軟磁材料很神奇,締造了一系列從前難以想象的變化。
1946年,世界上第一臺電子計算機ENIAC誕生,長30.48米,寬1米,占地面積170平方米。而不過20年后,第三代電子計算機開始發展,體積縮小千倍以上。
這種像“魔法”一樣的變化,除了與集成電路的現世有關,還與電源技術密不可分。因為要為電子設備“瘦身”,首先得讓電源變壓器小型化,高頻開關電源隨之出現在公眾視野。這種電源的變壓器、電感器、扼流圈等,均使用了軟磁鐵氧體磁心材料。
上世紀80年代以前,能與國外先進產品競爭的國產軟磁鐵氧體材料及磁心幾乎為零。但在一代人的努力下,我國的軟磁鐵氧體磁心最終實現了零的突破。其中有一位專家,對標業內國際巨頭,成功開發出國內第一代至第三代功率鐵氧體,推動了軟磁鐵氧體材料的換代升級,促進了國內電源應用的發展。他甚至主導和參與了軟磁鐵氧體磁心的部分國際標準的制定,讓中國在這一材料領域的話語權日益強硬。
他便是南京新康達磁業股份有限公司總經理趙光。
在光伏、5G、新能源汽車等新興產業快速發展的今天,對軟磁鐵氧體材料提出了更高應用頻率、更低功耗的要求,樂于挑戰的趙光看見了更寬廣的施展空間。
01
關鍵材料國產化,萬元彩電跌落神壇
上世紀80年代初,趙光的父母托一位回大陸的香港朋友購買了一臺日本松下原裝18吋彩電,花了近萬元人民幣。
在那個年代,花近萬元買一臺彩電是件奢侈的事情。而當時的彩電之所以價格昂貴,在于關鍵材料和彩電整機未能實現大規模國產化,極為依賴進口。
據統計,上世紀七十年代初期,國內僅有天津、北京等地幾個廠家試制出為數不多的彩電整機;1978年,我國彩電年產量不到4000臺;到了1989年,全國彩電擁有數量約3600萬臺,普及率仍不到20%。
人民生活物質需求在日益增長,彩電成為普通家庭夢寐以求的大家電。為了滿足這一需求,早在1982年,我國便提出彩電國產化的目標,力爭自主制造彩電內部的所有零件和整機。
位于江蘇南京的國營第898廠作為國家電子工業部四大部署磁性材料的企業之一,接到的任務是開發生產彩電行輸出變壓器磁心(U型磁心)和開關電源磁心(E型磁心)。
行輸出變壓器是彩電中的核心器件之一,用于提供顯像管所需的上萬伏高壓和其它各種電壓及行同步信號;而開關電源則是彩電運行的能量來源。
實際上,國內的軟磁鐵氧體材料在上世紀五十年代就已經起步,但生產裝備、工藝技術和產品性能質量,相對國外先進水平而言十分落后,無法滿足制造彩電的需求。于是電子工業部組織四大部署企業從德國、瑞士、日本等發達國家引進先進的設備和技術。
此時,剛畢業的趙光加入國營第898廠,參與了技術引進的過程。“當時國內落后的磁性材料行業,第一次得到了向國外先進水平看齊的機遇。”趙光對《大國之材》說。
