為了獲得渦輪葉片熱障涂層隔熱效果和溫度分度分布規律,以帶有內部冷卻結構的某型燃機高壓渦輪動葉為基礎模型,通過氣熱耦合的方法對有/無熱障涂層保護下的高壓渦輪動葉的冷卻效果進行了數值計算,并通過改變熱障涂層的厚度研究了熱障涂層對葉片換熱的影響規律。研究發現:涂有熱障涂層后,葉片溫度下降明顯,越靠近前緣溫度降低幅度越大,壓力側與吸力側相比溫度降幅更大;厚度為0.05~0.2 mm 的熱障涂層可使葉片金屬表面平均溫度降低21~49 ℃;隨著涂層厚度等增加,葉片金屬內部的溫度分布將更加均勻。
在燃氣輪機的發展過程中,為了提高發動機的功率和熱效率,渦輪入口溫度也在不斷提高。渦輪葉片承受高溫燃氣沖擊,在渦輪進口溫度不斷提高的情況下,僅依靠空氣冷卻已經不能滿足要求。熱障涂層作為提高材料耐高溫和耐腐蝕性能的有效手段,得到了越來越多的應用。
熱障涂層一般采用等離子火焰噴涂或者電子束沉積等方法黏附在葉片表面,具有熔點高和抗熱沖擊的特性,可以提高渦輪葉片抗氧化和抗熱腐蝕的能力,降低葉片溫度,延長葉片的工作壽命。Alizadeh 等通過氣熱耦合數值模擬的方法,對0.2 mm 熱障涂層的隔熱效果進行研究,結果表明,葉片的最高溫度降低了19 K,平均溫度降低了34 K。Prapamonthon 等研究了湍流強度對熱障涂層葉片的冷卻效率的影響,結果表明,熱障涂層可使葉片表面的綜合冷卻效率提升16%~20%,葉片尾緣處提升8%。朱健等從熱力學角度對帶涂層葉片建立了一維穩態模型,從理論上分析和計算熱障涂層的隔熱效果。石黎等對帶有的熱障涂層的C3X 進行數值研究,0.3 mm 陶瓷層可使葉片表面溫度降低72.6 K,綜合冷卻效率增加6.5%,熱障涂層對葉片表面冷卻效率的分布規律無影響。周鴻儒等對帶有熱障涂層的渦輪葉片前緣進行數值研究,結果表明,熱障涂層不僅可降低金屬葉片的工作溫度和葉片內的溫度梯度,同時在一定程度上可抵抗進口熱斑的熱沖擊。楊曉光等通過給定葉片內、外表面的傳熱系數,計算了帶熱障涂層導向葉片的二維溫度場分布和應力情況。王利平等對帶有復合冷卻結構的渦輪導葉進行三維氣熱耦合分析,研究了涂層厚度及氣體輻射對涂層溫度場影響。劉建華等針對帶有多層結構熱障涂層的MarkⅡ型冷卻葉片,通過內部設定換熱系數、外部氣熱耦合的方法對熱障涂層的隔熱效果進行分析。
本文對帶熱障涂層葉片的換熱特性進行研究,數值分析了熱障涂層對葉片冷卻及表面溫度分布的影響規律,研究工作對后續分析葉片涂層失效原因、葉片冷卻改進設計有一定指導意義。
1、計算方法
1.1 計算模型
熱障涂層處在高溫燃氣與葉片合金基體表面之間,由金屬黏結層和隔熱陶瓷層構成,其基本結構如圖1 所示。在計算模型構建時,忽略熱障涂層結構中熱導率較高的黏結層,僅保留熱導率較低的隔熱陶瓷層。
圖1 渦輪葉片熱障涂層結構示意
圖2為涂有熱障涂層后的葉片模型,葉片內部含有多通道的回轉冷卻結構,前緣開設2 排氣膜冷卻孔,尾緣為中間劈縫結構,葉頂為H 型凹槽結構,熱障涂層僅噴涂在葉身和下緣板表面。由于葉片伸根以下溫度較低,且不作為研究重點,為減少計算網格數量,在設置計算模型時,將伸根以下部分忽略,構建出如圖3 所示的計算域模型。
