半導體制造起始于對硅的加工,首先是將純度達到 99.9999%的硅晶柱切割成不同厚度的晶圓,一般來說4in晶圓的厚度為 520um,6in 的為670um,8in 的為 725m,12in的為 775um。在晶圓上按照窗口刻蝕出一個個電路芯片,整齊劃一地在晶圓上呈現出小方格陣列,每一個小方格代表著一個能實現某種特定功能的電路芯片。本文__【科準測控】__小編就來介紹一下半導體集成電路封裝流程的劃片方式、劃片工藝步驟、準備工作以及晶圓切割、芯片拾取等!
在半導體制造過程中,受到圓形影響,晶圓邊緣一定區域芯片圖形工藝不完整,大致有三種情況如圖 2-1 所示。考慮邊緣區域圖形不完整,制作掩模版時將其去除,每一個圖形都是工藝、功能完整的晶粒、以便于良率統計、晶粒分揀、盲封。硅晶柱的尺寸越大,能切割出來的晶圓面積就越大,能產出功能完整的有效芯片晶粒數量就越多。所以芯片制造工藝越先進,晶圓尺寸越大,其中的每一只電路芯片的成本越能攤薄,半導體的生產成本就能下降。
半導體器件的發展方向是單個芯片越來越小,且單個芯片集成的晶體管數量越來越多。硅晶圓的發展趨勢是晶圓尺寸越來越大,硅晶柱隨著工藝的進步能生長為1in、2in、4in、6in(約150mm)、8in(約200mm),近年來發展出12in甚至研發更大規格(14in、16in,甚至20in以上)。
in英寸(舊也作時),lin~2.54cm。
一片晶圓上重復刻蝕了幾只至幾十萬只電路芯片。晶圓上,電路芯片單元之間通過一定區域相互隔離開來,稱作芯片晶粒隔離區域稱作劃片槽,如圖2-2、圖2-3所示。在使用芯片晶粒前需要通過有效的手段將其分割并單獨取下。這時,就需要劃片這道工序,將晶圓分割成一個個單獨的芯片晶粒,再對芯片晶粒進行鏡檢、焊接、鍵合、封蓋等工序,從而封裝出能實現各種功能且不易被環境損傷的成品集成電路。
晶圓生產線制造好的一整片晶圓,在經過了探針臺電測試后,通過切割工藝分割成制作集成電路所需的具有電氣性能的獨立芯片的過程,稱為晶圓切割或劃片。
圖2-4給出了集成電路制造封裝流程及劃片工序位置。晶圓劃片是電子封裝工藝流程的首道工序,主要通過研磨、灼燒等方式完成分割。期間伴隨著對晶圓的固定、清洗等工藝步驟,以保證芯片不被劃片過程中產生的污物污染,保持晶粒的潔凈度。同時,還要保證在劃片過程中芯片電路功能的完整性和可靠性。
劃片方式
最早的晶圓切割方法是物理切割,通過劃片刀橫、縱的切割運動,將晶圓分割成方形的芯片晶粒。現在,用金剛石砂輪劃片刀(見圖2-5)進行晶圓切割的方法仍然占據主流地位。機械劃片的力直接作用在晶圓表面,會使晶體內部產生應力損傷,容易造成芯片崩邊及晶圓破損。特別是對厚度在 100um 以下的晶圓劃片時,極易導致晶圓破碎。機械劃片速唐一般為810mm/s,劃片速度較慢,且要求劃片槽寬度大于 30um,高可靠電路的劃片槽寬度則應更大,甚至達到 5060um,以確保芯片劃片后的完整性和可靠性。一般芯片的預留劃片槽寬度與切制用金剛石砂輪劃片刀的推薦值如表 2-1 所示。機械劃片原理示意如圖 2-6所示。
激光切割屬于無接觸式劃片,不對晶圓產生機械應力,對晶圓的損傷較小,可以避免芯片破碎、損壞等問題 (見圖 2-7)。由于激光在聚焦上可達到亞微米數量級的特點,對晶圓的微處理更具有優勢。同時激光劃片速度可達 150mm/s,較機械劃片速率有很大提高,并可以勝任較薄晶圓的加工任務,也可以用來切割一些較為復雜形狀的芯片,如六邊形。但是昂貴的設備成本是制約激光劃片普及的因素之一。
劃片工藝步驟
劃片工藝開始前,首先要進行必要的準備工作;之后,是將待切割的晶圓片粘貼到藍膜上,將藍膜框架放人劃片機開始劃片過程,并實時清除掉劃片產生的硅渣和污物;最后,把分割開的芯片拾取、保存,具體步驟如圖 2-8 所示。
1. 準備工作
采用乙醇、無塵布擦拭貼膜機,并用氮氣槍吹凈工作臺面及區域,必要時,打開去離子風扇,吹淋工作區域,去除靜電干擾。檢查待劃片的晶圓(見圖2-9),核對晶圓數量、批次信息,確保晶圓完好無破損。
2、貼裝藍膜
貼裝藍膜后的晶圓如圖 2-10 所示。