這次的設備和技術引進,為國內的軟磁鐵氧體產業夯實了基礎。當時,不少鄉鎮企業感到軟磁鐵氧體材料前景良好,紛紛投資建廠。有一些實力較強的鄉鎮企業,如江蘇王莊、港下等地的磁性材料廠,憑借較好的資金底子,也仿效898廠跑到國外采購設備。
引進西方先進的設備和技術后,國內開始仿造壓機、窯爐、磨床等軟磁鐵氧體生產專用設備,整個行業開始步入發展的春天。軟磁鐵氧體材料的國產化之路就這樣轟轟烈烈地搞了起來。
在此之前,一付彩電所用的行輸出U型磁心,進口價格為15元。隨著國產化的推進,產能、交貨期等獲得大幅度改善,生產成本下降,售價也因此一路下跌到2元左右。
緊隨其后,彩電的價格也大幅下降,得以走進更多百姓家庭。
但實現彩電國產化并非磁性材料行業發展的最終目的,服務于更多的領域,才是磁性材料發展的價值所在。
技術引進后,國內軟磁鐵氧體生產水平是有了大幅度的提升,但與國際先進水平仍有不小差距。當時,彩電的行掃描頻率僅為16kHz,這意味著引進技術所制造出的軟磁鐵氧體材料只能在十多kHz這樣較低的頻率下工作,無法勝任更高頻的工作場景。
而隨著電力電子技術的發展,電子設備的工作頻率越來越高,從線型電源的50Hz工頻到早期開關電源的20kHz低頻,再到數百kHz的高頻,甚至達到數兆Hz。
軟磁鐵氧體材料有一個關鍵指標是功率損耗,在工作頻率上升后,材料的功耗會隨頻率的1.3~2次方呈指數型增加,功耗上升引起元器件發熱,不僅消耗了寶貴的電能,而且會導致故障。
為了打破這一“魔咒”,行業不得不將軟磁鐵氧體材料換代升級。
或許趙光不曾想過,自己會成為推進這一材料改進的主導者。
02
對標國際巨頭,進一步為電子設備“瘦身”
上世紀八、九十年代,正值中國電子信息產業快速發展、傳統工業改造及節約能源理念逐漸被重視的階段。
相關數據顯示,“九五”期間,中國電子工業同比上一個五年增長了近12倍。傳統工業系統也進入了更新換代期,大量先進的電子技術和設備被采用,對供電質量提出高要求。電子設備小型化、智能化、高效率、高可靠、節能的呼聲也日益強烈。
這些都考驗著電源產業的迭代能力,倒逼著磁性材料技術的發展。
傳統線型電源采用的磁性材料是硅鋼片,制造出的工頻變壓器又大又笨重,行業意識到,只有采用開關式電源,才能實現小型化。但開關式電源的常見工作頻率在100kHz左右,而國內當時制造出的軟磁鐵氧體材料僅支持16kHz的工作場景,差距十分明顯。
開發出新一代功率鐵氧體材料才是出路!
當時已在國營第898廠研究所工作的趙光接過了這項任務,但國內并沒有相關的案例可借鑒,于是趙光把目光投向了日本產業界。
彼時的日本電子產業正值繁榮時期,電腦、打印機、通訊設備、照明等均采用新型功率鐵氧體材料,紛紛實現了小型化與節能。而最具代表性的新型功率鐵氧體材料來自于日本TDK公司,其產品當時在國際市場的占有率列居首位。
