文章鏈接:https://doi.org/10.1063/5.0172805
摘要
薄(100nm厚)疏水聚合物薄膜被用于許多需要防水的應用。然而,由于耐久性差,疏水薄膜的實現受到限制。薄疏水膜在冷凝過程中起泡已被認為是與失效相關的主要機制之一。然而,關于起泡形成的來源還存在著分歧。此外,人們還缺乏對促進蒸汽通過薄疏水薄膜滲透途徑的物理缺陷或針孔的了解。這些針孔控制著在疏水聚合物和金屬基板之間的界面上的水泡的成核。在這里,我們使用金屬電沉積作為一種手段來表征這些固有的針孔在薄疏水聚合物。證明了一種簡便的方法來在CFx和聚(聚氯二乙烯)(聚對二甲苯C)薄膜上定位針孔和測量針孔密度。我們的工作不僅有助于理解與薄膜沉積相關的內在缺陷,它也為高效薄膜疏水涂層的選擇和開發提供了設計指導。
介紹
薄膜聚合物具有優異的熱絕緣性能,氣阻隔能力,和化學和熱穩定性。因此,這些材料和涂層長期以來被用于有機發光二極管(OLED)中的柔性基底,生物醫學設備和包裝中的保護膜,和表面冷凝器上的傳熱增強涂層。特別是,需要防水的連續排水的系統已經廣泛使用疏水聚合物。例如,疏水薄膜在蒸汽凝結過程中增加了熱傳遞,在蒸汽凝結過程中,由于這些表面具有的水排斥性產生的引力,液滴成核、合并并從表面脫落。由于疏水薄膜的低表面能而形成的離散液滴有助于液滴的成核和去除。滴冷凝現象克服了經歷薄膜冷凝的親水金屬冷凝器的挑戰。薄膜式冷凝,即在冷凝器表面形成連續的液體膜,阻礙了離散水滴的進一步成核,并增加了相對于等效尺寸的滴式冷凝器更高的整體熱阻。聚合物涂層體系的預期壽命對性能提出了嚴格的要求,這依賴于這些聚合物薄膜極低的氧滲透性或蒸汽含量。當涉及到冷凝器涂層時,具有商業耐久性的疏水聚合物薄膜尚未實現,因為大多數100納米薄膜在運行幾小時內失效。
薄聚合物薄膜的失效機理已被描述為脫濕、起泡、和分層。薄膜(<10納米厚)會發生去濕現象,此時水對親水性基材的親和力更高,會將涂層推開。然而,對于較厚的膜(>10nm厚),起泡被認為是主要的失效機制。在起泡過程中,水在聚合物表面下滴下單核,并擴散到薄膜從襯底上完全剝離。腐蝕引起的起泡是聚合物涂層金屬表面的常見現象,腐蝕產物會導致水泡形成。
由于非腐蝕性襯底上存在離子,因此有人聲稱會在非腐蝕性襯底上引發水泡。然而,這一機制并不能解釋為什么不同的聚合物具有不同的壽命,而不管其襯底的化學性質和粗糙度如何。此外,一些研究人員聲稱,擴散是水分通過薄膜轉移的主要機制,最終導致水泡。與此相反,擴散的時間尺度與分層的時間尺度有顯著的不同。例如,考慮100nm厚的聚合物膜,菲克定律的擴散時間尺度為τ≈h2/Dm=10-4∽10-1s,其中h是膜厚度,Dm是聚合物膜中水汽的擴散系數[我們認為值從Dm=10-13m2/s(聚酰亞胺)到Dm=10-10m2/s(醋酸纖維素)]。雖然根據擴散時間尺度,分層應該是瞬時的,并且聚合物薄膜掃描在縮合起始后持續數小時。這種時間尺度的差異暗示了聚合物中的物理缺陷或針孔,它們可以作為蒸汽到達基底的運輸途徑。過去的研究表明,水泡可以在人工針孔上啟動,并且分層是由厚度依賴的靜水壓力驅動的。然而,不知道聚合物薄膜上固有針孔的本質,這控制著沉積薄膜上的內在泡,減少了開發和改進涂層的過程到嚴格的試驗和錯誤。
