伺服電機與定量泵組成的液壓動力源具有良好的節(jié)能效果,該系統(tǒng)由于使用伺服電機,所以具有響應速度快,壓力與流量控制精度高等特點。伺服電機轉速隨系統(tǒng)的流量需求而變化,無節(jié)流損失。在壓制保壓、冷卻時間長的產品時,該系統(tǒng)具有非常顯著的節(jié)能效果。
目前,大型高端液壓機對節(jié)能和精度的要求越來越高,但傳統(tǒng)的伺服電機泵控系統(tǒng)受電機容量和泵排量的限制,難以實現高壓大流量的設計要求。
本研究提出了利用高壓主泵和低壓副泵組合的方式,解決大型液壓機上應用伺服電機控制時對高壓大流量輸出的設計要求。
1、伺服電機泵控系統(tǒng)節(jié)能分析
1.1伺服電機泵控系統(tǒng)應用現狀
目前,在傳統(tǒng)中低端壓機行業(yè)還在普遍使用閥控液壓系統(tǒng),其動力源為普通定頻電機和定量泵。其主要缺點為加工精度的可控性差,難以進行準確的變壓力變速壓制工作,對于有特殊工藝要求的加工難以勝任。此外,該系統(tǒng)在保壓與待機等工序中因卸荷或溢流將造成極大的能量消耗,能量效率低使得其使用成本大。
為解決上述問題,將伺服電機控制技術與液壓技術有機結合,利用伺服電機控制諸多優(yōu)點可大大優(yōu)化傳統(tǒng)液壓系統(tǒng)。通過伺服電機泵控系統(tǒng),可提高液壓系統(tǒng)控制精度,使液壓油路簡化,降低液壓系統(tǒng)的能耗,減小噪聲污染,提升系統(tǒng)效率等。
1.2大型液壓機應用伺服泵控系統(tǒng)的節(jié)能分析
目前,伺服電機泵控技術已開始應用于注塑機、制磚機等大功率液壓設備中,并取得了良好的節(jié)能效果。但在某些液壓設備上應用時,由于液壓系統(tǒng)對動力源有大流量、高壓力的要求,現行的伺服電機驅動單臺液壓泵的模式難以達到其技術要求。
如大型液壓機在快速下降行程中需要液壓動力源提供大流量輸出,對流量的要求達到了300 L/min;同時,在液壓機工進時又對動力源的壓力輸出提出了要求,通常要達到25 MPa左右。
在高壓大流量液壓機上應用伺服電機控制技術,將具有非常明顯的節(jié)能效果。因此,研發(fā)伺服電機控制的高壓大流量動力源有非常現實的需求。但高壓大流量泵的加工制造成本大,難以實現產業(yè)化推廣。為此,本研究提出了利用串聯雙泵組成高壓大流量液壓動力系統(tǒng)的方案。
2、伺服電機控制的雙泵液壓動力系統(tǒng)設計
2.1大型液壓機動力源需求分析
從大型液壓機工作的實際情況來看,在快進環(huán)節(jié)系統(tǒng)阻力不大,但由于大型液壓機主油缸直徑大,雖有補油箱輔助進油,其對動力源的流量需求仍很大,因此快進時對液壓動力源需求一般為大流量小壓力;而在工進時,系統(tǒng)阻力很大但運動速度緩慢,此時對液壓動力源的需求為小流量大壓力,同時為保證加工產品的品質,高端液壓機對位置精度和壓力精度都有很高要求,因此要引入壓力和流量的反饋進行閉環(huán)控制。
以某大型稀土永磁粉末成型液壓機的需求為例,其動力源要求最高壓力25 MPa,最大流量300 L/min。
2.2伺服電機控制的雙泵液壓系統(tǒng)結構設計
如圖1所示,伺服電機控制的高壓大流量雙泵液壓動力系統(tǒng)主要由控制器、伺服電機、主泵PH、副泵PL合流閥塊及其他電氣附件組成。
其中控制器主要接受主機的壓力P1流量指令Q1控制變頻電機的轉矩T和轉速n,從而實現對泵出口壓力P0和流量Q0的控制。泵出口處的壓力傳感器將壓力信號反饋回控制器。
同時,電機的轉速通過編碼器也反饋回控制器,通過泵的排量V與電機實時轉速n即可計算出實時流量Q(Q=Vn)。通過此系統(tǒng),泵的出口壓力和流量可由主機根據系統(tǒng)需求實時設定,并能根據壓力流量反饋自動調整。
主泵PH與副泵PL的合流/分流狀態(tài)也由主機給出信號,經由控制器控制合流閥塊中的電磁閥進行切換。系統(tǒng)電源為380 V/50 Hz三相交流電,需分別為控制器和伺服電機風扇供電。制動單元與制動電阻為消耗伺服電機再生制動時產生的逆向能量所設置。
2.3雙泵合流與分流實現高壓大流量控制的方法
為實現高壓、大流量的輸出要求,系統(tǒng)采用高壓主泵(PH)和低壓副泵(PL)組合的方式,使用由日本三星公司定制生產的雙聯齒輪泵。
高壓主泵額定壓力25 MPa,排量54 mL/r,低壓泵副泵額定壓力18 MPa,排量46 mL/r。在快進等環(huán)節(jié),將由主泵與副泵一起輸出液壓油,實現大流量輸出的目的。在工進等環(huán)節(jié),副泵將卸荷,只由主泵輸出。
