集成電路前道工藝及對應設備主要分八大類,包括光刻(***)、刻蝕(刻蝕機)、薄膜生長(PVD-物理氣相沉積、CVD-化學氣相沉積等薄膜設備)、擴散(擴散爐)、離子注入(離子注入機)、平坦化(CMP設備)、金屬化(ECD設備)、濕法工藝(濕法工藝設備)等。
集成電路前道工藝及設備的標志性指標為集成電路的特征尺寸,主要沿摩爾定律方向持續延伸,根據國際器件與系統技術路線圖IRDS(2021),集成電路前道關鍵工藝、器件結構對應的設備加工技術能力將由當前的5 nm、3 nm發展到2.1 nm、1.5 nm直至等效1 nm、0.7 nm技術節點,如表1所示。
表1集成電路邏輯器件技術路線圖[1]
近期(2021-2025):FinFET晶體管結構繼續延伸,由5 nm直至3 nm、2.1 nm節點。 為進一步提升柵極控制能力,從3 nm節點開始, LGAA(Lateral gate-all-around,水平圍柵)結構開始引入并逐漸替代FinFET結構,相應的制造設備應該隨之進行技術迭代,支撐到這個制造節點的要求。
中期(2026-2030):晶體管全面進入2.1 nm以下節點,根據IRDS(2021)規劃,2.1 nm和1.5 nm這兩個工藝節點預計將分別在2025年和2028年出現。 LGAA晶體管結構可以繼續支撐這兩個制造節點的要求,相關制造設備需要根據工藝特征尺寸縮小的要求做進一步提升。
遠期(2031-2035):晶體管進入等效1 nm工藝節點和等效0.7 nm工藝節點,晶體管的工藝特征尺寸達到極限,多層垂直堆疊的LGAA晶體管結構將成為下一步發展方向。 單片三維堆疊工藝及設備技術將是這個階段的主要需求。
主要技術挑戰
(1)EUV光刻設備。 光刻技術直接決定了集成電路的特征尺寸(光刻線寬與***曝光波長成正比,與成像系統數值孔徑呈反比),是摩爾定律演進的核心驅動力之一。 傳統的193 nm***在經歷了“浸沒式技術”及“多重曝光”兩次重要技術升級后,已經大規模應用在10 nm節點集成電路制造中。 進入7 nm以下節點,雖然193 nm浸沒式光刻+多重曝光從技術上仍然可以滿足集成電路制造的需求,但工藝復雜度直線上升,造成了難以解決的良率和成本問題。 因此,采用13.5 nm極紫外光源的EUV***成為7nm及以下集成電路大生產首要選擇,在7 nm節點,EUV光刻工藝步驟是193 nm浸沒式光刻的1/5,光刻次數是后者的1/3[4]。
當前EUV***已經在產線批量應用并支持7~5 nm節點的工藝制程要求。 隨著摩爾定律繼續延伸,EUV光刻主要是按照兩個方向演進:一是由單重曝光(Single Patterning, SP)發展至雙重曝光(Double Patterning,DP); 另一個就是提高EUV數值孔徑(High-NA EUV)。 根據IRDS光刻技術發展路線圖預測,在3 nm節點(2022年),集成電路大生產將采用雙重曝光EUV技術; 在2.1 nm節點(2025年),集成電路大生產將采用高數值孔徑EUV技術,如表2所示。
當前ASML正在研發第二代EUV***,數值孔徑將由現在的0.33提升至0.5,同時不斷提升光源功率,預計量產時間為2024年,將支撐2025年之后集成電路制造的需求。
表2 光刻技術發展路線圖
(2)GAA(圍柵晶體管)制備設備。 GAA(Gate-All-Around)晶體管將是繼FinFET后的下一代晶體管結構。 相對于FinFET的三面柵控結構,GAA晶體管溝道為水平或垂直納米線,柵極四面環繞溝道,柵控能力更強,可以有效降低短溝道效應[5]。 GAA結構預計于2022年3 nm節點開始導入集成電路大生產線,并于2025年2.1 nm節點成為主流器件結構。
GAA晶體管結構的引入和特征尺寸的進一步微縮,對集成電路制造工藝設備提出了更高的要求:離子注入機將更加強調共形摻雜(Comformal Doping)、薄膜和刻蝕工藝更加強調原子級的精度控制(ALD-原子層沉積、ALE-原子層刻蝕)、其他設備(如CMP、ECD、濕法工藝設備等)也需要做相應調整,以滿足更高精度加工、非銅互聯材料、 新型HKMG材料等方面的需求。 下面就共形摻雜設備、原子層刻蝕設備、原子層沉積設備做詳細介紹。
