埋嵌元件基板由于元器件的三維配置而使PCB或者模組小型化,縮短元件之間的連接路徑,降低傳輸損失,它是可以實現(xiàn)便攜式電子設(shè)備多功能化和高性能化的安裝技術(shù)。鑒于此,本文主要概述了埋嵌元件PCB的元件互聯(lián)技術(shù),以及對埋嵌元件PCB的評價解析。
1 前言
埋嵌元件基板由于元器件的三維配置而使PCB或者模組小型化,縮短元件之間的連接路徑,降低傳輸損失,它是可以實現(xiàn)便攜式電子設(shè)備多功能化和高性能化的安裝技術(shù)。多層板中埋嵌LSI或者無源元件方式的埋嵌元件基板從2003年開始采用,從2006年開始正式用作高功能便攜電話或者用于表用的小型模組基板。這些基板分別采用了元件制造商和PCB制造商獨(dú)自開發(fā)的特征構(gòu)造和工藝。本文就參考日本電子電路工業(yè)協(xié)會(JPCA)的規(guī)格中埋嵌方式的埋嵌元件基板技術(shù)的分類,采用的元件和安裝技術(shù)和評價解析等加以介紹。
2 埋嵌元件基板技術(shù)的分類
埋嵌元件基板大致分為埋嵌個別制造的元件的方式和在基板上形成直接元件的方式。本人只限于前者方式的技術(shù)。圖1表示了埋嵌型的埋嵌元件基板按照嵌入元件的安裝方式的分類。PCB上的元件安裝方式大致有焊盤連接方式和導(dǎo)通孔連接方式兩大類。
圖2表示了焊盤連接方式和導(dǎo)通孔連接方式的代表性制造工藝。
在焊盤連接方式中,首先在基板上形成的電極上安裝嵌入的元件并進(jìn)行電氣連接。連接完成以后采用絕緣樹脂同時填充和埋沒元件和電極。連接時采用現(xiàn)有的表面安裝技術(shù)。連接材料采用焊料或者導(dǎo)電膠。嵌入元件的安裝:元件為裸芯片時選擇裸芯片粘結(jié)(Die Bonding);元件為無源元件或者模塑封裝(Mould Package)或者WLP(Wafer LevelChip Scale Package)時安裝選擇(Mounting):裸芯片的倒芯片連接(Flip Chip Bond)采用超聲波接合、C4(Controlled Collapse Chip Connection控制熔化高度芯片連接)、ESC(Epoxy Encapsulated SolderConnection環(huán)氧樹脂囊包焊接)、導(dǎo)電性樹脂和各向異性導(dǎo)電樹脂(ACF/ACP,Auisotropic ConducliveFilm /Anisoropic Conductive Paste)和非導(dǎo)電性樹脂(NCF/NCP,Non Conductive Film / Non CondctivePaste)等安裝技術(shù)。無源元件的連接采用焊料再流焊或者導(dǎo)電性樹脂。焊盤連接方式中由于元件連接采用傳統(tǒng)的表面安裝技術(shù)而具有有效利用現(xiàn)有制造設(shè)備的優(yōu)點(diǎn)。另外,由于實施了元件安裝連接以后和埋嵌以前的檢查,所以可以對安裝過程中發(fā)生的不良品進(jìn)行篩選或者修理和返工。
