來源:電子工藝技術
摘 要
采用砂漿多線切割工藝加工6英寸(1英寸=25.4 mm)N型碳化硅晶體,研究了此工藝中鋼線張力、 線速度、進給速度等切割參數對晶片切割表面的影響。通過優化切割工藝參數,最終得到高平坦度、低翹曲度、 低線痕深度的6英寸N型碳化硅晶片。
0 引言
碳化硅半導體作為寬禁帶半導體材料的典型代 表,具有高臨界擊穿場強、高熱導率、高電子飽和 漂移速度、大禁帶寬度的特點,極大地擴展了功率 器件的能量處理能力,能夠滿足下一代電力電子裝 備對功率器件更大功率、更小體積和更惡劣條件下 工作的要求,是制作高溫、高頻、大功率和低 損耗器件的優良材料。同時,碳化硅也是目前 晶體生長技術和器件制造水平最成熟、應用最廣泛 的寬禁帶半導體材料。近年來,PFC(Power Factor Correction,功率因數校正)電源、光伏逆變器,尤 其是新能源汽車領域的快速發展,使碳化硅功率器 件的接受度和認可度越來越高,碳化硅材料行業迎 來井噴式增長。
目前,碳化硅襯底材料的供應全球緊張,成 本居高不下,主要受制于碳化硅晶體生長及晶片 加工過程中較低的生產效率和生產良率。大尺寸功 率芯片對碳化硅晶片的表面加工提出越來越高的 要求,如對表面幾何形貌彎曲度(Bow)、翹曲度 (Warp)參數進一步收斂以及對表面劃傷、粗糙度 的進一步降低。碳化硅晶片生產加工過程中,由于 表面形貌控制不佳造成的良率損失占據最大比例, 而對于碳化硅晶片的表面幾何形貌不良,主要原因 是多線切割過程工藝不匹配造成,因此通過優化多 線切割工藝,提高切割質量,進而提高最終的晶片 表面幾何形貌參數,對于提升碳化硅晶片生產合格 率,降低碳化硅晶片生產成本是非常必要的。
1 試驗
碳化硅晶片切割常用的加工技術有三種:1)固 結金剛石多線鋸切割技術,是將金剛石磨粒通過電 鍍、釬焊的方法固結在不銹鋼切割線上,通過金剛 石線的高速往復運動,實現對碳化硅晶體的切割。2)游離磨料多線鋸切割技術,是配置金剛石懸浮切 削液,利用不銹鋼線將切削液帶入鋸縫,通過不銹 鋼線的往復運動,促使金剛石磨料達到“滾動-壓 痕”機制以達到材料去除目的。3)激光隱形切割技術,是將激光在材料內部聚焦,破壞焦點附近的 分子鍵,在焦點區域形成改質層,當垂直于改制層 施加壓力時,晶圓沿著改質層分離。固結金剛石多 線鋸切割技術,具有切割效率高、成本低的優點, 但金剛石顆粒造成的碳化硅晶片表面損傷層深度 大,需增加磨拋過程去除量,切割晶片的預留厚度 大,降低了晶錠的出片效率。游離磨料多線鋸切割 技術,具有線損小、晶片表面損傷層淺、出片率高 的優點,但是由于切割效率低、時間長,單臺設備 的綜合產能低。激光隱形切割技術具有損耗小、出片率更高的特點,因此為進一步降低碳化硅襯底生 產成本提供新的解決思路,但目前工藝技術尚不成 熟,處于工程化開發階段。
本文采用砂漿多線鋸切割方式進行碳化硅晶錠 切割,線鋸切割設備選用萊瑪特公司生產的DW288 型號產品;鋼線采用0.16 mm的不銹鋼線;砂漿采用 5 μm金剛石砂漿切削液,砂漿濃度600 ct/L;羅拉 槽鋸0.65 mm;單次切割晶錠長度100 mm。針對鋼線 張力、線速度、進給速度等切割參數分別設計對比 試驗,每個工藝條件20組試驗數據。切割完成后,晶片經清洗去除表面顆粒,測試 表面幾何形貌Bow、Warp等數據,檢測設備為康寧 公司FM200。
2 結果和討論
2.1 鋼線張力對晶片表面幾何形貌影響
隨試驗A研究鋼線張力對晶片表面幾何形貌影 響。切割使用鋼線的破斷張力為65 N,設計A1~A4四 個對照組,見表1,分別采用36 N、40 N、44 N、58 N 的張力進行切割工藝試驗;切割線速度統一設置為 15 m/s;切割時間為120 h,對應的平均切割進給速 度為1.28 mm/h。
切割晶片的典型幾何形貌如圖所示。
隨著鋼線張力的增加,碳化硅晶片的Bow均 值從-10 μm降至-6 μm;Warp均值從19 μm收斂 15 μm,Bow、Warp分布整體呈現收斂趨勢。但是 在采用張力為48 N的切割過程中,發生一次斷線, 導致該批次續切時Bow、Warp的失控,并且造成 了部分晶片的碎片。這是由于多線切割過程中切割 線保持較高的張力可以得到更加穩定和可靠的切割 系統,較高的張緊力減小了一定頻率下切割系統的 振幅,可以獲得較高的切割線固有頻率,使得振幅 隨著激勵頻率接近切割線固有頻率的變化率有所減 小,從而提高了切割過程的穩定性,得到更佳的切 割效果[6]。但考慮切割線本身比較細,在切割過程 中,線的直徑隨著磨損不斷變細,自身破斷力降 低,在過高張力的情況下很容易發生斷線情況,因 此從生產的角度,選擇40~44 N的鋼線張力是比較適 宜的(如圖2所示)。
