車削作為常見的加工方式之一,用于加工軸、盤、套和其他具有回轉(zhuǎn)表面的回轉(zhuǎn)體或非回轉(zhuǎn)體工件。今天我們來分享一篇干貨滿滿的車削經(jīng)驗,從外圓車削、內(nèi)圓車削、硬零件車削技巧以及提升工件質(zhì)量等方面幫助大家。
外圓車削應(yīng)用技巧
易于振動的零件
一次走刀完成切削(例如管件)
建議通過一次走刀完成整個切削,以將切削力沿軸向引導(dǎo)至夾頭/主軸方向。
示例:
外徑(OD)=25mm(0.984英寸)
內(nèi)徑(ID)=15mm(0.590英寸)
切深ap=4.3mm(0.169英寸)
得到的壁厚=0.7mm(0.028英寸)
可使用接近90°的主偏角(接近0°的切入角)沿軸向引導(dǎo)切削力。這將最大限度地減少零件受到的彎曲力。
兩次走刀完成切削
同步進行的上下刀架加工將使徑向切削力達(dá)到平衡,并避免零件振動和彎曲。
細(xì)長/薄壁零件
車削細(xì)長/薄壁零件時,應(yīng)考慮以下因素:
使用接近90°的主偏角(接近0°的切入角)。在加工過程中,即使是微小的變化(主偏角/切入角從91°/-1°變?yōu)?5°/-5°)也將影響切削力方向
切深ap應(yīng)大于刀尖半徑RE。大切深ap將增加軸向力Fz并減小徑向切削力Fx,從而減少振動
使用具有鋒利切削刃和小刀尖半徑RE的刀片,由此降低切削力
考慮使用金屬陶瓷或PVD材質(zhì),以確保耐磨性和鋒利的刀片切削刃,這是此類工序的首選
臺肩加工/臺肩車削
遵照步驟1~5以免損壞刀片切削刃。這種方法非常適用于CVD涂層刀片,可大大減少刀片斷裂。
第1~4步:
使每個步驟(1~4)的距離與進給率保持相同,以免堵屑。
第5步:
通過從外徑開始朝向內(nèi)徑進行一次垂直切削來完成最后切削。
如果對臺肩進行端面車削時的加工順序是由內(nèi)徑到外徑,則也可能出現(xiàn)切屑卷繞在刀具半徑上的問題。更改刀具路徑可以改變切屑方向并解決問題。
車端面
從車端面(1)和倒角(2)開始。如果可能且工件的幾何條件允許,則優(yōu)先加工倒角(3)。縱向切削(4)是最后一道工序,刀片在加工過程中將平穩(wěn)進刀和退刀。 端面車削應(yīng)是在零件上設(shè)置下一次走刀的參考點的第一道工序。 當(dāng)切削刃離開工件時,在切削末端形成毛刺,這通常比較麻煩。離開倒角或圓角(翻轉(zhuǎn)圓角)可以最小化甚至避免毛刺形成。 零件上的倒角將使刀刃能夠更順利地進入(無論是端面還是縱向車削)。
斷續(xù)切削
進行斷續(xù)切削加工時:
在快速斷續(xù)切削(例如六角棒材)應(yīng)用中,使用PVD材質(zhì)確保刃線韌性
在大型零件和重載斷續(xù)切削應(yīng)用中,使用韌性CVD材質(zhì)確保整體韌性
考慮使用高強度斷屑槽充分提高抗崩刃性能
關(guān)閉冷卻液可能有利于避免熱裂紋
在精加工零件上加工出退刀槽使用盡可能大的刀尖半徑RE進行縱向車削和端面車削,由此可確保:
高強度切削刃,更高的可靠性
良好的表面質(zhì)量
能夠使用高進給
不要超過退刀槽寬度,將其作為去除毛刺的最后一道工序執(zhí)行。
內(nèi)圓車削應(yīng)用技巧
選擇盡可能大的鏜桿直徑,但同時應(yīng)確保在鏜桿與孔之間留出足夠的排屑空間
確保所使用的切削參數(shù)有利于充分排屑,并產(chǎn)生正確的切屑類型
選擇盡可能小的懸伸,但同時應(yīng)確保鏜桿長度能夠?qū)崿F(xiàn)推薦的夾緊長度。夾緊長度不得小于鏜桿直徑的3倍
加工振動敏感零件時,使用減振鏜桿
選??????????????擇?????????????????盡???????????可能接近90°的主偏角(接近0°的切入角),以沿著鏜桿引導(dǎo)切削力。主偏角不得小于75°(切入角不得大于15°)
作為首選,可轉(zhuǎn)位刀片應(yīng)具有正前角基本形狀和正前角刀片槽型,以最大限度地減小刀具偏斜
選擇小于切深的刀片刀尖半
切削刃吃刀量不足可能增加由切削過程中的摩擦導(dǎo)致的振動
選擇大于刀尖半徑的切削刃吃刀量,以確保良好的切削作用
切削刃吃刀量過大(大切深和/或進給)可能增加由刀具偏斜導(dǎo)致的振動
無涂層或薄涂層刀片產(chǎn)生的切削力通常要低于厚涂層刀片。當(dāng)長徑比較大時,這一
點變得尤為重要。鋒利的切削刃通常能夠最大限度地減少振動趨勢,從而提高孔質(zhì)量
對于內(nèi)圓車削而言,具有開放式斷屑槽的槽型通常更有利
在某些工序中,可以考慮韌性水平更高的刀片材質(zhì),因為它能應(yīng)對任何切屑堵塞風(fēng)險或振動趨勢
如果需要改善切屑形成,可考慮修改刀具路徑??????????????????????
