1.前言
隨著汽車市場的大變革,新能源汽車逐漸替代傳統燃油汽車。新能源汽車絕大多數離不開電池模組,同時又需要滿足汽車車身輕量化的要求,故電池外殼通常采用密度小、強度高的鋁合金來制造。但是鋁合金焊接起來難度大,尤其是薄板鋁合金焊接難度更大。本文主要研究采用脈沖激光焊機對0.5毫米鋁合金薄片焊接時,采用合適的焊接參數,焊前采用CCD實時成像技術監測母材拼接距離,定位準確后再進行焊接,焊接過程中選用平均焊接速度≥20mm/s,能夠獲得焊接熔深0.4~0.7mm,熔寬0.8~1.2mm,并且焊縫成形美觀的焊縫。
2.新能源汽車電池外殼激光焊接工藝流程
激光焊接由于采用能量密度特別高的激光作為焊接熱源,故焊接起來速度快,熱影響區小,焊接變形量小,對于鋁合金焊接也能夠獲得焊接質量優良的焊縫。其中,電池外殼焊接時焊接材料涉及鋁合金和紫銅兩種異種材料的焊接,鋁合金焊接時極易氧化,銅由于導熱性極強,焊接難度非常大。電池外殼有圓形和方形兩種形式。焊接方式有拼接焊和搭接疊焊兩種方式,焊接部位涉及防爆網、極柱、封口處、模組等部位。
3.實驗方案設計
3.1 實驗總體方案描述
實驗采用兩臺激光焊接機進行焊接,兩臺檢測機進行檢測,一條主流水線運送電池,主流水線又有多個分支,機器外形尺寸11000mm×2500mm×2000mm(長×深×高)。針對新能源汽車電池外殼激光焊接要求,本方案由激光焊接機、檢測機、在線打標機、自動流水線等單元構成。其中激光焊接機最先工作,主要完成電池的焊裝工作,檢測機主要對焊縫進行測試,檢測其是否短路,以及密封性,打標機打印標簽,并自動把不合格品剔除流水線。
其中位于流水線前端的兩臺激光焊接機均配備有激光發射器、立式激光焊接頭、三軸機械臂、氣動夾具、傳送帶、機械手配合上下料等,兩臺激光焊接配置一致。采用雙機械手上下料,相互不干擾,裝配精度高,生產效率高。
本方案的顯著優點是:
(1)焊接采用兩套激光焊機,配置兩套上下料裝置,同時進行焊接,提高生產效率,同時減少焊接變形;
(2)兩個焊接工作臺各配備一臺機械手上下料,焊接區域與上料區域分開,在工作過程中,保證操作人員的人身安全。
3.2 設備總體布局圖
最終實驗采取的實驗布局如圖1所示。
圖1 設備總體布局圖
4.實驗操作過程
電池外殼組裝好后,立放在傳送帶上,然后經由傳送帶傳至焊接區域。由焊接機械手上料,然后組裝,采用啟動夾具進行定位夾緊,焊前采用CCD檢測拼縫,保證焊縫間距,間距一致且合適才能焊接。CCD定位誤差在0.05毫米以內。采用激光焊接機對電池進行封裝焊后,能夠達到焊接熔深0.4~0.7mm,熔寬0.8~1.2mm。激光焊后,焊縫整體外觀整潔,焊縫成形美觀,焊接變形量小于0.5毫米。同時,在焊接機頭上方配備排煙除塵裝置,及時除去焊接過程中產生的煙塵,維護生產環境。焊接夾具采用氣動控制,能夠實現自動定位、夾緊工序,能夠利用輸送軸把電池外殼精準送到焊接位置,焊接期間,采用CCD實時監測焊接過程。夾具可以根據被焊電池外殼大小自動調節。
圖2 整條流水線操作流程圖
5.實驗小結
通過實驗發現,采用流水線作業更能獲得質量一致度高的產品,焊前采用CCD監測焊縫間距,定位準確后再進行焊接,焊接過程中選用平均焊接速度≥20mm/s,焊接熔深0.4~0.7mm,熔寬0.8~1.2mm的焊接參數能獲得焊縫成形美觀的焊縫,同時采用兩臺激光焊機焊接,能有效減小焊接過程中的變形量,能將變形量控制在0.5mm以下。
審核編輯:郭婷
-
新能源汽車
+關注
關注
141文章
10622瀏覽量
100104 -
電池
+關注
關注
84文章
10674瀏覽量
131242
原文標題:新能源汽車電池外殼激光焊接工藝研究
文章出處:【微信號:AMTBBS,微信公眾號:世界先進制造技術論壇】歡迎添加關注!文章轉載請注明出處。
發布評論請先 登錄
相關推薦
激光焊接機:新能源動力電池焊接的高效解決方案
多型號電池蓋帽焊接激光焊接機,電池鎳片激光焊接機
薄板拼焊激光焊接工藝
激光焊接機:新能源動力電池焊接的高效利器
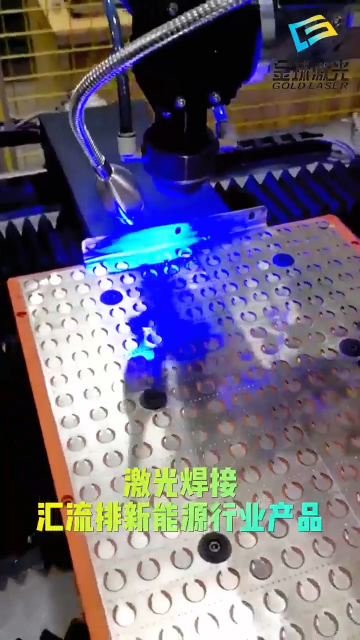
評論