數字化工廠由設備、機器人、AGV、網絡、信息數據等構成,集成了產品制造過程和工廠模型的數據庫,以提高產品的質量和生產過程所涉及的質量和動態性能。通過借助計算機,對整個生產過程進行數據采集,并可進一步擴展到整個產品制造過程的全生命周期,將打通產品設計和產品制造之間的橋梁,實現信息的集成。而生產車間是組成工廠最重要的組成部分,實現了生產車間的數字化,基本上完成了數字化工廠最核心的部分。在數字化系統建設中以數據的可視化管理和應用為核心,而非簡單注重完全的自動化程度。利用PLM系統實現主數據流和工業網絡、智能裝備、智能倉庫、智能系統等方面系統集成,實現數據流貫通與共享。
1 數字化車間硬件平臺搭建
1.1 智能化生產
智能化在引入數控機床、機器人等生產設備并實現生產自動化的基礎上,再以ERP、MES 等管理軟件作為中樞管理系統,以視覺相機、RFID標簽、掃碼器、條碼、傳感器等為組件,以NC數控系統或PLC為控制單元,以現場總線 PROFIBUS、工業以太網PROFINET、MODUBUS等通信技術為傳輸網絡。能夠借助完善的系統獲取狀態信息、傳遞控制指令,以此實現科學決策、智能設計、合理排產,監控設備狀態,提升設備使用率,指導生產運行,讓自動化生產智能設備高效運轉。
1.1.1 智能硬件
智能化生產制造單元是將一組能力相近的加工設備和輔助設備進行模塊化、集成化、一體化的聚合,使其具備多品種少批量產品的生產輸出能力。打造智能制造單元是開啟智能化道路行之有效的切入點。為各車間配置智能制造單元,“智造單元”是一種模塊化的小型數字化工廠實踐,整個單元由自動化模塊、信息化模塊和智能化模塊三部分組成,以“最小的數字化工廠”實現在多品種小批量的生產智能化。在加工領域,注重從單一功能型設備向多功能型設備過渡;在裝配領域,突破人工操作的枷鎖,逐步由人工操作向人機協作、自動化作業轉變;不斷發掘高精尖設備,致力于質量檢測、SPC工站建設;將傳統、簡易的人工搬運等,采用機器人配合視覺定位技術全部實現自動化搬運。
1.1.2 智能設備互聯
智能化生產車間以信息化作為根基,通過將生成車間的不同設備與通訊網絡連接,收集設備的狀態數據和質量數據,并作為數據采集和分析的基礎。對不同生成設備,采取不同的數據采集方式:對存在數據接口的設備,如加工中心、磨床、PLC控制器、機器人、儀器儀表等,通過Profibus或Profinet網絡將設備數據傳輸到網關;對于沒有數據接口的設備,通過外接傳感器完成設備狀態采集,提升通訊能力,可采取有線或無線兩種方式進行,數據傳輸到網絡后,通過邊緣計算方式完成數據就地分析和存儲,對于數據分析結果匯總,并采用有線或無線的方式,存儲到云服務器進行數據顯示和后續數據分析工作。設備的聯網接入需完成三項重要的工作:硬件接口的連接、軟件數據接口互通、接口規范定義。