疏水薄膜中針孔缺陷的表征對于制定標稱可接受缺陷的標準和設計起泡形成的有效屏障以提高薄膜的耐久性至關重要。由于氣泡和污染物的隨機缺陷已被觀察和報道。然而,在疏水性涂層內的缺陷密度及其空間分布尚未得到研究。針孔缺陷密度可以提供關于涂層的預期壽命的信息,而無需對冷凝器涂層進行長期測試,這可能是耗時和昂貴的。非導電性和非常薄的聚合物薄膜的性質使得針孔缺陷更難以探測。本文報道了疏冰聚合物CFx、疏水聚對二甲苯C的缺陷密度。我們使用固有針孔作為銅微結構的成核和生長通道,使針孔位置在掃描電子顯微鏡(SEM)和光學顯微鏡(OM)下可見。我們使用聚焦離子束(FIB)銑削結合SEM進行針化測量。我們的工作闡明了控制薄膜固有缺陷的機制,并為高效薄膜疏水涂層的選擇和開發提供了設計指導。
實驗部分
我們考慮了兩種不同的聚合物薄膜,CFx沉積的振動粒子增強化學氣相沉積(PECVD)和通過化學氣相沉積(CVD)沉積的聚(2-氯-對二甲苯)(聚對二甲苯C)。選擇這兩種薄膜可以更好地了解它們的相對缺陷密度和沉積過程對各自薄膜質量的影響。此外,CFx是一種氟化薄膜化學物質,而聚對二甲苯C是一種非氟化分子。圖1(a)描述了在CFx上制造Cu微結構的過程。鏡面多用途110銅片(McMaster-Carr)用作所有沉積工藝的襯底。適當的處理和清潔拋光的銅基質是至關重要的,以使顆粒污染在沉積過程中引發針孔,保持到最低限度。雖然陶瓷和聚合物的沉積機制不同,但考慮到顆粒僅僅作為物理阻斷劑,禁止任何材料在基底上沉積,顆粒導致的針孔形成機制是相似的。因此,陶瓷和聚合物的位置都會形成針孔。
圖1.(a)通過針孔制備銅液滴的制備工藝示意圖。示意圖不能縮放。在薄膜生長過程中,由于制造過程中的缺陷而產生針孔。隨后在電沉積過程中,Cu通過針孔生長。接收和清洗的(b),銅上的(c)在銅上的498nmCFx薄膜(d)490nm聚對二甲苯C薄膜的原子力顯微鏡圖像。接收到的Cu、CFx和對苯二甲苯C的表面粗糙度Rq值分別為8.8、7.8和18.5nm
此外,我們還保持了類似的沉積條件(樣品在沉積室內的位置和樣品數量),以盡可能地消除外部效應。在沉積之前,銅標簽通過四個步驟進行清洗。首先,用丙酮清洗標簽,然后是異丙醇(IPA),水,最后再次是IPA。清洗后,銅片在丙酮中超聲以適當地脫油脂。CFx薄膜通過等離子體深反應離子蝕刻工具(ICPDRIE-等離子體熱)沉積,其中C4F8和固化酶作為反應氣體。等離子體中存在的CF3+、Ar0和F-自由基形成保形CFx層。具體來說,我們沉積了101±37到4986±15nm厚的非晶態氟化聚合物(CFx,x≈1)氟碳薄膜。
