退火工藝又稱為熱退火 (Thermal Annealing),其過程是將硅片放置于較高溫度環境中一定的時間,使硅片表面或內部的微觀結構發生變化,以達到特定的工藝目的。退火工藝的最關鍵的參數為溫度和時間,溫度越高、時間越長,熱預算(Thermal Budget)越高。在實際集成電路制造工藝中,熱預算都有嚴格的控制。如果工藝流程中有多步退火工藝,則熱預算就可以表達為多次熱處理的疊加,即
DT(eff)=DT(1)+DT(2)+…+DT(n)
隨著工藝節點的微縮,在整個工藝過程中容許的熱預算越來越少,即高溫熱過程的溫度變低、時間變短。 通常,退火工藝是與其他工藝(如離子注入、薄膜沉積、金屬硅化物的形成等)結合在一起的,最常見的就是離子注入后的熱退火。離子注入會撞擊襯底原子,使其脫離原本的晶格結構,而對襯底晶格造成損傷。熱退火可修復離子注入時造成的晶格損傷,還能使注入的雜質原子從晶格間隙移動到晶格點上,從而使其激活。晶格損傷修復所需的溫度約為 500°C,雜質激活所需的溫度約為950°C 。
理論上,退火時間越長、溫度越高,雜質的激活率越高,但是過高的熱預算將導致雜質過度擴散,使得工藝不可控,引發最終的器件和電路性能退化。因此,隨著制造工藝的發展,傳統的長時間爐管退火已逐漸被快速熱退火(Rapid Thermal Annealing, RTA)取代。 在制造工藝中,某些特定的薄膜在沉積后需要經過熱退火過程,以使薄膜的某些物理或化學特性發生變化。例如,疏松的薄膜變得致密,改變其在干法刻蝕或濕法刻蝕時的速率;或者在高k柵介質生長后進行退火 (Post Deposition Annealing, PDA),改善高k介質的特性,可降低柵泄漏電流,并提高介電常數。還有一種使用得較多的退火工藝發生在金屬硅化物 (Silicide)形成過程中。
金屬薄膜如鈷、鎳、鈦等被濺射到硅片表面,經過較低溫度的快速熱退火,可使金屬與硅形成合金。某些金屬在不同的溫度條件下形成的合金相不同,一般在工藝中希望形成接觸電阻和本體電阻均較低的合金相。 如前所述,根據熱預算需求的不同,退火工藝分為高溫爐管退火和快速熱退火。高溫爐管退火是一種傳統的退火方式,其溫度較高且退火時間較長,熱預算很高。在一些特殊的工藝中,如注氧隔離技術 ( Seperation by Implantation of Oxygen,SIMOX)制備 SOI 襯底、深n井(Deep n-Well)擴散驅入 (Drive-in)工藝中應用較多,此類工藝一般需要通過高的熱預算來獲得完美的晶格或均勻的雜質分布。
快速熱退火是用極快的升/降溫和在目標溫度處的短暫停留對硅片進行處理,有時也稱快速熱過程 ( Rapid Thermal Processing, RTP)。在形成超淺結過程中,快速熱退火在晶格缺陷修復、雜質激活、雜質擴散最小化三者之間實現了折中優化,在先進技術節點的制造工藝中必不可少。升/降溫過程及目標溫度短暫停留共同組成了快速熱退火的熱預算。傳統的快速熱退火溫度約為1000°,時間在秒量級。
近年來對其要求越來越嚴格,逐漸發展出閃光退火(Flash Lamp Annealing, FLA)、尖峰退火(Spike Anneal)及激光尖峰退火(Laser Spike Annealing, ISA),退火時間達到了毫秒量級,甚至有向微秒和亞微秒量級發展的趨勢。激光退火最獨特的優點是空間上的局域性和時間上的短暫性,采用激光光源的能量來快速加熱晶片表面到臨界熔化點溫度。由于硅的高熱導率,硅片表面可以在約 0. 1ns時間內快速降溫冷卻。激光退火系統可以在離子注入后以最小的雜質擴散激活摻雜物離子,已被用于 45nm 以下工藝技術節點。激光退火系統可與尖峰退火系統一起使用,以實現最優的結果。
審核編輯 :李倩
-
工藝
+關注
關注
4文章
656瀏覽量
29165 -
退火
+關注
關注
0文章
5瀏覽量
6738
原文標題:退火工藝(Thermal Annealing)
文章出處:【微信號:Semi Connect,微信公眾號:Semi Connect】歡迎添加關注!文章轉載請注明出處。
發布評論請先 登錄
相關推薦
TS3DV520ERHUR中間的EXPOSED THERMAL PAD接到哪里?
