目前,快速原型制造技術的發展趨勢是直接制造出全密度、高強度的功能性金屬零件,也稱為金屬直接成型制造技術。基于快速原型技術的快速模具制造是金屬直接成型制造技術的最直接應用之一,它提供了一條從模具CAD模型快速制造模具的新概念和方法,使模具制造在縮短研制周期、提高制造柔性、提高質量等方面取得了顯著效果。目前,金屬零件直接成型加工都以平面為基體,實際生產中還可能要求以金屬零件的回轉表面為基體進行金屬零件直接成型加工,例如汽車輪胎模具快速原型加工、汽車制動轂內表面花紋快速原型加工、回轉類零件表面損傷修復等。以輪胎模具快速原型加工為例。在輪胎模具的回轉內表面上規則排列著用于加工輪胎花紋的型腔,這些型腔的精度和質量直接影響輪胎的質量和性能。目前輪胎模具的基本制造過程為:下料或鑄造_+車削加工_+電火花加工_加工排氣孔_+雕刻字符一模具后處理_÷表面拋光。其中電火花加工主要完成輪胎模具的復雜型腔的成形加工,是輪胎模具加工的最重要環節,占總加工周期的70%—90%。由于電火花加工效率較低,因此目前輪胎模具制造過程工序復雜,加工時間長,靈活性差。如果采用快速原型技術進行輪胎模具的快速制造,則可以克服上面的缺點,提高輪胎模具加工的效率和靈活性。
本文研究以回轉表面為基體的金屬零件直接成型技術的基本理論和加工實驗,與常規快速原型加工不同,回轉表面金屬零件直接成型加工需要在回轉表面上進行層疊加工,因此其數據處理和加工過程控制都與常規快速原型加工具有較大的區別。本文首先研究以回轉表面為基體的金屬直接成型技術的基本原理,然后推導回轉表面金屬零件直接成型加工的實體模型分層算法,編制以回轉表面為基體的快速原型加工軟件系統,并進行加工實驗研究。
1 以回轉表面為基體的金屬零件直接成型技術的基本原理
傳統快速原型加工設備通常以平面為基體,因此只有平動軸而沒有回轉軸,激光器相對于被加工工件只能進行平行運動而不能進行回轉運動。為實現以回轉表面為基體的金屬零件直接成型加工,必須在傳統快速原型加工設備中引入回轉軸。如圖1所示,在原有X、y、Z 3個平動軸的基礎上,引入一個繞z軸旋轉的回轉軸,構成一個四軸聯動加工系統(即3個平動軸加1個轉動軸)。在加工過程中,金屬零件基體在回轉軸的帶動下作勻速回轉運動,以其回轉表面(內表面或外表面)為基體進行層疊加工,這樣就可以在回轉表面加工出符合精度要求的表面熔覆結構,實現以回轉表面為基體的金屬零件直接成型快速原型加工。
圖1 以回轉表面為基體的金屬零件直接成型加工設備
目前,金屬直接成型制造技術的實現方法包括多相組織沉積制造技術、三維堆焊成型技術、選擇性激光高溫燒結技術和激光熔覆技術等。其中激光熔覆技術利用高能激光束局部熔化金屬表面形成熔池,同時采用送粉裝置將金屬粉末噴入熔池,進而形成與基體金屬冶金結合、稀釋率低并且與基體密度相近的金屬層。與其它金屬直接成型技術相比,激光熔覆技術具有獲得的熔覆金屬層密度與常規金屬零件相同,加工過程便于數字控制,可以實現金屬零件外形尺寸的精確控制,對基材的熱影響小等優點。由于激光熔覆技術所具有的這些突出優點,因此它是金屬直接成型制造技術諸多方法中最具發展前途的制造技術之一。本文采用激光熔覆技術進行回轉表面金屬零件直接成型技術研究,如圖2所示。
圖2 金屬零件直接成型加工設備
2 以回轉表面為基體的金屬零件直接成型加工的模型分層算法