聚對二甲苯C沉積在SCS聚對二甲苯涂布器中,以二對甲苯-二甲苯二聚體作為引發劑。沉積的聚對二甲苯涂層厚度為100±29~501±16nm。
結果與討論
圖1(a)描述了我們的制造方法的示意圖。針孔是通過薄膜上的孔或物理缺陷,將底部親水銅襯底暴露在離子溶液中。因此,針孔和任何裂縫或空隙都是親水部位,可以被溶液弄濕,而聚對二甲苯C包膜保持干燥。在電沉積過程中,溶液中的Cu2+離子由于應用電位而向樣品遷移。這些離子通過針孔擴散,到達導電襯底,引發銅的成核。銅離子通過低缺陷密度的惰性保護膜,如聚對二甲苯C的擴散是非常不可能的,因為聚對二甲苯C膜阻礙Cu2+離子穿透的時間超過了我們研究的研究時間范圍。此外,與擴散相關的成核在整個表面都是全局的。然而,在我們的案例中,由于聚合物薄膜中針孔和裂紋的隨機和局部分布,銅的成核高度局限于薄膜上。在涂層和銅基底形成的界面上暴露的導電位點上的核酸。最后,銅通過針孔生長,并在薄膜的頂部呈液滴狀的形狀突出。銅濃度隨著時間的推移而生長,隨著電沉積時間的延長(>50min),銅濃度可達100μm。電沉積70min后,表面通過涂層被銅生長完全飽和。在電沉積過程中,最初在導電銅襯底上形成的銅島的演化與時間依賴,并遵循一階動力學增長。在沒有聚合物涂層的導電基板上,Cu以孤立的島生長,島的數量隨著時間的推移而增加。Cu島的成核遵循一級動力學過程,可以表示為:Nt=N0(1-exp(Knt)),其中Nt為t時刻的銅島數,Kn為成核速率,N0為飽和時的Cu島數。因此,在我們的樣品上的銅成核也表現出時間依賴性,并且成核并沒有同時在所有的針孔處開始。
在我們的例子中,雖然成核位點或島的數量受到針孔密度的限制,但仍然可以觀察到Cu滴成核的時間依賴性(圖2)。而電壓和電流影響了銅液滴的形態和生長速率,我們保持了一個固定的電壓輸出,以保持樣品之間的成核動力學近似相似,以抵消潛在效應。在電沉積的初始階段,銅的微觀結構呈圓形,類似于在凝結過程中在非潤濕基質上成核的水滴[圖2(b)]。然而,根據所用的電壓,可能會出現不同的形態。在大量生長之后,由于在可能存在大量針孔的高度局部化區域中的接近,銅液滴可以合并[圖2(d)]。
圖2.電沉積前(a)、10min后(b)、20min電沉積后(c)、40min電沉積后(d)的光學顯微鏡圖像(10)。圖像中的黑圓圈是生長在具有470nm厚度的CFx薄膜上的銅液滴。在(a)到(d)中顯示的圖像被放大,并沒有用于獲得數字密度數據。它們旨在顯示銅隨著時間的推移而增長。(e)銅液滴密度隨電沉積時間的函數。45min處銅液滴的密度是CFx薄膜的最終固有針孔密度。x軸的不確定度條小于符號的大小,并且沒有顯示出來。
在CFx薄膜上,在40min后,Cu液滴的數量沒有增加[圖2(e)]。由于團聚體的形成,隨著液滴的空間擴散,每一個液滴的特征變得復雜[圖2(c)]。在這一點上,我們假設銅的成核遍布于暴露的銅活化位點,因此,液滴的數量近似表示CFx膜中針孔的密度。
