在研發、設計、生產、封測、通路五大半導體產銷流程中,研發、設計所需的時間比以往多出50%以上,一個新產品的上市,背后還有長達12~18個月的Debugging等工作。為了使客戶更有效率的推出新產品,上游EDA公司除提供完整的產品線之外,也開始布局更多的軟件投資,而與云端服務業者的合作,也成了加速、效率化的捷徑。
對晶圓制造業者而言,80~90%的稼動率是常態,85~95%的良率都是基本的要求。但這些大規模的生產設備,所需要的相關投資已經成為天價,可以理解為何進入7nm世代之后,只有臺積電、三星電子(Samsung Electronics)與英特爾(Intel)有具體的投資計劃。
我們已經可以預測,到了比7nm更先進的工藝之后,供應端與需求端同時寡頭化將成為產業的關鍵趨勢。屆時,上游的設備、材料廠,如何與少數的買家協商最佳方案,也必然會是產業界津津樂道的話題。
至于封測廠商則可能面對更大的挑戰。大約有30%的資本支出將用在封測流程上,但封測業者如何驗證自己的價值,將是個非常困難的挑戰。從10年前開始,封測業者對于后續的投資便采取相對保守的措施,導致臺積電自行布局封測事業。
最后端的營銷通路,企業憂心的不是半導體技術,而是背后大規模的金融操作,會不會面臨新的挑戰。
全球六大晶圓代工業者工藝演進
半導體價值鏈的關鍵變革
1983年,韓國三星決定投入存儲器的發展行列,打破日本業者獨占的局面,埋下今日三星主導全球存儲器產業的種子。1987年,臺積電成立,并以獨特的晶圓代工模式,吹皺了全球半導體產業的整池春水。
1980年代,是日本第一的年代,美國半導體產業的實力無可比擬,沒有人料到三星、臺積電竟然成為全球三家角逐7nm以下最高階工藝的主導者。
三星、臺積電改變全球生態的原因各異,只是時空環境、產業條件不同,1980年代是工業時代的末期,誰能掌握投資資源,加上正確的企業定位與決心,就有可能翻云覆雨,成為一方之霸!
經過幾年沉潛、積累,三星與臺積電都在1990年代中期進入「井噴」階段。1993年,掌舵的三星董事長李健熙召開法蘭克福會議,宣示「生產不良品的人就是罪犯」,三星必須以全球頂級企業自許的企業方針,改變了三星的自我定位與策略方針。
三星開始以全球第一為目標,存儲器便是攻堅的核心事業部,再搭上PC在1990年代中期快速擴張的成長商機,三星終于成就了存儲器產業的霸業,并將原本領先的日商擠到市場的角落。
臺積電雖然從一開始就能站穩腳根,但真正成為世界級的公司,也在1990年代中期之后。手機、PC廠商的上游零件業者,逐年成為臺積電的座上賓。1990年代時,臺積電的主力客戶是二線的NVIDIA、ATI等繪圖芯片供應商,并非2000年以后的蘋果(Apple)、高通(Qualcomm)與聯發科。
而在21世紀的第一個10年,國內的海思、展訊或之后的挖礦機等業者,根本不在臺積電的雷達范圍之內。隨著產業條件的變革,三星、臺積電都能與時俱進,并在市場上呼風喚雨。
IC設計費用暴增縮短工時成關鍵
臺積電、三星都宣稱要在2020年建構3nm的代工能力,但據研究機構IBS估計,屆時每顆IC的設計費用至少5億美元起跳,如果高達15億美元的天價也不令人意外,而其中以GPU成本耗費至巨。