硬零件車削應(yīng)用技巧
除了一般車削建議之外,硬零件車削還有一些關(guān)鍵考慮因素(如生產(chǎn)過程包括在硬化之前的軟車階段零件準(zhǔn)備):
避免毛刺
保持嚴(yán)格尺寸公差
在熱處理前進行倒角和加工半徑
不要突然進刀或退刀
通過圓弧切入或切出進刀或退刀
表面測量
X軸:特征長度
Y軸:直徑偏差
裝夾
良好的機床穩(wěn)定性、工件正確夾緊和定位至關(guān)重要
總的準(zhǔn)則是,對于只有一端受到支撐的工件,一般推薦工件長徑比不超過2:1。如果存在附加的尾座支撐,則可增加長徑比
請注意,卡座和尾座的熱對稱設(shè)計將進一步增加尺寸穩(wěn)定性
使用Coromant Capto系統(tǒng)
最大限度地減少所有懸伸,以最大限度地提高系統(tǒng)剛性
對于內(nèi)圓車削,考慮硬質(zhì)合金刀柄鏜桿和Silent Tools
刀片微觀槽形
兩種典型的刃口鈍化CBN刀片是S型和T型。
S型:具有最佳刃邊強度。具有抗微崩刃性能,可確保一致的表面質(zhì)量。
T型:能夠在連續(xù)切削中實現(xiàn)最佳表面質(zhì)量,在斷續(xù)切削中盡可能減少毛刺形成。切削力較低。
刀尖槽形
如果工況穩(wěn)定,請務(wù)必使用Wiper(修光刃)槽型以確保最佳表面質(zhì)量。
對生產(chǎn)率要求較高時,使用小主偏角刀片。
當(dāng)穩(wěn)定性較差(細(xì)長工件等)時,應(yīng)使用常規(guī)半徑刀片。
濕式或干式加工
不使用冷卻液進行硬零件車削是理想情況,并且完全可行。CBN和陶瓷刀片都能承受較高的切削溫度,因此消除了與冷卻液有關(guān)的成本問題和難題。 某些應(yīng)用可能需要冷卻液,例如為了控制工件的熱穩(wěn)定性。在這些情況下,確保冷卻液在整個車削工序中的連續(xù)流動。 通常,加工時產(chǎn)生的熱量會分配給切屑(80%)、工件(10%)和刀片(10%)。由此可以看出從切削刃區(qū)域排屑的重要性。
切削參數(shù)和磨損
