碲鋅鎘(CZT)單晶材料作為碲鎘汞(MCT)紅外焦平面探測器的首選襯底材料,其表面質量的優劣將直接影響碲鎘汞薄膜材料的晶體質量以及成品率,故生產出外延級別的碲鋅鎘襯底表面是極其重要的。目前,碲鋅鎘單晶片的主要表面加工處理技術包含機械研磨、機械拋光、化學機械拋光、化學拋光以及表面清洗。其中,機械研磨、機械拋光以及化學機械拋光工藝都會存在磨料殘留、磨料嵌入、表面劃痕較多、粗糙度較高等一系列問題,要解決這些問題需要對相應的表面處理技術進行了解和掌握,包括表面處理技術的基本原理以及影響因素。
據麥姆斯咨詢報道,近期,昆明物理研究所的科研團隊在《紅外技術》期刊上發表了以“碲鋅鎘襯底表面處理研究”為主題的文章。該文章第一作者為江先燕,通訊作者為叢樹仁高級工程師,主要從事紅外材料與器件方面的研究工作。
本文主要從碲鋅鎘表面處理工藝及表面位錯缺陷揭示兩個方面對碲鋅鎘襯底的表面處理研究進行了詳細介紹。
表面處理工藝
碲鋅鎘單晶作為生長外延碲鎘汞薄膜材料的首選襯底材料,要求其表面不能存在機械損傷及缺陷密度大于10? cm?2的微觀缺陷,如線缺陷、體缺陷等。襯底表面的機械損傷可通過后期的表面處理工藝進行去除[18],而微觀缺陷只能通過提高原材料的純度以及合理調控晶體的生長過程方能得到有效改善。經垂直梯度凝固法或布里奇曼法生長出的低缺陷密度的碲鋅鎘體晶會先被切割成具有固定方向(如(111)方向)和厚度的碲鋅鎘晶片,然后再經過一系列的表面處理工藝才能用于碲鎘汞薄膜的生長。通常情況下,碲鋅鎘晶片會經歷機械研磨、機械拋光、機械化學拋光及化學拋光等表面處理工藝,通過這些工藝處理后的晶片才能達到外延級水平,因此本部分主要詳細介紹上述4種表面處理工藝。
機械研磨
機械研磨工藝的研磨機理為:加工工件與研磨盤上的磨料或研磨劑接觸時,工件表面因受到形狀不規則磨料的擠壓而產生破裂或裂紋,在加工工件與研磨盤的相互運動下,這些破裂的碎塊會隨著不規則磨料的滾動而被帶離晶片表面,如此反復,從而達到減薄晶片厚度及獲得低損傷表面的加工目的,機械研磨裝置及磨削原理示意圖如圖1所示。
圖1 機械研磨裝置及研磨機理示意圖
碲鋅鎘體晶切割成一定厚度的晶片后首先經歷的表面處理工藝是機械研磨工藝。機械研磨的主要目的是去除機械切割對晶片表面造成的損傷層,從而獲得一個較低損傷的晶片表面。表面處理工藝中,機械研磨還可細分為機械粗磨和機械細磨,兩者的主要區別在于所使用的磨料粒徑不一樣,粗磨的磨料粒徑大于細磨的磨料粒徑。機械細磨的主要目的是去除機械粗磨產生的損傷層,同時減少拋光時間,提高工藝效率。研究報道,機械研磨產生的損傷層厚度通常是磨料粒徑的3倍左右。
影響機械研磨工藝對加工工件研磨效果的因素有磨料種類、磨料粒徑及形狀、研磨盤類型、磨料與溶劑的配比、磨料滴速、研磨盤轉速、工件夾具轉速以及施加在加工工件上的壓力等。磨料種類一般根據加工工件的物理及化學性質(如強度、硬度、化學成分等)進行合理選擇。常用于機械磨拋的磨拋料有MgO、Al?O?、SiC及金剛石等,其中,為了避免在碲鋅鎘襯底上引入其他金屬雜質,MgO和Al?O?這兩種研磨劑很少在碲鋅鎘表面處理工藝上進行使用,使用最多的是SiC和金剛石兩類磨料。
磨料的形狀可分為規則(如球狀、棒狀、長方體等)和不規則(如多面體形狀)兩類,如圖2所示。通常情況下,磨料形狀越不規則,材料去除速率越快,同時造成的表面損傷也大,反之,磨料越規則,去除速率越慢,但造成的表面損傷也越小。
