工業物聯網 (IIoT) 應用有望提高復雜工業系統的效率。由于能夠實現這些 IIoT 應用的是下一代基于微控制器的可編程邏輯控制器 (PLC),因此對開發人員提出了挑戰,既要支持這些系統中所需的各種工業接口,還要使器件足夠緊湊以便能適合工廠設備。
這些挑戰已經成為創建更高級 IIoT 應用這一終極目標的重大障礙。不過,采用模塊化方法來定制 PLC IO 可能是開發人員需要的解決方案。
本文首先會討論 IIoT 高級 IO 設計所面臨的挑戰,然后介紹 Maxim Integrated 的模塊化系統解決方案,最后說明該解決方案作為現成方案或作為現代定制 IIoT 應用的參考設計時如何使用。
PLC 在 IIoT 中的角色演變
作為工廠自動化系統中的中間設備,PLC 多年來一直提供將傳感器、致動器和其他設備連至主機系統所需的多個接口。在服務于 IIoT 應用時,PLC 系統不但需要支持更多數量的終端器件和本地處理能力,同時還要足夠小巧,以便可以安裝在單個機件上,或者位于工作單元或子裝配線中不顯眼的位置。這樣會造成開發人員深陷于設計細節的泥沼中,為工業環境中所需的許多接口考慮解決方案。
在許多情況下,這不能有效利用開發人員的時間,如果將這些時間用在為智能工廠、自適應制造、預測性維護以及其他基于人工智能方法的新興功能方面提供高水平解決方案的話,則會取得更佳效果。對傳感器和致動器采用靈活的模塊化接口方法,可以縮短開發時間,不過,這種接口解決方案必須足夠堅固耐用,以便可以承受惡劣的工業環境。
工業接口
典型的工業環境需要各種接口,以滿足外設和主機系統之間數字及模擬信號的通訊需求,其中,IO-Link 行業標準已經成為連接兼容的終端器件,以及傳統傳感器和致動器的有效方法。
在標準點對點 IO-Link 連接中,開發人員可以使用 PLC 中的 IO-Link 主站,通過端接有標準 M12 連接器的低成本 3 線或 4 線非屏蔽式電纜連接到 IO-Link 收發器。憑借其電氣接口和功能協議,IO-Link 即使在惡劣的存在電噪的工業環境中也能確保可靠通信。IO-Link 主器件(如 Maxim Integrated MAX14819)解決了 IO-Link 電氣接口及協議的實施復雜性。對于電氣接口,MAX14819 集成了生成 L+ 和 L- 穩壓電源,以及 IO-Link 標準要求的 C/Q 數據信號所需的電路。對于通信協議,該器件集成了 IO-Link 通信方法的基礎構件,如 IO-Link 成幀器、UART 和 FIFO(請參閱“使用 IO-Link 收發器來降低功耗、提升性能和簡化開發”)。
要將傳感器或致動器連至 PLC 中的 IO-Link 主站,開發人員可以輕而易舉地找到兼容的 IO-Link 器件,也可以使用 Maxim MAX14827A 收發器輕松構建自己的器件(圖 1)。
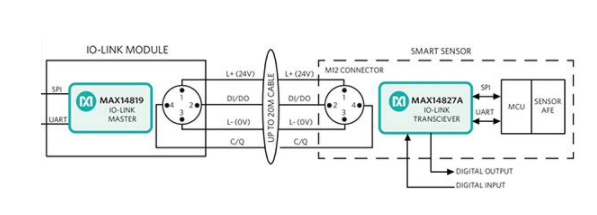
圖 1:通過將外圍傳感器中的 Maxim Integrated MAX14827A IO-Link 收發器與 PLC 或其他主機系統中的 Maxim MAX14819 IO-Link 主站配對,開發人員可以快速實現 IO-Link 點對點通信鏈接。(圖片來源:Maxim Integrated)
盡管 IO-Link 已在較新的工業環境中得到廣泛采用,但傳統及較新環境中的應用仍然可以發現其他標準接口的身影。其中,RS-485 仍然是最廣泛使用的串行接口標準之一,該接口是一種標準電氣接口,是 RS-232 或 RS-422 等早期串行接口的替代品,具有更加堅固耐用的特點,設計用于通過一根 24 AWG 雙絞線進行雙向通信,RS-485 具有共模性能特點,這使其在滿足延長電纜仍能可靠運行要求方面發揮了核心作用,即使在嘈雜的環境中也是如此。因此,這種接口為許多工廠網絡奠定了基礎,例如在 Profibus 和現場總線中充當物理層 (PHY)。
