引言
目前高功率砷化鎵基單片微波集成電路(MMICs)已廣泛應用于軍事、無線和空間通信系統。使用連接晶片正面和背面的襯底通孔,這些MMICs的性能顯著提高。
在蝕刻通孔之前,在晶片的正面制造器件,然后根據需要將晶片從背面減薄到100-200μm的厚度。從晶片的背面執行通孔蝕刻,以接觸正面上的接地金屬焊盤。干法蝕刻優于濕法蝕刻,因為它具有優異的均勻性和尺寸控制。
由于通孔蝕刻在所有其他器件制造工藝之后進行,因此工藝的可靠性和再現性非常重要。為了蝕刻非常高縱橫比的孔,干法蝕刻工藝必須提供高蝕刻速率、良好的蝕刻各向異性、平滑的側壁以及對掩模材料和正面金屬焊盤的高選擇性。目前滿足上述要求的最常見技術是反應離子蝕刻(RIE)。
實驗與討論
我們將晶片放置在施加了13.56 MHz射頻功率的下電極上。使用冷卻器將該電極的溫度保持在30℃。在將工藝氣體(CCl2F2和CCl4)引入腔室之前,通過由機械泵支持的渦輪分子泵將腔室抽空至約8E-6托的基礎壓力。由于四氯化碳在室溫下是液體,所以使用鼓泡器中的N2氣體將其蒸汽輸送到室內。我們在砷化鎵中蝕刻孔之后,分別通過在丙酮中清洗和在FeCl3 /H2O溶液中濕法蝕刻來去除光致抗蝕劑和Ni掩模。
圖1顯示了在功率=150W、壓力=100mTorr、CCl4 =7sccm、CCl2F2=35sccm的相同條件下,對于60μm直徑的開口,分別使用光致抗蝕劑和Ni掩模獲得蝕刻輪廓。這些蝕刻曲線表明,在更高的壓力下(100毫托),使用光刻膠掩模時蝕刻本質上是各向異性的,而使用Ni掩模時是結晶的。
圖1:橫截面掃描電鏡圖
為了獲得大于116μm的蝕刻深度和期望的輪廓,因此英思特在大約40-50毫托的較低壓力下研究了Ni掩模。在較低壓力下,平均自由程增加,這增強了物理蝕刻分量,因此增強了各向異性。實驗表明,在沒有任何掩模的情況下,砷化鎵平均蝕刻速率約為3-4 m/min。
然而,在Ni掩模的情況下,蝕刻速率有非常小的降低,從60分鐘的2.1米/分鐘降低到120分鐘的1.9毫米/分鐘。在這兩種情況下,蝕刻速率隨著深度的增加而降低,這是因為提供活性物質和去除蝕刻副產物的效率降低。與Ni掩模相比,用光致抗蝕劑掩模觀察到較少的底切。
如圖2所示,在100毫托工藝壓力下蝕刻時間為120分鐘。該蝕刻輪廓清楚地表明,使用光致抗蝕劑掩模的RIE工藝僅適用于蝕刻100μm深的通孔。
圖2:經過120 min的蝕刻后,用光刻膠掩模獲得的掃描電鏡輪廓
從上面的討論可以清楚地看出,Ni掩模適用于使用RIE工藝的200μm深的通孔蝕刻,這導致非常好的選擇性、再現性和可重復性。
結論
英思特研究了各種工藝參數對采用四氯化碳氣體的RIE深度各向異性刻蝕砷化鎵的影響。發現鎳金屬掩模適合于實現200μm的蝕刻深度,平均蝕刻速率約為1.3 m/min,并且具有期望的各向異性輪廓。
英思特研究表明在40毫托壓力、950瓦線圈功率、90瓦壓板功率、約4毫米/分鐘的蝕刻速率和通孔蝕刻產率下整個晶圓的90%以上,具有非常好的均勻性和再現性。與RIE工藝相比,ICP工藝產生了具有可接受的蝕刻側壁形態的高蝕刻速率。這種高密度等離子體蝕刻工藝已經集成到生產線中,用于以高產量制造MMIC,而不影響使用現有設計和掩模組的生產。
審核編輯:湯梓紅
-
集成電路
+關注
關注
5387文章
11530瀏覽量
361647 -
半導體
+關注
關注
334文章
27290瀏覽量
218102 -
蝕刻工藝
+關注
關注
3文章
51瀏覽量
11736
發布評論請先 登錄
相關推薦
MESFET集成電路應用-概述
單片微波集成電路設計分析介紹
黑科技!看大神如何使用AI設計微波集成電路
怎么設計制作一種基于GaAs工藝的可變增益功率放大器單片微波集成電路?
微波集成電路(MMIC)是什么意思
用于毫米波范圍的單片微波集成電路

微波集成電路設計作者: 顧其諍 項家楨 彭孝康
射頻微波集成電路設計探討
微波元器件和微波集成電路的學習課件免費下載
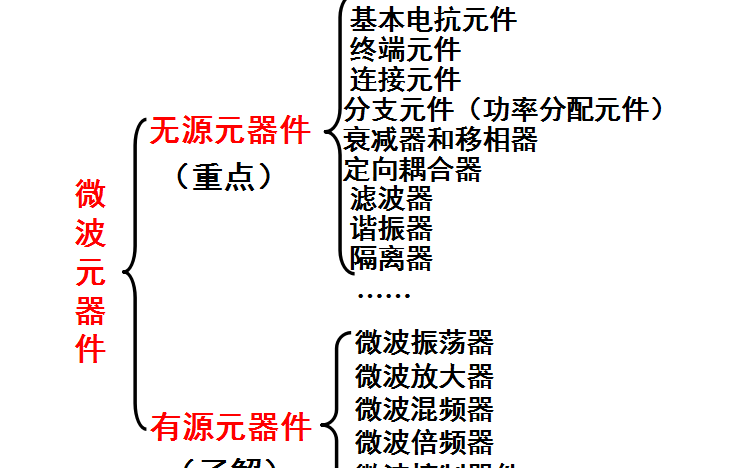
關于穩懋:全球最大的砷化鎵晶圓代工龍頭
多極碳化硅基氮化鎵(GaN-on-SiC)單片微波集成電路(MMIC)器件
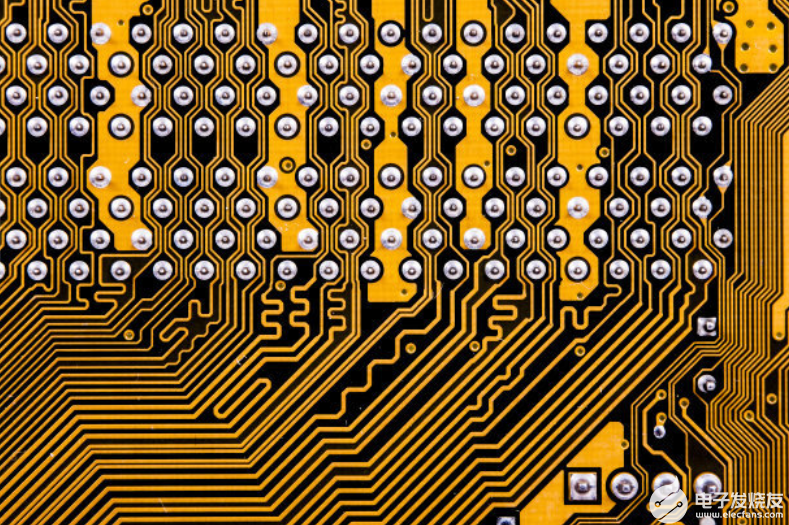
評論