第二章:沉鎳金線設備(含附屬設備)條件
第三章:工藝流程及工藝條件
一、工藝流程:
來料檢查----板面前處理→插架或串珠→上板→除油→熱水洗→溢流水洗(2級)→微蝕→溢流水洗(2級)→預浸→活化→DI水洗(2級)后浸→DI水洗(2級)→沉鎳→DI水洗(3級)→沉金→回收水洗→DI水洗(2級)→DI熱DI水洗→下板→后處理
二、前處理機基本參數:
1、傳送速度: 2.5-3.5m/Min
2、水平微蝕:0.3-0.5um/cyc,SPS 80-120g/l,H2SO4 3-5%,Cu2+≥20g/L時更換
3、磨轆規格: 1000---1200#上下各一對尼龍針刷
4、磨痕寬度: 8-12mm
5、水洗要求:壓力1.5-2.5Kg/cm2,每班更換清洗
6、噴砂: 400#金剛砂,噴砂含量10-20%
7、超聲波水洗:28KHz
8、烘干溫度: 70-80℃。
三、化金線藥水配槽及工藝條件:
3.1 藥水配槽
3.2 工藝控制條件
四、后處理機基本參數:
1、傳送速度: 2.5-3.5m/Min(根據板子水分烘干情況調整)
2、酸洗濃度:檸檬酸 0.5-1%
3、水洗要求:壓力1.5-2.5Kg/cm2,水質 DI水,每班更換清洗
4、超聲波水洗:28KHz
5、烘干溫度: 75-85℃。
第四章:生產操作注意事項
一、水平噴砂前處理機操作注意事項
1、每板檢查設備狀態是否正常,磨刷是否變形(兩頭大中間細),磨痕檢查是否合格,噴砂濃度和噴砂效果檢測是否符合要求。刷板后,板面應無任何污漬或油漬,及無氧化銅層。
2、刷板時,在有效刷板區域內生產板應左右交替放置,以避免磨轆中部過度磨損。
3、每班生產前或更換不同板厚生產板時,需用寬度>360mm同厚度的廢板做磨痕實驗,磨痕寬度應為8-12mm。
4、磨板后的生產板,必須插架或隔膠片存放,應在2小時內完成化鎳金生產,防止板面氧化污染,避免受外來污染,如出現氧化情況,需重新過水平噴砂前處理。
5、線路板上的Sn/Pb須完全剝離干凈。
二、化鎳金拉操作注意事項
1. 生產前需要檢查各缸液位是否正常;抽風系統是否開啟;用溫度計驗證各缸溫控系統是否工作正常;各缸打氣、循環過濾是否正常。
2. 輔助設備的檢查:搖擺是否正常;掛籃是否清潔,要求無破損,無上鎳金現象。
3. 各水洗槽溢流水洗量要求保證為1-2 TURN OVER/H。每次停拉或連續生產20小時后需更換各水洗缸內污水,并清洗各水洗缸。鎳后水洗槽每班清洗。
4. 鎳缸的穩壓器是否工作正常。鎳缸防析出穩壓器的控制電壓0.9V,防析出棒不可與槽壁接觸。務必檢查保護電壓之導線、導線接觸點是否完好及安裝正確,檢查缸壁與陰極保護桿的實際電壓。
5. 鎳缸溫度升至50℃后,必須開啟陰極保護裝置;停拉生產時需待溫度降至50℃以下時方可關閉打氣、過濾及陰極保護裝置。
6. 藥水的分析檢查:各缸藥水是否在要求范圍內,有偏差藥水是否已經調整到要求范圍內。
7. 新鎳缸拖缸必須采用裸銅板拖缸,鎳板使用次數不要超過一個鎳缸壽命周期,防止鍍鎳層分層脫落,污染鎳缸。(注: 鎳板出現裂紋或有鎳層脫落的板切勿使用)。
8. 拖缸方法:當鎳缸溫度達操作溫度80℃以上時進拖缸板拖缸,拖缸浴負載0.4-0.6dm2/L。用裸銅板拖缸: 磨板后按正常流程進入化鎳缸,拖缸時間30min,拖缸后生產試板首板。
9. 生產中需保證鎳缸每缸板的負載應為0.2-1.0dm2/L,針對邦定板或IC、pad間距<5mil之生產板,負載量控制在0.2-0.5dm2/L。化金面積過大的板因為在鎳缸負載太大易造成活性太強產生滲鍍等品質問題;化金面積過小的板在鎳缸負載太小易造成活性下降產生漏鍍等品質問題,此兩種板子在生產時可交替進板(如進一掛化金面積較大的板,再進一掛化金面積稍小的板)以此來平衡鎳缸的負載量.