與常規快速原型加工相似,回轉表面快速原型加工也需要首先對CAD模型進行分層計算,但是由于是在回轉表面上進行快速原型加工,因此其分層算法與常規快速原型分層算法具有較大的區別,主要表現在以下3個方面:
(1)分層計算采用圓柱面分層而不是平面分層。傳統快速原型加工采用一組平行平面對STL實體模型進行分層計算,而回轉表面快速原型分層算法則采用一組同軸圓柱面與實體模型進行相交求解,這是回轉表面快速原型加工與傳統快速原型加工在分層算法上的最大區別;
(2)實體模型內部截面的填充采用螺旋線而不是直線,常規快速原型加工基于直角坐標系,用于實體模型內部截面填充的掃描路徑為笛卡爾坐標系內往復運動的直線段,而回轉表面快速原型加工以螺旋線為掃描路徑。在這過程中,當運動軌跡運動到實體模型內部時,打開激光器光闡進行激光熔覆加工;當激光器運動到實體模型外部時,關閉激光器光闡停止激光熔覆加工;
(3)實體模型內部截面的填充采用單向掃描而不是往復掃描。由于金屬零件基體通常具有較大的慣性,并且加工設備的回轉軸可能存在回程誤差,因此經常改變運動的速度和方向不可避免地導致運動精度的降低。因此,以回轉面為基體的快速原型加工的掃描軌跡采用單向均速螺旋線運動,而不采用往復掃描的方式。
以回轉表面為基體的快速原型加工分層算法可以歸納為4個基本步驟:
驟1 收集用戶設置信息并進行必要的初始化工作
首先需要收集用戶的設置信息,針對不同的實驗內容,用戶可能提出不同的分層要求,因此用戶設置信息是分層計算的重要依據。需要收集的信息首先包括起始圓柱面半徑,螺旋線螺距和圈數等基本信息。由于分層計算通常需要進行多層計算,因此還需要包括各層之間距離、總層數和半徑增長方向等其它信息。除此之外,在計算開始之前還需要進行必要的初始化工作,如讀入STL文件并生成計算所需的數據結構,計算實體模型的總體高度和半徑范圍等。
步驟2 計算回轉類實體模型與圓柱面之間的交線
在STL模型中,實體模型是由一系列三角面片組成的,因此實體模型與圓柱面的相交求解首先涉及到三角面片與圓柱面的相交求解問題,三角面片與圓柱面的相交求解可以分為兩個步驟進行。首先計算圓柱面與三角面片所在無限平面之間的交線,獲得的交線是一條空間橢圓線。由于三角面片只是無限平面的一部分,因此三角面片與圓柱面之間的交線應該只是該空間橢圓線的一部分,第二個步驟就是求出空間橢圓線參數的取值范圍。設實體模型中某三角面片的3個項點為P1、P2和P3,則可以獲得該三角面片所在無限平面π的方程:
若使用半徑為r的圓柱面對實體模型進行分層操作,則該圓柱面的參數方程可以寫為:
將式(1)代入式(2)可以獲得無限平面與圓柱面的交線:
式(3)所代表的曲線是一段空間橢圓線,其參數t的取值范圍為[0,2π]。如上所述,三角面片與圓柱面的交線應該只是式(3)代表的無限平面與圓柱面交線的一部分。如圖3所示,根據三角面片與圓柱面之間位置關系的不同,三角面片與圓柱面之間的交線可能是空間橢圓線的1、2或3段,三角面片與圓柱面之間也有可能根本不存在交線。因此,參數t的取值范圍應該是E0,2仃]中的0—3個區間。
圖3 三角面片與圓柱面的交線
為確定三角面片與圓柱面之間交線的參數取值區間,考察三角面片及圓柱面在X-Y平面上的投影。如圖4所示,三角面片在X-Y平面上的投影為一個三角形,而圓柱面在曩y平面上的投影為一個圓,通過計算三角形與圓之間的交點,可以確定三角面片與圓柱面交線的參數范圍。
