每年在SPIE高級(jí)光刻會(huì)議召開(kāi)之前的星期日,尼康都會(huì)舉行其Litho Vision研討會(huì)。我有幸連續(xù)第三年受邀發(fā)言,不幸的是,由于新冠肺炎的影響,該活動(dòng)不得不取消。但是到活動(dòng)宣布取消時(shí),我已經(jīng)完成了演講文稿,所以在此分享。
概述
我演講的題目是“ Economics in the 3D Era”。在演講中,我將討論三個(gè)主要的行業(yè)領(lǐng)域,即3D NAND,邏輯和DRAM。對(duì)于每個(gè)部分,我都會(huì)討論當(dāng)前的狀態(tài),然后進(jìn)入技術(shù),掩模數(shù)量,密度和成本預(yù)測(cè)的各自路線(xiàn)圖。所有狀態(tài)和預(yù)測(cè)都將針對(duì)公司,并涵蓋每個(gè)細(xì)分市場(chǎng)的領(lǐng)導(dǎo)者。此演示文稿的所有數(shù)據(jù),技術(shù),密度,掩模數(shù)量和成本預(yù)測(cè)均來(lái)自我們的 IC Knowledge–戰(zhàn)略成本和價(jià)格模型– 2020 –修訂版00模型。該模型基本上是一份詳細(xì)的行業(yè)路線(xiàn)圖,可以模擬成本,設(shè)備和材料要求。
3D NAND
3D NAND是業(yè)界最“ 3D”的細(xì)分市場(chǎng),其層堆疊技術(shù)可通過(guò)在豎直方向上添加層來(lái)提高密度。
圖1展示了3D NAND TCAT制程。
圖1. 3D NAND TCAT制程。
在3D NAND領(lǐng)域,市場(chǎng)領(lǐng)導(dǎo)者是三星,他們使用的是TCAT制程。市場(chǎng)上排名第二的是Kioxia(前身為T(mén)oshiba Memory),他們使用的工藝與三星基本相同。美光也正在采用電荷陷阱技術(shù),我們希望其工藝類(lèi)似于TCAT制程,從而使TCAT制程能夠代表行業(yè)大多數(shù)。SK海力士使用不同的制程,但在許多關(guān)鍵要素上與TCAT制程相同。唯一不使用電荷陷阱技術(shù)的公司是英特爾美光公司,但由于英特爾和美光已經(jīng)在3D NAND領(lǐng)域分道揚(yáng),,英特爾將是唯一一家仍然采用浮柵技術(shù)的公司。
TCAT制程包括三個(gè)主要部分:
制作CMOS – 這些CMOS用于寫(xiě)入,讀取和擦除比特信息。最初,除英特爾-美光公司外,每家公司都在存儲(chǔ)器陣列外圍制造CMOS,而英特爾-美光公司在存儲(chǔ)器陣列下方制造一些CMOS。隨著時(shí)間的流逝,其他公司已經(jīng)遷移到陣列下的CMOS,我們希望在幾代之內(nèi),所有公司都將遷移到陣列下的CMOS,因?yàn)樗峁┝烁玫穆闫娣e利用率。
制作存儲(chǔ)陣列–對(duì)于電荷陷阱技術(shù),可通過(guò)沉積氧化物和氮化物的交替層來(lái)進(jìn)行陣列制造。然后向下蝕刻穿過(guò)各層的溝道孔,并重新填充氧化硅/氮化硅/氧化硅(ONO)層,多晶硅管(溝道)并填充氧化物。然后使用光刻-蝕刻-收縮-蝕刻方法制造階梯。然后穿過(guò)陣列向下蝕刻狹隙,并蝕刻掉氮化物膜。然后沉積阻擋層和鎢以填充蝕刻氮化物的水平開(kāi)口。最后,將通孔蝕刻停止到到鎢的水平片上。
互連– CMOS和存儲(chǔ)器陣列然后互連。對(duì)于陣列下的CMOS,一些互連發(fā)生在存儲(chǔ)器陣列制造之前。