導(dǎo)通孔連接方式中,PCB和元件進(jìn)行電氣連接以前采用絕緣樹脂埋嵌元件。元件埋置以后,覆蓋元件電極的樹脂上進(jìn)行激光加工,形成導(dǎo)通孔以后采用鍍層填充導(dǎo)通孔,進(jìn)行PCB與元件的電氣連接。導(dǎo)通孔連接方式的特征是元件的電極上接合直接鍍銅(Cu)層。由于沒有介入表面安裝中使用的焊料或者凸塊那樣的接合部,所以期待著與多層板的內(nèi)部線路同等的低連接電阻和高連接可靠性,另外還可以采用全層IVH(Interstitial Via Hole)使用的導(dǎo)電膠進(jìn)行導(dǎo)通孔連接,與多層板的層間連接同樣的導(dǎo)電膠用于與元件的連接,采用同時進(jìn)行埋置和連接的匯總積層工藝可以簡化工程復(fù)雜的元件埋嵌基板的制造工藝。
上面介紹了按照埋嵌元件的安裝技術(shù)分類的埋嵌元件基板的種類和大致的制造工藝。下面參照迄今的開發(fā)事例介紹埋嵌元件基板的制造中采用的各種安裝技術(shù)。
3 焊盤連接方式的埋嵌元件基板
焊盤連接方式中在內(nèi)層基板上安裝元件以后,采用絕緣樹脂埋置。嵌入的元件分為裸芯片(Bare Die)和其它元件,下面介紹連接用的表面安裝技術(shù)。
3.1 裸芯片粘結(jié)方式
圖3表示了利用倒芯片安裝嵌入裸芯片的工藝。
圖3(a)表示在裸芯片的電極上形成金(Au)堆積凸塊。使用NCP與PCB的電極進(jìn)行加熱加壓連接的方式。PCB的電極表面上沒有進(jìn)行鍍金(Au)或者鍍錫(Sn)等,而是原本的銅(Cu)。銅(Cu)表面上施行粗化處理,旨在提高與樹脂的附著力。加熱加壓連接時,接合部必須維持壓縮應(yīng)力,對于提高連接可靠性至關(guān)重要。圖3(a)中著眼于NCP的熱機(jī)械特性,選擇高彈性和高膨脹系數(shù)的樹脂可以獲得充分實用的連接可靠性。
另外還有使用ACP代替NCP的熱壓連接的安裝方法。在裸芯片的鋁(Al)電極上形成金(Au)球凸塊以后,涂布底膠ACP,實施加壓加熱,即可電氣連接。接合可靠性與NCP時同樣取決于底膠樹脂的物理性能。圖3(b)表示了使用銀(Ag)膠凸塊和ACP的連接方式。PCB的電極上印刷銀(Ag)膠形成銀(Ag)凸塊,涂布底膠ACP使用倒芯片粘結(jié)器熱壓接合。裸芯片的電極上沒有形成銅(Cu)或者金(Au)凸塊而是采用鋁(Al)進(jìn)行熱壓連接。
圖3(b)的熱壓連接銀(Ag)膠凸塊的連接技術(shù)在積層板中已經(jīng)量產(chǎn)化,它是應(yīng)用了利用導(dǎo)電性凸塊的層間連接技術(shù)(B2it,Buried Bump InterconnectionTechnology)。
圖3(a)和(b)與多層板制造技術(shù)相組合的元件嵌入基板的實用化比例,利用NCP和ACP的元件連接技術(shù),采用導(dǎo)電性凸塊進(jìn)行層間連接。制造利用導(dǎo)電性樹脂凸塊連接的雙面板,在內(nèi)層上安裝元件以后,與外層的基板組合在一起加熱加壓而埋入元件,同時采用凸塊使線路層間匯總連接。采用元件埋入以前進(jìn)行線路形成的工藝有利于減少不良率和提高生產(chǎn)性。
3.2 芯片安裝方式
圖4表示了印刷焊膏的內(nèi)層的基板上采用芯片安裝器(Chip Mouuter)搭載元件并采用再流焊工藝熔融焊料的連接方式。采用使LSI WLP化的芯片安裝(Chip Mounting)和再流焊工藝同時的搭載和連接有源元件和無源元件。它是模型封裝的LSI或者模組等大多數(shù)通用元件可以采用的嵌入技術(shù)。采用焊接連接嵌入元件時,由于基板表面上安裝元件的模組基板第二次安裝到母板上,經(jīng)過再度再流焊工藝時擔(dān)心焊料凸塊(焊料球)熔融而影響到導(dǎo)通和絕緣特性。因此采用樹脂覆蓋焊料的周圍,抑制再熔融產(chǎn)生的流動,從而可以避免上述問題。