三角面片與圓柱面交線的參數范圍通過以下3個步驟獲得:
①計算三角形與圓的所有交點,需要注意的是由于切點的存在并沒有改變三角形與
圖4 交線在X-Y平面上的投影
圓的相交狀態,因此切點不在考慮范圍之內;
②將所有交點處參數按照從小到大的順序進行排序操作,獲得一個參數序列
③判斷參數t=0時該點是否位于三角形內部。如果該點位于三角形的內部,則[0,t1]為第一段交線的參數范圍,[t1,t2]為第二段交線的參數取值范圍,以此類推。如果該點位于三角形的外部,則[t1,t2]為第一段交線的參數范圍,[t2,t3]為第二段交線的參數取值范圍,以此類推。
對于實體模型中的所有三角面片,均采用這種方法計算其與圓柱面之間的交線,這些曲線集合構成了圓柱面內若干個封閉曲線,它代表了實體模型與圓柱面之間的交線集合。
步驟3 螺旋線掃描軌跡的生成
以回轉面為基體的快速原型加工采用空間螺旋線進行實體模型內部截面的填充。螺旋線被實體模型分為內外兩個部分,在進行加工時,當激光器運動到實體模型的內部時,打開激光器光闡進行激光熔覆加工;反之,當激光器運動到實體模型的外部時,關閉激光器光闡停止熔覆加工,這樣就可以獲得實體模型所定義的熔覆結構。為達到這一目的,需要計算螺旋線與實體模型的交點,這樣才能區分螺旋線的內部和外部邊界,這可以通過計算螺旋線與該圓柱面和三角面片交線(上一步驟所計算的空間橢圓線集合)之間的交點獲得。
螺旋線與空間橢圓線都位于圓柱面內,為求它們之間的交點,將圓柱面展開為一個平面。隨著圓柱面的展開,空間螺旋線被展開為一組平行線段,而空間橢圓線集合則被展開為若干個封閉曲線。這樣,空間螺旋線與空間橢圓線的相關交解轉化為線段與曲線的相交求解問題。
如圖5所示,展開之后空間橢圓線仍然可以通過式(3)表示,為方便下面的推導,將其改寫為式(4):
圖5 螺旋線的展開
利用非線性方程求解方法,可以求出方程(7)在參數范圍[ti,ti+1]內的解。求出第1圈螺旋線與圓柱面內所有空間橢圓線的交點之后,將所有交點處參數按從小到大的順序進行排序操作,從而獲得參數序列{t1,t2,t3,...}。則[0,t1]為第一條螺旋線的參數范圍,[t1,t2]為第二條螺旋線的參數范圍,以此類推。為判斷各段螺旋線是位于實體模型內部還是外部,考察參數t=O時螺旋線的點是否位于實體模型內部。如果該點位于實體模型內部,則[O,t1]段螺旋線位于模型內部,[t1,t2]段螺旋線位于模型外部,以此類推。當t=0時螺旋線的點位于實體模型外部時,則與上述情況相反。
步驟4 計算結果的后置處理
為生成完整且合理的加工軌跡,還需要對計算結果進行必要的后置處理,主要包括以下兩部分內容:
①各層掃描軌跡的過渡連接。上述計算過程只生成了各層圓柱面內的螺旋線軌跡,為實現連續的加工過程,各層螺旋線掃描軌跡之間還必須用直線軌跡進行過渡。過渡軌跡從某層最一后條軌跡的終點開始,到下一層第一條軌跡的起點結束;
②多余掃描軌跡的去除。所生成的掃描軌跡中可能有一些軌跡沒有任何熔覆加工,這些軌跡可以視為是多余的軌跡,應該予以去除,并采用適當的過渡軌跡過渡到下一個存在熔覆加工操作的軌跡的起點。
圖6 為一個計算實例,使用Solidworks軟件在半徑為100mm、高度為50ram的圓柱體外表面包覆5個高度為38ram英文字母(圖6左側部分)。使用上述分層算法對導出STL文件進行分層計算,取分層圓柱面半徑為101mm,計算結果如圖6右側部分所示,其中實線是位于實體模型內部的軌跡,虛線是位于實體模型外部的軌跡。