IBS指出,28nm平面型的IC設計平均費用為5,130萬美元,使用FinFET技術的7nm,則是需要2億9,780萬美元,設計費用幾乎多了6倍,因為背后所需要的IP、檢測等費用,都是跟著水漲船高。因此,設計公司必須選擇具有高超技術的晶圓代工廠,但晶圓代工費用也是令很多企業頭痛不已。
臺積電宣布2019第2季將進行5nm的風險生產,也將成為全球第一個量產5nm的企業,而三星則宣稱將在3nm工藝中使用GAAE(Gate-All-Around-Early)技術,三星并以MBCFET(Multi Bridge Channel FET)為這項技術命名。
各工藝半導體設計費用
FinFET的技術雖然可以讓三個不同面向的電流流通,GAAE技術卻可以在各個不同的角度、面向都可以達到電流流通,進一步提高效能。三星這項技術是與IBM、GlobalFoundries一起開發,但由于牽涉到蒸鍍等各種多元的技術、設備,巨額費用可想而知,估計現在會對這些技術有興趣的公司,不外乎高通、NVIDIA與蘋果而已。
上游EDA業者也受沖擊
過去類似亞馬遜(Amazon)、微軟(Microsoft)、Google這些云端服務大廠,一直嘗試說服各家企業將自己的運算功能、存儲設備放在由他們提供的云端系統上。這兩年企業端的消費者開始買單,「云端運算」不再只是口號,甚至不再是個議題,而是已經開弓的箭,再無回頭的可能。關鍵是這個大趨勢現在、未來對各個產業的影響,以及企業如何因應。
以微軟的Azure云端服務平臺為例,過去IC設計業者從EDA業者取得的各種設計工具,在自家的計算機系統上運算,不免要面對運算資源、速度的壓力,而存儲各種演算成果、信息,也必然面對一樣的侷限性。
事實上,IC設計業運用的工具越來越復雜,從前端的規格設定開始,包括Block design、Synthesis、Formal verification、Simulation,以及后端的Place and route、Static timing analysis、Physical verification、Tape-out,各大云端服務平臺的業者,都嘗試讓IC設計公司將EDA設計工具,透過云端系統得到最大的效率。
使用這些服務的企業,可以運用云端上已經備妥的各種運算資源,以On-premise的模式,高度彈性的使用最佳、最大的運算能力。這樣的服務架構,可以讓原本的設計流程加速。而及早上市這件事,對IC設計機構代表著更高的利潤、更低的成本,而這也可能是整個流程中,最具有價值的部分之一。
例如,前端Synthesis的流程,可以與Verification或Validation的流程平行處理。后端設計上可以使用EDA設計工具,以邏輯設計同步合圖(Mapping)的模式,可以與晶圓工藝完全吻合,以避免可能出現的偏差。
其他包括STA(Static Timing Analysis)、DFT(Design for test)等Validation的工具,在設計規則的確認(Design rules check)、LVS(Layout versus schematic)測試這些多元、重復不斷的動作,牽涉到大量Data set之間的互動,其實也都只是為了確保制造時的精確度而已。