4 導(dǎo)通孔連接方式的元件埋嵌基板
導(dǎo)通孔連接方式中,元件嵌入以后進(jìn)行與基板的連接。有源元件和無源元件的全部元件的電極視為內(nèi)層的線路圖形,利用積層技術(shù)在元件上部形成線路層。
4.1 裸芯片粘結(jié)方式
嵌入的LSI WLP化,采用銅(Cu)線路引出WLP化的電極,擴(kuò)大了電極間節(jié)距,實現(xiàn)了與現(xiàn)有PCB加工工藝親和性高的埋入工藝。另外由于WLP化而確保良好的裸芯片(KGD,Known GoodDie)。相對與連接以后元件難以修理的導(dǎo)通孔連接方式來說具有很大的優(yōu)越性。
圖5表示了代表性的導(dǎo)通孔連接方式的有源元件嵌入技術(shù)的制造工藝。嵌入的LSI WLP化,形成銅(Cu)線路和銅(Cu)凸塊,施行樹脂涂復(fù)。薄片化的裸芯片背面粘貼裸芯片附著膜(DAF,DieAttachment Film)以后進(jìn)行位置重合,在基板上面朝上粘結(jié)。半固化片和表層基板積層,加熱加壓以后使裸芯片嵌入。在嵌入的WLP的電極位置上從基板表面進(jìn)行激光加工,形成導(dǎo)通孔以后采用鍍層填充導(dǎo)通孔,連接WLP的電極和基板的線路。由于裸芯片的表面由樹脂保護(hù),所以在嵌入加工工程中可以減少損傷或者污染等方面的危險。
圖6是導(dǎo)通孔的材料使用導(dǎo)電膠的方式。使用多層板的層間連接所用的銅(Cu),銀(Ag)和燒結(jié)合金等材料,通過壓接或者金屬結(jié)合而連接元件。
圖6表示了在聚酰亞胺多層板上嵌入經(jīng)過背面研磨而薄型化的WLP例。嵌入的LSI經(jīng)過WLP加工使電極的節(jié)距擴(kuò)大到與PCB的導(dǎo)通孔同樣的節(jié)距,厚度達(dá)到0.1 mm以下的薄型化。基板上形成的導(dǎo)通孔填充未固化的導(dǎo)電膠,基板/WLP和隔板(Spacer)/基板積層,一次加熱加壓。加熱過程中依次進(jìn)行導(dǎo)通孔中填充的導(dǎo)電膠固化,粘結(jié)材的流動和固化,同時完成了PCB/WLP之間的電氣連接和嵌入粘結(jié)。利用導(dǎo)電膠導(dǎo)通孔的一次積層法中,由于在PCB的積層與元件的嵌入以前已經(jīng)形成全層的線路,所以具有降低元件嵌入以后所發(fā)生的不良率的優(yōu)越性。為了使該工藝適應(yīng)將來的LSI的多針化,與裸芯片連接的導(dǎo)通孔節(jié)距的微細(xì)化是今后的課題。
4.2 芯片安裝(Mounting)方式
圖7表示了使用激光導(dǎo)通孔加工和鍍層連接的元件嵌入工藝。把嵌入的元件置于基板的一部分上設(shè)置的空腔(Cavity)內(nèi),然后用樹脂填充而嵌入元件。使用厚銅(Cu)芯的基板,利用銅(Cu)的蝕刻形成空腔。芯板一面上貼附樹脂片,堵塞空腔的一側(cè)以后,在它的底面上固定元件。空腔的開口側(cè)積層樹脂片并進(jìn)行加熱,空腔內(nèi)壁與元件的間隙用樹脂填充使元件固定。嵌入元件的電極上的樹脂形成激光導(dǎo)通孔開口。采用半加成法形成基板表層線路的同時采用鍍銅(Cu)層填充導(dǎo)通孔。基板正反面的連接,空腔形成時預(yù)先在銅(Cu)芯的一部分開口,充填樹脂以后采用激光形成貫通孔。采用該技術(shù)的基板具有優(yōu)良的導(dǎo)熱性,尤其是嵌入發(fā)熱量多的元件時具有高散熱性的特征。