圖6 計算實例
3 以回轉表面為基體的快速原型加工軟件
以回轉表面為基體的快速原型加工軟件系統主要由兩部分組成:即數據處理部分和加工控制部分。數據處理軟件根據上一節描述的圓柱面分層算法對實體模型進行分層計算,其輸入是由實體建模軟件(如Unigraphics、Solidworks等)導出的STL文件,輸出則是包含了各層掃描運動軌跡和激光器控制信息的數據文件。加工控制軟件主要用于實現加工過程所涉及的各項控制操作,包括加工設備各軸的運動控制、送粉器控制以及激光器光閘開關操作等,控制操作的依據是數據處理軟件所生成的數據文件。整個軟件系統采用MS VC++編制,并且使用OpenGL和Glut圖形庫實現實體模型及分層結果的三維顯示。
3.1 數據處理軟件
數據處理軟件是分層算法的軟件實現。由于分層過程中需要用到不同類型的幾何元素,并且這些幾何元素之間存在著一定的內在聯系,因此根據面向對象編程原理,建立幾何元素的類層級結構。如圖7所示,CGeometry類是所有圖形類的基類,它定義了所有圖形類共有屬性和接口。繼承于CGeometry類的CCurve類則是所有曲線類的基類,它定義了
圖7幾何元素類的層次結構
曲線類的基本屬性和接口,如查詢該曲線是否位于回轉體內部,查詢某一參數處的坐標位置等,以及該曲線的運動控制線等。直線類CLine3D、線段類CLineSegment3D和二次曲線類CConic都是繼承自曲線類CCunre,其中二次曲線類還派生出了圓類CCircle3D、空間橢圓線段類CConicSection和螺旋線類CSpiral等。除此之外,其它類還包括派生于CSurface類代表圓柱面的CCylinder類,派生于CGeometry類的代表STL模型中三角面片CFacet類等。
如圖8所示,數據處理軟件在讀入STL文件之后,生成模型特定的數據結構,之后采用基于圓柱面的分層算法對STL模型進行分層計算,計算結果是一個CCurve類指針鏈表,該鏈表通過序列化操作以文檔的形式保存起來。加工控制軟件通過打開保存的文檔獲得曲線鏈表,然后根據這些曲線信息控制伺服電機及激光器光闡的操作。
圖8 軟件的整體結構
3.2 加工過程控制軟件
在獲得分層計算結果之后,由加工過程控制軟件實現快速原型加工過程中各軸的運動控制和激光器光闡控制,此外還包括一些輔助操作功能,如工作臺移動、激光器控制、工藝參數設置和系統參數設置等。采用研華公司的PCIl240運動控制器實現加工過程中各軸的運動控制,同時使用其輸入/輸出功能實現激光器電子光闡的開關操作。為了降低系統模型與人機交互界面之間的耦合,提高軟件設計的靈活性,軟件系統采用MVC(即M0del-View·Controller)結構(圖9)。整個軟件由模型、視圖和控制3部分組成,模型負責處理應用程序的數據和操作邏輯;視圖用于模型數據的顯示以供用戶觀察,同時還可以接受用戶的輸入;控制部分的作用是將視圖的用戶輸入以系統模型可以接受的形式傳遞給系統模型。
圖9 加工軟件的內部結構