圖2 帶涂層葉片模型
圖3 計算域模型
1.2 數值計算方法
渦輪冷卻動葉的內部幾何形狀較為復雜,很難采用結構化網格,而采用非結構化網格計算量又顯著增加,對此,本文采用多面體網格生成器,對葉片和氣體域進行網格劃分,網格模型如圖4所示。
圖4 網格模型
在計算模型中,熱障涂層的厚度極小,不足葉片壁厚的1/10,為此本文采用薄體網格生成器,將熱障涂層劃分成3 層多邊形棱柱網格,其中薄體網格的層數已經過無關性驗證,薄體網格的層數對葉片溫度場幾乎無影響。
流體域采用雷諾平均納維-斯托克斯(Reynoldsaveraged Navier-Stokes equations,RANS) 湍流模型中的Realizable K-Epsilon Two-Layer 模型,該模型為全y+壁面的網格處理提供更大的靈活性,既可以很好地處理精細網格(即低雷諾數類型或低y+網格),又能夠以最精確的方式處理中間網格(即1<y+<30),可有效地平衡穩定性、計算成本和精度。
1.3 邊界條件
燃氣進口設置為總壓滯止進口,冷卻空氣進口為質量流量進口,出口設置為靜壓出口。燃氣通道內的涂層表面設定為流-固耦合面,涂層與葉片金屬表面設置固體交界,通道兩側設置為旋轉周期。冷氣與燃氣均為理想氣體,氣體熱容和熱導率采用薩瑟蘭公式設定。相應的計算邊界條件為:燃氣通道主流進口總壓為2.5 MPa,帶徑向溫度梯度的進口溫度分布如圖5 所示,葉片內冷通道冷氣進口流量為45 g/s,總溫為540 ℃,出口壓力為0.9 MPa。葉片材料為鎳基單晶高溫合金,材料的熱導率隨溫度變化。就現有材料而言,熱障涂層一般采用穩定的氧化釔氧化鋯(YSZ)材料或氧化鋯(ZrO2),其熱導率隨溫度變化很小,因此在計算中熱導率設為1.03 W/(m·K)。
圖5 燃氣進口溫度分布
2 計算結果分析
2.1 葉片表面溫度
圖6和圖7分別為無涂層葉片表面溫度分布和不同涂層厚度下葉片金屬表面溫度分布。可以看出,隨著涂層厚度的不斷增加,葉片金屬表面溫度逐漸降低,不同厚度下葉片金屬表面的溫度分布規律基本一致,壓力面中部溫度較低,葉頂溫度較高。葉頂通常是整個葉片較難冷卻的位置,葉頂的凹槽肋很難被冷氣直接冷卻。在計算模型中,涂層只覆蓋在葉身表面,葉頂無涂層覆蓋,對于來自葉頂燃氣側的熱量沒有阻隔作用,因此葉頂處的高溫區一直存在。
圖6 無涂層葉片表面溫度分布
圖7 不同涂層厚度下葉片金屬表面溫度分布
圖8 為葉片金屬表面平均溫度隨厚度的變化曲線。可以看到,葉片金屬表面平均溫度隨涂層厚度的增加而降低。這是由于熱障涂層導熱系數低,在高溫燃氣與金屬葉片增加了導熱熱阻,有效降低了葉片金屬表面的溫度。涂層厚度為0.05 mm 時,葉身平均溫度降低21 ℃,而后隨著熱障涂層厚度的增加,葉片表面的溫度不斷降低;當涂層厚度為0.20 mm 時,葉身平均溫度降低49 ℃。這與張志強等通過冷效試驗測量的隔熱效果基本一致。
圖8 葉片表面平均溫度隨涂層厚度的變化