與 IO-Link 一樣,工程師可以輕松找到旨在簡化實現 RS-485 通信的集成器件。Maxim Integrated MAXM22511 RS-485 收發器專為工業應用而打造,不僅簡化了該接口的實現,而且能在惡劣環境中保護其完整性。使用該器件,開發人員只需將 MAXM22511 的電纜側連至雙絞線,將 UART 側連至微控制器或其他數字設備,即可實現電位隔離的 RS-485 接口,且無需額外元件(圖 2)。集成在該器件內的高壓電容器可以隔離數據通道,內置在器件 DC-DC 穩壓器中的變壓器可通過片上低壓差 (LDO) 穩壓器為電纜側提供隔離電源
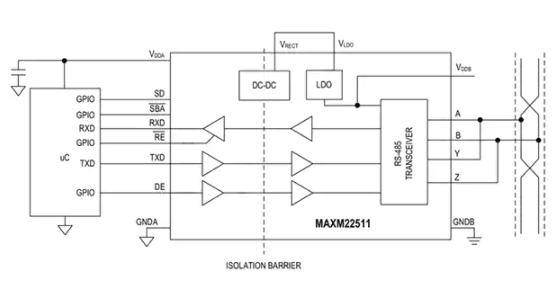
圖 2:Maxim Integrated MAXM22511 收發器簡化了工業 RS-485 接口的實現,同時配備內置隔離保護,可防止電纜側發生電氣事件。(圖片來源:Maxim Integrated)
實際上,典型的工業自動化系統可能需要支持 IO-Link 和 RS-485 接口以外的接口。在輸入側,這些系統通常需要支持符合 IEC 61131-2 標準及其所有三種輸入類型的數字輸入設備:第一類是較早的帶機械開關觸頭的 3 線式傳感器,第二類是更早的帶半導體接口的 2 線式傳感器,第三類是最近的 2 線或 3 線式低功耗傳感器。
對于本電路而言,開發人員可以使用 Maxim MAX22192,該器件配有 8 個符合 IEC 61131-2 標準的輸入通道,只需添加電流設定電阻器即可將各通道配置為 1 類、2 類或 3 類輸入。
在輸出側,許多此類系統都依賴于數控驅動器,這些驅動器能夠支持精確控制致動器或其他設備所需的高速切換。本圖中,工程師可以使用諸如 Maxim Integrated MAX14912 等器件,此器件具有 8 個通道,可將這些通道配置為高壓側開關或驅動器。
對于直接控制直流電機等更專業的輸出要求,開發人員可以選擇 Maxim MAX14870,這款器件可提供完全集成的電機控制解決方案,旨在減少零件數量,降低設計復雜性。為響應脈沖寬度調制 (PWM) 信號和方向 (DIR) 控制信號,該器件的集成驅動器可在最高 36 伏電壓條件下,直接驅動有刷直流電機和繼電器,并且添加的元件最少(圖 3)。設計人員可將 MAX14870 的輸出功能與 Maxim MAX14890E 編碼器接收器相結合,以實現精密運動控制子系統。
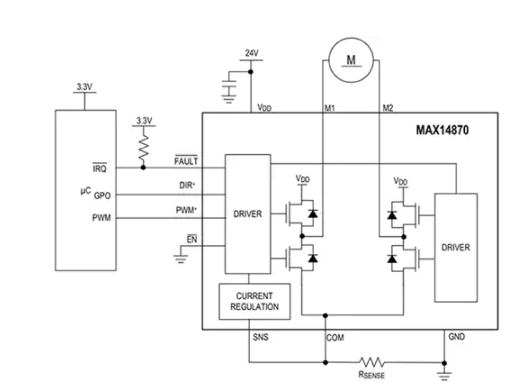
圖 3:Maxim Integrated MAX14870 集成了驅動器和開關,可使開發人員能夠在幾乎不添加元件的情況下,即可實現 PWM 控制的電機子系統。(圖片來源:Maxim Integrated)
下一代 PLC 設計
由于市場上擁有種類繁多的專用 IC,因此許多與實現工業系統所需的各種接口相關的低級設計挑戰得到了緩解。即便如此,因需要接口的設備數量眾多,并且每一種設備的設計要求各不相同,因此仍然需要工程師來應對挑戰,即:在盡可能最小的設計空間內將多個接口設備與一個微控制器相結合。對于希望為高級 IIoT 應用奠定基礎的開發人員,Maxim Integrated MAXREFDES212 Go-IO PLC 系統可以幫助他們消除這一障礙。
