摘要
文章詳細的研究了導電膏塞孔替代電鍍銅制作任意層互連印制板時的可靠性及其對電性能的影響。根據范·米塞斯屈服準則分析了塞孔材料CTE可靠性原理并進行實驗驗證,同時評估了塞孔階數、孔底殘膠、塞孔孔內氣泡對可靠性的影響,最后分析了導電膏塞孔對阻抗及損耗的影響。結果表明,對于導電膏塞孔工藝,在11階盲孔設計時,其熱應力、溫沖測試等性能測試均滿足產品可靠性要求,且導電膏塞孔對25G以下高速產品信號傳輸無明顯影響。
前言
導電膏塞孔是實現任意層互連的技術方案之一,其雛形是松下的ALIVH(Any Layer Interstitial Via Hole)技術和東芝B2it(Buried Bump Interconnection Technology)技術[1]。任意層互連技術發展的一個關鍵技術是微孔化,即層與層之間通過微孔進行導通互連。微孔加工目前激光鉆孔技術可以實現;而在微孔金屬化技術這塊,目前主要分三種:電鍍填孔、導電材料塞孔、銅凸塊[1]。其中,導電膏互連技術由于其用導電膏替代電鍍進行填孔,不僅精細線路、高厚徑比等制作工藝難度降低,流程簡化;而且可以實現綠色生產,節省能源等特點,因此該技術具有廣闊的發展前景。
導電膏主要成分是銅、錫、環氧樹脂,因此導電率較電鍍銅差,其結合與導通機理區別于電鍍銅方式,主要是通過高溫燒結在焊盤表層形成銅錫合金互連[2]。文章通過實驗設計,評估了導電膏塞孔互連對于高速信號完整性的影響,同時評估了材料熱膨脹系數與多階盲孔設計可靠性問題,為該技術的推廣應用提供技術參考。
1
試驗部分
1.1試驗材料與儀器
材料:very low loss覆銅板和半固化片、導電膏等。
儀器:四端口網絡分析儀、高低溫沖擊試驗箱、金相顯微鏡。
1.2試驗設計
(1)導電膏塞孔互連可靠性評估:
為評估導電膏塞孔互連結構可靠性,分別設計了30 ppm/℃、35 ppm/℃、45 ppm/℃不同CTE材料的測試板。同時設計了1、3、5、7、11階盲孔塞孔互連設計。可靠性測試條設計如下:
(2)塞孔互連對電性能影響:
為確定導電膏塞孔對于高速信號傳輸信號完整性影響,設計了8層板。采用阻抗計算軟件進行阻抗設計,單端阻抗設計為50Ω;差分阻抗設計為100Ω。其疊層結構及阻抗線設計如下:
2
結果與討論
2.1塞孔互連可靠性影響
2.1.1材料CTE影響
(1)材料CTE可靠性原理分析
根據范·米塞斯屈服準則[3],盲孔結構等效應力公式如下:
其中,Ef表示孔內物質彈性模量,vf表示孔內物質泊松比,af表示孔內物質熱膨脹系數,as表示層間介質材料<Tg下熱膨脹系數,Td表示測試最高溫,T0表示測試最低溫。因此,可將以上等效應力公式轉化為:
式中,△α為熱膨脹系數差異。在溫度沖擊過程中,受材料變形產生孔內應力的影響,電阻值相應產生一定的改變。從而可以將孔內應力與阻值變化之間建立函數關系:
因此,從以上推論可知:
即:在固定溫度沖擊測試溫度、時間等測試條件下,其可靠性結果正比于產品設計材料之間的熱膨脹系數差異[3-6]。
(2)材料CTE可靠性驗證
圖4為不同CTE材料1階盲孔設計對應-55℃-125℃溫度條件,200次溫沖循環阻值變化關系曲線。相同設計下,隨著盲孔塞孔材料與板材之間CTE差異的增大,其溫度沖擊過程中孔內界面應力增大,從而導致溫沖前后阻值變化增大。因此,對于產品設計,為滿足更好的可靠性,材料CTE越接近越好,而不是CTE越小越好。
2.2.2塞孔階數設計影響
圖5是相同材料下不同盲孔階數疊孔設計對應-55℃-125℃溫度條件,200次溫沖循環阻值變化關系曲線。隨著盲孔疊孔階數的增加,受外界溫度沖擊時內部應力疊加,導致熱脹冷縮過程變形量增大,溫沖阻值變化相應增大。該阻值變化值直接體現產品可靠性,因此,產品設計時應考慮疊孔影響。避免疊孔層數太多導致可靠性不良。從實驗結果可知,導電膏塞孔燒結互連結合力較好,盲孔疊孔階數每增加一層,阻值變化增大0.174%。盲孔設計11階時,溫沖前后阻值變化為6.88%,滿足±10%變化標準。
2.2.3塞孔氣泡影響
