISA-88著重于實現批量過程控制的設計策略,描述設備和步驟可用于軟件的實現和手動的處理。系列標準的第一個標準在1995年被ISA所批準,而后在997年被IEC以IEC 61512-1的編號采納。 ISA-88位批量控制提供了一致性的系列標準和名詞術語,定義了物理模型、規程和配方。標準針對廣泛的需求,包括建立批量控制的通用模型、在通信發生困難時如何表達用戶要求的常用措施、批量自動化供應商之間的集成,以及簡化批量控制的配置。如今ISA-88已經成為溝通批量生產從產線、車間到企業管理系統一切所有方面的工具性的手段。 Tom Fisher長期在批量控制的企業擔任過程工程師,積累了豐富的批量控制和安全聯鎖系統的經驗。是他創建ISA-88專委會,為批量生產的標準化制定了開發的目標、方法和路線圖。他還是IEC的SC65A的批量控制工作組的領導人,世界批量論壇(World Batch Focus)的主席。他培養了一代批量過程控制的工程師。 深度介入ISA-88和ISA-95的還有Lynn Craig,為此做出了重大貢獻。他同樣也是長期在流程自動化現場和批量控制現場積累了豐富經驗的過程工程師,還有極高的系統思維素養。
ISA-95控制系統集成 企業控制系統集成標準闡述了從傳感器到企業管理系統之間的接口內容,目前在全世界被廣泛采用。工業4.0參考架構模型RAMI4.0中有一個維度就采用了ISA-95的分層結構。ISA-95增進了接口名詞術語的統一和一致性,減少了在將這些界面付諸實踐時可能帶來的風險,降低了成本和出錯因素。標準還有助于減少新產品投入生產時所花費的工作量。這個標準還提供了一致性的名詞術語和對象模型,這對于供應商和制造商之間的交流和通信是基礎性的。由于有助于定義企業業務管理系統和控制系統的邊界,ISA-95 模型清晰闡明了應用程序的功能性以及如何來使用這些信息。 在美國,ISA-95 又被稱為ANSI/ISA-95,這是因為美國的國家標準研究院在1976年就認定ISA為美國國家標準的一個制定單位。IEC采納ISA-95為國際工業標準,編號為IEC 62264。
ISA-95企業-控制系統集成標準B2MML
繼ISA-95在全球范圍內被很大范圍內的工業行業所接受,最新的發展是業務至制造的標記語言(Business to Manufacturing Markup Language,B2MML)建立了企業計算、云計算、IoT和工業4.0的兼容性。通過提供名詞術語和目標模型的一致性,以及IT與OT的溝通,B2MML進一步提升了ISA-95的附加價值。B2MML用XML模式的標準集合來表達ISA-95(IEC/ISO 62264)的數據模型,用3W的XML模式語言(XSD)編制XML模式的標準集合。 B2MML是ISA-95和IEC62264標準的XML的開源實現。MESA(制造企業解決方案聯盟)把B2MML用作事實上的接口標準,來交換ISA-95所定義的內容。B2MML還與OPC UA合作,用其作為框架為制造企業提供信息安全和可靠的架構。
電子游戲技術
游戲機產業正在推動計算技術的外部包裝,這也是工業自動化應用青睞的一個優點。原來為了發展視頻游戲的產業,目前正在影響著云計算、人工智能、數據科學,以及自動駕駛的運載工具。龐大的游戲機行產業的體量在2018年超過了1250億美元,這使得其在技術性能大幅提升的同時還能顯著地降成本下降。視頻游戲工業的硬件和軟件正在越來越多地引導著工業自動化的技術和業務用例。尤其是虛擬現實平臺和用戶界面正在以創造性的方式被引入工業自動化,例如虛擬現實眼鏡。 工業和流程自動化工業積極采納商用技術提高自身的應用水平,已經有許多年頭了,這一主流的趨向為實際的應用創造了巨大的價值。增強現實AR正加速進入日常生活,被用于從移動游戲到重工業等方方面面。這些創新的技術可在項目的每一個階段都起到支持輔助的作用,包括從設計、虛擬調試、生產裝置的開車啟動、故障定位和排除,以及質量控制。下面列舉一些應用這些技術獲得一定收益的例子:
機器和過程的仿真,包括虛擬調試、在安裝實際設備之前發現問題和瓶頸等等,都能夠做到節省金錢和時間。
智能眼鏡具有立即查看手冊、操作指令視頻和其它有關的材料,這有助于現場排除故障的工作人員查找問題。通過通信工具與處在遠程的專家聯系,取得他們的指導幫助。這對改善生產的正常進行有重要價值。
培訓仿真器為剛入職的裝置操作人員提供高效學習的手段。例如有許多的報道描述為被培訓的人員創建一種石化工廠的環境,并給予他們的一些挑戰性問題,使他們了解如何應對具有危險性的突發事件,并進行正確的操作。
OPCUA
采用面向服務架構(SoA)的OPC UA為工業自動化與最新的計算和IoT技術架設了溝通的橋梁。建立在面向應用的數據模型的基礎之上,使它提供的高質量而且前后相關、上下相關的數據。OPC UA是一種統一的技術,OPC基金會的成員涵蓋自動化、PLC、DCS、傳感器、工業軟件、企業資源規劃(ERP)以及云服務有關的組織和單位。目前它已成為IT和OT集成融合的一種關鍵技術。 OPC UA可用于任何一種操作系統,包括Windows、Linux、實時操作系統和專用操作系統。與現代的軟件實踐保持一致,OPC UA已處于開源狀態,通過開源托管網站GitHub可供公眾使用。 OPC UA正在成為一種統一的系統架構,為來自許多工業自動化專業的數據和信息進行高效率且效果良好的通信和交換。OPC基金會與不同的標準化組織共同努力建立了許多標準化的信息模型,這就是所謂的伙伴規范,或者叫做配套規范,從而達到從傳感器到企業的互操作性,而無需經過軟件層面對完全不同的或異構的系統進行轉譯和規范化。
機器學習
機器學習(ML)是人工智能一個分支,建立在系統可以從數據中學習的概念之上,通過數據進行圖像識別,或以最小的人工干預進行決策。機器學習正在加速應用于高性能低成本的硬件、低成本的數據采集、開源框架的大型程序庫和軟件模塊等方面,通過這些應用使機器學習在很大的范圍內獲得推廣應用。ML運用算法和統計模型來分析和預測未來的性能,無需為執行任務專門按要求明確的編程。 機器學習的迭代體很重要,因為一旦新的數據輸入模型,就會自動從先前的計算中去適應和學習,產生可靠、可重復的決策和結果。現今對大數據自動應用復雜的數學計算重復進行高性能、低成本的計算,正在推動ML的應用,例如:
汽車的自動駕駛
欺詐檢測
過去機器學習的應用必須從頭構建,現在最新的解決方案可在公共開源的框架內實現(例如TensorFlow、PyTorch、Sclikit-learn),這樣使之可能快速地建立應用。 運用機器學習的預測維護通過消除可能產生重大隱患的非計劃事件,避免造成生產線的停車事故,達到保證長時間無故障的運轉。采用監控設備和標準檢查模型和規則系統(benchmarking against models and rules system)可預測問題,同時提醒維護人員在發生一連串問題造成大的故障之前進行修復維護。另外在設備若干特定的部位加裝嵌入微處理器的傳感器,用來分析即將發生的問題,并發出需要加緊維護的報警信號。為了改善機器和過程的性能,機器學習也可以在閉環自動化控制中的策略環節運用。
工業4.0的倡議