圖8表示了利用一次積層法的元件嵌入工藝的概念圖,作為利用導(dǎo)電膠的一次積層法的無源元件埋入技術(shù),Ag-Sn系合金材料用于導(dǎo)通孔,LCP用作絕緣材料。配置元件處形成空腔的單面板積層規(guī)定的枚數(shù),與此同時元件插入空腔以后進(jìn)行加熱加壓。導(dǎo)通孔內(nèi)填充的由Ag和Sn構(gòu)成的膠材料由于加熱而燒結(jié),與此同時Sn擴(kuò)散到線路板和元件的Cu電極上形成金屬結(jié)合。熱可塑性材料LCP(Liquid CrystalPolymer)由于加熱而軟化,使基板之間接合,與此同時流入到元件與空腔的間隙而嵌入元件。加熱加壓過程中由于樹脂的流動影響到導(dǎo)通孔形成,元件與小型基板的間隙附近存在導(dǎo)通孔時,樹脂流通的精確控制對于確保連接可靠性至關(guān)重要。
5 嵌入用元件
焊盤連接方式時,嵌入可以采用再流焊或者粘結(jié)劑等表面安裝技術(shù)的大多數(shù)元件。為了避免板厚的極端增大而要使用元件厚度小的元件。裸芯片或者WLP情況下,它們的大多數(shù)研磨了硅(Si)的背面,包括凹塊等在內(nèi)的安裝以后的高度為(300~150)mm以下。無源元件中采用0603型,0402型或者1005的低背型。導(dǎo)通孔連接方式時,上面介紹的鍍層連接和導(dǎo)電膠連接的各種事例都是采用Cu電極的元件。用作嵌入元件時銅(Cu)電極的無源元件厚度150 mm成為目標(biāo)之一,還有更薄元件的開發(fā)例。
6EPASD 評價解析T V (TestVehicle)
6.1 測試運(yùn)載工具(TV)概要
以闡明元件嵌入PCB的技術(shù)課題為目的,制作了評價解析***TV(Test Vehicle)并進(jìn)行了評價。從2007年再次關(guān)于構(gòu)造和設(shè)計的討論,最終制作了如圖9所示的裸芯片嵌入基板的構(gòu)造。線路層為4層,L2~L3之間嵌入元件。根據(jù)元件嵌入PCB的用途,初期應(yīng)該相同于HDI基板的評論,而提出元件嵌入特有的課題被視為最本質(zhì)的問題,嵌入部分以外極為容易的優(yōu)先制造,層間連接為貫通孔。分別使用無鹵FR-4和FR-5基材進(jìn)行制造。
嵌入的元件是由SIPOS(System IntegrationPlatform Organization Standard)提供的“SIPOSTEG”,形成與PCB連接的菊鏈?zhǔn)綀D形那樣的焊盤配置。圖10表示了這種圖形和主要規(guī)格。其中電極上形成金(Au)螺拴形凸塊(Stud Bump),采用面朝下(Facedown)的倒芯片連接的安裝方式。這時采用熱壓接合法和超聲波法2種方法。因此制作成兩種材料和兩種安裝方式的共計4種樣品。
6.2 評價結(jié)果
2008年實施了TV制作,2009年度進(jìn)行了評價解析。首先為了評價再流焊耐熱性,采用JEDEC3級的條件實施前處理。許多樣品再流焊以后發(fā)生起泡。
另外還伴隨著發(fā)生斷線或者電阻上升。
