引言
如果有人認為化學鍍銅和其他金屬化系統深不可測,那么關于電鍍就更像是復雜的腦外科手術。
文章將詳細介紹電沉積技術的復雜性及其在孔和表面上形成銅厚度的功能。還將介紹鍍銅溶液中活性成分的作用,各種鍍液成分的過程控制限制及其對沉積完整性的影響。
電沉積
與典型初始通孔金屬化的化學鍍銅不同,通孔中的導電層需要通過電沉積銅累積達到一定厚度。據了解,這些技術相互重疊,即一些初始金屬化工藝使用直接電鍍,相反,全加成工藝僅通過化學鍍工藝生成銅。
通過電鍍形成銅層的優勢在于成本較低、沉積速率較快以及電鍍銅性能更佳。改進集中在電解液的“均鍍銅”上,即電解液在板表面和通孔內沉積相對均勻銅沉積物的能力。采用高酸低銅濃度,以及改進的有機添加劑系統(光亮劑、載體、整平劑),提高了深鍍能力。不要低估電鍍槽設計、從電源到母線的電纜連接以及溶液移動對電鍍分布及沉積層整體質量的影響。
電路板設計技術的發展變化導致了其他挑戰和復雜性。電路設計向更高密度和超高密度的轉變帶來了工藝技術的新一波改進。
PCB制造中使用了其他幾種電鍍工藝。作為金屬抗蝕劑的錫、金屬抗蝕劑的鉛或錫通常采用電鍍工藝,有時也采用化學鍍工藝。其他電鍍金屬包括鎳、金和鈀(也是通過浸鍍液或化學鍍液沉積),以形成適當的表面涂層,用于插入連接器或元件連接,例如引線鍵合。后續專欄文章將概述這些工藝。
按照酸浸清洗劑、微蝕和酸預浸的順序進行預鍍清洗,開始本文的重點酸銅電鍍工藝。酸預浸是可選的,如果微蝕后的沖洗足夠,可以省略酸預浸工序。然而,這種情況僅適用于使用過氧化氫、過氧化硫酸微蝕劑。使用過硫酸鹽蝕刻劑需要進行酸預浸。酸清洗劑關鍵的變量是化學成分、濃度、時間和溫度。
對于微蝕,蝕刻深度是關鍵參數,反過來又受化學成分、濃度、時間和溫度的影響。酸預浸通常與鍍液中使用的酸和濃度相同,可保護鍍液,避免帶入殘留液,殘留液可能會對鍍液的成分或濃度產生不利影響。因此,預浸的化學成分及其污染物含量至關重要。
酸性鍍銅液的關鍵參數包括電氣、機械、物理和化學變量。從電氣參數開始,電流密度和一次電流密度分布影響電鍍速度、厚度分布和冶金性能,例如延展性、粗糙度和沉積層顏色。
電鍍表面的電流密度取決于整流器容量、相關陽極和陰極尺寸和間距、屏蔽、電鍍槽效率和溶液電導率。電鍍表面的電流密度分布取決于前面提到的一些參數,在圖形電鍍中,還取決于電路圖形。
通孔中的電流密度取決于以下附加變量:
通孔直徑和厚徑比;
鍍液(攪拌)的補充效率(孔內);
鍍液的深鍍能力,在很大程度上取決于酸/銅比、有機電鍍添加劑和干擾有機電鍍添加劑的雜質(浸出劑)含量。
圖1為深鍍能力的定義。后續專欄將介紹電沉積過程的實際力學和工藝參數的影響。
圖1:均鍍力的定義電鍍通孔的難度取決于板厚和孔徑。
例如,厚徑比均為10:1的兩個孔,一個孔使用厚度為100密耳的面板和直徑為10密耳的導通孔,而另一個使用厚度為200密耳的面板和直徑為20密耳的孔。兩種設計具有相同的厚徑比。
圖2強調了隨著厚徑比和板厚度的增加,保持均鍍力的難度。它說明了IR降(或通過導通孔的電阻)將會隨板厚度的平方提高,而導通孔直徑僅以線性方式影響電阻(或均鍍力)。
圖2:左欄表示板厚,右欄表示孔直徑
審核編輯:湯梓紅
-
pcb
+關注
關注
4319文章
23105瀏覽量
398087 -
電路板
+關注
關注
140文章
4963瀏覽量
97940 -
蝕刻
+關注
關注
9文章
414瀏覽量
15404 -
電沉積
+關注
關注
0文章
6瀏覽量
6646
原文標題:電沉積銅
文章出處:【微信號:actSMTC,微信公眾號:actSMTC】歡迎添加關注!文章轉載請注明出處。
發布評論請先 登錄
相關推薦
詳細解析STM32的外部中斷
高速數字設計374頁詳細解析
高速數字設計374頁詳細解析
BBE系統技術詳細解析
鋰離子在含人工SEI薄膜的鋰金屬負極表面的電沉積行為
晶片表面沉積氮化硅顆粒的沉積技術
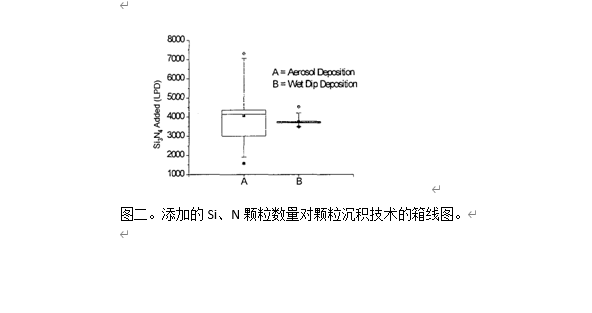
硅片形貌效應及其與底部抗反射涂層(BARC)沉積策略關系的解析
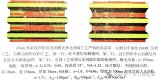
選擇性沉積技術介紹
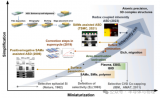
評論