工業4.0的重點在于應用一系列的新技術建立高效的自行管理的生產過程,通過運用工業物聯網IoT和開放的軟件和通信標準,將傳感器、控制器、人、機器、設備、物流系統以及產品統統實現直接通信和協同。德國的工業4.0的遠景規劃的思想對全世界長生了很大的影響,成為其他國家規劃工業長遠發展的樣板和參照模型。這其中包括“中國制造2025”、日本的“工業價值鏈倡議”、印度制造和美國的智能制造領導聯盟SMLC(Smart Manufacturing Leadership Coalition)。 工業4.0的核心理念是自動化系統必須采用開源的、由多個供應商提供、具有互操作性的軟件應用和通信標準,類似于在計算機、互聯網和移動通信已經采用的理念。工業4.0表述中所確認的現有的工業標準包括ISA-88批量制造標準、ISA-95企業和控制系統集成標準、OPC UA、IEC61131-3,以及PLCopen國際組織的相關規范。 工業4.0最初是作為德國在2006年建立的德國10點高技術策略計劃中的一部分。2010年7月14日德國的內閣決定通過引入高技術策略2020規劃繼續這一策略,著重于選擇具有前瞻性的科學技術的發展,制定10到15年的研究創新策略。工業4.0就是通過提升計算技術、軟件和互聯網技術來實現集成工業、互聯工業的遠景規劃。所謂4.0就是指第四次工業革命。德國強調加強工業與科學的合作,推進知識與技能的緊密結合。工業4.0的愿景是通過把人員、機器、設備、物流系統和在制工件彼此間直接通信的辦法實現顯著高的生產率和高效率,以及自管理的生產過程。其中一個大目標是充分發揮嵌入式的處理和通信的作用,使得定制生產也具有低成本的規模制造的效率。制造過程和物流過程跨越公司的邊界進行智能集成,建能夠成一種更有效率、更靈活的實施精益制造的生態系統。
數字孿生
數字孿生已經成為工業4.0最強有力的概念之一。通過整個制造和生產過程基于模型、實時、云回路監控、控制和優化的實現,數字孿生有助于達到實時集成制造的組織實施。數字孿生的基本概念是要建立一個理想的制造操作運行和處理的虛擬模型。這個模型將是實時而全面表達實際生產狀況的基準。最廣泛的實現模型包括所有影響生產的效率和盈利能力的因素,這里涵蓋機器、過程、人力資源、原材料的質量、訂單流和經濟因素。生產組織可以利用信息的價值來識別和預測問題所在,使得高效的生產得以維系,而所有可能影響和中斷生產的問題,都能在在發生之前被發現和解決。 由于運用了先進的硬件、軟件、傳感器和系統技術,數字孿生作為一個實際的宏觀級別的閉環控制的杰出實例就變得可行了。創建數字孿生的關鍵部分是需要一個完整的信息集合,包括根據建模的要求部署大量而廣泛的傳感器采集實時信息。實際上工業4.0就是運用包括工業物聯網在內的最新技術,將制造系統和業務系統集成為一體的廣泛應用。
云計算和邊緣計算
云計算正在影響著包括工業自動化在內的方方面面的應用,這是因為它提供了易于使用、計算和存儲能力出眾,且具有高性能等諸多優越性,而所有這些都是在不要求巨大的投資,或者在不要求目前已經負載過重的自有計算機和服務支持的前提下進行的。云計算和服務的提供者有像微軟的Azure和亞馬遜的AWS等這樣的公有云,他們有許多各種各樣的軟件工具,例如數據分析和預測的軟件工具,這些都可以為廣大的工業部門和流程自動化裝置所利用,來解決和應付制造、生產和業務的挑戰。許多工業自動化的應用,諸如歷史數據、基于狀態的監控、預測維護、資產管理和故障分析等,目前都在運用云計算的方法,已經獲得了更好的性價比。 云計算在提升共享資源和規模經濟性方面類似于公用的電網,可以提供幾乎沒有限制的計算能力,并且可以按照需要提供數量巨大的存儲量。另外,邊緣計算正在變得普遍起來,這是一種低成本、高性能計算和通信的部署方法,導致計算和數據存儲盡可能靠近產生數據的源頭,這樣來改善響應時間,增強數據與其生成源頭的前后關系和相互關系,同時可按要求就地執行,而無需往返云端與就地。