圖2 不規則磨料及規則磨料的掃描電鏡圖
毛曉辰等人研究了這3種不同形狀磨料對碲鋅鎘襯底機械研磨的影響。當磨粒形狀為板片狀時,材料的去除模型將不再遵從李巖等人提出的“不規則磨料研磨去除模型”,即三體磨粒去除模型,如圖3(a)所示,而是會發生變化。基于此,毛曉辰等人提出了如下的去除模型,即:當磨粒為板片狀時,磨粒以一定的傾斜角度平躺于磨盤表面,如圖3(b)所示,當加工工件(晶片)與磨盤發生相互運動時,磨粒被短暫的固定在磨盤表面,形成二體磨粒,板片狀磨粒便以其片狀邊緣對加工工件表面進行磨削,最終實現去除材料的目的。
圖3 不規則磨料及板片狀磨料去除機理示意圖
常見的研磨盤類型可簡單分為開槽和不開槽兩類,如圖4所示,開槽和不開槽研磨盤對晶片研磨效果的影響如表1所示。
圖4 磨盤示意圖
表1 開槽和不開槽研磨盤對晶片研磨效果的影響
機械拋光
機械拋光工藝的拋光機理為:加工工件與柔性拋光墊上的拋光粉或拋光顆粒接觸后,工件表面將受到形狀不規則的拋光顆粒的擠壓而產生破裂或裂紋,在加工工件與拋光盤的相互運動下,這些破裂的碎塊會隨著不規則拋光顆粒的滾動而被帶離晶片表面,反復如此,從而達到降低加工工件表面粗糙度和獲得光亮、平整表面的目的。拋光粉是一種形狀不規則且粒徑很小的微納米級顆粒,故而對加工工件造成的表面損傷較小且加工后的工件表面像鏡面一樣光亮。拋光墊的柔韌性削弱了拋光顆粒與加工工件表面的相互磨削作用,從而進一步降低了拋光顆粒對工件表面的損傷。機械拋光裝置及拋光原理示意圖如圖5所示。
圖5 機械拋光裝置及拋光原理示意圖
機械拋光的主要目的是去除機械研磨工藝對晶片表面造成的損傷層,同時降低晶片表面粗糙度和減少表面劃痕,獲得光亮、平整的表面。影響機械拋光工藝對加工工件表面拋光效果的因素有拋光粉種類或者拋光液種類、拋光粉粒徑大小及形狀、拋光墊種類、拋光盤轉速、工件夾具轉速、施加在工件上的壓力、拋光液滴速以及拋光時間等。圖6所示為碲鋅鎘晶片經不同廠家生產的同種拋光液機械拋光后的表面形貌圖,如圖所示,在相同的拋光條件下,不同廠家生產的拋光液的拋光效果差別較大。因此,機械拋光工藝中對拋光液的合理選擇是極其重要的。
圖6 不同廠家生產的同種拋光液的機械拋光表面
拋光粉的粒徑大小和形狀主要影響加工工件的表面質量和材料去除速率,通常,粒徑越大以及形狀越不規則,則材料的去除速率越快,表面質量也越差,如表面粗糙度大、劃痕多等;反之,則去除速率慢,表面質量好。
拋光墊具有貯存拋光液及去除拋光過程產生的殘留雜質等作用,拋光墊的種類(或材質)也是影響工件拋光效果的主要因素之一。圖7為目前一些常見拋光墊的表面紋理及根據仿生學理論研究設計的拋光墊表面紋理圖,主要包括放射狀紋理、柵格狀紋理、同心圓狀紋理、放射同心圓復合狀紋理、螺旋狀紋理及葵花籽狀紋理。
圖7 拋光墊表面紋理圖
化學機械拋光
化學機械拋光工藝的拋光機理為:加工工件表面與拋光墊上的拋光液接觸后,將同時受到來自拋光液中的不規則拋光顆粒的擠壓作用和強氧化劑的腐蝕作用,即工件表面同時受到機械作用和化學作用。化學機械拋光的主要目的包括去除工件表面損傷層、降低表面粗糙度、消除或減少表面劃痕以及工件表面平坦化等。
影響化學機械拋光工藝對加工工件表面拋光效果的因素有機械作用和化學作用的協同情況、拋光粉種類、拋光粉粒徑大小及形狀、氧化劑種類及濃度、拋光墊種類、拋光盤轉速、工件夾具轉速、施加在工件上的壓力、拋光液滴速以及拋光時間等。