圖3顯示了CFx和聚對二甲苯C涂層的總針孔密度與薄膜厚度的函數。薄膜的厚度取決于二聚體(聚對二甲苯C)的質量和沉積時間(CFx)。對于這兩種聚合物薄膜,針孔密度均隨薄膜厚度的增加而減小。這些聚合物是通過鏈生長機制沉積的,其中單體被添加到自由基鏈上,而在階梯生長機制中,如果滿足條件,可以在任何兩個相鄰的分子之間發生反應。當單體被吸附在表面時,它們可以到達現有的聚合物鏈,并通過過量的能壘附著在那里,或通過聚合物島分散,找到另一個活性位點。否則,單體可以與其他單體發生反應,形成一個新的聚合物島。聚合物的傳播、單體分散和新的聚合物引發作用同時發生,這取決于單體的化學、動力學和各自過程的能壘。在這種反應中,空間擴散和分層生長同時以一種依賴于生長動力學的競爭方式發生。因此,隨著厚度的增加,表面的聚合覆蓋范圍增加,導致物理缺陷減少。此外,在聚對二甲苯C中觀察到的針孔密度比CFx薄膜低一個數量級以上,這是由它們各自的生長機制引起的。CFx薄膜由PECVD培養,利用等離子體蝕刻和沉積同時生長速度快。由于血漿的化學降解,PECVD鞘酶中功能物種的保留率低于CVD過程。雖然聚對二甲苯C被宣稱沒有針孔,但在許多情況下,這取決于膜的覆蓋率,因此也取決于膜的厚度。當厚度接近∽1μm時,我們觀察到總針孔密度顯著降低。此外,與CFx相比,聚合物的鏈傳播速率要高得多,這可能決定了觀察到的更高的覆蓋率。
圖3.CFx和聚對二甲苯C的針孔密度隨涂層厚度的變化,其固有針孔密度隨厚度的增加呈下降趨勢。聚對二甲苯的針孔比CFx少,因為在沉積過程中表面覆蓋率更高。x軸不確定度條小于符號大小,沒有顯示。
圖4描述了使用ThermoScios2雙光束掃描電鏡/FIB,在0.1nA電流和2kV電壓下獲得的銅液滴的掃描電鏡圖像。圖4(a)顯示了CFx薄膜(540nm厚)上缺陷分布的掃描電鏡圖像。在0.15-0.3V的電沉積電位下,沉積的銅液滴具有多孔泡沫樣形態。隨著電沉積電位的增加,樹突的出現和突起的團聚體被觀察到。這些封閉的三維結構的出現可以歸因于過電位。銅微觀結構的形態取決于析氫和銅沉積之間的競爭反應,其中析氫可以抑制銅的沉積。
圖4.在500放大倍數下拍攝的局部區域的CFx上針孔分布的(a)SEM圖像。(b)銅液滴的橫截面,顯示液滴中心的針孔位置(5000的放大倍數)。(c)在(b)中確定的針孔的高倍掃描電鏡,作為Cu沉積的通道和Cu液滴生長在CFx膜的頂部。CFx薄膜的厚度為470nm,電沉積時間為20min