在計算機和工業自動化應用的歷史上,處理計算往往都被放置在遠離網絡邊緣的地方。直到今天還有許多應用還在這樣做。現今的邊緣設備可以是一臺小的定位節點的計算機,或者是嵌入在傳感器、執行器和其他設備中的SoC,具有特別高的性價比。將這些邊緣設備部署在就地,使他們像移動的智能手機一樣具有強大的計算能力和不高的成本。 這些計算設備可視作為一種平臺,其中可執行許多不同功能的軟件,包括IoT、基于IEC 61131-3的PLC、OPC UA和MQTT,還有與云端的接口、時序數據庫、HMI以及數據分析軟件。ISA-95 從L0到L2的功能和L3的部分功能,再加上新的IoT的分布式計算模型,都可以在邊緣設備中執行。 將工業傳感器網絡與邊緣設備連接的方案得到越來越多的認可和接受,今后在開放式的系統中會有較多的應用來取代PLC和DCS控制器。將邊緣設備部署在工業網絡聯網和企業網絡聯網之中,其通信的功能有助于無縫地將IT與OT集成。
協作機器人
協作機器人是一種新出現的輕型且價廉的機器人,在生產環境中與工人協同地工作。這是一種實現靈活制造的新方式,無需對生產場地和流程進行大的改動,也不需要很大的投資。協作機器人應該是本質安全的,它們能感知人和其他障礙,并自動停下來,這樣就不會發生傷害和損壞的事故。不要求保護柵欄和保護籠,既增加了靈活性,又降低了成本。 協作機器人特別吸引中小型企業的投資,這類機器人的編程過程也很簡單,不要求編程的老手。這類機器人可以仿照使用案例編程,或者用類似于游戲的方法編程。大多數任務不用熟練的編程人員,只要簡單地移動機器臂和末梢執行器,對機器人進行示教操作,機器人便將這些運動動作記憶下來,程序就此創建。這就是所謂的大眾化電腦“所見即所得”編程的物理形式。對于用戶來說,關鍵是憑藉直覺獲得編程的結果。簡化編程意味著協作機器人不必聘用專業工程師便可部署。 這一類新型機器人的開發類似于在PC機問世以后如何擴展計算機的應用。剛開始計算機很貴,只能放置在專用的房間由軟件專家來編程,寫出在一般人看來是很神秘的代碼。因為實現的成本很高,應用面不廣。直到PC機導入之后,盡管它的運算能力和存儲容量遠不如大型計算機和小型計算機,但它價格低,又靈活,才使計算機的應用面大為擴展,人們得以在很寬泛的范圍內應用計算機去解決許許多多的問題。這一因素再加上簡化了編程,導致計算機在工業自動化領域的應用產生了革命性的變化。 這些新型的協作機器人不能抓起一臺發動機,但可以完成大量不同種類的任務,能承受負載一般在10-30公斤。協作機器人可以完美地替代操作工完成重復的、平常的和有危險的任務。操作工不再被迫在機器前站立幾個小時干那些乏味的工作,或者在有危險的環境下工作。這既提高了生產效率,又提高了工作質量,而操作工也從繁復的勞動中解放出來,去干那些要求熟練技工才能完成的任務。 協作機器人是增長最快的自動化部門,根據美國機器人工業協會RIA的預測數據,到2025年協作機器人將在工業機器人中的份額躍居到34%。將協作機器人與視頻系統、圖像識別和人工智能結合起來,可以完美重復人工的制造的過程,這一進展相當令人興奮。 協作機器人大大降低了自動化的壁壘,有相當大的范圍內的用戶,特別是中小型企業用戶,即使缺乏高度熟練的自動化人才,也能夠采用和駕馭協作機器人。而協作機器人的靈活性使得過去難以采用的許多自動化功能現在都變得容易解決了。由于編程簡易方便,一臺協作機器人可以完成許多不同的任務,所以特別適合按訂單要求制造的生產過程。
先進過程控制發展的推動者