圖11表示了截面解析的一例。嵌入的芯片下方的底膠樹脂與芯片之間發(fā)生剝離,部分剝離發(fā)生在螺栓形凸塊與PCB電極界面。這種剝離是起泡的發(fā)生原因。耐熱性的FR-5也發(fā)生若干起泡。由于四種條件中沒有顯著差別。所以認(rèn)為發(fā)生起泡的主要原因在于構(gòu)造本身。根據(jù)截面解析的結(jié)果芯片本身顯著翹曲,由于嵌入以后內(nèi)在的殘留應(yīng)力在再流焊時被釋放而發(fā)生變形,或者由于芯片本身的尺寸或者PCB圖形的影響等。關(guān)于翹曲方面,在內(nèi)層板上安裝時由于芯片與內(nèi)層板的熱膨脹系數(shù)差別而表現(xiàn)出凸?fàn)盥N曲,但是如圖11所示的起泡以后的截面中反而逆轉(zhuǎn)為凹狀翹曲而值得注意。
發(fā)生起泡的評價本質(zhì)上是由于爆玉米花(Popcorn)現(xiàn)象引起的,使用不同的兩種底膠樹脂的安裝方式都發(fā)現(xiàn)同樣的起泡,因此認(rèn)為PCB構(gòu)造有很大影響。為了調(diào)查這種現(xiàn)象,第二次制作了TV-1′芯材厚度為0.1 mm和0.3 mm,導(dǎo)體圖形有TV-1采用的銅(Cu)中間(Beta)圖形和PCB的網(wǎng)且(Mesh)圖形兩種。共計四種樣品。圖12表示了TV-1′PCB的導(dǎo)體圖形和層構(gòu)造。各種構(gòu)造實施了5次再流焊耐熱試驗,與TV-1′同樣構(gòu)造的芯材0.1mm/Cu中間圖形再現(xiàn)起泡現(xiàn)象,而其它構(gòu)造都沒有發(fā)生起泡或者電阻上升,確認(rèn)了構(gòu)造變更的效果。
6.3 熱變形解析
為了考察基材的厚度或者線路導(dǎo)體圖形給予元件嵌入PCB的熱變形行為的影響,利用模擬迄今獲得的試驗結(jié)果進(jìn)行解析。根據(jù)前節(jié)敘述的EPADS TV的Geber數(shù)據(jù)制成三D模型(Model),通過解析從室溫加熱到260 ℃時的熱變形行為而求得。解析時使用ADINA8.6(美國ADINA公司制造)進(jìn)行非線性的彈性解析。解析以TV-1′為標(biāo)準(zhǔn)。基材厚度為0.1 mm和0.3 mm兩種,PCB的導(dǎo)體設(shè)定為銅(Cu)中間圖形和網(wǎng)目圖形兩種,實施共計組合成四種的解析。制成的模型如下。
(a)模型1 芯材0.1 mm厚/網(wǎng)目圖形。
(b)模型2 芯材0.1 mm厚/中間圖形。
(c)模型3 芯材0.3 mm厚/網(wǎng)目圖形。
(d)模型4 芯材0.3 mm厚/中間圖形。
另外嵌入的芯片為0.1 mm,厚度10 mm□,與TV同樣的周邊配置金(Au)凸塊和下面填充底膠樹脂的構(gòu)造。實際的制造狀況有所不同,在解析中室溫下的應(yīng)力和變形設(shè)定為0,求出加熱到260 ℃時的熱變行為。圖13表示了熱變形解析結(jié)果的一例。途中的PCB L1表示上面的,裸芯片嵌入部分的中心部表現(xiàn)出凸形狀變形的傾向。它的周圍收到裸芯部嵌入部變形的影響。變形行為隨著部位而有所不同,這是由于導(dǎo)體圖形的形狀和疏密的影響所致。解析的四種模型中。模型2相當(dāng)于TV-1發(fā)生起泡的構(gòu)造。
解析所獲得的熱變形量以模型2為最大,表現(xiàn)出與實際基板同樣的傾向。模型2的變形量為108 mm,其它模型的變形量范圍為46 mm ~ 60 mm.
