隨著全球電子產品市場的需求升級和快速擴張,電子產品的小型化、高精密、超細線路印制電路板技術正進入一個突飛猛進的發展時期。為了能滿足市場不斷提升的需求,特別是在超細線路技術領域,傳統落后的蝕刻技術正被先進的真空蝕刻技術所代替。
一、PCB 蝕刻定義
蝕刻:將覆銅箔板表面由化學藥水蝕刻去除不需要的銅導體,留下銅導體形成線路圖形,這種減去法工藝是當前印制電路板加工的主流。
二、 蝕刻的關鍵是蝕刻溶液、蝕刻操作條件和蝕刻設備
1. 蝕刻溶液
目前是以氯化銅與鹽酸的酸性氯化銅蝕刻液,及以氯化銅與氨水的堿性氯化銅蝕刻液為主流。
2. 蝕刻操作條件
蝕刻操作條件是對溫度、壓力、時間以及溶液濃度等工藝參數的控制,使蝕刻過程處于最佳狀態。
3. 蝕刻設備是圍繞著生產效率、蝕刻速度和蝕刻均勻性而不斷改進。目前主流是水平傳送噴淋式。
蝕刻線
三、 蝕刻設備
主要體現在傳送方式和噴淋方式。
1. 傳送方式分為:固定式、垂直式、水平式
固定式:早期的設備是一個槽缸,存放蝕刻液后,將 PCB 板浸泡在里面。缺點:放板取板效率低;蝕刻效率低;無法做細線路,線條寬度 / 間距在 0.5mm 以上。
垂直式:PCB 板子垂直掛吊于夾具上進入蝕刻機內, 在蝕刻室兩側溶液噴淋板面。由于蝕刻設備復雜和沒有體現優良的蝕刻效果, 因此此技術沒發展起來。
水平式:使用滾輪傳送 PCB,滾輪之間有間距,上下安裝噴嘴,用噴淋方式進行蝕刻。優點:傳送速率一致,蝕刻相對均勻;效率高,兩面可同時蝕刻。目前主流是水平傳送方式。
2. 噴淋方式
為了使溶液能全面地噴淋到 PCB 板子表面每個部位, 并促使板面溶液加快流動, 需移動噴淋桿 / 噴嘴來實現這個效果;
噴嘴的結構也有多種式樣, 按照噴出液體形狀不同有 a. 實心線束型、b. 空心圓錐形、c. 實心圓錐形、d. 扁平扇形等。從噴射液體不同形狀的效果來看, 實心線束型面積太小, 圓錐形面積過大, 在較密滾輪情況下都被遮擋掉了。因此較多蝕刻機中選擇扁平扇形噴嘴, 溶液呈扇面與 PCB 板子表面垂直沖擊銅箔, 效果較好。
四、“水池效應”
目前主流的水平傳送噴淋式,能實現最大程度上的生產自動化,成本降低,但是這種方式也不是完美的,會導致“水池效應”,使蝕刻結果產生差異。普通板子影響不大,但是對于超細線路,無法達到蝕刻的公差要求。“水池效應”發生的情況:PCB 水平傳送時,位于板子下面和板子上面靠近邊緣部分,蝕刻液容易流走,新舊蝕刻液更容易進行交換;而板中心的位置,容易形成“水池”,蝕刻液流動受到限制;因此 PCB 板上面中間的線路會比其他位置的蝕刻效果差一些。
德國 PILL e.K. 公司發布了一項新的工藝技術,通過吸取使用過的蝕刻液來可改善板面上部分的蝕刻液的流動性,從而阻止“水池效應”的產生。這種方法被稱為真空蝕刻。
五、真空蝕刻
原理:在蝕刻段中安裝了噴嘴,也在噴管之間離線路板表面相對距離較近的位置安裝了抽氣單元。抽氣單元使操作區域形成負壓,剛好夠防止蝕刻液產生“水池效應”的較低的吸力。經比較,板朝上部分與朝下部分的蝕刻效果基本一致。
效果:通過蝕刻的均勻性試驗來確認, 采用 35μm 銅箔的覆箔層壓板分別在常規與真空這兩種蝕刻機上進行全板面蝕刻, 約板中間銅箔蝕刻到 18μm 厚度時停止, 檢測全板面銅厚度分布。常規蝕刻得到的銅厚度分布通常是中央呈高山狀, 而真空蝕刻得到的銅厚度分布均勻。在 600mm 長度內, 常規蝕刻的中央與邊緣銅厚度差約有±4μm (18~10μm), 而真空蝕刻的中央與邊緣銅厚度差僅約±1μm (19~17μm), 后者只是前者的四分之一。
采用真空蝕刻機使得線寬 / 線距≤30/30μm 的線路圖形容易實現。而要得到理想的效果其中還需把握的是真空力度、噴淋壓力和銅箔厚度等因素。蝕刻機中真空吸嘴對板面溶液的吸引量應是等于或稍大于噴淋量, 若吸引量小又會造成老溶液滯留。噴淋壓力會影響到蝕刻速度與側腐蝕程度, 但壓力大會破壞抗蝕刻膜, 尤其是細節距線路圖形上。對于線寬 / 線距=30/30μm 線路, 常規設備下被蝕刻銅箔厚度小于 12μm, 真空蝕刻時銅箔厚度 18μm 也可加工。可參考的數據, 線寬 / 線距=30/30μm, 采用 18μm 銅箔, 噴淋壓力 0.1Mpa (1.02kgf/cm2)時吸引量 40Hz (約 120L/min), 得到均勻的線路圖形。
審核編輯黃昊宇
-
pcb
+關注
關注
4322文章
23124瀏覽量
398509 -
真空蝕刻
+關注
關注
0文章
4瀏覽量
6307
發布評論請先 登錄
相關推薦
真空及真空泵有什么作用
芯片濕法蝕刻工藝
探索無損密封檢測技術:真空衰減法測試的原理及實踐
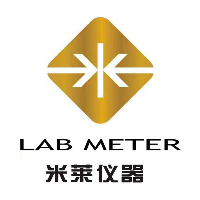
DL-T846.9-2004高電壓測試設備通用技術條件第9部分:真空開關真空度測試儀
打破常規,開創未來:PCB板真空樹脂塞孔
玻璃基電路板的蝕刻和側蝕技術
玻璃電路板表面微蝕刻工藝
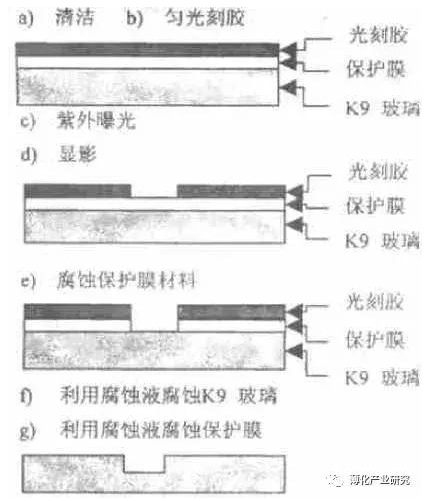
基于光譜共焦技術的PCB蝕刻檢測
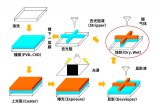
真空的秘密:正壓、負壓與真空度的神秘關系
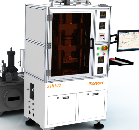
評論