鋼管作為原材料,廣泛應用于如石油、化工、電力、船舶、汽車等行業。近年來,經濟全球化發展使企業對產品質量提出更高要求,鋼管表面存在缺陷會嚴重影響其使用壽命,同時在設備某些重要位,使用劣質鋼管會存在安全隱患,嚴重威脅人員生命,對企業造成產財產損失。
因此,為了控制鋼管質量,相關企業會對其進行質量檢測,但檢測措施通常由人工實現,無法實現快速、精準檢測缺陷。 在鋼管生產的過程中,由于原材料、軋制設備和加工工藝等多方面的原因,將導致其表面出現劃痕、 輥痕、氧化鐵皮、表面夾雜、孔洞、裂紋、麻面等不同類型的缺陷。這些缺陷不僅嚴重影響產品的外觀,還降低了產品的抗腐蝕性、耐磨性和疲勞強度等性能,給企業的發展帶來不良影響,同時也增添以鋼管為原材料的下游產品使用過程中的安全隱患。 表面缺陷區域具有應力集中、受力薄弱的特點,同時性能突變、疲勞損傷和銹蝕往往集中在此區域, 使得鋼管在復雜惡劣環境下的工作性能大大降低。通過對鋼管表面存在的缺陷區域進行檢測,及時發現缺陷,為生產工藝的調整、設備狀態改進提供依據具有重要意義。 目前,鋼管的表面缺陷的檢測大多通過人工方式實現,人工方式依賴于現場經驗且效率低,受現場環境的影響,勞動強度大,易產生漏檢和誤檢現象,不能全面反應鋼管表面的質量,檢測實時性差,檢測種類少,檢測效率低,缺乏對產品的表面質量的綜合評估。隨著計算機水平的發展和人工智能領域的興起,機器視覺技術得到廣泛的應用,采用機器視覺方法能有效彌補人工檢測不足,且檢測精度高、能進一步為智能制造提供數據平臺。
01、鋼管表面缺陷檢測特點
國內外利用機器視覺方法檢測冶金產品的對象主要為板材、帶鋼、鋼條等,這些產品表面較平整、粗糙度低、材料反射率一致,只要保證入射光照角度合理,強度分布均勻,無論使用面陣或線陣相機均能獲取較為理想的被檢測材料表面缺陷圖像,這也有效降低了后續圖像處理算法的復雜程度; 如圖平面材料表面缺陷檢測的光照分布示意圖,通常采用單個或多個面陣相機即可獲得理想的光照結果;而采用線陣光源則更容易實現,因為被照射區域各點到達光源中心的距離是相等的。
平面材料表面缺陷檢測的光照分布示意圖 對于鋼管而言,因其幾何結構特點,當采用面陣光源時,弧形外表面使得光源中心與被照射區域各處之間距離相差過大,如圖所示,與光源最短距離位置處表現為較高亮度,而在最短距離位置兩測,光照亮度分布減弱,圖像成像結果也表現類似特點,中間區域像素灰度分布較高而兩側區域像素灰度值較小。
面陣光源光照分布(正視圖) 另一情況如圖所示,采用線陣相機和線陣光源實現鋼管表面缺陷動態檢測時,因振動、裝配誤差等因素,線陣光源中心線與線陣相機視野長度方向并非位于同一直線,相機視野方向通常與鋼管回轉中心所在直線一致;這種情況會降低照射區域與視野區域重合性,導致成像結果光照不均現象嚴重,進一步增加圖像處理的困難度。
線陣光源光照分布(俯視圖)
02、關鍵技術難點
鋼管因其幾何結構特點,易產生光照不均現象;為實現鋼管圓弧表面動態實時檢測,必然影響光源光照區域與相機視野的重合性,易造成光照分布不均,這種現象會覆蓋掉缺陷區域的特征。當圖像獲取不理想時,會增加圖像處理的難度。盡管相關學者在機器視覺檢測領域已經作了很多工作,但國內對鋼管的表面缺陷檢測的研究較少,主要存在如下難點:(1)熱軋無縫鋼管與熱軋帶鋼、重軌等類似,表面覆蓋大量氧化鐵皮,會導致各類偽缺陷的產生;(2)鋼管弧形外表面易產生光照不均現象;(3)因光照不均的影響,缺陷灰度差異較大,使得漏檢嚴重;(4)受彎曲度、不圓度和表面凸起缺陷的影響,鋼管在檢測過程中產生振動,使得圖像采集存在誤差,特征不明顯;(5)實現動態檢測時,光源照射區域與相機視野區域重合性會降低,進而造成光照分布不均。
03、成像光路設計
照明系統包括照明方式選擇,相機與光源的位置關系確定。 鋼管表面的照明方式可分為明場照明和暗場照明,本文選擇明場照明方式,該方式有益于鋼管表面缺陷和背景形成高對比度。由于采用單個線陣相機和線光源,其有效工作區為窄條,與其它冶金產品表面不同的是,熱軋無縫鋼管在成型過程中,因其工序工藝的特點,表面未經拋光處理,光照反射類型以漫反射為主。圖為明場照明光路結構圖。
根據圖像采集原理,需要確定線陣相機、線光源等的位置,這有益于后續硬件選型中參數的確定。 為保證視野區域能夠將不同長度的鋼管表面覆蓋,在光路設計中,使視野幅寬大于鋼管長度。