6.4 與熱變形實測的比較
為了驗證熱變形解析的準(zhǔn)確性,進(jìn)行了熱變形行為的實測。樣品制造成TV-1′,構(gòu)造相當(dāng)熱變形解析的模型1~模型4供給試驗。根據(jù)莫瑞光影法(Shadow Moire)的非接觸翹曲測量一邊加熱到最高260 ℃一邊進(jìn)行測量。圖14表示了室溫初始狀態(tài)下翹曲分布圖。與解析結(jié)果相反,由于L4側(cè)具有凸?fàn)盥N曲,所以在上面配置PCB L4.由于這種翹曲方向?qū)?yīng)于圖11中表示的起泡以后芯片翹曲方向,所以芯片在嵌入時和安裝時表現(xiàn)出不同的翹曲。
從室溫初始狀態(tài)到260 ℃一邊升溫一邊進(jìn)行數(shù)點(diǎn)的測量,確認(rèn)了室溫初始狀態(tài)時翹曲小的傾向,即L1側(cè)表現(xiàn)出翹曲行為,這一點(diǎn)與模擬的傾向一致。以室溫初始狀態(tài)的翹曲量為基準(zhǔn)求出L1測變位量,表1表示了它與模擬結(jié)果的比較結(jié)果。厚度0.1 mm的構(gòu)造中實測結(jié)果大大超出模擬結(jié)果的變形量。特別是模型2中呈現(xiàn)出很大剝離,雖然外觀沒有確認(rèn),但是也有可能發(fā)生微細(xì)的層間剝離。然而厚度0.3 mm的構(gòu)造中,實測結(jié)果與模擬結(jié)果比較一致,表明元件嵌入PCB的熱變形預(yù)測是有效的。0.1 mm厚度的構(gòu)造中兩者的剝離點(diǎn)今后還有研究的余地,可以采用彈性解析預(yù)測熱變形行為,在工業(yè)上比較有用,期待著有助于元件嵌。
7 標(biāo)準(zhǔn)化WG中無源元件嵌入的課題
圖15表示了無源元件嵌入構(gòu)造的三種代表性形態(tài)。這種形態(tài)已經(jīng)有10年左右的實用化,其優(yōu)點(diǎn)是可以使用特性保證的元件,可以使用現(xiàn)有設(shè)備進(jìn)行制造。
另一方面,對PCB的市場要求是“更薄”。特別是模組元件中“低背化”是重要的關(guān)鍵詞。因此第一要求嵌入元件特別是無源元件芯片的低背化。由于元件制造商的開發(fā)努力,已經(jīng)實現(xiàn)0.15 mm厚度(1005尺寸,0603尺寸)的薄型化。另外PCB本身也要求成品板厚的薄型化,但是由于為了實現(xiàn)高集成度的線路,不得不增加厚度,因此希望使用更薄的內(nèi)層芯板,部分嵌入銅(Cu)箔的0.05 mm左右的內(nèi)層芯板也已經(jīng)實用化。在表面安裝時的再流焊工程或者基板制造工程中存在處理困難的擔(dān)心。根據(jù)這種狀況,近年來采用圖15(b)所示的導(dǎo)通孔連接方式。這種方法是在內(nèi)層上安裝的元件電極上進(jìn)行直接線路板的導(dǎo)通孔連接的方式(有源元件情況下面朝上)。采用這種方式,元件安裝只有安裝(Mount)工程,與再流焊方式比較,簡化嵌入工藝的同時降低了成本,然而為了實現(xiàn)這種方式正在提出若干技術(shù)課題。EPADS研究會的標(biāo)準(zhǔn)化WG中正在進(jìn)行討論。
第一是確保導(dǎo)通孔與元件外部電極的位置精度,它的影響因素如下。
(1)外部電極尺寸。目前的0603尺寸通用品中外部電極幅度為0.10 mm ~ 0.15 mm左右。一般PCB中激光導(dǎo)通孔內(nèi)層焊盤徑為φ0.20 mm左右。這樣導(dǎo)通孔的一部分有可能偏離電極。
(2)元件安裝精度。現(xiàn)在的安裝機(jī)中一般安裝精度為±0.05 mm程度。考慮到元件尺寸,咋一看數(shù)值較大,但是在表面安裝中利用焊料的自動調(diào)準(zhǔn)(Selfalignment)效果可以確保再流焊以后的元件位置精度。但是安裝采用導(dǎo)通孔連接方式的元件時使用樹脂系粘結(jié)劑,這時不能期望有自動調(diào)準(zhǔn)效果。