切削刃區(qū)域中的高熱量減小了切削力。因此,切削速度過低會產(chǎn)生較少的熱量并可能導(dǎo)致刀片破裂。
月牙洼磨損會逐漸影響刀片強度,但不會對表面質(zhì)量產(chǎn)生同等程度的影響。相反地,后刀面磨損會逐漸影響尺寸公差。
決定刀具壽命的磨損比例
*) 后刀面磨損 **) 月牙洼磨損
換刀準(zhǔn)則
預(yù)定表面質(zhì)量(B)是一種常用且實用的換刀標(biāo)準(zhǔn)。表面質(zhì)量會在一個單獨的工位自動測量,并給出表面質(zhì)量的規(guī)定值。
為了實現(xiàn)優(yōu)化且更加穩(wěn)定的加工過程,將預(yù)定零件數(shù)(A)設(shè)為換刀標(biāo)準(zhǔn)。該值應(yīng)比平均零件數(shù)小10%~20%,確切的數(shù)值根據(jù)具體情況而定。
A:預(yù)定零件數(shù)
B:預(yù)定表面質(zhì)量
X軸:零件數(shù)
Y軸:表面質(zhì)量
藍(lán)線:刀片磨損
紅線:最大Ra/Rz值
一次切削策略一次切削“金屬去除”策略對于外圓和內(nèi)圓工序都是可行的。在內(nèi)圓車削中,穩(wěn)定裝夾非常重要,刀具懸伸不應(yīng)超過鏜桿直徑(1×D)。為了獲得良好的加工結(jié)果,建議使用經(jīng)過倒棱處理的輕微珩磨刀片以及中等切削速度和進給。 優(yōu)點
盡可能快的加工時間
一個刀位
缺點
難于滿足小的尺寸公差
刀具壽命較短(與二次切削相比)
因磨損相對較快而出現(xiàn)尺寸偏差
兩次切削策略
兩次切削策略可使用在無人化生產(chǎn)加工高表面質(zhì)量。建議使用半徑為1.2 mm(0.047英寸) 的粗加工刀片以及只有一條倒棱的T型精加工刀片。兩種刀片都應(yīng)采用Wiper(修光刃)槽形。
優(yōu)點
刀具針對粗加工和精加工經(jīng)過優(yōu)化
更高的安全性、更小的公差和可能更長的換刀間隔
缺點
需要兩個刀片
兩個刀具位置
一次換刀