共形摻雜的離子注入設備:晶體管采用三維結構以后,對共形摻雜(各向同性的摻雜,各個方向上均勻摻雜)的要求不斷提升。 傳統的離子注入設備中,離子通過加速電場加速注入晶圓,摻雜的定向性強,為滿足三維晶體管共形摻雜工藝的需求,離子注入設備有以下兩個發展方向:(1)進一步提升離子注入機的束線角度、束線形狀和注入劑量的控制能力,如應用材料公司的VIISta900 3D系統; (2)采用等離子體浸沒式注入設備[6],在一層貼合晶圓表面結構的等離子體輔助下,實現各個方向的均勻摻雜,如應用材料公司的VIISta PLAD系統。
原子層沉積(Atomic layer deposition, 縮寫ALD)和原子層刻蝕(Atomic layer etching, 縮寫為ALE)[7]:進入納米尺度以后,半導體制造對加工精度要求不斷提高。 以IMEC的堆疊納米線GAA晶體管結構為例,制備過程為:在襯底上沉積多層SiGe/Si超晶格結構,完成Fin刻蝕后,通過選擇性刻蝕去除SiGe,釋放Si納米線,然后沉積高K介質及金屬柵(置換式金屬柵工藝); 在此過程中,SiGe結構刻蝕和納米線的釋放需要對實現對多層Si納米線之間SiGe的橫向精確去除,高K介質及金屬柵的沉積需要在SiGe去除后的極小空間內完成,以上工藝均需通過ALE和ALD設備實現。 ALE和ALD技術可以以一種自我限制且有序的方式在原子尺度逐層去除/沉積材料,賦予人們原子尺度的精細加工能力。
(3)設備智能化。 集成電路技術在賦能信息技術產業的同時,新一代信息技術也在促進集成電路產業的發展,推動其不斷邁向“智能制造”。 集成電路制造設備智能程度不斷提升,將逐漸具備晶圓狀態追溯、先進工藝控制(缺陷監測、工藝過程控制)、設備能耗管理、預測性排產、預測性維護和虛擬量測等功能。
要實現這些,除設備需要具有相應的信息采集及決策執行功能外,還需要產線信息系統的配合,單純從設備的角度,根據IRDS預測,設備將按照表3所示的技術路線圖發展,逐步支持智能化功能的實現。
表3 設備智能化技術路線圖[1]
(4)450 mm(18英寸)設備。 在一次工藝過程中,更大的晶圓尺寸可以生產更多的芯片,可以顯著降低單顆芯片成本。 晶圓尺寸不斷增大是集成電路產業一直以來的發展趨勢之一,由最初的100 mm (4英寸)、150 mm(6英寸),一直發展到今天的300 mm(12英寸,2001年引入,最早用于0.13 μm產線)。
2008年起,450 mm(18英寸)晶圓及其制造設備的生產被提上日程,初定于2012年組建18英寸試驗產線,2015年開始大生產線替代。 目前450 mm (18英寸)大硅片及450 mm(18英寸) 設備接口標準早已完成,但是由于450 mm(18英寸)設備研發及晶圓廠建線耗資巨大,450 mm(18英寸)晶圓設備的應用時間一再拖期。 根據最新的IRDS技術路線圖,450 mm(18英寸)設備的大生產線替代時間已經延后到了2025年之后。
審核編輯:湯梓紅
-
集成電路
+關注
關注
5391文章
11617瀏覽量
362810 -
半導體
+關注
關注
334文章
27687瀏覽量
221431 -
工藝
+關注
關注
4文章
602瀏覽量
28868 -
光刻機
+關注
關注
31文章
1156瀏覽量
47522 -
刻蝕機
+關注
關注
0文章
52瀏覽量
4246
原文標題:半導體工藝裝備現狀及發展趨勢(上)
文章出處:【微信號:閃德半導體,微信公眾號:閃德半導體】歡迎添加關注!文章轉載請注明出處。
發布評論請先 登錄
相關推薦
半導體工藝技術的發展趨勢
5G創新,半導體在未來的發展趨勢將會如何?
廣播電視發展現狀及趨勢
云計算產業發展現狀及趨勢
恒興隆機電:深圳電主軸行業市場現狀及發展趨勢是什么?
高清視頻監控技術的現狀及發展趨勢
張波教授論述功率半導體的現狀及發展趨勢
半導體工藝裝備現狀及發展趨勢
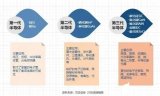
評論