TDK公司先后研發出PC30、PC40、PC50三代功率鐵氧體材料,每推出一代,可應用的頻率就越高。這三代功率鐵氧體材料被國際磁性材料行業視為標桿,趙光也以此為標桿,展開了對標TDK的國內第一代功率鐵氧體的研發工作。
趙光回憶道,當時的研發條件相當簡陋,缺乏先進的分析測量儀器和實驗設備,做實驗只能采用很原始的方法。
趙光采用手工的方式,用球磨罐一罐一罐地混合和粉粹材料,在手動真空燒結爐內,一爐一爐地試燒磁心;沒有電腦存儲和處理海量的試驗數據,趙光就用紙、筆記錄、用計算器計算,很快就用掉了厚厚的幾大記錄本;缺乏最新的參考文獻,他就設法通過在國外大學工作的同學代為尋找資料。
經過兩年艱辛的付出,趙光團隊終于完成了對標日本TDK公司PC30材料的國產功率鐵氧體材料的開發。1988年,我國第一代功率鐵氧體材料完成了技術鑒定,1989年獲得電子工業部科技進步三等獎。
在接下來近十年時間里,趙光又帶領團隊完成了對標TDK公司PC40和PC50材料的國產第二代、第三代功率鐵氧體的開發工作,分別獲得機械電子工業部科技進步二等獎和三等獎,還榮獲國家科技委頒發的國家科技成果完成者證書。
三代材料的成功研發和量產,使得國產功率鐵氧體技術水平大幅提升。盡管比日本的三代材料推出時間遲了數年,但這從無到有的突破實屬壯舉。隨著成果的推廣應用,帶動了軟磁鐵氧體行業技術和市場的發展,趙光深感意義重大,“這促進了國內電源應用的發展。”
03
從0到主導國際標準制定
如今,國內中高端軟磁鐵氧體材料的生產技術水平已大幅提高,與國外同行的差距越來越小,但站在“金字塔”頂端的仍然是國際品牌。
趙光分析道,國內外軟磁鐵氧體材料的差距主要體現在三個方面:一是材料的關鍵性能,如功率損耗、飽和磁通密度、高頻、寬溫特性等的差距;二是國內在高端元器件的制造技術方面有所不足,如高端一體化成型電感80%仍依賴進口;三是國內產品的質量一致性和穩定性與國外差距還較為明顯。
要縮小差距,軟磁鐵氧體制造業應進行全面提升。
趙光認為,首先必須通過創新形成核心技術,如材料技術、大生產工藝技術、裝備技術和分析測量技術。其次,對于企業而言,扎實打基礎也是關鍵,“企業應該靜下心打基礎,培養工匠型人才,扎實做好應用、市場和顧客研究。”
中國科學院院士都有為曾指出,一個國家現代化的程度、人民生活水平,可以用磁性材料的使用量來衡量。作為都有為院士的學生,趙光對此深表贊同。
眼下,5G通信、光伏新能源、新能源汽車及充電設施等產業發展火熱,為軟磁鐵氧體行業提供了良好的發展機遇。