為了獲得高質(zhì)量的車削零件,切屑控制是需要考慮的最重要因素之一。選擇正確的切削參數(shù)并運用我們的應(yīng)用技巧可獲得理想的零件質(zhì)量。
成功的切屑控制
切屑控制是車削加工的關(guān)鍵因素之一,含有3種基本的斷屑形式變化:
自斷屑(例如灰口鑄鐵)
撞擊刀具斷屑
撞擊工件斷屑
自斷屑
撞擊刀具斷屑
撞擊工件斷屑
斷屑的影響因素
刀片槽型:切屑更開放還是更緊湊取決于容屑槽的寬度以及微觀和宏觀結(jié)構(gòu)設(shè)計
刀尖半徑:小刀尖半徑對切屑的控制程度要高于大刀尖半徑
主偏(切入)角:根據(jù)主偏角,切屑被引導(dǎo)至不同的方向:朝向臺肩或遠(yuǎn)離臺肩
切深:根據(jù)工件材料,更大的切深將影響斷屑,從而產(chǎn)生更大的切削力來實現(xiàn)斷屑和排屑
進給:更高的進給通常將產(chǎn)生強度更高的切屑。在某些情況下可能有助于斷屑和切屑控制
切削速度:切削速度變化可能影響斷屑性能
材料:短切屑材料(例如鑄鐵)通常容易加工。對于具有出色的機械強度和抗蠕變性(材料緩慢移動或在壓力之下變形的趨勢)的材料(例如Inconel),斷屑性能更受關(guān)注
車削的切削參數(shù)
為車削選擇正確的速度和進給時,請務(wù)必考慮機床、刀具、刀片和材料。
開始時使用低進給率,以確保刀片安全性和表面質(zhì)量;然后提高進給率,以改進斷屑性能
使用大于刀尖半徑的切深。這樣可將刀片的徑向偏斜減至最小,這在內(nèi)圓加工中很重要
切削速度設(shè)置過低將縮短刀具壽命。請務(wù)必使用推薦的切削速度vcm/min(英尺/分鐘)
使用冷卻液提高車削零件質(zhì)量
如果正確應(yīng)用,冷卻液將提高加工安全性、刀具性能和零件質(zhì)量。使用冷卻液時,應(yīng)考慮以下因素:
強烈建議將采用高精度冷卻液的刀具用于精加工應(yīng)用
斷屑所需的冷卻液壓力取決于噴嘴直徑(出口)、所加工的材料、切深和進給
所需的冷卻液流量取決于壓力和冷卻液孔的總冷卻液輸送面積
在半精加工和粗加工應(yīng)用中,建議使用下方冷卻液