拋光粉的粒徑大小及形狀、拋光墊的種類(或材質)、拋光墊的使用時長、拋光盤轉速、工件夾具轉速、施加在工件上的壓力大小以及拋光時間等因素對工件拋光效果的影響原理與機械拋光工藝中所述影響原理類似。
化學拋光
化學拋光工藝的拋光機理為:當加工工件與拋光墊上的化拋液接觸后,化拋液中的氧化劑將對工件表面進行腐蝕,在拋光墊與工件表面的相互運動作用下,工件表面上的損傷層以及淺劃痕等都會被去除,得到光亮、平整且無任何劃痕及損傷的外延級襯底表面。化學拋光工藝中使用的拋光液只包含氧化劑和溶劑,沒有磨料顆粒或拋光顆粒。同時,對工件進行化學拋光時,沒有對工件施加額外的壓力,只有拋光夾具的自身重力。因此,化學拋光工藝中幾乎不涉及到機械作用,只有純化學腐蝕作用。化學拋光工藝的裝置及拋光原理如圖8所示。
圖8 化學拋光裝置及拋光原理示意圖
化學拋光的主要目的是去除化學機械拋光或機械拋光工藝對晶片表面造成的損傷層,并同時為生長碲鎘汞薄膜提供新鮮、潔凈、無損的外延級表面。影響化學拋光工藝對加工工件表面拋光效果的因素有氧化劑種類及濃度、拋光墊種類、拋光盤轉速、拋光夾具自重、化拋液滴速以及拋光時間等。
表面位錯揭示
與硅等幾乎無缺陷的單晶材料相比,碲鋅鎘單晶材料具有較高的位錯密度(10?~10?/ cm?2)。目前,觀察位錯的主要手段是化學腐蝕法,雖然透射電子顯微鏡法(TEM)也能對材料的位錯進行檢測,但因其具有設備成本太高、制樣非常困難、視場太小等原因而無法作為常規的位錯檢測手段。化學腐蝕法因具有成本低、制樣簡單、操作簡單且所觀察的視場較大等優勢而成為了目前主要的表面位錯檢測手段。
碲鎘汞薄膜主要是通過在碲鋅鎘襯底的(111)面和(211)面上外延得到,因此,要求碲鋅鎘襯底表面不能存在損傷及大量的微觀缺陷。襯底表面的損傷主要來自于表面處理工藝,而微觀缺陷如沉淀物、位錯、空位等則是在晶體生長過程中產生的。事實上,表面損傷對應的是晶格的周期性被破壞,即晶體表面形成大量的位錯。所以,對于外延襯底而言,不管是損傷還是微觀缺陷,只要超過一定的數量都會直接影響碲鎘汞外延薄膜的質量,故而需要對碲鋅鎘襯底表面的缺陷(包括損傷和微觀缺陷)進行檢測,從而篩選出優質的外延級襯底。如上所述,化學腐蝕法是目前最常用的位錯檢測手段,因此這部分主要介紹用于揭示碲鋅鎘表面位錯缺陷的腐蝕液。
(111)A面位錯揭示腐蝕液
1979年,K. Nakagawa等人報道了一種可用來揭示碲化鎘(111)A面位錯缺陷的化學腐蝕液,其組分為20 mL H?O:20 mL H?O?:30 mL HF。
(111)和(211)B面位錯揭示腐蝕液
1995年,W. J. Everson等人報道了一種可用于揭示碲鋅鎘(111)和(211)B面位錯缺陷的化學腐蝕液,其組分為6 mL HF: 24 mL HNO?:150 mL C?H?O?(乳酸),即體積比為125。由于這種化學腐蝕液是W.J.Everson首次提出并驗證其有效性的,所以作者將這種腐蝕液命名為“Everson腐蝕液”。
其他晶面位錯揭示腐蝕液
1962年,M. Inoue等人報道了一種可揭示碲化鎘(CdTe)不同晶面上位錯缺陷的EAg腐蝕液,EAg腐蝕液的組成為10 mL HNO?: 20 mL H?O : 4 g K?Cr?O? :x g AgNO?