這種技術(shù)掩模使用效率非常高,因?yàn)榭梢杂萌舾蓮堁谀?duì)很多層進(jìn)行構(gòu)圖。整個(gè)制程只需要一張溝道孔掩模,若干張階梯掩模(取決于層數(shù)和制程需求)。在早期的工藝中,單張掩模可以制作大約8層,但是如今某些工藝可以通過(guò)單張掩模做到32層。狹縫(slot)蝕刻需要一張掩模,有時(shí)還有另一個(gè)淺狹縫需要一張掩模,最后接觸通孔也需要一張掩模。
溝道孔蝕刻是非常難的高深寬比(HAR)蝕刻,一旦達(dá)到一定的最大層數(shù),該制程就必須以所謂的“串堆疊”(string stacking)方式分成多個(gè)“串”(存儲(chǔ)單元串)。基本上,在串堆疊中,沉積一組層,應(yīng)用掩模,蝕刻,填充溝道。然后沉積另一組層,光刻,蝕刻和填充。理論上,這可以循環(huán)很多次。英特爾-美光科技公司使用浮柵工藝,該工藝使用的氧化硅/多晶硅層比氧化硅/氮化硅層更難蝕刻,所以他們是最早使用串堆疊技術(shù)的。
圖2展示了Intel-Micron串堆疊技術(shù)。
圖2. Intel-Micron串堆疊制程。
每家公司都有自己的溝道孔蝕刻方法,并且在串堆疊方面有自己的限制。因?yàn)槭褂醚趸嗑Ч鑼樱訧ntel-Micron通過(guò)堆疊2次32層的串制作了64層芯片,然后通過(guò)堆疊2次48層的串量產(chǎn)了96層芯片。英特爾已經(jīng)發(fā)布了144層存儲(chǔ)芯片,預(yù)計(jì)將是3次堆疊48層。SK Hynix到72層時(shí)開(kāi)始串堆疊,Kioxia是96層開(kāi)始堆疊(都是電荷陷阱技術(shù),都是氧化硅/氮化硅層)。三星是最后一個(gè)串堆疊技術(shù)的支持者,他們量產(chǎn)了一款92層的單串芯片,并發(fā)布了一款128層的單串器件。
通過(guò)在一個(gè)單元中存儲(chǔ)多個(gè)比特,也可以提高存儲(chǔ)密度。NAND閃存已從單層單元(SLC)到2個(gè)比特的多層單元(MLC),再到3比特的三層單元(TLC),再到4比特的四層單元(QLC)。業(yè)界現(xiàn)在正準(zhǔn)備推出5個(gè)比特的五層單元(PLC),甚至還有關(guān)于6比特的6層單元(HLC)的討論。增加每個(gè)單元的比特?cái)?shù)有助于提高密度,但收益卻在降低,從SLC到MLC的比特?cái)?shù)是2倍,從MLC到TLC的比特?cái)?shù)是1.5x,TLC到QLC的比特?cái)?shù)是1.33x,從QLC到PLC的比特?cái)?shù)是1.25倍。如果業(yè)界達(dá)到了PLC,則接下來(lái)到HLC的比特?cái)?shù)將只是1.20倍。
圖3在左軸上顯示了按年份和公司分類(lèi)的串堆疊,在右軸上顯示了每個(gè)單元的最大比特?cái)?shù)。
圖3.堆疊層數(shù),每單元比特?cái)?shù)。
圖4展示了我們對(duì)按曝光類(lèi)型,公司和年份劃分的掩模數(shù)量的分析。虛線(xiàn)是每年的平均掩模數(shù),從2017年的42張?jiān)黾拥?025年的73張,這與層數(shù)從2017年的平均60個(gè)增加到2025年的512個(gè)相對(duì)應(yīng)。換句話(huà)說(shuō),掩模數(shù)量?jī)H增加1.7倍就增加了8.5倍的層數(shù)以突出3D NAND工藝的掩模使用效率。