孔內氣泡主要受兩方面影響:一是導電膏內部空氣、揮發性成分存在,熱固化燒結時沒有排出殘留;另一方面受塞孔過程壓力、速度、抽真空等導致塞孔不飽滿影響。因此,氣泡或多或少會有存在,一般直徑大小<20μm。
圖6是11階盲孔疊孔設計華為無鉛+288℃三次漂錫處理后的切片圖。從圖可以看出,孔內導電膏中不均勻的分布有一些氣泡。但是熱應力測試后,盲孔頂底部及孔壁與介質材料界面都未發現分層等問題。圖7為盲孔頂底與銅面燒結界面IMC層掃描電鏡觀測圖。熱應力處理前后,IMC層保持完好,未出現裂痕等不良問題。因此,塞孔氣泡存在燒結完全的情況下,對產品可靠性無明顯影響。
2.1.4孔底殘膠影響
除塞孔控制外,激光鉆孔是導電膏塞孔互連工藝非常重要的一環。當孔底激光鉆孔樹脂或碳膜未清除干凈,塞孔后殘留樹脂或碳膜會阻礙孔內導電膏與底銅的燒結,無法形連續、均勻的IMC層,直接決定了信號導通性和可靠性。上圖8是孔底樹脂殘留導致溫沖過程中盲孔失效過程監控圖。
對上圖失效處切片可知,孔底與底銅結合處出現裂痕。對此處的導電膏樹脂、介質層樹脂和激光孔孔底與導電膏結合處進行元素分析對比可知,導電膏中的樹脂與介質層樹脂差別在于介質層樹脂中含有Si元素。而在激光孔孔底結合界面元素分析發現Si元素的存在,說明激光鉆孔有樹脂殘留。因此,導電膏塞孔工藝,需對激光鉆孔品質進行過程嚴格管控保證產品質量。
2.2塞孔互連信號完整性影響
2.2.1塞孔互連對阻抗的影響
下圖9是導電膏塞孔與常規電鍍填孔工藝相同設計下單端過孔阻抗對比。由于導電膏電導率較電鍍銅大,導電膏塞孔過孔阻抗較電鍍填孔過孔阻抗大2Ω,兩者之間過孔阻抗差異在4%左右。因此,對于導電膏工藝制作,在前端工程阻抗設計時需進行評估補償。
2.2.2塞孔互連對損耗的影響
圖10是導電膏塞孔與常規電鍍填孔工藝相同設計下單端損耗測試結果。在12.5 GHz測試頻率下,導電膏塞孔與電鍍填孔損耗分別為0.62 dB/cm和0.59 dB/cm,兩者之間差異0.03 dB/cm;當測試頻率繼續增大,兩者之間損耗差異開始明顯。頻率增大到20 GHz時,兩者損耗差異增大到0.12 dB/cm。因此,25G以下高速產品采用導電膏塞孔工藝信號損耗基本無影響。但對于更高速需求產品的應用則需評估塞孔互連對信號完整性影響來確認。
3
結論
通過以上試驗,得出以下結論:
(1)材料的選擇對于導電膏塞孔互連可靠性有著至關重要的影響,選擇與導電膏CTE越接近的材料、優化盲孔設計、做好激光鉆孔品質管控是提升導電膏塞孔互連產品可靠性的關鍵;
(2)隨著盲孔疊孔層數的增加,失效概率直線增大。常規Z-CTE值45 ppm/℃左右的材料,其盲孔疊孔設計11階可靠性測試滿足IPC標準要求。推論預估設計達到30階時會出現溫沖循環測試前后阻值超過±10%而失效;
(3)導電膏塞孔互連工藝對25G以下高速產品應用時信號傳輸無明顯影響;但隨著信號或頻率繼續增大,由于導電膏電阻率較電鍍銅大的原因,信號損耗開始有明顯差異。
-
PCB設計
+關注
關注
394文章
4725瀏覽量
87842 -
信號完整性
+關注
關注
68文章
1423瀏覽量
96057 -
電鍍銅
+關注
關注
0文章
26瀏覽量
9206 -
導電
+關注
關注
0文章
240瀏覽量
21734 -
可制造性設計
+關注
關注
10文章
2065瀏覽量
15879 -
華秋DFM
+關注
關注
20文章
3496瀏覽量
5032
原文標題:導電膏塞孔的可靠性及其對電性能的影響
文章出處:【微信號:ruziniubbs,微信公眾號:PCB行業工程師技術交流】歡迎添加關注!文章轉載請注明出處。
發布評論請先 登錄
相關推薦
淺析印制板的可靠性2
碳膜印制板制造技術概述及特點
線路電鍍和全板鍍銅對印制電路板的影響
電鍍對印制PCB電路板的重要性
網印貫孔印制板制造技術
如何才能獲取高可靠性的印制板?
干貨:PCB電鍍銅前準備工藝有哪些?
分析 | 電鍍銅前準備工藝:沉銅、黑孔、黑影,哪個更可靠?
如何提高印制板的可靠性
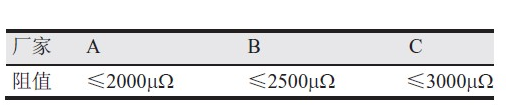
評論