(3)激光導(dǎo)通孔的調(diào)準(zhǔn)(Alignment)。一般的激光導(dǎo)通孔加工時,以事前形成的線路層的對準(zhǔn)標(biāo)記(Alinment Mark)為基準(zhǔn)進(jìn)行加工。內(nèi)層與元件的位置精度不能保證時,就會引起元件與導(dǎo)通孔的位置偏離。
第二是元件端子電極的鍍層。通用元件的電極最外層一般是鍍錫(Sn)層。由于激光導(dǎo)通孔進(jìn)行鍍銅(Cu)層連接,因此元件電極也希望是鍍銅層。這時要經(jīng)過PCB的去沾污和化學(xué)鍍銅工程,因此必須形成經(jīng)得起這些工程的保護(hù)膜。
第三是元件高度的波動度。元件高度的波動度即成為導(dǎo)通孔深度的波動度。希望從激光加工和鍍層兩方面進(jìn)行導(dǎo)通孔深度的統(tǒng)一。
導(dǎo)通孔連接方式中,這些因素還會相互影響和重疊,希望以PCB制造商,元件制造商和安裝機(jī)制造商為主的關(guān)系者作為開發(fā)的共同目標(biāo)。
如圖15(C)所示,PCB內(nèi)層上制造進(jìn)入元件的構(gòu)造于1990年代后期進(jìn)行研究開發(fā),現(xiàn)在已有許多開發(fā)例,還沒有適用的實用品事例。然而它對于PCB的薄板化極為有利,期待著它的實現(xiàn)。為此實現(xiàn)穩(wěn)定的元件特性是第一的,希望同時進(jìn)行材料研究和工藝技術(shù)的確認(rèn)。
8 結(jié)語
進(jìn)入21世紀(jì)以來,將會迎來元件嵌入PCB正式實用化的時期,今后將會迅速發(fā)展,為此嵌入元件的規(guī)格化或者評價方法等的標(biāo)準(zhǔn)必須緊緊跟上。新的嵌入技術(shù)的開發(fā)將會層出不窮,數(shù)年以后元件嵌入基板將會克服各種課題,成為通用的安裝技術(shù)而固定下來。
關(guān)于元件嵌入PCB的可靠性評價本文只是介紹了制造上的技術(shù)課題,此外還有CAD設(shè)計上的相應(yīng)課題或者包括元件檢查在內(nèi)的最終檢查技術(shù),PCB制造商與用戶之間的品質(zhì)保證契約上的課題等。
-
pcb
+關(guān)注
關(guān)注
4322文章
23126瀏覽量
398585 -
元器件
+關(guān)注
關(guān)注
112文章
4727瀏覽量
92496 -
焊盤
+關(guān)注
關(guān)注
6文章
555瀏覽量
38177
原文標(biāo)題:埋嵌元件PCB的技術(shù):二
文章出處:【微信號:pcb3com,微信公眾號:小哥Allegro】歡迎添加關(guān)注!文章轉(zhuǎn)載請注明出處。
發(fā)布評論請先 登錄
相關(guān)推薦
全印制電子技術(shù)在pcb中的應(yīng)用
埋嵌元件PCB的技術(shù)(第三部分)
埋嵌元件PCB的技術(shù)(第二部分)
【微信精選】對PCB行業(yè)前景有疑惑?聽聽他們怎么說
埋容PCB的概念與設(shè)計
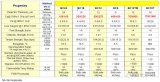
埋嵌元件PCB的元件互聯(lián)技術(shù)和評價解析
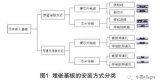
埋嵌銅塊印制電路板的設(shè)計和關(guān)鍵工序的制造方法
全印制電子技術(shù)給PCB工業(yè)帶來了怎樣的積極影響
PCB元件如何創(chuàng)建?
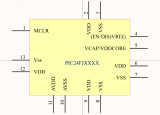
評論