圖4.掩模數(shù)量趨勢(shì)。
圖5展示了各家公司2D NAND和3D NAND的實(shí)際和預(yù)測(cè)比特密度隨年份變化的趨勢(shì)。這里是整個(gè)芯片的比特密度,即芯片的容量除以芯片的尺寸。
圖5. NAND比特密度。
從2000年到2010年,在光刻微縮的推動(dòng)下,2D NAND比特密度每年增長(zhǎng)1.78倍。大約在2010年左右,繼續(xù)縮小2D NAND的難度導(dǎo)致增長(zhǎng)減慢至1.43倍,直到2015年左右3D NAND成為驅(qū)動(dòng)力并繼續(xù)以每年1.43倍的速度增長(zhǎng)。我們預(yù)計(jì)從2020年到2025年的年增長(zhǎng)率將略有下降,為1.38倍。與去年相比,這是我們的預(yù)測(cè)的一項(xiàng)改進(jìn),因?yàn)槲覀兛吹竭@些公司推動(dòng)該技術(shù)的速度超出了我們最初的預(yù)期。最后,SK海力士談到了2025年的500層和2030年的800層,導(dǎo)致2025年之后的速度進(jìn)一步放緩。
圖6給出了NAND單位比特成本趨勢(shì)。
圖6. NAND單位比特成本。
在該圖中,我們采用了使用戰(zhàn)略成本和價(jià)格模型計(jì)算出的晶圓成本,并將其與圖5中的位密度相結(jié)合以產(chǎn)生單位比特成本趨勢(shì)。在所有情況下,這些晶圓廠(chǎng)都是新建的月產(chǎn)能75,000片晶圓的工廠(chǎng),因?yàn)檫@是NAND晶圓廠(chǎng)在2020年的平均產(chǎn)能。這些晶圓廠(chǎng)對(duì)應(yīng)所在的國(guó)家分別是新加坡-英特爾美光,英特爾-中國(guó),Kioxia-日本,三星和SK海力士-韓國(guó)。這些計(jì)算不包括封裝和測(cè)試成本,不考慮劃片槽寬度,并且僅包含粗略的芯片良率假設(shè)。
圖表中的前三個(gè)節(jié)點(diǎn)是2D NAND,每個(gè)節(jié)點(diǎn)的成本趨勢(shì)為0.7倍。隨著向3D NAND的過(guò)渡,大多數(shù)公司的比特成本最初都增加了,但現(xiàn)在已降至2D NAND比特成本以下,并且每個(gè)節(jié)點(diǎn)的趨勢(shì)為0.7倍,直到大約300到400層。我們預(yù)計(jì)單位比特成本會(huì)趨于平緩,除非在工藝或設(shè)備效率方面取得一些突破,否則該技術(shù)將面臨成本極限。
-
半導(dǎo)體
+關(guān)注
關(guān)注
335文章
28178瀏覽量
227806 -
3D
+關(guān)注
關(guān)注
9文章
2934瀏覽量
108872 -
IC設(shè)計(jì)
+關(guān)注
關(guān)注
38文章
1338瀏覽量
104838
發(fā)布評(píng)論請(qǐng)先 登錄
相關(guān)推薦
下一代3D晶體管技術(shù)突破,半導(dǎo)體行業(yè)迎新曙光!
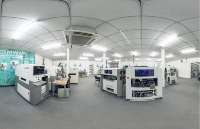
?超景深3D檢測(cè)顯微鏡技術(shù)解析
芯片3D堆疊封裝:開(kāi)啟高性能封裝新時(shí)代!
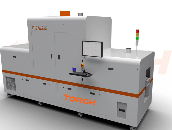
英倫科技裸眼3D便攜屏有哪些特點(diǎn)?
