作者:Pete Sopcik and Dara O’Sullivan
半導體技術和功能的進步為工業應用中的數據檢測、測量、解釋和分析提供了新的機會,特別是基于狀態的監控解決方案。基于MEMS技術的下一代傳感器與用于診斷和預后應用的先進算法相結合,擴大了測量各種機器的機會,提高了有效監控設備的能力,延長了正常運行時間,提高了過程質量和增加吞吐量的能力。
為了實現這些新功能并獲取基于狀態的監控的優勢,新的解決方案必須準確、可靠且穩健,以便實時監控可以擴展到潛在設備故障的基本檢測之外,以提供有見地和可操作的信息。下一代技術的性能與系統級洞察力相結合,可以更深入地了解解決這些挑戰所需的應用和要求。
振動是機器診斷的關鍵組成部分之一,已被可靠地用于監測各種工業應用中最關鍵的設備。有大量文獻支持實現高級振動監測解決方案所需的各種診斷和預測功能。不太清楚的是振動傳感器性能參數(如帶寬和噪聲密度)與最終應用故障診斷能力之間的關系。本文介紹了工業自動化應用中的主要機器故障類型,并確定了與特定故障相關的關鍵振動傳感器性能參數。
下面重點介紹幾種常見的故障類型及其特征,以深入了解在開發基于狀態的監控解決方案時必須考慮的一些關鍵系統要求。這些包括但不限于不平衡、不對中、齒輪故障和滾動軸承缺陷。
不平衡
什么是不平衡,是什么原因造成的?
不平衡是質量分布不均,導致載荷將質心從旋轉中心移開。系統不平衡可歸因于安裝不當,例如耦合偏心率、系統設計錯誤、組件故障,甚至碎屑或其他污染物的堆積。例如,大多數感應電機內置的冷卻風扇可能會由于灰塵和油脂的不均勻積累或風扇葉片損壞而變得不平衡。
為什么不平衡的系統是一個問題?
不平衡系統會產生過度振動,這些振動以機械方式耦合到系統內的其他組件,例如軸承、聯軸器和負載,從而可能加速處于良好運行狀態的組件的劣化。
如何檢測和診斷不平衡
整體系統振動的增加可能表明不平衡系統造成的潛在故障,但通過頻域分析來診斷振動增加的根本原因。不平衡系統以系統的旋轉速率(通常稱為 1×)產生信號,其幅度與旋轉速率的平方成正比,F = m × w2.1×分量通常始終存在于頻域中,因此通過測量1×和諧波的幅度來識別不平衡系統。如果1×的幅度高于基線測量值,諧波遠小于1×,則系統可能是不平衡的。水平和垂直相移振動分量也可能處于不平衡系統中。1
診斷不平衡系統時必須考慮哪些系統規格?
需要低噪聲來減少傳感器的影響,并能夠檢測不平衡系統產生的小信號。這對于傳感器、信號調理和采集平臺非常重要。
需要采集系統具有足夠的分辨率來提取信號(尤其是基線信號),以檢測這些小的不平衡。
帶寬對于捕獲除旋轉速率之外的足夠信息是必要的,以提高診斷的準確性和可信度。1×諧波可能受到其他系統故障的影響,例如未對準或機械松動,因此分析旋轉速率或1×頻率的諧波有助于區分系統噪聲和其他潛在故障。1對于旋轉速度較慢的機器,基波轉速可能遠低于 10 rpm,這意味著傳感器的低頻響應對于捕獲基波轉速至關重要。ADI公司的MEMS傳感器技術能夠檢測低至直流的信號,并能夠測量較慢的旋轉設備,同時還能夠測量通常與軸承和齒輪箱缺陷相關的更高頻率內容的寬帶寬。
圖1.基于旋轉速率或1×頻率下振幅的增加,存在不平衡系統的可能性。
失調
什么是錯位,是什么原因造成的?