為了研究針孔的幾何形狀和尺寸,我們使用相同的Scios2FIB設備,使用50kV和0.1nA離子束對Cu液滴進行了邊對邊的銑削。FIB圖像顯示,銅液滴首先填充針孔,然后從薄膜中生長出來,形成一個半球形。銅液滴通過半球形擴散向外生長[圖4(b)]。通過連續銑削,可以近似于銅液滴的中心。根上有針孔,這是銅最初生長的途徑。圖4(c)中指示的紅框顯示了一個這樣的針孔,該針孔大約位于圖4(b)中所示的液滴的中心。在某些情況下,由于涂層的不一致,有核的銅碰撞可以在穿透涂層形成涂層之前大量形成最終的半球形結構。銅液滴是多晶的,由大小從幾納米到微米的晶粒組成。隨著晶粒向針孔的徑向延伸,可以觀察到一些各向異性。通過FIB-SEM分析,我們可以確定每個薄膜的針孔尺寸,CFx的尺寸在≈50-200nm范圍內,聚對二甲苯C的尺寸在70-150nm范圍內。
我們的方法揭示了薄疏水薄膜的失效動力學。在縮合過程中,疏水膜不能從支撐襯底上分層。這種失效機制可以通過兩個步驟來描述:(1)泡起始和(2)泡生長導致分層。過去的工作研究了起泡的起始,并建立了起泡(Ω)的標準,它確定了針孔中的凝聚核是否會在針孔頂部以水泡或冠狀物的形式生長。
式中,Rb0為初始分層泡罩半徑,Rd為松松半徑,γ為冷凝物的液蒸氣表面張力,E為薄膜的楊氏模量,G為薄膜與基底之間的界面附著力,h為薄膜的厚度。更厚的薄膜,更高的彈性模量,和更高的附著力有助于防止水泡的發生。無論具有優異的物理性能,針孔暴露部位都將開始凝結。生長可以使用更厚和更硬的薄膜來延遲,但由于針孔的存在而不能被阻止。因此,除了材料的熱物理性質外,針孔密度是表征耐久性的關鍵。因此,如果一個水泡開始,其生長表現如下:
其中,Rb(t)是與時間相關的泡罩半徑,JV是蒸汽質量通量,被認為是恒定環境條件下的一個常數。針孔半徑越大,泡罩越大。此外,水泡的生長導致水泡合并,導致局部分層。更高的針孔密度會增加泡皰聚結的可能性,從而導致疏水膜分層更快。更多的針孔的總面積覆蓋將引發更多的分層區域。最終,局部分層區域導致薄膜從襯底上的整體分層。
對于疏水表面單位面積的N個針孔,根據泊松分布,最近針孔之間的平均距離為d=1/(4N)?當半徑rb合并時發生分層,因此分層過程中針孔之間的平均距離等于水泡直徑d=2Rb。使用這個條件并將其替換為等式(2),我們得到了一個劇烈的退化時間
從等式(3)中,我們看到起泡時間是t∽N-3/2和t∽Rd-2。因此,最小化針孔尺寸和針孔密度對于提高蒸汽凝結過程中的耐久性都很重要。然而,針孔的尺寸對分層時間的影響大于針孔的數量密度。
為了支持我們的論點,我們進行了持久性測試,以確定啟動水泡所需的時間。我們使用了兩個鍍有100和1000nm厚的聚對二甲苯C薄膜的銅片。然后,我們將樣品放置在一個定制的蒸汽冷凝室中。100nm厚的樣品在蒸汽冷凝不到24小時內失敗,而1000nm厚的樣品持續時間超過1080小時。從實驗結果中,我們可以看到1000nm樣品的耐久性比100nm厚的樣品高出兩個數量級以上。根據等式(3),利用我們的冠狀密度數據考慮到泡的直徑是相同的數量級,1000nm樣品的泡降解時間理論上應該比100nm厚的樣品高三個數量級,這與實驗結果很好地一致。