系統模型用于處理回轉類零件激光熔覆加工過程中的所有數據和控制邏輯。系統控制的對象包括各軸伺服電機、激光器光闡、送粉器電機等。除此之外,為實現加工過程中非常重要的定時操作,模型還包含了3個軟件定時器,這些定時器均采用Windows多媒體定時器,分別用于用戶界面更新、激光器光闡開關檢測、加工軌跡末尾檢測等工作。以激光器光闡開關定時器為例,該定時器僅在進行螺旋線加工時開啟,為獲得較高的加工精度,通常設該定時器的延時時間小于5ms。當定時器的延時時間到達時,定時器通知系統模型執行相應的處理函數。在處理函數中,讀取當前加工位置,并與分層計算結果進行比較,如果當前位置位于模型的內部則打開激光器,否則關閉激光器電子光闡。
加工的操作邏輯,控制對象包括各軸電機、激光器光闡、送粉器電機及定時器的啟動和停止等。操作邏輯是基于事件驅動的在不同狀態之間進行轉換的過程,采用有限狀態機(Finite-State Machines)可以方便地對整個系統的狀態及其轉換進行描述。如圖10所示,系統共有5個狀態,即Empty(未打開數據文件)、Ready(準備就緒)、Moving(運動)、Machinig(加工)、Pause(暫停)。系統在不同狀態之間的轉換會觸發與該轉換相關的動作,例如由就緒狀態轉換到加工狀態時將進行以下操作:啟動送粉器電機、運動控制器根據當前軌跡控制各軸電機進行加工運動、啟動界面更新定時器和軌跡末尾檢測定時器等。采用狀態圖的優點是可以直觀清晰地反映出各狀態之間的轉換關系,極大地方便了軟件實現。輔助功能用于加工之前的準備工作。工作臺移動功能主要實現定位移動、手工移動、回零運動和坐標設置等。定位移動和手工移動功能主要用于待加工工件的定位和調整。系統的使用者可能根據實驗內容的不同采用不同的工藝參數,因此系統還必須提供工藝參數管理功能。工藝參數主要包括熔覆軌跡速度、非熔覆軌跡速度和送粉器旋轉角速度等。激光器控制主要實現激光器各種控制操作,如電子光闡、氣動光闡、引導激光和保護氣體的開關控制。系統設置功能主要用于設置各軸的脈沖當量等功能,圖11為所編制的加工控制軟件的用戶界面。
圖10 加工過程的狀態以及狀態之間的轉換
圖11 加工控制軟件用戶界面
采用該軟件進行了加工實驗,圖12為加工結果,該實驗在回轉表面加工了若干個漢字和英文字母。
圖12 加工實驗結果
表1列出了該實驗的基本實驗參數。
表1 實驗參數
4 結論
以回轉表面為基體的快速原型加工可以用于汽車、國防、航空、航天等多個領域,例如汽車輪胎模具的快速制造,汽車制動轂內表面花紋的快速制造,航天航空領域中大型金屬零件回轉表面的激光熔覆修復等。如果用于基于回轉表面的模具的快速制造,該技術可以大幅度提高模具加工制造效率,并可以具有很大的靈活性。此外,對于長時間使用所造成的金屬零件回轉表面損傷問題,應用該技術可以延長易損回轉表面的使用壽命。由于回轉軸參與金屬直接成型加工過程,因此分層算法及加工控制與常規快速原型加工具有較大的區別。本文采用基于圓柱面分層的方法研究了以回轉表面為基體的快速原型加工的STL模型分層算法,并在該分層算法的基礎上開發了數據處理軟件及加工軟件。
-
激光器
+關注
關注
17文章
2588瀏覽量
61020 -
CAD
+關注
關注
18文章
1099瀏覽量
73072
發布評論請先 登錄
相關推薦
自動零件分析儀的原理和應用
加工軸類零件的注意細節
模架、模具、零件相關知識
切削參數對零件加工精度影響的研究
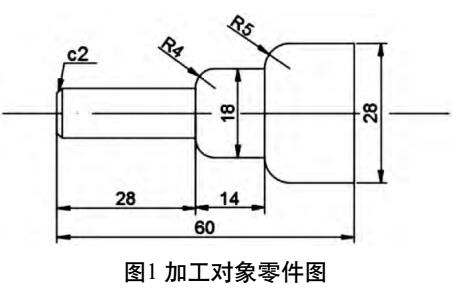
評論