顧名思義,當兩個旋轉軸未對齊時,就會發生系統未對中。圖2顯示了一個理想的系統,從電機開始,然后是軸,聯軸器,一直到負載(在本例中為泵)實現對準。
圖2.一個理想的對齊系統。
錯位可能發生在平行方向和角度方向上,也可能是兩者的組合(見圖3)。當兩個軸在水平或垂直方向上移位時,就會發生平行不對中。當其中一個軸與另一個軸成相關角度時,就會發生角度不對中。2
圖3.不同錯位的例子包括(a)角度,(b)平行或兩者的組合。
為什么錯位是一個問題?
未對準誤差會迫使組件在比組件最初設計處理的更高的應力或負載下運行,從而影響更大的系統,并最終導致過早失效。
如何檢測和診斷錯位
未對準誤差通常表現為系統旋轉速率的二次諧波,稱為2×。頻率響應中并不總是存在2×分量,但是當它存在時,幅度與1×的關系可用于確定是否存在未對準。增加的錯位可以將諧波激發到10×具體取決于錯位的類型、測量位置和方向信息。1圖 4 突出顯示了與潛在未對準故障相關的特征。
圖4.2×次諧波增加,加上高次諧波增加,表明存在潛在的失調。
診斷未對準的系統時必須考慮哪些系統規格?
需要低噪聲和足夠的分辨率來檢測小的錯位。機器類型、系統和工藝要求以及轉速決定了允許的錯位公差。
帶寬對于捕獲足夠的頻率范圍并提高診斷的準確性和可信度是必要的。1×諧波可能受到其他系統故障的影響,例如未對準,因此分析1×頻率的諧波有助于與其他系統故障區分開來。對于更高轉速的機器尤其如此。例如,運行在 10,000 rpm 以上的機器(如機床)通常需要超過 2 kHz 的質量信息,以便以高置信度準確檢測不平衡。
多向信息還可以提高診斷的準確性,并提供對錯誤差類型和未對準方向的洞察。
系統的相位與方向振動信息相結合,進一步改善了對錯位誤差的診斷。通過測量機器上不同點的振動并確定相位測量或整個系統的差異,可以深入了解未對準是角度、平行還是兩種未對準類型的組合。1
滾動體軸承缺陷
什么是滾動軸承缺陷,是什么原因造成的?
滾動軸承缺陷通常是機械引起的應力或潤滑問題的產物,這些問題在軸承的機械部件內產生小裂紋或缺陷,導致振動增加。
為什么滾動軸承故障是一個問題?
滾動軸承幾乎存在于所有類型的旋轉機械中,從大型渦輪機到較慢的旋轉電機,從相對簡單的泵和風扇到高速CNC主軸。軸承缺陷可能是潤滑污染(圖 5)、安裝不當、高頻放電電流(圖 5)或系統負載增加的跡象。故障可能導致災難性的系統損壞,并對其他系統組件產生重大影響。
如何檢測和診斷滾動體軸承故障?
有許多技術用于診斷軸承故障,并且由于軸承設計背后的物理原理,可以根據軸承幾何形狀、旋轉速度和缺陷類型計算每個軸承的缺陷頻率,這有助于診斷故障。軸承缺陷頻率如圖6所示。
圖6.軸承缺陷頻率取決于軸承類型、幾何形狀和旋轉速率。
對特定機器或系統的振動數據的分析通常依賴于時域和頻域分析的組合。時域分析對于檢測系統振動水平總體增加的趨勢非常有用。然而,該分析中包含的診斷信息很少。頻域分析可提高診斷見解,但由于其他系統振動的影響,識別故障頻率可能很復雜。
為了早期診斷軸承缺陷,缺陷頻率的諧波用于識別早期或初期故障,以便在災難性故障發生之前對其進行監控和維護。為了檢測、診斷和理解軸承故障的系統影響,包絡檢測等技術(如圖7所示)與頻域頻譜分析相結合,通常可提供更深入的信息。
圖7.包絡檢測等技術可以從寬帶寬振動數據中提取早期軸承缺陷特征。
診斷滾動體軸承故障時必須考慮哪些系統規格?