圖9為葉片截面表面溫度沿軸向弦長的變化曲線。從圖9 中可以看出,在不同熱障涂層厚度下,溫度沿軸向弦長變化趨勢基本一致,吸力面溫度明顯高于壓力面溫度。在軸向弦長方向上,壓力面和吸力面溫度先降低后升高,尾緣區域有一定波動,這是由于尾緣中間劈縫噴冷的結構形式造成的。同時涂有熱障涂層的葉片溫度明顯下降,且吸力面溫度下降的幅度明顯大于壓力面。從前緣到尾緣溫降逐漸減小,越靠近葉片前緣處,溫度降低幅度越大。
圖9 葉片中截面表面溫度變化
葉片金屬溫度的均勻性影響著葉片的熱應力水平,因此本文采用溫度的體均勻度指數來衡量固體葉片的溫度均勻程度。溫度的體均勻度指數:
式中:c 為每個單元體積,T-為溫度T 的體平均值, Tc為網格單元中的溫度值, Vc為網格單元體積。如果體溫度場均勻分布,則體均勻度指數為1。從圖10 中可以看出,噴涂熱障涂層后,葉片溫度均勻度明顯提高,當涂層厚度為0.2 mm 時,葉片的溫度均勻度指數提高0.4%。
2.2 涂層表面溫度
涂層表面溫度變化情況如圖11 所示。從圖11可以看出,隨著涂層厚度的增加,熱障涂層的表面溫度不斷升高,這與葉片表面平均溫度變化趨勢正好相反。由于涂層厚度方向熱阻增大,涂層表面與葉片表面的溫差逐漸增大,表面累積的熱量更難向金屬葉片擴散。當涂層厚度為0.20 mm時,涂層內外的溫差達到86 ℃。
2.3 葉片截面溫度
圖12為涂有熱障涂層和未涂熱障涂層葉片的前緣與尾緣截面溫度分布。表面涂有熱障涂層后,葉片的截面溫度明顯降低,溫度梯度有所緩解。這是因為涂有熱障涂層后,涂層內熱流密度減小,同時由于熱障涂層材料具有較低的低導熱率,在熱障涂層固體內部溫度變化非常劇烈。
圖12 前緣與尾緣固體截面的溫度分布
3 結論
本文建立了帶涂層高壓渦輪動葉的冷卻效果計算模型,通過對葉片的氣熱耦合模擬,研究了熱障涂層的隔熱性能,主要結論如下: 1)隨著熱障涂層厚度的增加,葉片表面溫度逐漸降低。厚度0.05~0.2 mm 的熱障涂層可使葉片金屬表面平均溫度降低21~49 ℃。 2)敷設熱障涂層后,葉片吸力側溫降明顯高于壓力側,且從前緣到尾緣隔熱效果逐漸變差,熱障涂層對尾緣溫度影響最小。 3)隨著涂層厚度的增加,涂層表面溫度增加,葉片表面溫度減小,兩者溫差逐漸加大,當涂層厚度為0.2 mm 時,涂層內外的溫差達到86 ℃。
4)隨著涂層厚度的增加,葉片內的溫度場變得更加均勻,溫度梯度也有所緩解,而在熱障涂層厚度方向上,溫度的變化則非常劇烈。
-
渦輪
+關注
關注
0文章
39瀏覽量
11927 -
燃氣輪機
+關注
關注
1文章
37瀏覽量
11402
原文標題:703所:某型燃氣輪機熱障涂層對渦輪動葉冷卻效果的影響機制研究
文章出處:【微信號:AMTBBS,微信公眾號:世界先進制造技術論壇】歡迎添加關注!文章轉載請注明出處。
發布評論請先 登錄
相關推薦
2025(第七屆)民用航空發動機與燃氣輪機行業大會暨渦輪技術展覽會震撼登陸蘇州
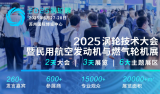
我國重型燃氣輪機小型化取得新突破
蔡司掃描儀3D抄數建模設備助力渦輪機葉片檢測
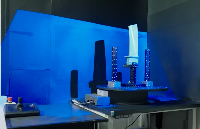
卡特彼勒旗下索拉透平亮相2024進博會
如何實現風力渦輪機等可再生能源設備的性能監測?