如圖2所示,在主機工進需要高壓輸出時,主泵PH單獨接入回路,電磁換向閥SOL 1中1YA通電,換向閥處于右位,主泵PH的高壓油通過P、A閥口與液控單向閥的控制油口連通,液控單向閥反向導通,此時副泵PL通過液控單向閥卸荷,不參與到主機液壓系統(tǒng)中,即為分流狀態(tài)。
當主機快進需要大流量輸出時,控制器接收主機合流信號D1并控制1YA斷電,使合流閥塊中電磁換向閥SOL 1換向至中位,由于中位機能為O形,閥口P、A斷開,液控單向閥反向關閉,此時副泵PL通過普通單向閥與主泵PH合流,主泵PH與副泵PL都輸出到主機液壓系統(tǒng),即為合流狀態(tài)。
3、實驗設計
為研證該液壓動力系統(tǒng)應用于大流量高壓力液壓機的性能,在某大型稀土永磁粉末成型液壓機上裝載了此系統(tǒng)。液壓機主要油路的液壓回路如圖3所示。
主機液壓系統(tǒng)中電磁閥SOL3與插裝閥1配合,主要在加壓環(huán)節(jié)為主油缸送油;電磁閥SOL 4與插裝閥2配合,為主油缸卸荷;電磁閥控制兩個輔助油缸的上升與下降,此外電磁閥SOL 2左位接入即活塞桿上升時,補油箱的液控單向閥反向導通,主油缸內液壓油回到補油箱中。
本研究的伺服電機泵控液壓動力單元如圖4所示。圖4a為伺服電機泵與合流閥塊組成的液壓動力單元;圖4b為信號采集單元,用于采集液壓系統(tǒng)的壓力流量及電控系統(tǒng)的電壓電流等信號;圖4c為伺服電機泵的電控單元。
實驗以一典型的液壓機工作流程為基礎,主要包括合流下行(快進)、單流下行(慢進)、加壓、主油缸卸荷、合流上行(快退)幾個階段。各階段主機的壓力指令、流量指令,雙泵合流指令及液壓機主油缸行程圖如圖5所示。
在各工序階段,主機液壓回路中電磁閥動作情況如表1所示。
該實驗中,高速下行(A-B)高速上行(C-H)、慢速上行(H-I)過程中雙泵為合流狀態(tài),液壓系統(tǒng)為流量控制,響應主機的流量指令;中速下行(B-C)時,雙泵為單流狀態(tài),但液壓系統(tǒng)仍為流量控制;其他工序中,雙泵為主泵單獨工作狀態(tài),系統(tǒng)為壓力控制,響應主機的壓力指令。
在上述大型液壓機中應用本液壓動力系統(tǒng)作為液壓源,對其一個工作循環(huán)中的壓力與流量響應進行監(jiān)測可知:
從測量結果來看,在高速下行(A-B)時,雙泵的合流輸出達到了300 L/min,符合最大流量的設計要求;在慢速下行(C-D)時,只有主泵PH有效工作,監(jiān)測顯示在小流量(5L/min)時流量平穩(wěn),其小流量狀態(tài)工作穩(wěn)定。壓力控制方面,在材料成型的高壓加壓(E-F)階段,達到了設計要求的25 MPa高壓值,此外在高壓加壓時壓力超調量極小,能保證較高的壓制精度。
從伺服電機轉速的監(jiān)測結果來看,在中壓加壓(D-E)和高壓加壓(E-F)時電機速度反應良好,結合實測壓力來看,達到了良好的控制效果。在主缸卸荷(F-G)階段,伺服電機快速反轉實現卸荷,此時電機發(fā)電產生的逆向電流將反向輸出到控制器中,與控制器相連的制動電阻和制動單元將吸收這部分能量。
綜上可知,
(1)利用高壓主泵和低壓副泵組合的形式,可以滿足系統(tǒng)對液壓動力源在不同時刻大流量或高壓力的輸出要求;
(2)利用伺服電機控制雙泵,在滿足高壓大流量輸出的同時,其小流量特性穩(wěn)定、壓力控制精度高,能滿足高精度液壓機的要求;
(3)在保壓環(huán)節(jié),副泵卸荷、主泵高壓低速運轉,有顯著節(jié)能效果。
-
液壓
+關注
關注
3文章
208瀏覽量
20765 -
伺服電機
+關注
關注
85文章
2053瀏覽量
57967 -
動力系統(tǒng)
+關注
關注
1文章
293瀏覽量
20670
原文標題:伺服電機控制高壓大流量雙泵液壓動力系統(tǒng)
文章出處:【微信號:旺材伺服與運動控制,微信公眾號:旺材伺服與運動控制】歡迎添加關注!文章轉載請注明出處。
發(fā)布評論請先 登錄
相關推薦
金屬帶式CVT與動力系統(tǒng)的優(yōu)化匹配及液壓系統(tǒng)控制
“御疆”號動力系統(tǒng)完工
汽車動力系統(tǒng)解決方案集錦
汽車動力系統(tǒng)大盤點:助你設計絕佳方案
RoboMaster發(fā)布M2006動力系統(tǒng)!體積小、性能強,助力高性能機器人開發(fā)
壓機液壓系統(tǒng)的基本工作原理
原理 - 動力系統(tǒng)-電機控制器MCU與驅動電機
變速驅動提供動力的泵可以降低能源成本
豐田普銳斯混合動力系統(tǒng)原理
關于雙電機混合動力系統(tǒng)的功能介紹和應用
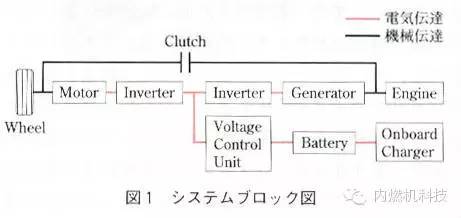
評論