這些動作如果能夠透過云端的架構,由功能更強大的數據中心來處理,不僅對于IC設計公司而言是成本、效率上的一大解脫,但也可能是未來非常關鍵的競爭模式。
此外,類似DFM(Design for manufacturing)的流程,通常有好幾千個Cores,也非常適合云端服務的平行處理架構,可以讓過去要花上好幾天的運算流程,縮短到幾個小時。我們可以期待,如果專利授權沒有太大的問題,這些EDA使用流程上的改善,將會是這個產業流程的創新與革命。
核心與存儲器用比大幅改善
如今,完備的基礎建設讓云端上的大量運算成為可能,企業可以優化計算機資源,可以利用虛擬的設備,在Linux/Windows的技術基礎上進行,微軟甚至說,核心(Core)與存儲器(Memory)之間的用比可以從以往的1:2,大幅改善為1:30。
現在連臺積電都與微軟Azure、AWS兩大云端服務公司合作,微軟Azure E系列Core與Memory的用比可達1:8。Azure M系列在Timing Analysis與Physical verification的流程上,則可以128 Cores對比3.8TB RAM,這些都可讓設備投資得到很好的回報。
在存儲設備上,Azure Storage提供多重存儲模式的選擇,例如名為「Blob」的服務系統,可以存儲大量非結構性的數據或檔案,也可以提供NFS的使用情境,這種方式既可以是單純的云端服務,也可以在線線下隨意選擇不同的作業環境。
針對Verification的流程,可能產生上百萬個非常小(4~16K)的臨時性檔案,Azure Avere也可以提供NFS的支援,而為了使所有的網絡通信環境無所窒礙,世界級的網絡巨擘都在布局海底電纜、光纖網絡,讓運算遲延(Latency)的現象降到最低。
這些新建的數據中心與基礎網絡,將隨著5G應用的擴大而同步推展,相關的需求也將水漲船高。
-
半導體
+關注
關注
334文章
27527瀏覽量
219892 -
eda
+關注
關注
71文章
2769瀏覽量
173439
原文標題:【深度專題】先進工藝設計費暴增 EDA走上云端
文章出處:【微信號:DIGITIMES,微信公眾號:DIGITIMES】歡迎添加關注!文章轉載請注明出處。
發布評論請先 登錄
相關推薦
功率半導體性能表征的關鍵技術研究與應用分析
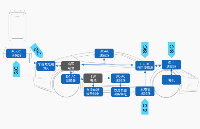
功率半導體性能表征的關鍵技術研究與應用分析
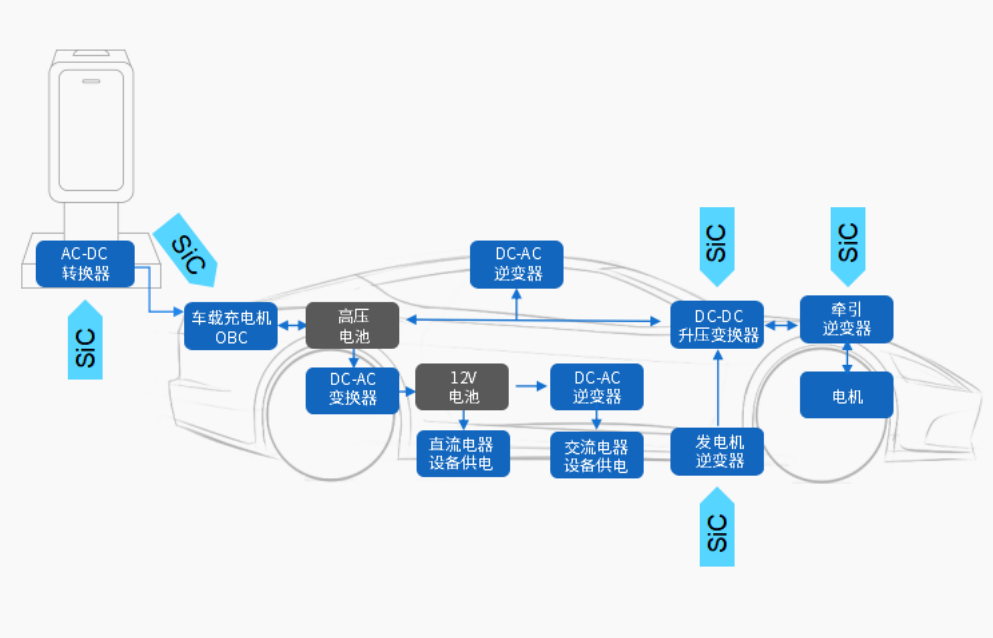
中國半導體的鏡鑒之路
可驗證AI開啟EDA新時代,引領半導體產業變革
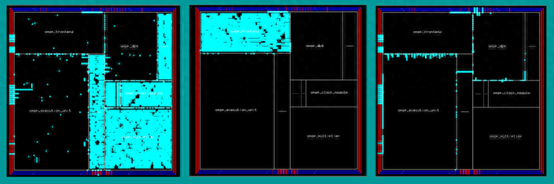
AI如何助力EDA應對挑戰
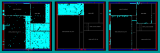
芯和半導體正式發布EDA2024軟件集
西班牙尋求與中國臺灣合作,共推120億歐元半導體宏圖
喜訊 | MDD辰達半導體榮獲藍點獎“最具投資價值獎”
晶科能源入選世界經濟論壇可再生能源價值鏈領先實踐案例
Syensqo加入全球半導體氣候聯盟(SCC)
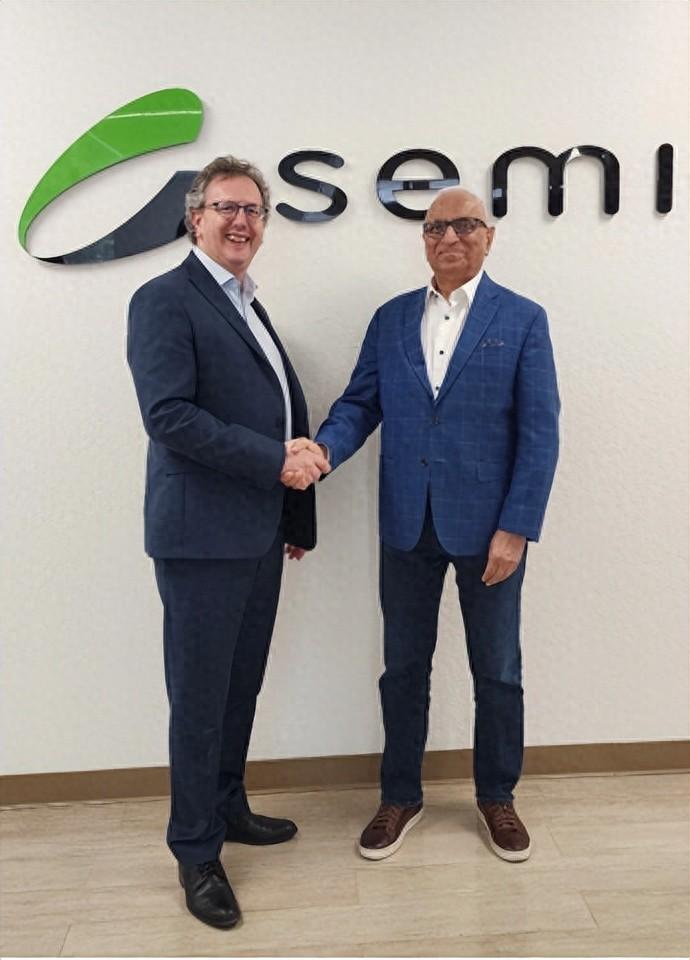
評論