10. 生產時化鎳槽副槽需要保持連續打氣;停拉時需保持打氣到鎳缸藥水溫度低于50℃后,才能徹底關閉鎳缸打氣。
11. 化鎳缸液位的補加應本著少量多次的原則,嚴禁一次性加入過多的DI水(每次5升),以及禁止在板子剛入鎳缸3分鐘內補加DI水。
12. 正常生產中自動添加化鎳藥水按A:B:C:D=1:1:1:0.4的比例。每周需要校正自動添加流量1次。
13. D劑的添加:新開缸按4ml/L添加。如因產量不足而停產超4-8小時,生產拖缸時每次需額外補加約1ml/升D劑;如停產超8小時以上,生產拖缸時每次需額外補加約2ml/升D劑;額外補加的D劑需減除正式生產前化鎳濃度調整時自動添加量。
14. 烘干機之水洗槽及滾輪需經常洗凈,化金后板需及時烘干插架或隔紙(不能使用硫皮紙)轉移到后工序,烘干前最好儲存干凈的DI水洗槽內養板,且不得超過半小時;防止板面氧化發黃;化金下板時,輕拿輕放避免擦花;化金后板不得與未化金銅板混合存放
15. 微蝕、化鎳槽均需按要求開起打氣,鎳槽主槽可少量打氣,其它各藥水槽一般不開打氣。
16. 在線設備異常,應實時告知相關人員(工藝、維修等)處理。生產中每2小時應檢查一次各槽的溫度、循環過濾和震動等設備及各生產參數是否正常,并做好記錄。
17. 金回收槽須過濾及定期更換。
18. 所有生產板,在每日批量生產前,均需進行首板品質確認,以及批量過程檢驗。
三、化鎳自動添加系統設置
MTO數 鎳控制點(設置) pH控制范圍
0-1.0MTO 4.5 4.4-4.5
1.0-2.0MTO 4.55 4.45-4.55
2.0-3.0MTO 4.6 4.5-4.6
3.0-4.0MTO 4.65 4.55-4.7
每次添加量:
904A、904B、904C、904D=0.5L、0.5L、0.5L、0.2L
四、化鎳金特殊要求板生產操作指引
1.單面板或板材為紙板(有要求孔內不允許上鎳金)
生產此類板子時,需依據鎳缸的使用周期長短來調整活化浸浴時間,來進行試板生產。鎳缸生產周期越長,相對穩定性會逐漸下降,需要縮短活化浸浴時間(浸浴時間在30-90秒)。
2.鎳厚要求≥5UM的板
調整鎳缸藥水Ni2+和pH值在控制范圍的偏上限試板生產,若還達不到鎳厚要求,需延長鎳缸浸浴時間(2-10min),具體延長時間視現場生產情況而定。建議此類板子盡量安排在鎳缸周期≤3.0MTO前生產。
3.薄板生產
生產此類板子時很容易疊板造成露鎳、滲鍍等品質問題,故在生產中,需特別留意,插板時盡量擴大板與板之間的空隙(如隔一格插一塊板或中間用兩顆串珠來間隔),以避免疊板造成的各類品質問題。
4.邦定板生產
生產此類板子時,由于IC間距較小,活化處理較強或化鎳活性強時,很容易產生滲鍍等品質問題;故在生產中,需與其它生產板分開進行生產,此類板需縮短活化時間(按90-150秒,首板確認)、降低化鎳活性(負載量、溫度按中下限管控,3MTO以內)進行生產。
5.半孔板生產
生產此類板子時,由于在半孔形成時,樹脂易松散或金屬殘存,活化時易形成電位差,而產生漏鍍品質問題;故在生產中,需與其它生產板分開進行生產,此類板需延長活化時間(按150-240秒,首板確認)進行生產。
6.其它:未提及特殊板子,在批量生產時,均需進行試驗,確認最佳生產條件。
第五章:維護與保養
一、水平前處理機的維護保養
1、每周需對去毛刺機磨轆進行檢查,確保磨轆兩端與中間大小一致,磨痕寬度是否保持在8-12mm,否則需要更換磨轆。
2、每班檢查噴嘴是否暢通,檢查金剛砂含量是否符合要求,每周徹底清洗噴嘴一次,確保無任何堵塞物。
3、每周對水洗缸及濾網進行清潔,保持無塵物沉積。
二、沉鎳金線維護保養
-
工藝
+關注
關注
4文章
596瀏覽量
28834 -
化學
+關注
關注
1文章
83瀏覽量
19433
原文標題:宇眾環保:化學沉鎳金工序操作指南
文章出處:【微信號:FPCworld,微信公眾號:FPCworld】歡迎添加關注!文章轉載請注明出處。
發布評論請先 登錄
相關推薦
多層印制線路板沉金工藝控制簡述
印制電路板用化學鍍鎳金工藝探討-悌末源
轉:pcb工藝鍍金和沉金的區別
PCB工藝流程的沉金工序
PCB板沉金工序的流程解析
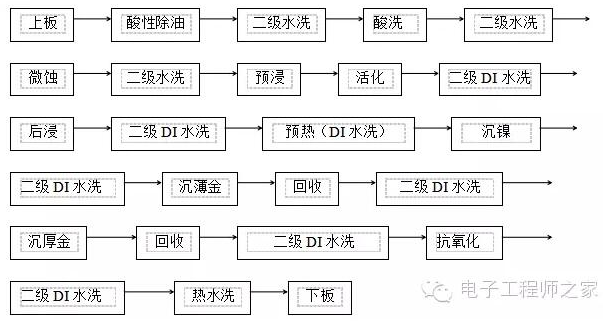
評論