對于精加工工序,建議同時使用高精度上方冷卻液和下方冷卻液
通過正確使用冷卻液應(yīng)對各種挑戰(zhàn)
切屑控制問題:使用上方冷卻液
尺寸問題:原因通常是溫度過高 - 同時使用上方和下方冷卻液以及盡可能高的冷卻液壓力
表面質(zhì)量差:如果缺陷是由切屑導(dǎo)致的,則使用上方冷卻液
粗加工工序中的刀具壽命不可預(yù)測:僅使用下方冷卻液
精加工工序中的刀具壽命不可預(yù)測:同時使用上方和下方冷卻液
內(nèi)圓車削工序排屑不良:同時使用上方和下方冷卻液,以及盡可能高的冷卻液壓力
在車削零件時如何獲得良好的表面質(zhì)量
表面質(zhì)量的通用規(guī)則:
通常可通過使用更高的切削速度來提高表面質(zhì)量
刀片槽型(中置型、正前角和負(fù)前角以及正后角)會影響表面質(zhì)量
刀片材質(zhì)的選擇對表面質(zhì)量有一些影響
如果出現(xiàn)振動趨勢,則選擇更小的刀尖半徑
Wiper(修光刃)刀片
Wiper(修光刃)刀片能夠以高進給率車削零件,而不會失去加工出良好表面質(zhì)量的能力或斷屑能力。 一般準(zhǔn)則是:進給率提高一倍,相同的表面質(zhì)量。相同的進給率,表面質(zhì)量提高一倍。 Wiper(修光刃)刀片的設(shè)計能夠使刀片沿著工件進給時加工出的表面更光滑,修光刃效果主要為直線車削和端面車削而設(shè)計。
標(biāo)準(zhǔn)半徑
Wiper(修光刃)半徑
標(biāo)準(zhǔn)刀片與Wiper(修光刃)刀片基于進給率的比較
注意!與標(biāo)準(zhǔn)刀尖R角對應(yīng)的所有值都是理論值。與Wiper (修光刃) 刀尖R角對應(yīng)的值是基于低合金鋼的試驗值。
審核編輯 :李倩
-
車削
+關(guān)注
關(guān)注
0文章
17瀏覽量
8260
原文標(biāo)題:高質(zhì)量的車削經(jīng)驗,一篇干貨,拿走
文章出處:【微信號:AMTBBS,微信公眾號:世界先進制造技術(shù)論壇】歡迎添加關(guān)注!文章轉(zhuǎn)載請注明出處。