總結與展望
本文主要從碲鋅鎘表面處理工藝及表面位錯揭示兩個方面對碲鋅鎘襯底的表面處理工藝研究進行了詳細介紹。表面處理工藝主要包括機械研磨、機械拋光、化學機械拋光以及化學拋光,研磨或拋光工藝中的參數選擇直接影響最終的襯底表面質量。碲鋅鎘襯底的表面位錯缺陷主要通過Everson或Nakagawa兩種化學腐蝕液進行揭示,Everson腐蝕液主要揭示碲鋅鎘(111)B面的位錯缺陷,Nakagawa腐蝕液主要揭示(111)A面的位錯缺陷。
另外,隨著碲鎘汞紅外焦平面探測器技術的發展,碲鋅鎘襯底的尺寸逐漸增大,這意味著獲得外延級碲鋅鎘襯底表面將會更加困難,這對晶片表面平整度、晶片面型控制及表面清洗等都提出了更高的技術要求。因此,如何在現有的基礎上探索出適用于大尺寸碲鋅鎘襯底的表面處理技術是至關重要的,這也是接下來亟待解決的技術問題和努力的方向。
審核編輯:劉清
-
TEM
+關注
關注
0文章
88瀏覽量
10419 -
拋光機
+關注
關注
0文章
33瀏覽量
6875
原文標題:碲鋅鎘襯底表面處理研究
文章出處:【微信號:MEMSensor,微信公眾號:MEMS】歡迎添加關注!文章轉載請注明出處。
發布評論請先 登錄
相關推薦
激光退火后,碳化硅襯底TTV變化管控
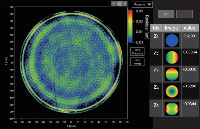
碳化硅襯底修邊處理后,碳化硅襯底TTV變化管控
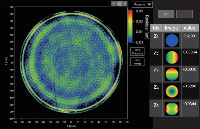
五種常見的PCB表面處理技術
碲化鉍和碲鋅鎘別傻傻分不清
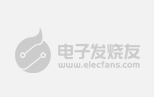
揭秘PCB板的八種神秘表面處理工藝
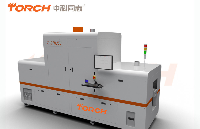
堿錳電池的銅針表面怎么處理
基于VLPE技術的碲鎘汞p-on-n雙層異質結材料與器件研究進展
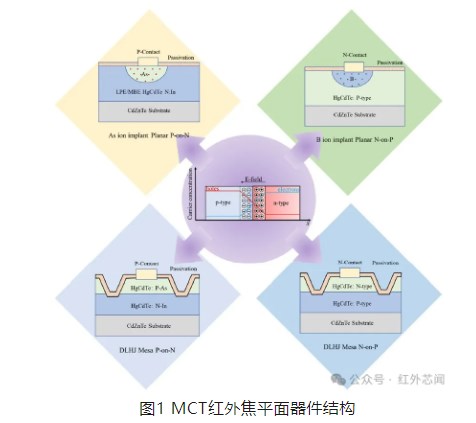
半導體襯底材料的選擇
表面處理方法HASL是什么
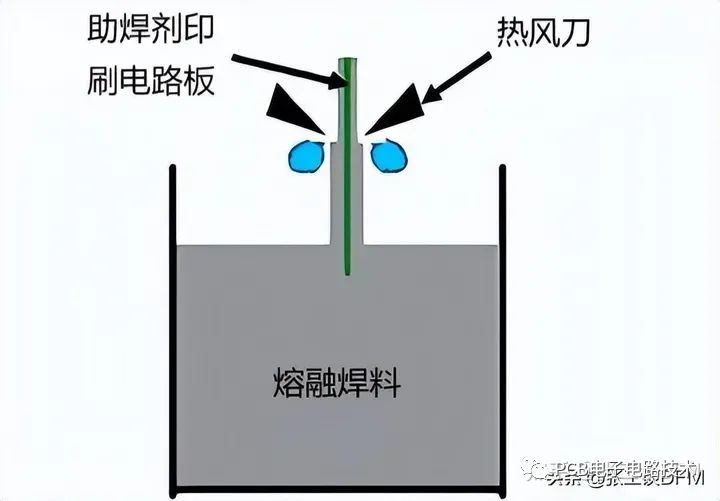
評論