文章來(lái)源:學(xué)習(xí)那些事
原文作者:小陳婆婆
本文介紹了半導(dǎo)體集成電路制造中的晶圓制備、晶圓制造和晶圓測(cè)試三個(gè)關(guān)鍵環(huán)節(jié)。
半導(dǎo)體集成電路制造中晶圓制造,可以分為五大制造階段:
本文針對(duì)前三個(gè)步驟進(jìn)行介紹,分述如下:
晶圓制備
晶圓制造
晶圓測(cè)試
晶圓制備
在晶圓制造中,其演變趨勢(shì)是尺寸不斷增大,其帶來(lái)的影響如下:
生產(chǎn)效率:增大晶圓尺寸可以顯著提高生產(chǎn)效率。同樣一臺(tái)加工設(shè)備,在處理大尺寸晶圓時(shí),由于每片晶圓上能容納的芯片數(shù)量顯著增加,因此單位時(shí)間內(nèi)可以生產(chǎn)的芯片總量也隨之增加。
生產(chǎn)成本:增大晶圓尺寸可以降低生產(chǎn)成本。大尺寸晶圓減少了晶圓之間的切割損耗,進(jìn)一步提升了材料利用率,同時(shí)降低了單顆芯片的平均生產(chǎn)成本。
芯片設(shè)計(jì):大尺寸晶圓為芯片設(shè)計(jì)提供了更大的空間,使得設(shè)計(jì)師能夠在單片晶圓上實(shí)現(xiàn)更復(fù)雜、更高效的電路設(shè)計(jì)。
工藝復(fù)雜性:晶圓尺寸增大也增加了制造工藝的復(fù)雜性。例如,對(duì)單晶硅生長(zhǎng)的均勻性要求更高,拉制大尺寸單晶硅棒時(shí)需精確控制溫度、旋轉(zhuǎn)速度等參數(shù)。
設(shè)備投資:大尺寸晶圓的生產(chǎn)線需專用設(shè)備,如EUV光刻機(jī)單臺(tái)成本超1億美元,且配套的沉積、蝕刻設(shè)備價(jià)格不菲。
晶圓制造
晶圓制造是半導(dǎo)體集成電路制造的核心環(huán)節(jié),它按照一定的工藝流程,通過(guò)反復(fù)多次對(duì)晶圓進(jìn)行清洗、薄膜制備、光刻圖形、刻蝕及摻雜等加工工藝,最終在晶圓上完成集成電路的芯片制造。
晶圓制造廠房?jī)?nèi)通常會(huì)根據(jù)各單項(xiàng)工藝模塊劃分不同的區(qū)域,以確保生產(chǎn)流程的順暢和高效。
光刻區(qū):將設(shè)計(jì)好的電路圖案轉(zhuǎn)移到晶圓表面。通過(guò)光刻膠和掩模版進(jìn)行曝光、顯影和刻蝕等步驟。光刻膠在紫外光照射下發(fā)生化學(xué)反應(yīng),形成與掩模版圖案相對(duì)應(yīng)的圖形。然后,通過(guò)刻蝕去除未被光刻膠保護(hù)的區(qū)域,形成所需的電路結(jié)構(gòu)。隨著器件特征尺寸的減小,光刻機(jī)所用的光源波長(zhǎng)向深紫外方向轉(zhuǎn)移,以提高光刻精度。現(xiàn)在,光刻間照明多用黃光,因此光刻間有時(shí)也被稱為黃房區(qū)。
刻蝕區(qū):去除晶圓表面材料,形成特定圖形。包括濕法刻蝕和干法刻蝕。濕法刻蝕使用化學(xué)溶液去除材料,而干法刻蝕則通過(guò)等離子體或反應(yīng)離子束等物理或化學(xué)方法去除材料。早期主要是濕法刻蝕,刻蝕通常和清洗在一個(gè)區(qū)域。但隨著器件特征尺寸的減小,各向異性的干法刻蝕用得更多。干法刻蝕具有更好的側(cè)壁控制和關(guān)鍵尺寸控制能力,能夠滿足更精細(xì)的電路結(jié)構(gòu)需求。