低噪音和足夠的分辨率對于檢測早期軸承缺陷至關重要。通常,這些缺陷特征在缺陷發作期間的振幅較低。由于設計公差,軸承固有的機械滑移通過將振幅信息分散到軸承頻率響應中的多個箱中來進一步降低振動幅度,因此需要低噪聲才能更早地檢測到信號。2
帶寬對于及早發現軸承缺陷至關重要。在旋轉過程中,每次撞擊缺陷時,都會產生包含高頻成分的脈沖(見圖7)。監測軸承缺陷頻率的諧波,而不是旋轉速率,以發現這些早期故障。由于軸承缺陷頻率與旋轉速率的關系,這些早期特征可能發生在幾千赫茲范圍內,并遠遠超出10 kHz至20 kHz范圍。2即使對于低速設備,軸承缺陷的固有性質也需要更寬的帶寬進行早期檢測,以避免系統諧振和系統噪聲的影響,從而影響較低頻段。3
動態范圍對于軸承缺陷監測也很重要,因為系統負載和缺陷會影響系統經歷的振動。載荷增加會導致作用在軸承和缺陷上的力增加。軸承缺陷還會產生激發結構共振的脈沖,從而放大系統和傳感器所經歷的振動。2隨著機器在停止/啟動條件或正常運行期間速度的上升和下降,速度的變化為系統共振創造了潛在的激發機會,從而導致更高的振幅振動。4傳感器飽和會導致信息缺失、誤診,以及(在某些技術的情況下)傳感器元件損壞。
齒輪缺陷
什么是齒輪缺陷,是什么原因造成的?
齒輪故障通常由于疲勞、剝落或點蝕而發生在齒輪機構的齒上。這些可以表現為齒根裂紋或齒面上的金屬去除。它們可能是由磨損、過載、潤滑不良、間隙以及偶爾不正確的安裝或制造缺陷引起的。5
為什么齒輪故障是一個問題?
在許多工業應用中,齒輪是動力傳輸的主要元件,并承受巨大的應力和負載。它們的健康對于整個機械系統的正常運行至關重要。可再生能源領域一個眾所周知的例子是,風力渦輪機停機(以及隨之而來的收入侵蝕)的最大因素是主動力系統中多級齒輪箱的故障。5類似的考慮也適用于工業應用。
如何檢測和診斷齒輪故障?
由于難以在故障附近安裝振動傳感器,并且由于系統內的多個機械激勵而存在明顯的背景噪聲,因此齒輪故障很難檢測。在更復雜的齒輪箱系統中尤其如此,其中可以有多個旋轉頻率、齒輪比和嚙合頻率。6因此,在齒輪故障檢測中可以采取多種互補的方法,包括聲發射分析、電流特征分析和油屑分析。
在振動分析方面,齒輪箱外殼是加速度計的典型安裝位置,其中主要的振動模式是軸向。7健康的齒輪以稱為齒輪嚙合頻率的頻率產生振動特征。這等于軸頻率和齒輪齒數的乘積。通常還存在一些與制造和裝配公差相關的調制邊帶。圖 8 中說明了一個健康的齒輪。當發生局部故障(例如齒裂)時,每轉的振動信號將包括系統在相對較低的能量水平下對短時間沖擊的機械響應。這通常是一種低幅度的寬帶信號,通常被認為是非周期和非平穩的。7,8
圖8.曲軸轉速為 ~1000 rpm、齒輪速度為 ~290 rpm、齒輪齒數 = 24 的健康齒輪的頻譜。
由于這些特殊特性,標準頻域技術本身被認為不適合準確識別齒輪故障。頻譜分析可能無法檢測到早期齒輪故障,因為沖擊能量包含在邊帶調制中,邊帶調制也可能包含來自其他齒輪副和機械部件的能量。時域技術(如時間同步平均)或混合域方法(如小波分析和包絡解調)通常更合適。9
診斷齒輪故障時必須考慮哪些系統規格?