從我們的針孔密度和水泡形成分析中獲得的基本知識揭示了幾種增強疏水薄膜可凝性的策略。一個重要的策略是使用多步沉積過程,而不是單層沉積。沉積過程中形成的多層應具有隨機的空間針孔分布,可能導致層間針孔錯位,從而形成蒸汽滲透的曲折路徑。因此,蒸汽不能通過一個連續的路徑來成核并形成水泡。多層應該優化等式(1)中概述的物理性能。基于這一發現,我們使用類似的方法創建了鋁層氟化金剛石類碳涂層(FDLC),在銅電沉積過程中發現沒有可見的銅液滴。因此,涂層中持續的疏水性可以部分歸因于針孔的缺失。我們的方法適用于大多數附著力合理的疏水性涂料。然而,由于使用非常薄的疏水薄膜(<100nm),在液滴生長過程中快速分層,該方法失敗了。
結論
總之,我們展示了一種簡單的疏水聚合物薄膜的前物理缺陷技術,它控制了冷凝過程中的失效機理。我們的研究結果提供了有關具有各自耐久性的聚合物薄膜的有效性的信息。其他更傳統的耐久性測試,如穩定冷凝實驗到失敗,包括進行數月或數年的實驗,這可能是昂貴和耗時的。相反,銅在聚合物薄膜上的電沉積為我們提供了關于薄膜的原始程度的信息,而無需進行耗時的測試。此外,我們的方法可以提供關于理想的加工和沉積條件的信息,以創造無缺陷或最小缺陷的涂層。總的來說,用于針孔可視化的電沉積棒聯體可以幫助正確表征疏水薄膜的潛在應用。
-
薄膜
+關注
關注
0文章
307瀏覽量
30305 -
納米
+關注
關注
2文章
703瀏覽量
37596 -
函數
+關注
關注
3文章
4359瀏覽量
63496
原文標題:納米級針孔缺陷的性能研究
文章出處:【微信號:深圳市賽姆烯金科技有限公司,微信公眾號:深圳市賽姆烯金科技有限公司】歡迎添加關注!文章轉載請注明出處。
發布評論請先 登錄
相關推薦
光譜傳感器:工業輪廓掃描的毫米級精度革新
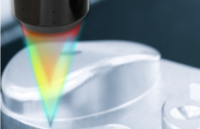
X射線成像系統:Kirkpatrick-Baez鏡和單光柵干涉儀
VirtualLab Fusion應用:用于X射線束的掠入射聚焦鏡
Aigtek功率放大器如何幫助制備(1~100nm)級的納米薄膜
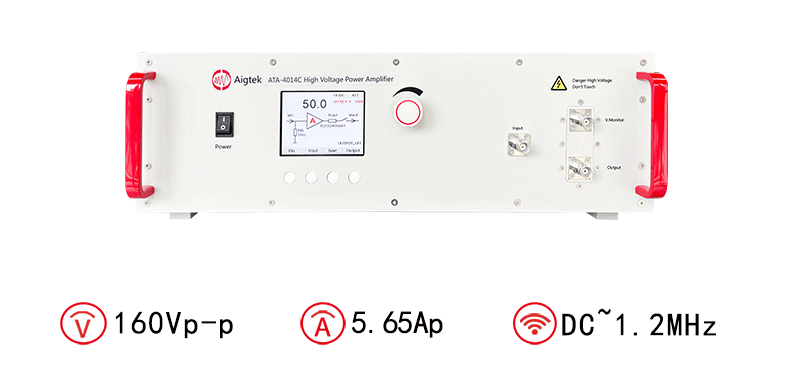
碳納米管的結構與特性解析 碳納米管在能源儲存中的應用
安泰功率放大器如何幫助納米材料領域進行創新研發
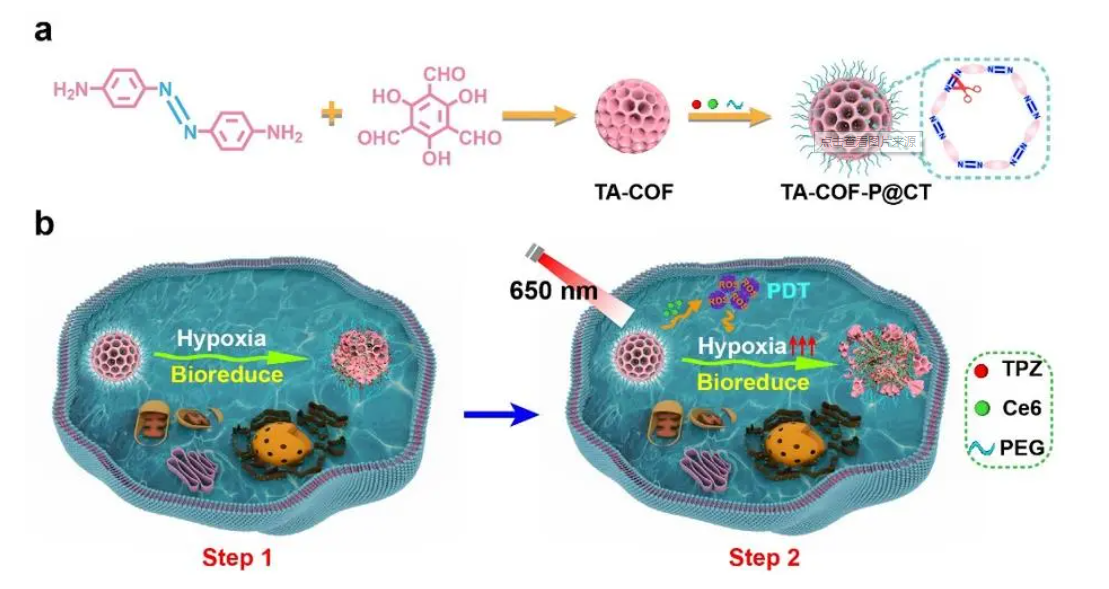
中國科大在納米級空間分辨紅外成像研究中取得新進展
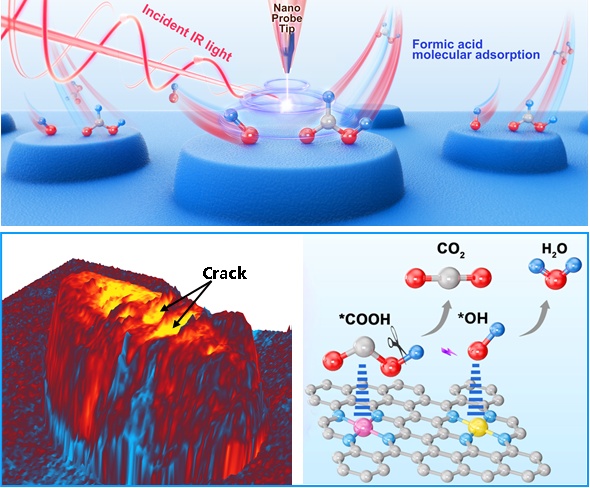
麻省理工學院研發全新納米級3D晶體管,突破性能極限
中國科大在納米級空間分辨紅外成像及催化研究中取得新進展
SK海力士開發出第六代10納米級DDR5 DRAM
納米級材料尺寸測量:從微觀到宏觀,納米精度,中圖智造
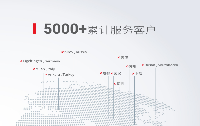
納米級材料尺寸如何測量?
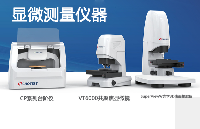
評論