離子注入?yún)^(qū):調(diào)整晶圓表面的電特性,形成所需的摻雜層。使用離子注入機(jī)將加速的摻雜原子離子束轟擊晶圓表面,將雜質(zhì)原子注入到晶圓內(nèi)部。注入后的晶圓通常需要進(jìn)行退火處理,以修復(fù)損傷并激活摻雜原子。早期對(duì)半導(dǎo)體摻雜主要是采取高溫爐擴(kuò)散工藝。但隨著器件特征尺寸的減小,對(duì)PN結(jié)結(jié)深和雜質(zhì)濃度在硅中分布的形貌要求提高,離子注入技術(shù)逐漸成為主流的摻雜方法。離子注入技術(shù)具有摻雜濃度高、均勻性好、可控性強(qiáng)等優(yōu)點(diǎn)。
薄膜區(qū):在晶圓表面形成各種薄膜,如絕緣層、半導(dǎo)體層或?qū)w層。包括化學(xué)氣相沉積(CVD)和物理氣相沉積(PVD)等方法。CVD通過(guò)熱分解或化學(xué)反應(yīng)將氣體化合物沉積在襯底上;PVD則通過(guò)物理過(guò)程如蒸發(fā)或?yàn)R射將材料沉積到襯底上。薄膜制備在晶圓制造中應(yīng)用廣泛。例如,SiO?薄膜常作為絕緣層使用,多晶硅薄膜用于制作晶體管柵極等。
擴(kuò)散區(qū):雖然現(xiàn)代晶圓制造中高溫爐擴(kuò)散工藝幾乎不再使用,但擴(kuò)散區(qū)這一名稱仍被沿用。現(xiàn)在,該區(qū)域主要用于熱生長(zhǎng)氧化硅膜、傳統(tǒng)的熱退火和快速熱退火(RTA)等工藝。隨著器件特征尺寸的減小和工藝要求的提高,擴(kuò)散區(qū)的工作內(nèi)容也發(fā)生了變化。現(xiàn)在,該區(qū)域更注重于氧化硅膜的質(zhì)量和退火工藝的效率。
金屬化區(qū):在晶圓表面形成金屬互連層,以便將各個(gè)器件連接起來(lái)形成完整的電路。包括鋁金屬化工藝和銅金屬化的大馬士革工藝等。鋁金屬化工藝需要電子束淀積鋁、磁控濺射鋁以及鋁的干法刻蝕工藝;而銅金屬化的大馬士革工藝則通過(guò)填充銅到預(yù)先刻蝕好的溝槽中形成互連層。隨著器件特征尺寸的減小和工藝要求的提高,銅金屬化的大馬士革工藝逐漸成為主流的金屬化方法。該工藝能夠避免銅對(duì)下面器件部分的沾污,提高電路的性能和可靠性。
外延區(qū):在硅襯底上生長(zhǎng)一層單晶硅薄膜(同質(zhì)外延)或在硅襯底上生長(zhǎng)其他材料的薄膜(異質(zhì)外延),以滿足特定器件的需求。包括氣相外延(VPE)等方法。通過(guò)化學(xué)反應(yīng)在晶圓表面沉積一層新的單晶硅層或其他材料的薄膜。外延工藝在高性能集成電路和特殊器件制造中有廣泛應(yīng)用。例如,外延層可以用于制作高速度的晶體管、低功耗的器件等。
為了進(jìn)一步提高光刻精度和效率,出現(xiàn)了極紫外光刻(EUVL)技術(shù);為了改善刻蝕工藝的性能和效率,出現(xiàn)了原子層刻蝕(ALE)技術(shù)等。這些新技術(shù)的應(yīng)用使得晶圓制造過(guò)程更加精細(xì)、高效和可靠。
晶圓測(cè)試