Maxim Integrated MAXREFDES212 Go-IO PLC 系統是一個模塊化系統,由多塊小電路板組成,每塊電路板的設計均可滿足下一代 PLC 的一系列要求。設計人員可將應用處理器板 (MAXREFDES211)、IO-Link 工廠自動化板 (MAXREFDES200) 和運動控制板 (MAXREFDES201) 插入基板 (MAXREFDES215),該基板配有 IO 端子塊以及與 IO-Link 相兼容的獨立 M12 連接器(圖 4)。(請注意,Maxim 為四種板提供了指示性 MAXREFDESxxx 名稱,不過,這些板僅作為 MAXREFDES212 Go-IO PLC 系統的部件提供。)插到一起后,Go-IO 系統內所含的這些板即可形成一個尺寸小于 3 平方英寸的基于微控制器的緊湊型 PLC,同時提供 20 多個 IO,可支持各種接口,其中包括 IO-Link、RS-485、符合 IEC 61131-2 標準的數字輸入、數字輸出和電機控制。開發人員隨即可使用 Go-IO PLC 來補充現有工業系統,或將其用作自定義 PLC 的參考設計。
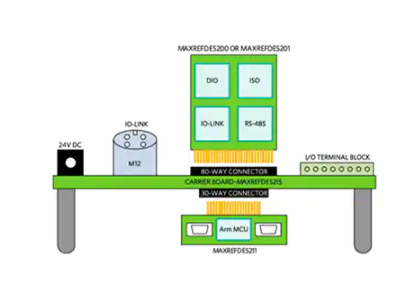
圖 4:借助 Maxim Integrated GO-IO PLC 模塊化設計,開發人員能夠通過將單塊板(包括基于 Arm 微控制器的應用處理器板 MAXREFDES211、工廠自動化板 MAXREFDES200 和運動控制板 MAXREFDES201)插入基板 MAXREFDES215 來配置 PLC。(圖片來源:Maxim Integrated)
除了充當 PLC 的物理框架外,載板還可為擴展板提供穩定電壓,該電壓可源自標準 24 伏壁式適配器,也可來自與載板上螺紋端子相連的獨立高電流電源。此電路板設計結合了 Maxim MAX17681 DC-DC 轉換器、電感器以及 MAX17608 電流保護 IC,可為其他電路板提供隔離電源(圖 5)。其他 MAX17608 器件可為各電路板上可用的其他 24 伏電源提供保護。
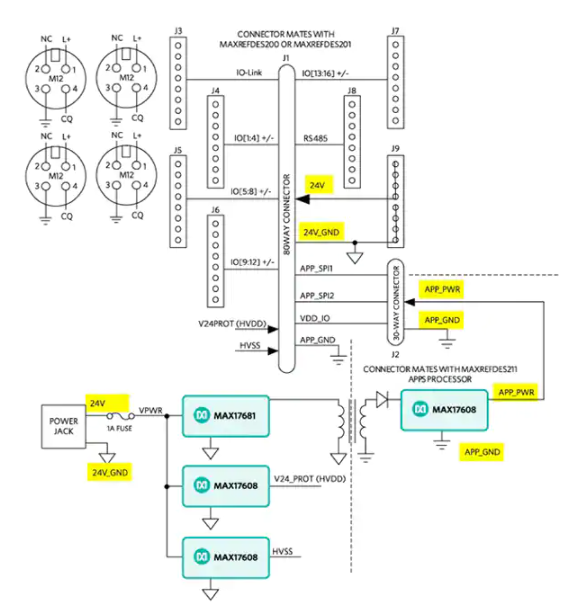
圖 5:Maxim Go-IO 載板可為這種模塊化 PLC 設計方法中的其他電路板提供連接器和電源。(圖片來源:Maxim Integrated)
應用處理器板設計用于插入載板底座,包括一個 Maxim MAX32630 微控制器,并且支持開發和執行組裝 PLC 的代碼(圖 6)。基于帶有 FPU CPU 的 Arm? Cortex?-M4,MAX32630 微控制器具有新興 IIoT PLC 所需的低功耗、安全性以及處理器性能。該應用處理器板從載板取電,并且使用 MAX17502 DC-DC 轉換器將 24 伏電源降至 3.3 伏,以便為兩個 MAX1806 線性穩壓器供電,從而為 MAX32630 提供所需的 1.8 伏和 1.2 伏電源。
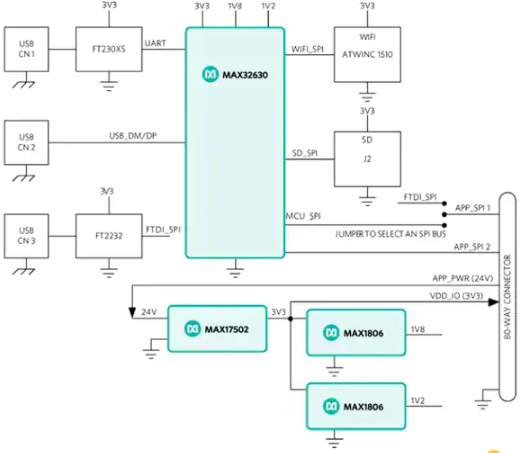
圖 6:Maxim Go-IO 應用處理器板可承載能夠協調擴展板功能的 Maxim MAX32630 微控制器,并且通過共享的 SPI 總線和 80 路連接器進行通信,這種連接器用于連接此模塊化系統中使用的各種電路板。(圖片來源:Maxim Integrated)
除了用于連接開發系統的 USB 連接器外,該板還支持單線、I2C、UART 和 SPI 連接。實際上,這款應用處理器板配有多條 SPI 總線,可用于整個模塊化 Go-IO 系統。其中兩條 SPI 總線(APP_SP1 和 APP_SP2)與 80 路連接器相連,供其他插件板使用。如下所述,APP_SP2 在系統保護方面起著至關重要的作用。
截至撰寫本文時,還有兩條 SPI 總線尚未使用:SD_SPI 總線保留用于連接 SD 卡,WIFI_SPI 總線保留用于 Wi-Fi 模塊。盡管目前尚不支持,但設計硬件規范仍包括一個 Microchip Technology ATWINC1510-MR210PB1952 Wi-Fi 模塊,此模塊配有完整的 Wi-Fi 子系統,包括功率放大器 (PA)、低噪聲放大器 (LNA)、開關和印制線天線。