1.1.3 智能設備數據采集
完整的制造設備應具備完善的檔案信息,包括產品編號、產品描述、產品狀態、產品時間戳等信息。按照已定義的通信接口,與其他設備、裝置以及執行層實現設備和數據的互聯互通。對收集完成的數據進行分析,篩選出合格數據,對于不合格數據采用自動處理和人工處理兩種模式完成,最終保證產量質量狀態的穩定,并可滿足產品的質量追溯。
1.1.4 智能制造執行系統
建立MES制造執行系統,運用生產調度管理、工藝執行與管理、過程控制管理、排程管理、質量管理、設備管理等模塊,可時刻管理和展示生產制造全流程。通過開發數字化生產制造執行平臺,打通計劃、生產、物流、設備間的數據流,構成計劃、控制、反饋、調整的完整系統,通過規范的定義接口實現計劃、命令的傳遞和實際生產的無縫銜接,使生產計劃、控制命令、信息數據在整個 MES 系統、過程控制系統、自動化體系中透明、及時、順暢地交互傳遞,最終實現生產全過程數字化,打造數字化生產車間。
1.2 智能化物流倉儲
物流倉儲是制造業中極為重要的一環,通過應用智能物流倉儲系統可快速完成產品原材料、產品配套件、成品件之間快速流轉和輸送工作,通過采用堆垛機輸送方式和立體倉庫存儲方式提升倉庫貨位周轉效率,降低倉庫轉運過程造成的人工成本,提升轉運效率,實現倉庫儲流數字化管控和智能化運輸。
建設智能物流倉儲系統,完善系統組成架構:設備層、操作層、企業層。設備層建設立體倉庫、智能叉車、碼垛機器人、提升機等倉儲設備,建設AGV、智能托盤、物流機器人等物流設備、RFID、機器視覺、智能攝像頭等識別設備;操作層增加 WMS、WCS、TMS 等運維軟件;企業層則對接ERP、CRM、SCM等管理軟件的采購、計劃、庫存、發貨等模塊,融入總系統的閉環中。
2 數字化車間平臺搭建
工藝是將研發設計的產品賦予靈魂的重要一環,推進數字化技術應用并覆蓋于產品的設計、工藝、制造全生命周期,是實現智能制造的關鍵一點。通過工藝數字化信息平臺建設,將打通設計、工藝、制造之間數據流,實現上下游高效協同,通過數字化工藝的深化應用,工藝一致性將實現100%,20%的問題將在規劃早期被驗證發現,產品的生產準備周期將縮短20-30%。
2.1 數字化工藝平臺建設初期
完成基礎功能模塊開發及應用。產品準備管理按照APQP實現管控,系統化管控項目進度及交付物;BOM及工藝管理,實現數據及時、準確,提高工藝一致性及標準化;變更管理實現正向與逆向的閉環管理,提升變更執行質量;實現工藝資源管控,實現知識積累、共享和重用。
2.2 工藝數字化平臺建設中期
