Premium AEROTEC 專門從事形狀復雜的大型飛機部件的設計和生產,例如空客 320 系列的機身 19 段。為了提高產品件數,同時降低生產成本,Premium AEROTEC 組建了一臺專為航空領域研發的 KUKA 生產設備。由此在奧格斯堡誕生了目前全球最先進的飛機裝配線
最初情況:以較低的成本增加數量
目前投入使用的所有民航客機中,有三分之二是只有一條通道(單通道)的標準機身飛機,并且這種需求還在不斷增加。自從引入單通道機型后,空客公司在這一市場所占的份額也在不斷上升。為了滿足這一需求,空客公司最重要的量產機型結構供應商 Premium AEROTEC 需要大大提高產品件數,同時降低生產成本。然后很快發現:只有通過自動化,才能實現每年提供最多 575 個單通道機身段的目標。
任務:智能聯網自動化
具體來說是要使空客機身 19 段的生產實現自動化。這一段在機身中位于客艙末尾和最后一段(輔助動力裝置位置)之間。與呈圓錐形的機身其余部位不同,由六片蒙皮分塊組成的 19 段向后收窄,這種特殊形狀對各個分段的裝配提出了更高要求。KUKA 生產設備應以全自動方式將加固元件(桁條)、連接角架(夾扣)和邊緣支架與蒙皮分塊的外殼鉚接起來。與這一生產步驟相關的蒙皮分塊的運輸同樣應以自動方式進行。手動裝配步驟應與智能自動化解決方案連接起來。
解決方案:KUKA提供一站式解決服務
蒙皮分塊需經過長達 80 米的 KUKA 生產設備。在手動和自動化步驟中對其進行鉚接并預組裝為機身段半體。每月可生產最多 50 個機身段。使用三臺KUKA KR 1000 titan 搬運機器人和三臺“全電動自動鉆孔/鉚接裝置”。這些全部由 KUKA 制造,其中也與其分包商合作,如美國 Gemcor 公司。
KUKA 以系統集成商身份,與 Premium AEROTEC 和其他合作伙伴的負責人一起,花了兩年時間實施這一項目。KUKA 主導了規劃與研發工作,負責生產和采購所有組件和設備部件,集成控制系統,協調所有分包商,并確保按時組建好生產設備并投入運行。
走向透明生產的工業 4.0
在生產流程開始,每片蒙皮分塊都會獲得一塊RFID 芯片。根據這塊芯片,各個工作站上的搬運機器人和鉚接設備可識別正在處理的部件,并切換至相應的工具等。由此可在整個生產流程中無縫追蹤每個部件,從而實現完全符合工業 4.0意義的透明生產。
創新的輕型部件支架
迄今為止采用的部件支架是重達 1000 千克的鋼制模塊托盤。KUKA 與 Premium AEROTEC 一起研發了一個鋁合金輕型結構作為機器人上的抓爪,以及一個加上蒙皮分塊在內也僅重約 400 千克的部件支架。負載可以快速而精確地移動,從而大大降低了生產和裝配成本。
集成各種控制系統
KUKA 集成了Siemens Sinumerik 840D作為上級機器控制系統。KUKA 還定義并實現了 Siemens 控制系統和KUKA 機器人控制系統 KRC4之間的接口。 由此,工人可通過單一的熟悉界面操作所有機器。在此,使用 KUKA 搬運機器人還是第三方的機器并不重要,例如 KUKA 在系統中無縫集成了美國的自動鉚接裝置。通過 KUKA 自主創立的控制標準 miKUKA, 可收集信息,在生產線上可視化顯示,并提供給客戶系統。鉆孔/鉚接流程的機器人運動已全部離線編程好。
自動化解決方案的優勢:
?縮短維護時間和通過時間?降低物流成本?透明的生產流程?手動操作步驟更符合人體工學?在成本低廉的同時,實現最高的精度和生產率
-
機器人
+關注
關注
211文章
28526瀏覽量
207585 -
自動化
+關注
關注
29文章
5598瀏覽量
79443 -
智能聯網
+關注
關注
0文章
21瀏覽量
10901
原文標題:Premium AEROTEC 可以更迅速、更低成本、更透明地生產空客飛機的機身段
文章出處:【微信號:jiqirenyingyong,微信公眾號:jiqirenyingyong】歡迎添加關注!文章轉載請注明出處。
發布評論請先 登錄
相關推薦
用ADS1191設計一臺心電儀遇到的幾個疑問求解
臺積電2納米工藝生產設備提前部署完成
手持式激光焊機一臺多少錢?