雖然該應用處理器板僅在受控的數字域內工作,但工業接口始終容易受到電纜短路或靜電放電帶來的突然高壓的影響。無論哪種原因引起的高壓,都會降低或破壞設計用于在窄電壓軌內運行的數字電子器件。如前所述,諸如 Maxim Integrated MAXM22511 RS-485 收發器 IC 等接口器件內置隔離功能,可以保護其數字電路免受電纜副作用的影響。然而在電路板級別,工程師需要在總體設計中構建隔離功能。Go-IO PLC 系統參考設計展示了一種系統級隔離方法。
MAXREFDES212 套件和參考設計旨在保護與 APP_SPI2 總線的連接,對剩余的兩塊擴展板(工廠自動化板和運動控制板)采用的是常見的隔離方法。在這種方法中,多個數字隔離器件可以保護 APP_SPI2 SPI 總線,以及 80 路連接器承載的其他信號線。此連接器用于將擴展板上的器件連接到應用處理器板上的 MAX32630 微控制器。
本電路的 Go-IO 設計利用的是 MAX22192 內置的隔離 SPI 接口,可為其他擴展板器件(包括各擴展板中內置的 Maxim MAX3108 UART)提供受保護的板側 SPI 總線。Go-IO 設計還采用了 Maxim MAX14483 IC,可提供 6 個針對 SPI 事務優化的隔離通道。最后,此設計還使用了多個 Maxim MAX14130 四通道數字隔離器,可為其他 SPI 連接和特定信號線提供保護。
盡管兩塊擴展板上的 MAX14483 和 MAX14130 數字隔離器的配置略有不同,但兩塊板共享上述通用架構,這種架構也被工廠自動化板設計所采用(圖 7)。除采用類似隔離方法外,兩塊電路板均可連接 Maxim MAX22192 提供的符合 IEC 61131-2 標準的輸入,以及 MAX3108 和 MAXM22511 提供的受保護 RS-485 接口。
圖 7:Maxim Go-IO 工廠自動化板可在微控制器和專用接口器件之間提供隔離連接,從而為開發人員提供多種工業接口(包括數字輸入、數字輸出、RS-485 和 IO-Link)支持。(圖片來源:Maxim Integrated)
兩塊擴展板的主要區別在于器件的配置,其中一塊擴展板的器件用于支持工廠自動化接口,另一塊的器件則用于支持運動控制功能。在工廠自動化板 (MAXREFDES200) 內,受保護的 SPI 總線和信號線與高速輸出驅動器連接,進而連至 IO-Link 子系統。此電路板設計使用上文提到的 Maxim MAX14912 高速開關/驅動器進行數字輸出控制。對于 IO-Link 子系統,該電路板設計將一對 Maxim MAX14819 IO-Link 主收發器與 STMicroelectronics STM32F412 微控制器結合在一起,可執行其預裝的 IO-Link 協議棧。
對于穩壓電源,每塊電路板都包含一對 Maxim MAXM15462 DC-DC 轉換器,可將來自載板的 24 伏電源降至每塊板所需的供電電平,即 3V3_DIO、3V3_MCU 和 5V0_DIO。此外,MAX22192 集成的 LDO 可將 24 伏電源轉換為 3.3 V VDD_IO 電源,從而使 MAX14130 數字隔離器 IC 可在其受保護域中使用。
對于運動控制板 (MAXREFDES201) 而言,設計可將數字隔離器件與一組 MAX14870 電機驅動器和 MA14890 編碼器結合在一起(圖 8)。如前所述,MAX14870 和 MA14890 的組合使用可為開發人員提供所需關鍵功能,從而實現精密控制系統(由電機、繼電器和其他裝置構成)。
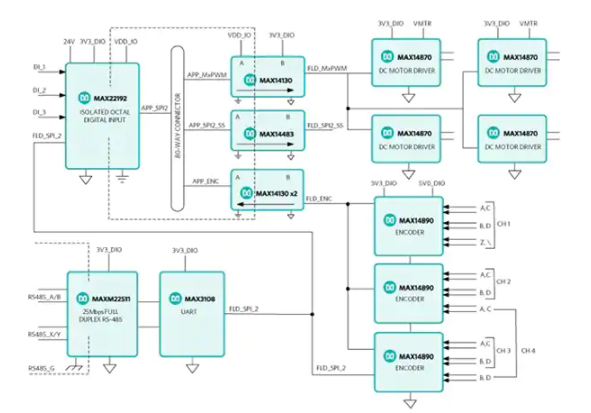