發(fā)布評論請先 登錄
相關(guān)推薦
電子工程師的電源設(shè)計經(jīng)驗分享
電子工程師的經(jīng)驗分享
提升開關(guān)電源效率的理論分析與實戰(zhàn)經(jīng)驗
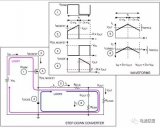
干貨來嘍!實用樹莓派Linux編譯指南
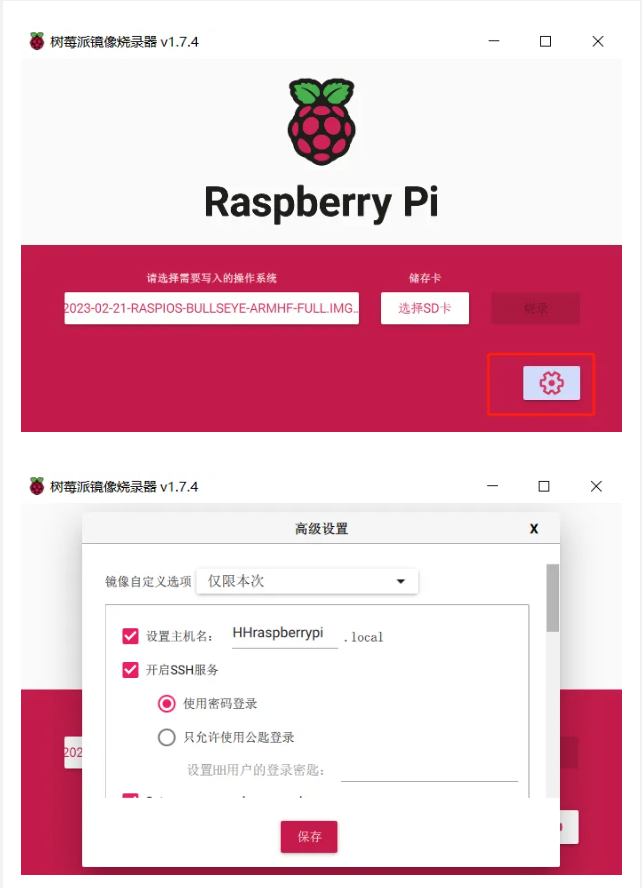
數(shù)控車削中的粗加工的編程方法
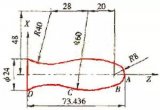
AI干貨補給站04 | 工業(yè)AI視覺檢測項目實施第三步:模型構(gòu)建
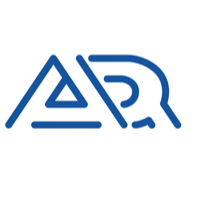
AI干貨補給站03 | 工業(yè)AI視覺檢測項目實施第二步:數(shù)據(jù)收集
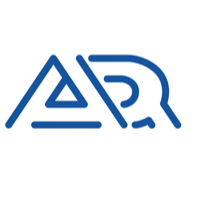
AI干貨補給站 | 深度學(xué)習(xí)與機器視覺的融合探索
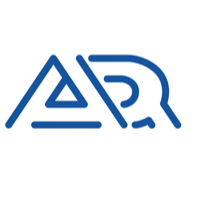
Kennametal以三款全新車削產(chǎn)品擴展其傳統(tǒng)產(chǎn)品系列
干貨滿滿!一文了解AGV軟件系統(tǒng)的構(gòu)成
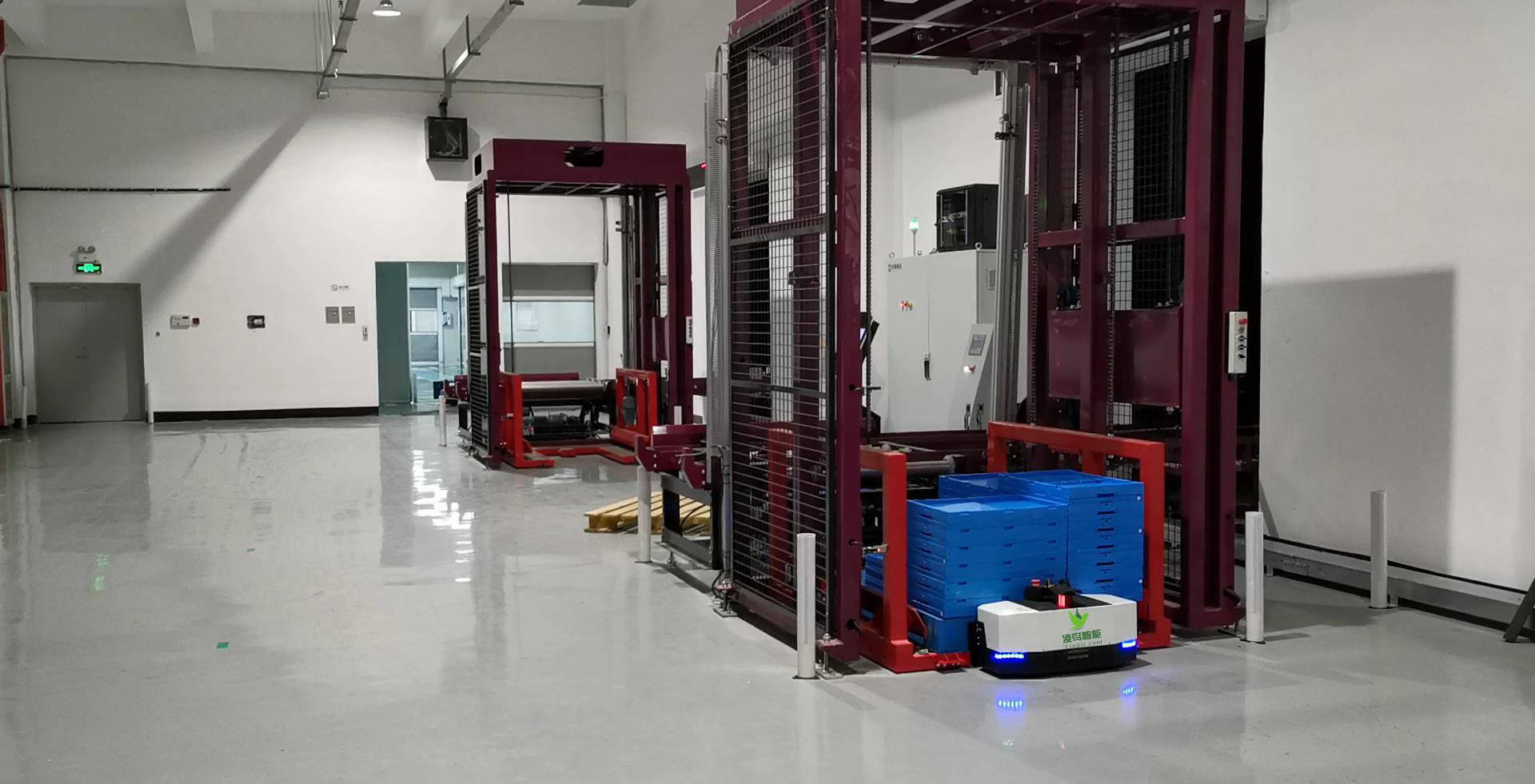
滿滿干貨,談?wù)凩oRa和星閃的現(xiàn)在與未來
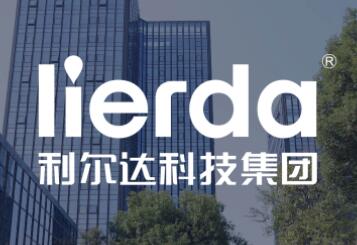
干貨滿滿:ARM的內(nèi)核寄存器講解
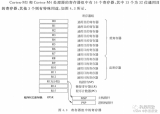
議題預(yù)告|電子峰會干貨滿滿!
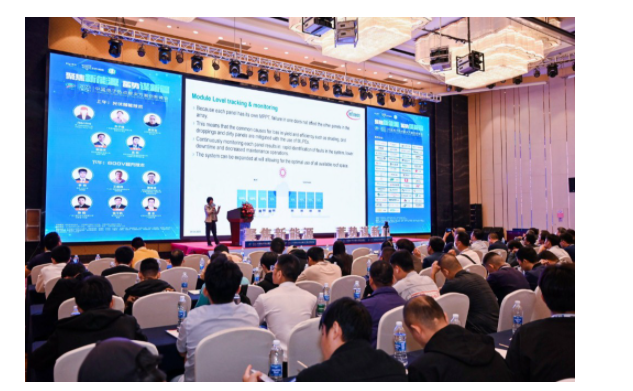
V2X與ETC到底有什么不同?
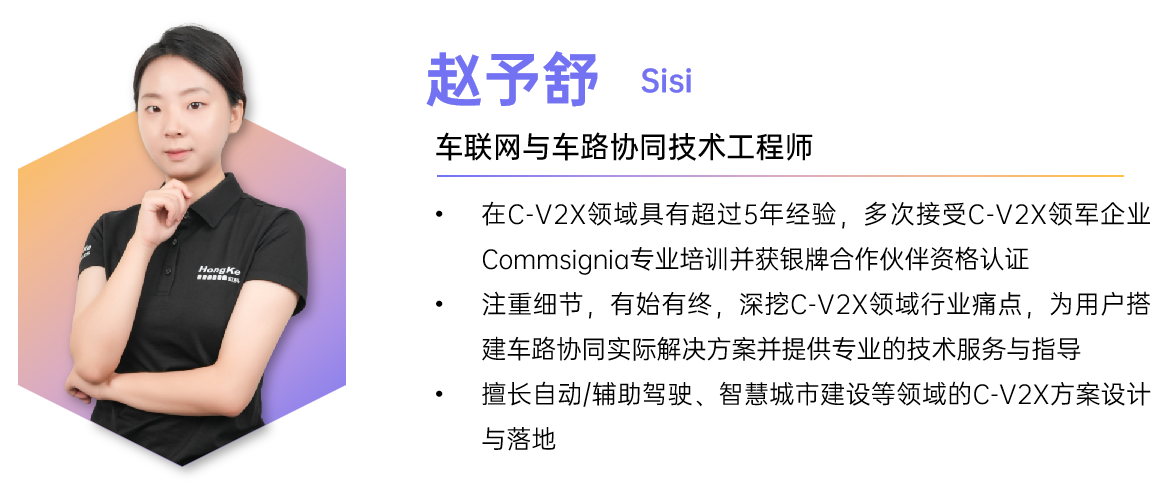
評論