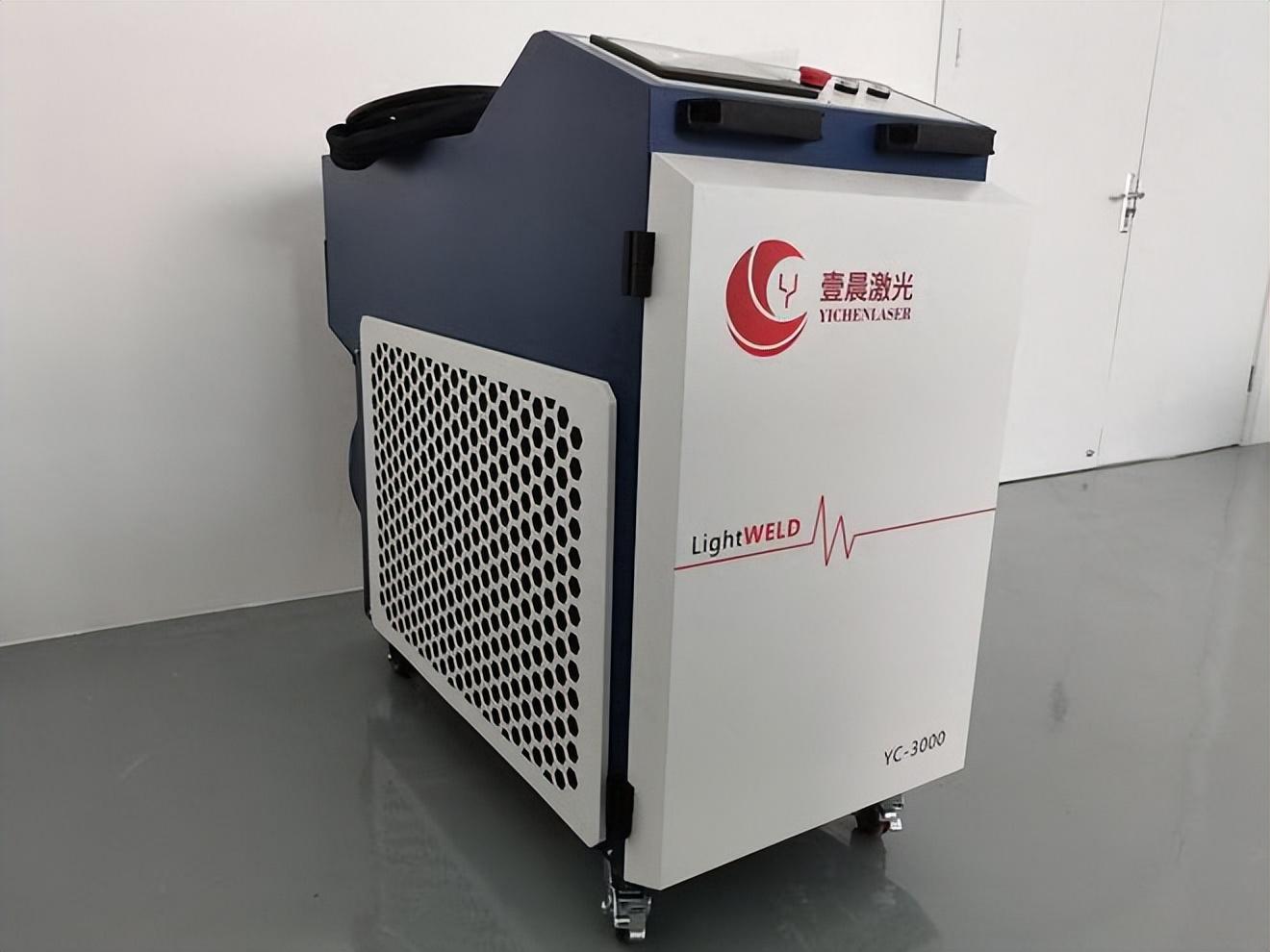
我有一臺天津無線電一廠生產的HG1946型數字繁用表需要修理,很長時間沒找到電路圖,請壇里的老師提供幫助。
消息稱三星組建百人工程師團隊
曝光航空機器人激光焊接機可以為企業節省多少錢
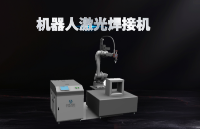
STM32F401VC USB枚舉成自定義HID,為什么每臺設備連接到同一臺電腦上都要有一個加載驅動的過程?
三星在印度設立SSD研發團隊
見到一臺國外的設備,直接在labview界面里執行C文件,哪位大俠知道怎么實現的,或者有什么工具包
本地電腦遠程控制工控現場一臺豐煒PLC上,實現讀寫與監控PLC程序
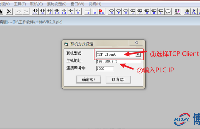
評論