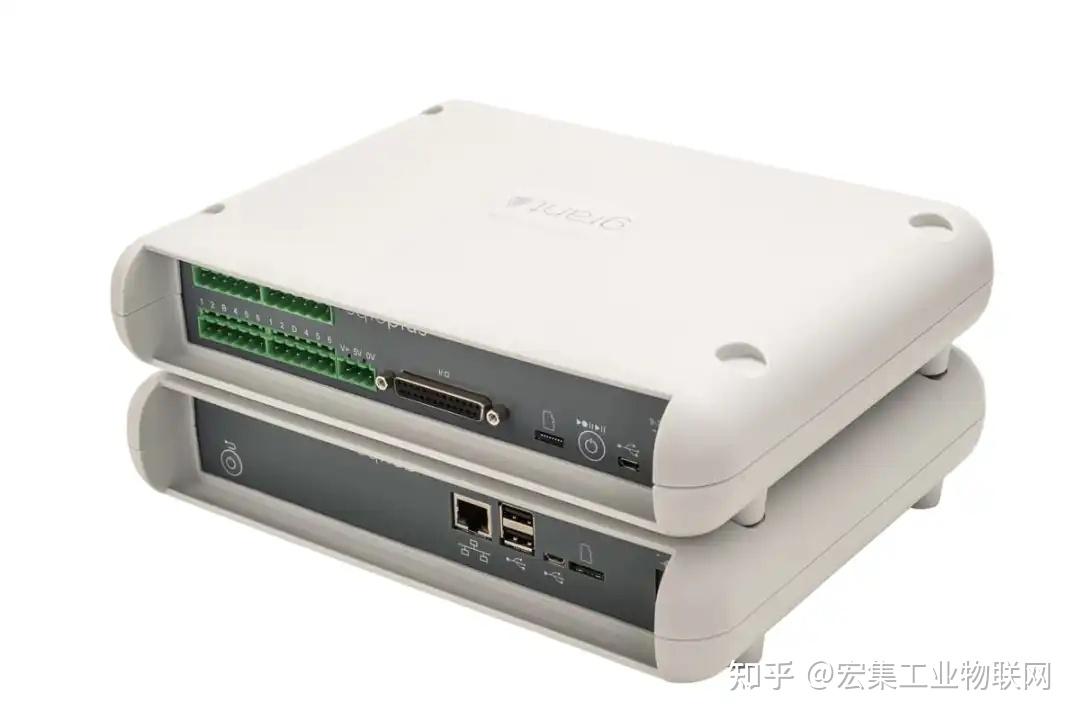
重磅定檔!2025渦輪技術大會暨民用航空發動機與燃氣輪機展將于2025年5月舉辦
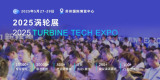
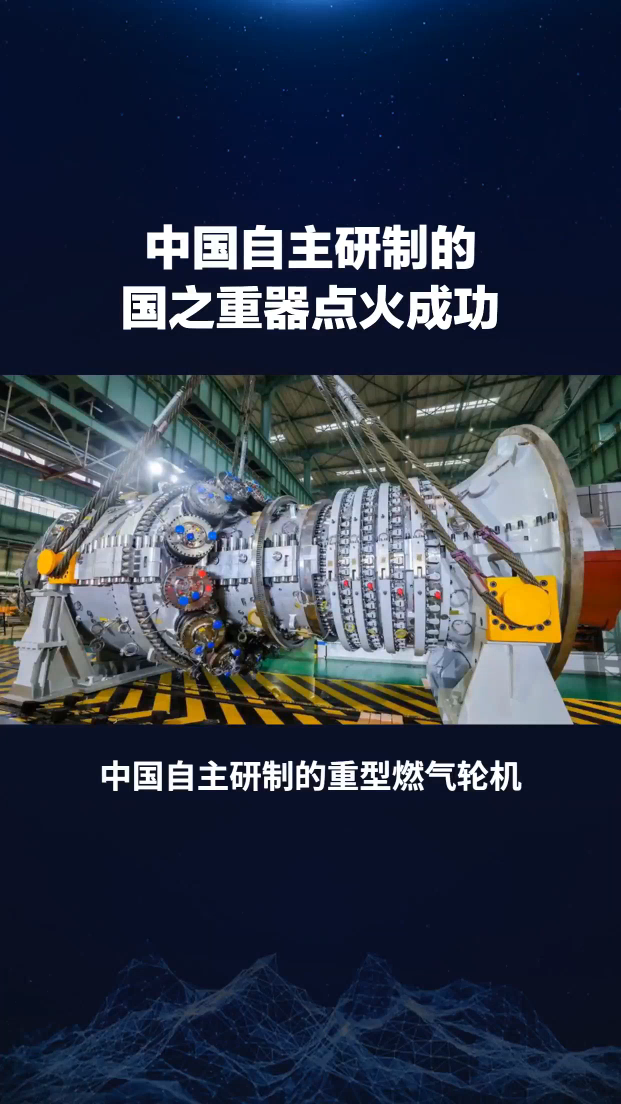
必優傳感2024渦輪技術博覽會精彩回顧
CASAIM與三菱重工東方燃氣輪機達成合作,攜手并進電子化、數字化、智能化檢測時代
Dymax戴馬斯將關注的核心市場拓展至能源領域
影像儀掃描儀顯微鏡檢測航空發動機和燃氣輪機
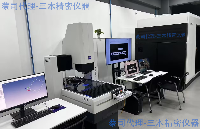
評論