離子注入的目的及退火過程
ADS1292系列VQFN封裝的芯片,Thermal pad該如何處理?
激光退火后,碳化硅襯底TTV變化管控
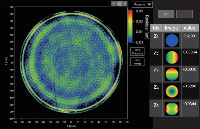
硅鍺材料、硅退火片和絕緣體上硅(SOI)的介紹
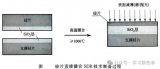
在實際的電氣連接中,是直接將Exposed Thermal Pad連接到AGND嗎?
軸承結構生產工藝流程柴油機軸承的結構與安裝
請問CDCLVC1310的Thermal Pad需要接地嗎?
INA826AIDRGR的DFN封裝中Exposed Thermal Die Pad是否接地?
TC wafer 快速退火爐溫場均勻性校準 熱電偶校準儀
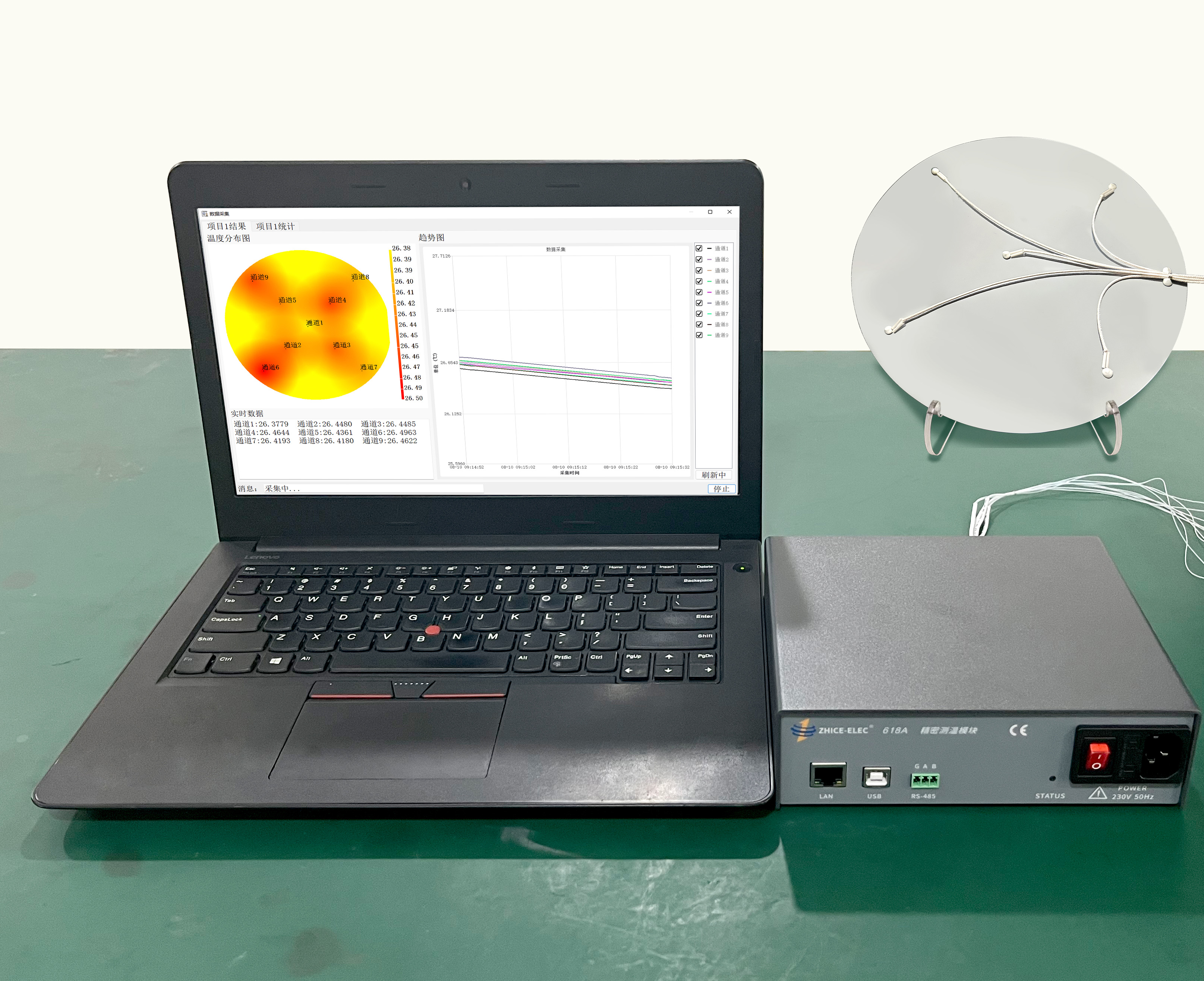
評論