在流程工業中鼎鼎大名的美國Aspen公司是Larry Evans創建的。他原是麻省理工學院化工系的教授,也是ASPEN項目的主要研究者。這個項目的目的是開發第三代的流程建模仿真系統,用于在技術和經濟兩方面評估合成燃料的過程。1981年在這個項目完成之后他和項目中7個關鍵的成員創建了Aspen Technology公司,從MIT取得該技術的應用許可,并進一步對此項技術進行開發、支持和商業化。作為AspenTech的CEO,在接下去的多年中他擴展和深化了該技術,使得建模仿真技術成為可在相當寬的范圍內應用的相互補充的產品。公司也由10個人發展成為上市的公司。 Charlie Cutter原來是美國國家工程院的成員,他發明了高度成功的多變量控制器,并完成了了其商業化的進程,成為重新定義先進過程控制(APC)的首創者。他是化工工程師出身,長期在殼牌石油公司工作。他所構思并付諸實現的動態矩陣控制算法,為石油化工工業節省了成百萬上千萬美元的開銷。1984年他創建了DMC公司,即動態矩陣控制公司。以后有成立了第二家名為Cutler Technology Corporation的公司,運用動態矩陣控制(DMC)和實時優化(RTO)技術,在當代的石油天然氣工業的控制工程應用中居于有競爭力的前沿位置。2000年因對新一類的先進過程控制的貢獻被遴選為美國國家工程院院士。 Karl ?str?m是瑞典的控制理論家,他對控制理論、控制工程、計算機控制和自適應控制都做出很大貢獻,常被人稱為自適應之父。在1965年他提出了在信息不完全的情況下馬爾可夫決策過程(MDP)的框架,導致產生了部分可觀察馬爾可夫決策過程(POMDP)的概念。POMDP模型是一種智能體決策過程,假定系統的動態過程有一個馬爾可夫決策過程,但是智能體不可直接觀察到底層狀態。取而代之的是必須基于一個觀察集合和觀察的概率以及底層的MDP,維持在可能狀態集合傷的概率分布。POMDP框架足夠為各種各樣的實時世界的序貫決策過程建模。其應用包括機器人的導航問題、機器維護和存在不確定因素下的總體規劃。Leslie P. Kaelbling和Michael L. Littman將此理論推廣并適應于解決人工智能問題和自動規劃。
責任編輯:lq
-
數據庫
+關注
關注
7文章
3845瀏覽量
64581 -
工業自動化
+關注
關注
17文章
2471瀏覽量
67331 -
協作機器人
+關注
關注
2文章
496瀏覽量
30186
原文標題:20個工業自動化的里程碑
文章出處:【微信號:vision263com,微信公眾號:新機器視覺】歡迎添加關注!文章轉載請注明出處。
發布評論請先 登錄
相關推薦
三星電子1c nm內存開發良率里程碑推遲
三星1c nm DRAM開發良率里程碑延期
破萬億!中國芯片出口迎來里程碑
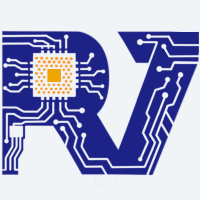
e絡盟實現重要里程碑:成功分銷 1000 萬套 micro:bit 設備
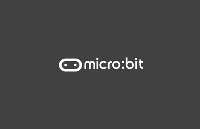
比亞迪達成新能源汽車下線千萬輛里程碑
江森自控推出EasyIO Neo Series樓宇自動化新系統
黑芝麻智能與Nullmax達成重要合作里程碑
特斯拉里程碑達成:第1億顆4680電池震撼問世
Waymo自動駕駛里程碑:Alphabet引領未來出行新篇章
特斯拉迎來里程碑:全球第1000萬個電驅系統下線
國產通信衛星新里程碑:亞太6E全電推衛星正式運營
工業自動化和自動化區別是什么
捷科智誠成功中標某大型國有銀行的自動化測試平臺項目
它人機器人與俄羅斯的AVIALIFT正式攜手,達成里程碑式合作
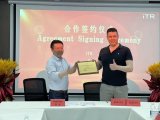
評論