以新能源汽車為例,需用到軟磁鐵氧體材料的地方就有車載充電機、電驅和輔助系統供電用DC-DC變換器、車燈照明系統、無鑰匙進入系統、EPS、安全氣囊、音響、導航、車聯網、無人駕駛傳感器等,需求十分強勁。
據統計,傳統汽車的軟磁鐵氧體用量為0.3kg左右,新能源車的用量則達到2kg左右。另外,配套一個充電樁的軟磁鐵氧體用量約為2~3kg。按照新能源車每年生產150萬輛,以及充電樁100萬個計算,國內新能源車產業對于軟磁鐵氧體年需求量達5、6千噸。
有了需求,企業還得有能力抓住機會。“企業應該洞悉不同的應用端對于磁性材料的特定要求。”早在2000年,TDK公司就針對汽車應用推出著名的寬溫低功耗錳鋅鐵氧體材料PC95,成為國內外軟磁鐵氧體廠商爭相模仿的產品。
由于汽車的駕駛環境復雜多變,某些部位的電子元器件可能經歷從零下數十攝氏度到100多攝氏度的寬泛溫區,這對材料的溫度特性提出了嚴格考驗,而既往的軟磁鐵氧體材料的局限在于只能在狹窄的溫區保持低功耗的特性。TDK洞悉這一痛點,適時推出了PC95,可在很寬的溫區下始終保持低功耗性能。
趙光如今所在的新康達公司,也在緊緊抓住新能源車發展的機遇,在PC95的基礎上推出了新一代寬溫低功耗材料,在改善寬溫下可靠性的同時,還能提高能量轉換效率。
距離爬上金字塔頂端,國內軟磁鐵氧體企業任重道遠,但步子卻愈發穩健。
眼下,趙光還擔任了全國磁性元件與鐵氧體材料標準化技術委員會(SAC/TC 89)副主任委員,也是國際電工委員會第51技術委員會(IEC/TC 51)的注冊專家,正忙著制修訂有關軟磁材料的國際、國內標準。
“早前國內的軟磁材料標準化工作,都是關起門自己做,國際上幾乎沒有中國的聲音。”2015年,隨著我國主導的有關兩項鐵氧體磁心IEC國際標準正式發布,實現了零的突破,中國的話語權開始飛速提升。2020年,由趙光牽頭制定的關于鐵氧體磁心和金屬磁粉心的兩項國際標準,又被IEC正式發布。
“三流企業做產品、二流企業做品牌、一流企業做標準。”從一無所有到主導國際標準的制定,這是個了不起的變化,趙光如是感慨道。
【個人簡介】
趙光,畢業于南京大學物理系磁學專業,研究員級高級工程師,曾任國營第八九八廠總工程師,現任南京新康達磁業股份有限公司總經理。長期從事軟磁材料研究開發、制造工程、企業管理和標準化工作,曾獲部級科技進步二等獎一項、三等獎二項、國家級新產品認定一項、省、市級科技成果獎七項、IEC 1906大獎,享受國務院頒發的政府特殊津貼;現任IEC注冊專家、全國磁性元件及鐵氧體材料標準化技術委員會副主任、電源學會磁技術專業委員會副主任委員、中國電子學會高級會員及應用磁學分會委員、《磁性材料及器件》及《磁性元件與電源》雜志編委;曾主持制定三項IEC國際標準及五項國家及行業標準;多項專利發明人;在國內外各種期刊、會議發表論文四十余篇。