晶圓測(cè)試是半導(dǎo)體制造過(guò)程中的關(guān)鍵環(huán)節(jié),它旨在確保每個(gè)芯片在封裝前都符合設(shè)計(jì)規(guī)格和功能要求。晶圓測(cè)試包括在晶圓制造工藝過(guò)程中的各種在線檢查、測(cè)量,以及在芯片制造完成后用探針卡(Probe Card)對(duì)集成電路芯片進(jìn)行的功能和性能測(cè)試。以下是晶圓測(cè)試階段的詳細(xì)分述:
在線檢查與測(cè)量
目的:在晶圓制造工藝過(guò)程中進(jìn)行實(shí)時(shí)檢查,確保工藝參數(shù)符合標(biāo)準(zhǔn),及時(shí)發(fā)現(xiàn)并糾正工藝偏差。同時(shí),對(duì)晶圓的各種物理參數(shù)進(jìn)行精確測(cè)量,如直徑、平整度、厚度等,以確保晶圓的質(zhì)量符合標(biāo)準(zhǔn)要求。
方法:利用光學(xué)或其他對(duì)準(zhǔn)技術(shù),將晶圓上的測(cè)試點(diǎn)與探針卡精確對(duì)齊,進(jìn)行實(shí)時(shí)檢查。同時(shí),使用先進(jìn)的測(cè)量?jī)x器和設(shè)備,如激光干涉儀、原子力顯微鏡等,對(duì)晶圓進(jìn)行非接觸式測(cè)量。
應(yīng)用:在線檢查廣泛應(yīng)用于晶圓制造過(guò)程中的各個(gè)工藝模塊,如光刻、刻蝕、摻雜等,以確保工藝質(zhì)量和生產(chǎn)效率。測(cè)量則用于確保晶圓的質(zhì)量符合標(biāo)準(zhǔn)要求,為工藝優(yōu)化提供數(shù)據(jù)支持。
探針卡測(cè)試
目的:對(duì)晶圓上的每個(gè)芯片進(jìn)行電氣性能測(cè)試,篩選出合格的芯片進(jìn)行后續(xù)封裝。
方法:使用探針卡探測(cè)每一個(gè)裸芯片的電氣接觸點(diǎn),進(jìn)行功能性測(cè)試。探針卡上的探針與芯片上的焊點(diǎn)或者凸起直接接觸,導(dǎo)出芯片信號(hào),再配合相關(guān)測(cè)試儀器與軟件控制實(shí)現(xiàn)自動(dòng)化量測(cè)。
技術(shù)細(xì)節(jié):探針卡是晶圓功能驗(yàn)證測(cè)試的關(guān)鍵工具,通常由探針、電子元件、線材與印刷電路板(PCB)組成。探針卡上的探針細(xì)如毛發(fā),能夠精確地與晶粒上的接點(diǎn)(pad)接觸。
技術(shù)演變:隨著器件特征尺寸的減小和工藝要求的提高,探針卡測(cè)試技術(shù)也在不斷發(fā)展。例如,出現(xiàn)了飛針測(cè)試技術(shù),它能夠直接接觸探針卡連接器引腳,在PCB和陶瓷板之間進(jìn)行完整的連續(xù)性測(cè)試,無(wú)需用特定應(yīng)用的接口板或固定裝置。
故障芯片標(biāo)記方法
目的:在檢測(cè)出缺陷芯片后,將其標(biāo)記為不合格,以便在后續(xù)的晶圓切割和封裝過(guò)程中排除。
方法:早期是將測(cè)試出有故障的芯片打個(gè)墨水點(diǎn),以備封裝時(shí)將其剔除。現(xiàn)在多用測(cè)試的計(jì)算機(jī)將有故障的芯片在晶圓位圖上記錄下其位置。
技術(shù)演變:隨著自動(dòng)化和信息化技術(shù)的發(fā)展,故障芯片標(biāo)記方法也在不斷改進(jìn)。現(xiàn)在,計(jì)算機(jī)記錄的晶圓位圖可以更加精確地定位故障芯片,提高生產(chǎn)效率和產(chǎn)品質(zhì)量。