實現工藝創新性管理:通過工藝仿真技術,實現三維數字化工藝規劃及驗證,對工藝合理性進行虛擬仿真及評估;實現三維工藝下廠,提高工藝可視性;通過產線仿真技術,對生產線的裝備、物流、工藝、節拍、人員、生產過程等進行仿真、優化及管理。
2.3 工藝數字化平臺建設后期
實現工藝數字化技術深度應用:通過數字映射技術,實現實際生產與虛擬生產聯動,可以及時修正生產中的偏差及問題,實現更科學更智能的生產。加強數字化技術團隊建設,成立專門的項目團隊負責技術研究及系統建設,推進工藝數字化提升工作開展。
建立數字化標準體系及業務流程,根據數據流、業務流傳遞特點及上下游關系制定完善的數字化流程,實現管理創新促進技術創新、技術創新推進管理創新。加強數字化基礎建設及設計制造輔助工具開發。從軟件基礎環境、數據庫支撐平臺、網絡信息環境、信息安全體系等基礎方面進行投入和建設。
2.4 仿真系統應用
結合產線數模、物流仿真等,實現產線仿真,對生產線的裝備、物流、工藝、節拍、人員、生產過程等進行仿真、驗證、優化及管理。通過數字映射技術,實現實際生產與虛擬生產聯動,當生產線出現問題時能夠實時反饋至虛擬系統,通過虛擬系統驗證后更改虛擬參數,可實現生產線同步更改,這樣就可以及時修正生產中的偏差及問題,實現更科學更智能的生產。
通過與MES、ERP、工藝裝備、工藝資源等車間系統深度集成,實現數字化車間技術研究與應用,為實現智能化車間、產線大數據分析等奠定基礎。
3結論
在數字化車間建設與實施過程中,關鍵點是引用PLM系統實現主數據流貫通和系統集成,數據流貫通保證了數據的準確、及時、共享,系統集成實現了數據的互聯互通。并在此基礎上進一步實現數據可視化、透明化。頂層規劃很重要,在項目開始階段,完成頂層設計方案,確保項目實施過程可控性和可預知性。智能工廠建造過程通過數字化雙胞胎,實現全集成可視化工廠。實現軟件和硬件的智能互聯,通過設置標準網絡接口實現機床間互聯互通。
審核編輯 黃宇
-
數字化
+關注
關注
8文章
8708瀏覽量
61726
發布評論請先 登錄
相關推薦
數字化生產車間物聯網平臺是什么
自動化生產車間異常告警運維管理系統解決方案
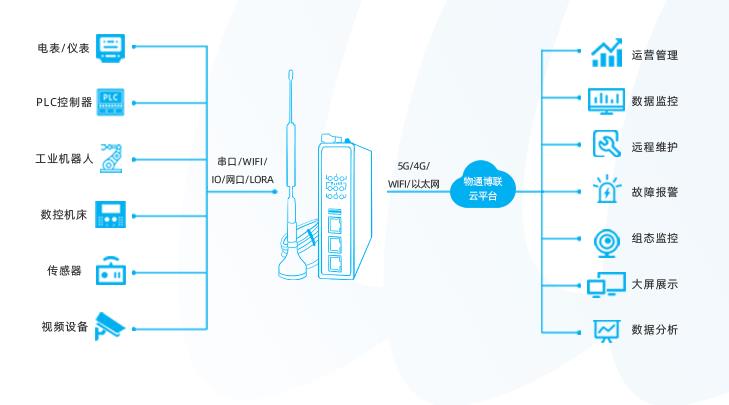
數字化生產管理物聯網系統解決方案
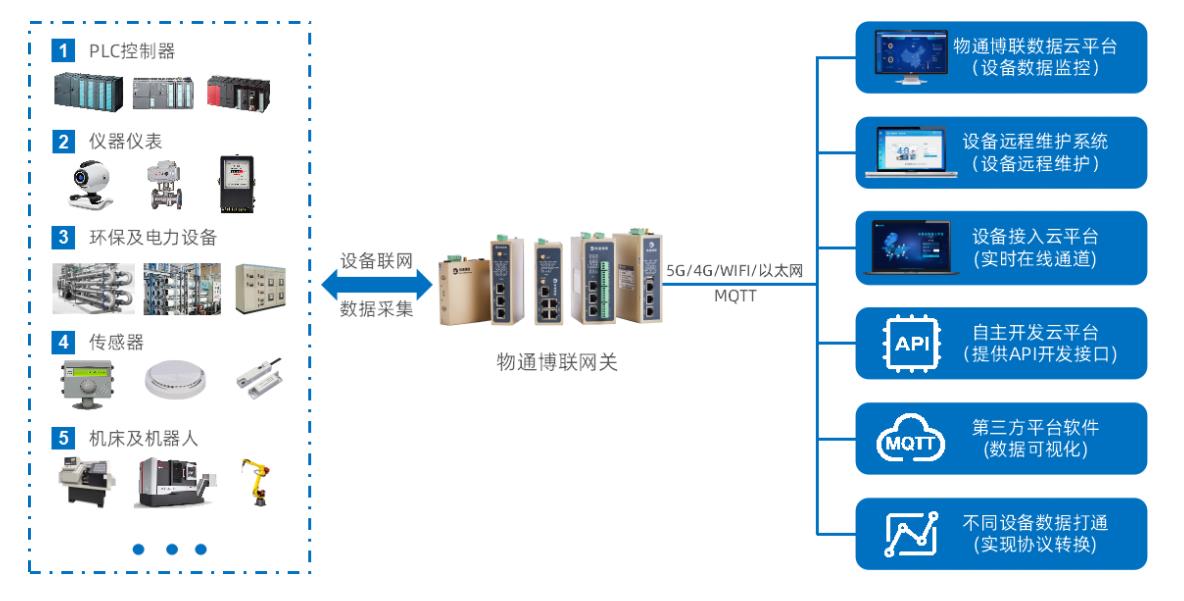
萬界星空科技MES打造數字化生產車間
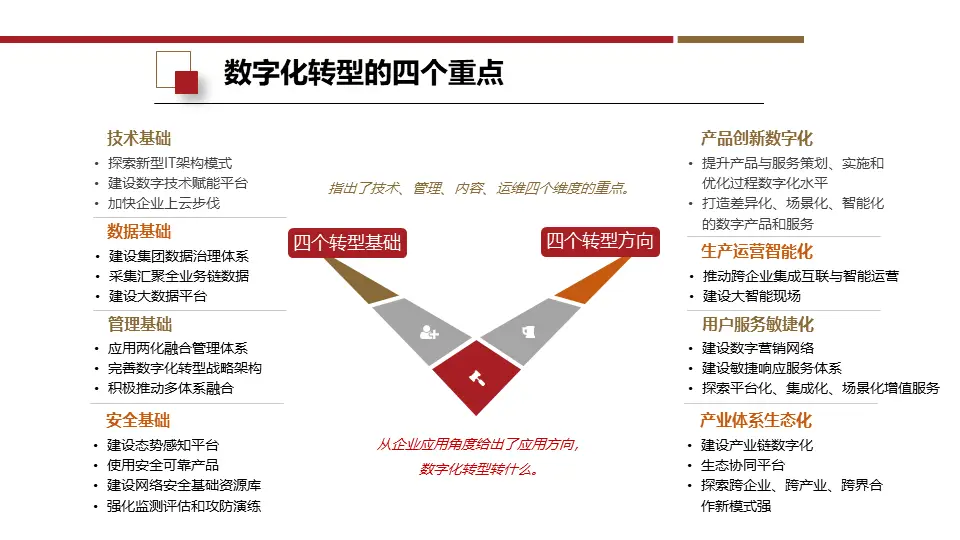
PLC智能網關如何助力車間實現數字化轉型?
工業網關的數字化車間機械手和工業生產設備遠程監控解決方案應用
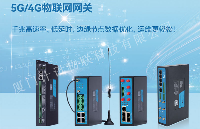
評論