- 藍膜
藍膜用來把晶圓背面固定在金屬膜框上,起到固定晶圓、束縛晶粒的作用,從而使晶圓被切割分開成晶粒后晶粒不會散落。晶圓一般按照尺寸區分,這里的尺寸指的是晶圓的直徑,常見的有6in、8in、12in。現在使用的高可靠電路,有一些穩定的老品種也使用4in 晶圓。藍膜也具有相應尺寸的不同規格。
藍膜的特征參數是厚度與黏附力。大多數用于硅晶圓劃片的藍膜厚度為 80~95um。膜的黏附力必須足夠大,保證劃片過程中能將已分離的每個晶粒牢牢地固定在膜上。當劃片完成后,又能很容易地從膜上取下晶粒。
最常用的是普通藍膜和紫外 (UV) 膜。普通藍膜的成本大約是 UV 膜的 1/3。UV 膜的粘接強度是可變的,經紫外線照射之后,由于其粘接劑聚合發生固化,其黏附力減小90%.更易脫膜、揭膜,且無殘留物。UV 膜具有極強的黏附力以固定晶圓,即使小晶粒也不會發生位移或剝除問題。通過紫外線照射降低黏附力,即使大晶粒也能輕松分揀,應力極其微弱,且晶粒背面無殘留物。
(2) 貼膜框
貼膜框又稱為晶圓環、膜框、金屬框架等,采用金屬材質,且具有一定的剛性,不會輕易變形,與貼膜機配套使用。貼膜框用于繃緊藍膜,固定晶圓,便于后期的晶圓劃片、晶粒分揀,避免晶圓切割后晶粒間由于藍膜褶皺相互碰撞擠壓而造成的損傷。
(3)裝配過程
圖2-11 給出了晶圓、藍膜及貼膜框的裝配圖,圖 2-12給出了晶圓、藍膜及貼膜框的裝配過程。首先,取出一片晶圓,正面朝下,背面朝上,將其放置在貼膜機工作盤上,打開真空開關,吸住晶圓。然后,將貼膜框放置在貼膜機工作臺上,使其中心與晶圓中心對齊,并將側邊定位框移動至貼膜框外側,將其左右限位。最后,拉出足夠長度的藍膜,拉緊后,貼在貼膜機后部,覆蓋整個貼膜框區域,用滾筒壓過藍膜,將晶圓、藍膜及框架裝配到一起。
3、晶圓切割
按照芯片大小將晶圓分割成單一的晶粒,用于隨后的芯片貼裝、引線鍵合等工序。雖然,機械劃片存在很多可靠性和成本上的問題,如晶圓機械損傷嚴重、晶圓劃片線寬較大、劃片速度較慢、需要冷卻水切割、刀具更換維護成本較高等,但是,機械切割現在仍然是主要的劃片方式。人們通過調整劃片工藝參數、選擇最佳的刀具類型、采用多次劃片等方式,來解決機械劃片中芯片崩邊、分層、硅渣污染等問題。劃片機切割晶圓如圖 2-13所示。
4、清洗
晶圓切割過程中主要是清洗劃片時產生的各種硅碎屑、粉塵,清潔晶粒,并對劃片刀起到降溫冷卻作用。
冷卻介質根據劃切材料的質量要求,用去離子水或自來水及其他冷卻介質。冷卻流量一般用流量計調節控制流量大小,正常為 0.2~4L/mn。流量大小要根據刀刃及劃切材料的種類和厚度來調節,流量大會沖走劃切中粘接不牢固的芯片,對特別薄的刀刃,流量大有時也影響刀刃的剛性:流量小又會影響刀刃壽命和劃切質量。
5、芯片拾取
用UV 光照射后,UV 膜黏性減退,便于拾取分割好的晶粒,如圖 2-14 所示
表 2-2 給出了劃片工序涉及的主要設備、部件及耗材和作用。
以上就是關于半導體集成電路封裝劃片方式、工藝步驟、準備工作及晶圓切割、芯片拾取的分享了,希望對大家能帶來幫助!如果您對半導體芯片、集成電路、推拉力測試機有任何不清楚的問題,歡迎給我們私信或留言,科準測控的技術團隊都會為大家解答!還想了解更多有關半導體集成電路的知識,敬請關注!
審核編輯 黃宇
-
芯片
+關注
關注
456文章
51155瀏覽量
426302 -
集成電路
+關注
關注
5391文章
11617瀏覽量
362826 -
半導體
+關注
關注
334文章
27687瀏覽量
221511 -
封裝
+關注
關注
127文章
7990瀏覽量
143276
發布評論請先 登錄
相關推薦
芯和半導體將參加2024集成電路特色工藝與先進封裝測試產業技術論壇
ASIC集成電路設計流程
集成電路工藝學習之路:從零基礎到專業水平的蛻變
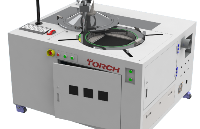
集成電路封裝基板工藝詳解:推動電子工業邁向新高度!
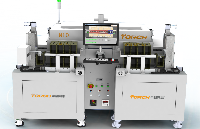
評論