【企業簡介】
南京新康達磁業股份有限公司成立于1999年,是一家高性能軟磁材料制造企業,在江蘇省南京市江寧區麒麟工業集中區和安徽省馬鞍山市雨山經濟開發區建有生產基地。公司被認定為國家級高新技術企業和江蘇省民營科技企業,設有江蘇省企業院士工作站和南京市企業技術中心,是軟磁材料領域IEC國際標準和我國國家和行業標準的起草單位,“新康達”牌商標被南京市認定為著名商標,先后通過了ISO 9001、ISO 14001、ISO 45001、IATF 16949和GJB 9001C等質量、環境、職業健康和安全管理體系認證。
新康達主要產品為軟磁鐵氧體粉料及磁心、軟磁合金粉料及金屬磁粉心。產品用于制造各種變壓器、電感器、電抗器、扼流圈和濾波器等,主要應用于光伏、5G通訊、汽車、云計算、電磁兼容、節能照明、工業和醫療設備、軍工等領域。公司產品側重于工業應用領域,擁有以華為為代表的國內外高端客戶群。
公司秉承“不求最大,但求最好”的發展理念,把握戰略性新興產業發展給軟磁行業帶來的機遇,加強技術創新,推進精益生產和智能制造,努力向客戶提供最好的產品和服務,以實現互利雙贏、共同發展。
責任編輯:lq
-
新能源汽車
+關注
關注
141文章
10617瀏覽量
99936 -
電感器
+關注
關注
20文章
2335瀏覽量
70698 -
電子設備
+關注
關注
2文章
2809瀏覽量
53907
原文標題:電子設備小型化與節能的關鍵是它 中國完成了從零到領先的轉變
文章出處:【微信號:xincailiaozaixian,微信公眾號:新材料在線】歡迎添加關注!文章轉載請注明出處。
發布評論請先 登錄
相關推薦
全國產化NTP時鐘服務器、全國產化授時服務器、全國產化校時服務器
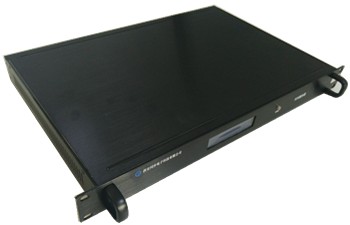
國產替代新材料 | 先進陶瓷材料
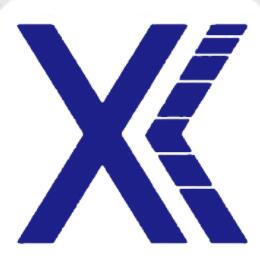
國產化,更可控 智微工業JVC國產化系列嵌入式工控機
半導體材料市場規模不斷增長 國產化持續推進
三星OLED核心材料供應鏈實現國產化
中國電信人工智能研究院完成首個全國產化萬卡萬參大模型訓練
最高扶持500萬元!廣州關于推動智能傳感器產業加快發展措施
今日看點丨聯發科宣布加入 Arm 全面設計;廣汽豐田凱美瑞宣布降價 3~3.2 萬元:現價 13.98 萬元起
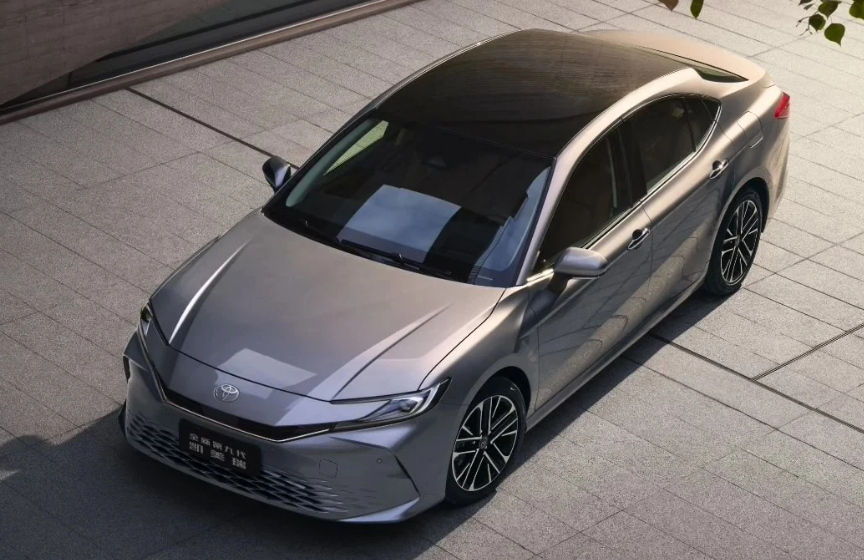
100%全國產化車載ACDC與DCDC電源
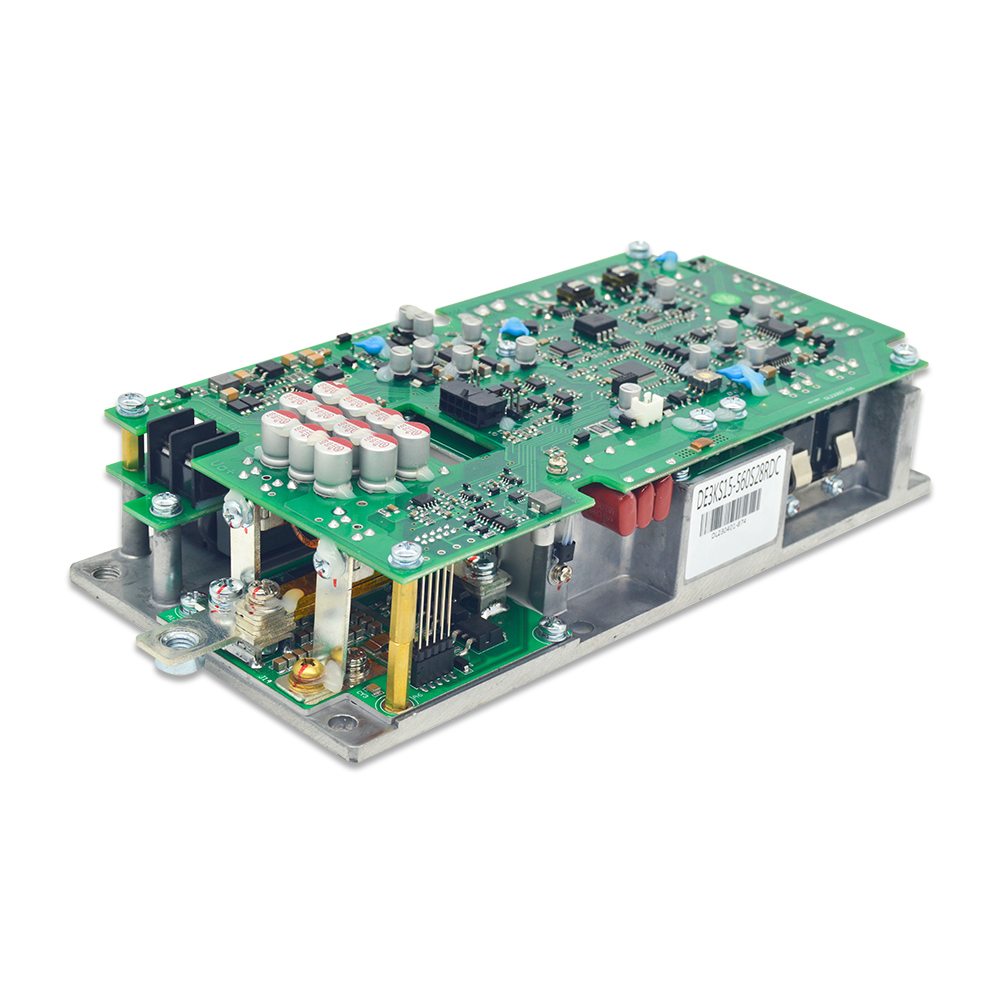
評論