圖 8:Go-IO 運動控制板集成了類似于工廠自動化板所使用的保護方案,可為開發人員提供驅動器輸出和編碼器輸入,以實現電機、繼電器和其他工業子系統的高級控制功能。(圖片來源:Maxim Integrated)
為幫助工程師加快 Go-IO PLC 系統的軟件開發,Maxim 提供了一款基本軟件包,其中包含驅動程序和基本測試程序。雖然基礎框架可作為固件預裝在 Maxim MAX32630 微控制器中,但開發人員仍可以研究示例軟件,該軟件演示了通過系統的應用程序編程接口與單個器件交互的基本設計模式(清單 1)。GO-IO PLC 系統硬件參考設計及配套軟件專注于工業 IO 接口,可為實現先進工業自動化系統提供所需的關鍵基礎。
* ************************************************************************* */
int TEST_MAX22192_run_tests(void){
int error;
di_channel_t di_ch;
TEST_print_line(0, 0, 0);
TEST_print_header(“MAX22192 Tests”, 0);
TEST_print_header(“HW”, 0);
//Read input for channel 1
di_ch = DI1;
error = MAX22192_read_input(di_ch);
printf(“Test- MAX22192_read_input(%d): %d”, di_ch, error);
TEST_print_pass(error == 1, 1);
。 . 。
/* ************************************************************************* */
int TEST_MAX14912_run_tests(void){
int error;
int counter;
do_channel_t do_ch;
do_mode_t do_mode;
uint8_t do_value;
TEST_print_line(0, 0, 0);
TEST_print_header(“MAX14912 Tests”, 0);
TEST_print_header(“HW”, 0);
//Write mode for channel 1
do_ch = DO1;
do_mode = DO_MODE_HS;
error = MAX14912_write_mode(do_ch, do_mode);
printf(“Test- MAX14912_write_mode(%d, %d): %d”, do_ch, do_mode, error);
TEST_print_pass(error == 0, 0);
。 . 。
清單 1:Maxim Integrated 的示例軟件平臺包括測試代碼,可展示外設操作的基本設計模式,包括從 Maxim Integrated MAX22192 數字輸入 IC 中的單個通道讀取 (MAX22192_read_input()),以及將 (MAX14912_write_mode()) 寫入 Maxim Integrated MAX14912 數字輸入 IC 中的單個通道。(代碼來源:Maxim Integrated)
結語
動態制造、預測性維護以及其他先進人工智能方法等高級應用取決于傳感器、致動器及其他工業設備是否可靠連接。Maxim Integrated Go-IO PLC 模塊化系統和參考設計可為現有環境提供現成的平臺,并且可為滿足新興需求提供可擴展的基礎。通過在 Go-IO PLC 平臺上構建,開發人員可以快速部署緊湊型 PLC 解決方案,從而實現先進的制造系統。
評論