測(cè)試方法的演變對(duì)生產(chǎn)效率和產(chǎn)品質(zhì)量的影響:
生產(chǎn)效率:自動(dòng)化測(cè)試,隨著自動(dòng)化測(cè)試技術(shù)的發(fā)展,晶圓測(cè)試過(guò)程變得更加高效和可靠。自動(dòng)化測(cè)試能夠減少人工干預(yù),提高測(cè)試速度和準(zhǔn)確性,從而提高生產(chǎn)效率;智能化測(cè)試,隨著人工智能技術(shù)的發(fā)展,開(kāi)始探索如何利用機(jī)器學(xué)習(xí)算法來(lái)改進(jìn)測(cè)試過(guò)程。例如,使用AI來(lái)識(shí)別UI元素變化,自動(dòng)調(diào)整測(cè)試腳本;或者通過(guò)機(jī)器學(xué)習(xí)模型來(lái)預(yù)測(cè)哪些部分的代碼更有可能包含缺陷。智能化測(cè)試能夠進(jìn)一步提高測(cè)試效率和準(zhǔn)確性,降低測(cè)試成本。
產(chǎn)品質(zhì)量:早期缺陷檢測(cè),通過(guò)在線檢查和探針卡測(cè)試等技術(shù),能夠在晶圓制造過(guò)程中早期發(fā)現(xiàn)缺陷芯片,避免其進(jìn)入后續(xù)封裝和測(cè)試流程,從而提高產(chǎn)品質(zhì)量;精確故障定位,隨著故障芯片標(biāo)記方法的改進(jìn),能夠更精確地定位故障芯片,避免誤判和漏判,進(jìn)一步提高產(chǎn)品質(zhì)量。
晶圓測(cè)試階段的這些技術(shù)和方法不僅確保了芯片的質(zhì)量和性能,還通過(guò)提高生產(chǎn)效率和降低測(cè)試成本,為半導(dǎo)體制造行業(yè)帶來(lái)了顯著的經(jīng)濟(jì)效益。
-
集成電路
+關(guān)注
關(guān)注
5415文章
11864瀏覽量
366203 -
半導(dǎo)體
+關(guān)注
關(guān)注
335文章
28336瀏覽量
229975 -
晶圓
+關(guān)注
關(guān)注
52文章
5077瀏覽量
128993
原文標(biāo)題:晶圓制備及其測(cè)試
文章出處:【微信號(hào):bdtdsj,微信公眾號(hào):中科院半導(dǎo)體所】歡迎添加關(guān)注!文章轉(zhuǎn)載請(qǐng)注明出處。
發(fā)布評(píng)論請(qǐng)先 登錄
相關(guān)推薦
最全最詳盡的半導(dǎo)體制造技術(shù)資料,涵蓋晶圓工藝到后端封測(cè)
基于無(wú)線傳感器網(wǎng)絡(luò)助力半導(dǎo)體晶圓制造廠保持高效率運(yùn)行
晶圓制造工藝的流程是什么樣的?
晶圓針測(cè)制程介紹
什么是半導(dǎo)體晶圓?
簡(jiǎn)述晶圓制造工藝流程和原理
使用GaN制造半導(dǎo)體晶圓
半導(dǎo)體集成電路和晶圓有何關(guān)系?半導(dǎo)體晶圓制造工藝介紹
晶圓制造與芯片制造的區(qū)別
半導(dǎo)體晶圓制造工藝流程
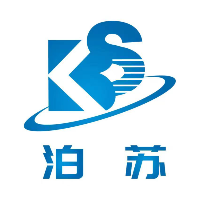
評(píng)論