04、硬件參數設計
(1)相機線陣相機分為主要分為 CCD和CMOS兩種類型。 由于工作原理,CCD 的表面上會因靜電場存在導致表面吸吸附較多灰塵,這在實際工業檢查中受到限制,而 CMOS 芯片內部集成性較高,對硬件設計的優化具有促進作用,具有圖像捕捉靈活、靈敏度高、動態范圍寬、分辨率高、低功耗及優良的系統集成等優點,同時在價格方面比 CCD 傳感器更實惠。 基于圖像采集方案, 設計檢測精度要求為 0.5mm , 即能夠檢出最小缺陷尺寸為0.5mm*0.5mm, 視野幅寬H=300mm , 相機分辨率不能低于以下值:
(2)鏡頭鏡頭與檢測對象距離最近,其作用是將檢測對象聚焦在相機光敏元件上,通常需要考慮鏡頭的相關參數,保證與相機的合理搭配,提高成像質量。鏡頭選型包括焦距、成像靶面尺寸等參數確定。 焦距為鏡頭重要參數,需由物距等因素確定,由成像原理可知焦距計算如下: 式中,s 為光敏芯片長度;H 是視野幅寬,即相機能拍攝到的視野范圍;d 為物距。(3) 光源光源的合理選擇能夠對成像系統起到增益效果,例如提高對比度,降低無關信息對成像的干擾。根據鋼管表面圖像采集原理,需選擇線陣光源實現照明,這樣可保證在視野范圍內,光照強度集中且均勻。 由于 LED 光源具有高效率、 低耗電量、 長壽命、 安全性高和可控性好等特點,本文以 LED 光源實現照明。
05、缺陷檢測
鋼管表面缺陷為凹坑、劃傷、翹皮及輥痕4 種缺陷,圖 (a)為凹坑缺陷, 其特征為點狀或塊狀凹陷,因氧化皮或異物未清除在軋制過程中嵌入鋼管表面再脫落形成;圖 (b)為翹皮缺陷,為附著在鋼管外表面的金屬層,在穿管深加工工序中,聚集夾雜物因管壁變薄而外漏,裂紋形成并延伸使表皮外翹;
圖 (c)為劃傷缺陷,鋼管表面被外金屬或硬物劃削所致,通常呈細長尖銳溝紋或較淺凹坑;圖 (d)為輥痕缺陷,該缺陷是由于軋輥調整不當或表面損壞所造成, 呈周期性或連續性分布。
在提取鋼管表面缺陷特征之前,需要確定那些特征是有效的,對于凹坑、翹皮、劃傷和輥痕,需要選擇具有良好區分度的特征構成特征向量;特征向量是缺陷特征數值化表征方式,特征提取通常遵循如下原則:1)圖像中特征應該容易獲取;2)所選擇特征在數值上不受噪聲和無關因素干擾;3)同種缺陷的特征具有緊致性, 不同種缺陷特征具有良好的區分度。 鋼管表面缺陷分布和大小不具規律性,且形態復雜,因此需要選擇能夠準確描述缺陷的特征。 機器視覺技術將CCD相機拍攝到的目標圖像實時轉換成圖像信號,然后將圖像信號輸入進嵌入式視覺圖像處理系統。 根據圖像飽和度、像素分布、目標圖像邊沿、亮度等信息轉換成計算機識別的數字信號,利用先進的算法對圖像進行特征識別,將特征識別出來的結果進行評價,輸出最終的缺陷結果,包括缺陷、尺寸、角度、個數、合格與不合格、有無等,實現自動識別功能。
總而言之,鋼管缺陷檢測系統采用的機器視覺自動識別的要求,必須解決以下主要問題:1.必須能在線檢測鋼管表面的瑕疵,如劃痕、刮傷、孔洞、結疤、墊坑等表面異常。 2.能應對因鋼管寬度、長度變化、以及鋼管在移動過程中產生的扭曲或傾斜、表面有油污或水滴所造成的干擾。 3.瑕疵檢測具備自學習、自適應功能適合于不同寬度、不同顏色、不同速度的要求,還必須應用模式識別、自動暴光、防抖動、瑕疵報警等功能,瑕疵檢測和瑕疵報警是動態實時的。 4.必須具備精度高、故障點少等特點,需用工業級數字攝像機和工業級PC機相結合來完成系統任務。
審核編輯:郭婷
-
計算機
+關注
關注
19文章
7520瀏覽量
88225 -
機器視覺
+關注
關注
162文章
4389瀏覽量
120446 -
人工智能
+關注
關注
1792文章
47442瀏覽量
238992
原文標題:基于機器視覺的鋼管表面缺陷檢測方法
文章出處:【微信號:vision263com,微信公眾號:新機器視覺】歡迎添加關注!文章轉載請注明出處。
發布評論請先 登錄
相關推薦
云計算HPC軟件關鍵技術
機器視覺檢測系統的關鍵技術和應用場景
基于AI深度學習的缺陷檢測系統
柔性制造系統的關鍵技術有哪些
儲能BMS的關鍵技術是什么
賽默斐視X射線薄膜測厚儀與薄膜表面缺陷檢測
基于深度學習的芯片缺陷檢測梳理分析
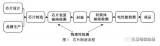
評論