寬帶寬在齒輪故障檢測中通常非常關鍵,因為齒輪齒數在頻域中充當乘法器。即使對于相對低速的系統,所需的檢測頻率范圍也會迅速推高到多個kHz區域。此外,局部故障進一步擴展了帶寬要求。
由于幾個原因,分辨率和低噪聲非常關鍵。將振動傳感器安裝在靠近特定故障帶的困難意味著機械系統對振動信號的衰減可能更高,因此能夠檢測低能量信號至關重要。此外,由于信號不是靜態周期信號,因此不能依賴從高本底噪聲中提取低幅度信號的標準FFT技術——傳感器本身的本底噪聲必須較低。在齒輪箱環境中尤其如此,其中混合了來自齒輪箱不同元件的多個振動特征。除了這些考慮之外,早期檢測的重要性不僅在于資產保護原因,還在于信號調理原因。研究表明,在單齒斷裂故障的情況下,振動嚴重程度可能更高,而不是具有兩個或更多齒斷裂的故障,這意味著在早期階段檢測可能相對容易。
總結
雖然常見,不平衡、不對中、滾動體軸承缺陷和齒輪齒故障只是高性能振動傳感器可以檢測和診斷的眾多故障類型中的一小部分。更高的傳感器性能與適當的系統級考慮相結合,可實現下一代基于狀態的監控解決方案,從而更深入地了解各種工業設備和應用的機械操作。這些解決方案將改變維護方式和機器運行方式,最終減少停機時間,提高效率,并為下一代設備提供新功能。
故障類型 | 帶寬 | 噪聲密度 | 動態范圍 | 分辨率 |
不平衡 | 低 | 中等 | 高 | 中等 |
失調 | 中等 | 低/中 | 高 | 中等 |
軸承 | 高/非常高 | 低 | 中等 | 高 |
齒輪 | 非常高 | 低 | 低 | 高 |
對于表1,低帶寬<1 kHz,中等帶寬在1 kHz至5 kHz之間,高帶寬>5 kHz。低噪聲密度>1 m g/√Hz,中等噪聲密度在 100 μ g/√Hz 至 1 m g/√Hz 之間,高噪聲密度<100 μ g/√Hz。低動態范圍<5 g,中動態范圍在5 g至20 g之間,高動態范圍>20 g。
審核編輯:郭婷
-
傳感器
+關注
關注
2551文章
51134瀏覽量
753842 -
半導體
+關注
關注
334文章
27390瀏覽量
219038 -
mems
+關注
關注
129文章
3934瀏覽量
190680
發布評論請先 登錄
相關推薦
狀態監測引入單對以太網,實現更強大的傳感器集群
NI InsightCM 全新企業級狀態監測解決方案
無線傳感器常見的五個問題及解決方案
活動與健康監測器解決方案
主流智能家居傳感器應用解決方案大全
AMEYA360設計方案丨胎壓監測系統解決方案
使用分立元件的功放監測與控制解決方案討論
ADIMEMS解決方案 傳感器性能如何支持狀態監控解決方案
UNIVO傳感器的解決方案
物聯網最低功耗解決方案是由什么傳感器實現的?
四種霍爾傳感器的開關解決方案
傳感器性能如何支持狀態監控解決方案?
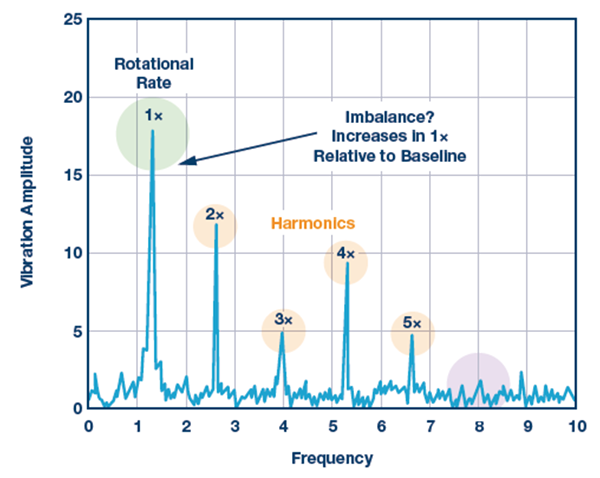
評論