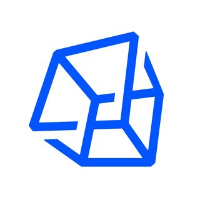
3D打印技術(shù)在材料、工藝方面的突破
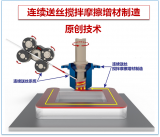
多維精密測(cè)量:半導(dǎo)體微型器件的2D&3D視覺(jué)方案
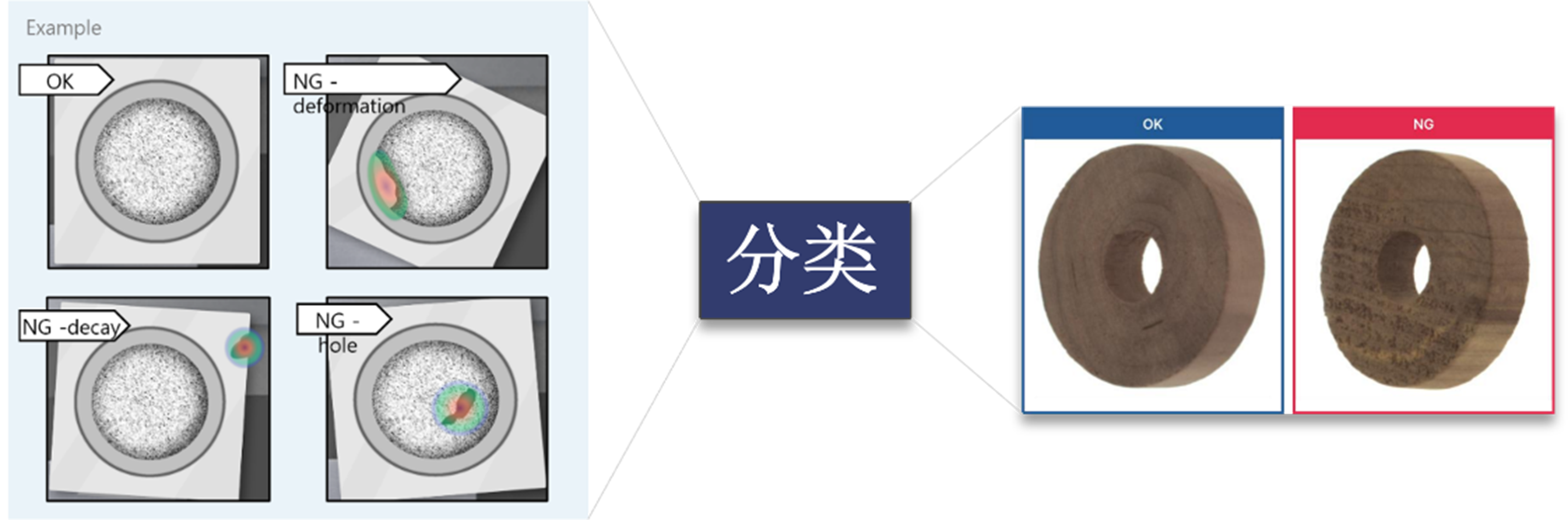
技術(shù)前沿:半導(dǎo)體先進(jìn)封裝從2D到3D的關(guān)鍵
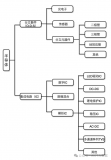
3D打印技術(shù),推動(dòng)手板打樣從概念到成品的高效轉(zhuǎn)化
技術(shù)資訊 | 2.5D 與 3D 封裝
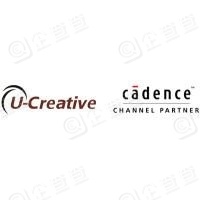
揭秘3D集成晶圓鍵合:半導(dǎo)體行業(yè)的未來(lái)之鑰
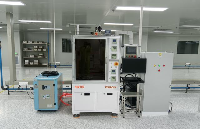
一文理解2.5D和3D封裝技術(shù)
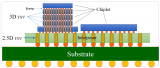
3D封裝熱設(shè)計(jì):挑戰(zhàn)與機(jī)遇并存
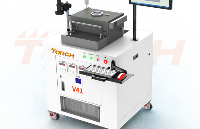
評(píng)論