2.2 鋼線速度對晶片表面幾何形貌影響
在試驗A基礎上,固定44 N鋼線張力;切割時間 為120 h,對應的平均切割進給速度為1.28 mm/h。試驗B研究鋼線速度對碳化硅晶片表面幾何形貌的影 響。設備的最大線速度為25 m/s,設計B1~B4四個對 照組,見表2,分別采用15 m/s、18 m/s、22 m/s、 25 m/s的張力進行切割工藝試驗。
B1~B4四個對照組的表面幾何形貌如圖3所示。
隨著鋼線速度從15 m/s增加到22 m/s,碳化硅晶 片的Bow值從-8 μm降低到-4 μm,Warp從17 μm 降低至12 μm。繼續提升線速度至25 m/s,碳化硅 晶片的Bow值和Warp均值變化不大,但是整體分布 呈現發散趨勢。這是由于隨著線速度的增加,參與 切割的金剛石磨料有效數量增加,整體切削能力變 強且單個磨粒承擔的法向力減少,線網運行更加平 穩,切割片的表面幾何形貌得到有效改善。但隨著 線速度的進一步提升,達到設備上限,線網本身的 振動趨勢增大,造成切割工藝的波動性變大,不同 批次之間的Bow、Warp分布開始離散。因此,選擇 22 m/s的線速度是比較適宜的。
2.3 進給速度對晶片表面幾何形貌影響
在試驗B基礎上,固定44 N鋼線張力,線速度 22 m/s。為提高生產效率,降低生產成本,對進給 速度做進一步優化。試驗C研究進給速度對碳化硅晶 片表面形貌的影響。設計C1~C4四個對照組,見表 3,分別采用1.18 mm/h、1.28 mm/h、1.41 mm/h、 1.54 mm/h的平均進給速度進行切割工藝試驗,對應 切割時間分別為120 h、110 h、100 h、90 h。
C1~C4四個對照組的表面幾何形貌如圖4所示。
隨著進給速度從1.28 mm/h提升至1.54 mm/h, 即切割時間從120 h縮短至100 h,Bow值從-4 μm變 到-6 μm,Warp中值從12 μm增加至13.5 μm,最大值 仍小于20 μm;隨著進給速度繼續提升至1.71 mm/h,即切割時間縮短至90 h,碳化硅晶片的Bow和Warp變 得離散并有部分晶片異常增大現象,部分晶片表面 出現明顯的波紋狀線痕并呈現出FM200測試局部面型 缺失的現象。
這是由于碳化硅晶錠在切割過程中,切割鋼 線、金剛石粉與碳化硅晶體之間高速摩擦,這一過 程中會放出大量的熱量,其中一部分熱量被切削液 及時吸收,另外一部分被碳化硅晶體吸收產生體變 形進而影響碳化硅晶片的幾何參數。隨著進給速 度增加,切割過程中通過磨粒鑲嵌去除的速度也加 快,產生的熱量相對增加,增大了單晶由于溫度變 化引發的變形。同時,在90 h切割過程中,可觀測到 線弓明顯增大,在直徑區域達到最大值,表明切削 能力不足,尤其是在直徑附近區域的向下磨削效率 跟不上線網進給,線網由于溫度引起的局部線性膨 脹、強度變化及張力抖動增加,造成局部側向磨削 增加,造成局部的深線痕和面型缺失。因此,現階 段采用1.54 mm/h的進給速度,即100 h的切割時間, 是相對合理的,可以在保證質量的基礎上提升16%的 生產效率。
3 結論
研究了切割工藝參數對砂漿多線切割6英寸N型 碳化硅晶片表面幾何形貌的影響,通過對比鋼線張 力、線速度、進給速度等切割參數量產晶片表面幾 何參數數據,選擇鋼線張力44 N、線速度22 m/s、進 給速度1.54 mm/h的工藝參數,既能得到穩定收斂的 表面幾何參數,又能兼顧較高的生產效率。
審核編輯:湯梓紅
-
半導體
+關注
關注
335文章
28213瀏覽量
228423 -
功率器件
+關注
關注
42文章
1852瀏覽量
91504 -
晶片
+關注
關注
1文章
406瀏覽量
31802 -
碳化硅
+關注
關注
25文章
2936瀏覽量
49802
原文標題:探索鋼線張力、線速度和進給速度對6英寸N型碳化硅晶片的影響
文章出處:【微信號:today_semicon,微信公眾號:今日半導體】歡迎添加關注!文章轉載請注明出處。
發布評論請先 登錄
相關推薦
中科院成功制備8英寸碳化硅襯底;華強北二手iPhone價格大跳水
海外大廠搶灘2023,國內企業加速追趕碳化硅襯底8英寸節點
碳化硅壓敏電阻 - 氧化鋅 MOV
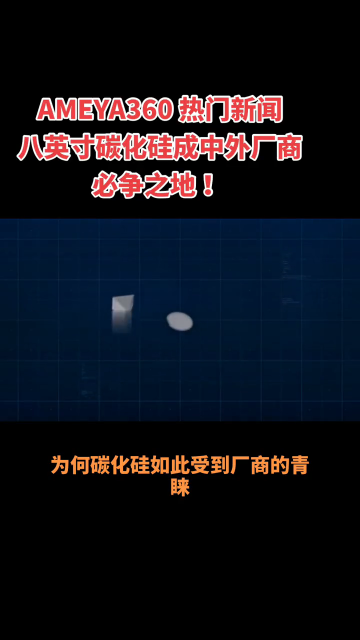
評論