隨著汽車電氣化的不斷發展,零部件的集成化設計趨勢亦不斷推進,三合一驅動總成方案成為各廠家競爭的熱土。相對早期電驅方案,三合一電驅系統具備以下優勢:結構緊湊、體積變小,利于布置;質量輕,低行駛能耗;三相直連,可靠又經濟;重心下降,利于整車操控;高速傳動,帶來較高扭矩容量和總成效率提升;可擴展的模塊化設計,大大縮短產品開發周期,降低開發成本效益。
1 三合一電驅系統概
圖1 三合一電驅系統結構
2、三合一電驅系統可靠性研究的依據
汽車產品可靠性是指在一定時間內、一定條件下,無故障地執行指定功能的能力或可能性。對于機械結構,其失效約90%來源于疲勞。可靠性可定義為:如果結構發生了不可修復性故障,其可靠性可等同于耐久性;若故障可修復,其可靠性就是產品大修期、報廢期或者退役期對應的耐久性。
3、三合一電驅系統對可靠性試驗技術要求的選擇與應用
在三合一電驅總成系統中對電子/電氣元件機械負荷可靠性考核將使用ISO 19453-3-2018標準,主要有以下幾點原因:
三合一電驅系統的電子/電氣部件機械負荷可靠性技術要求:
3.2 電機、減速器機械可靠性試驗方法的應用
3.2.1 電動汽車用驅動電機系統可靠性試驗方法介紹與分析
借鑒汽車發動機可靠性測試規范,采用定轉速、變化轉矩的工作模式且選用3個不同電壓平臺,對新能源驅動電機的可靠性進行考核,同時試驗對于不同車型的電機測試時間有所不同。圖2所示的是單個循環的試驗工況,其中nN為被試電機額定轉速,ns為試驗過程中被試電機轉速設定值(r/min),當電壓為額定電壓或者最高電壓時,ns=1.1×nN;而電壓為最低電壓時,ns =最低電壓/最高電壓×nN;Tpp為被試驅動電機系統在峰值功率的額定扭矩(N·m),當電壓為最高電壓時, Tpp=峰值功率/ns;當電壓為最低電壓時,Tpp=峰值功率/nN;TN為被試驅動電機系統的額定扭矩(N·m);t為時間。
圖2 電動汽車驅動電機系統可靠性測試循環示意圖
試驗加載循環過程如表1所示,總測試時間為402 h,結合電動汽車自身供電單元特性,電機及控制系統電壓采用浮動電壓,先在額定電壓下運行320 h,在最大電壓和最低電壓下各運行40 h,最后在額定工作電壓、額定功率下運行2 h。
表1 電動汽車驅動電機系統可靠性測試循環參數表
該測試方法是國內電機廠商的主流試驗方法,但應用于電驅系統時卻具有一定的局限性:
3.2.2 三合一電驅系統可靠性試驗方法應用基于第3.2.1節中對可靠性試驗方法的分析,該部分主要針對上述局限性展開,制定三合一電驅總成試驗規范。
(1)電機可靠性循環周期確認
圖3 電驅系統總成累計損傷折算方法獲得載荷譜流程圖
(2)溫度在可靠性工況制定溫度是影響產品可靠性的重要因素,可以使電氣元件和橡膠件加速老化、衰減、退磁、泄漏等,也可以使齒輪、軸承等零件加速膠合、點蝕、漏脂,因此在試驗過程中需要依據電機的散熱能力,確保試驗循環中零件的最高溫度點低于磁鋼許可溫度上限,增加循環水溫考核,使覆蓋整個可靠性循環工況。
(3)性能衰減評價標準定義性能衰減評價標準定義:5%-10%。
(4)轉速三合一電驅系統配備了高轉速電機,齒面相對滑動需要減小;較高轉速下,動態響應增大,增加了齒輪箱的載荷,需要在可靠性試驗中驗證;軸承和油封尺寸一樣,線速度增大,發熱量增大,失效風險增大,需要在持續高速工況下考核,高轉速下,齒輪發生膠合的風險增大,需要在可靠性試驗中驗證。
3.2.3 衍生可靠性循環工況
圖4 基于原可靠性循環工況衍生的循環工況
4 結論
(1)針對電子/電氣元件機械負荷,比較標準時效性和標準使用對象,選定了適用于三合一系統的考核指標;
(2)針對電機、減速器機械可靠性試驗,分析了現行標準的局限性,就此展開研究。定義了試驗溫度要求和性能衰減評判指標,結合項目應用狀況,衍生出適應于該項目的可靠性循環工況,使三合一電驅系統的驗證更為合理和完善。
編輯:lyn
-
電動汽車
+關注
關注
156文章
12118瀏覽量
231585 -
控制器
+關注
關注
112文章
16396瀏覽量
178514 -
電機
+關注
關注
142文章
9040瀏覽量
145737 -
減速器
+關注
關注
7文章
397瀏覽量
23323
原文標題:三合一電驅系統可靠性試驗研究與應用
文章出處:【微信號:motorcontrol365,微信公眾號:電機控制設計加油站】歡迎添加關注!文章轉載請注明出處。
發布評論請先 登錄
相關推薦
更小!更強!更新穎!三合一全隔離CAN收發芯片SM1500
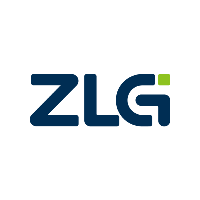
三合一傳感器:準確測量的未來之選
網絡信號三合一浪涌保護器應用選型方案
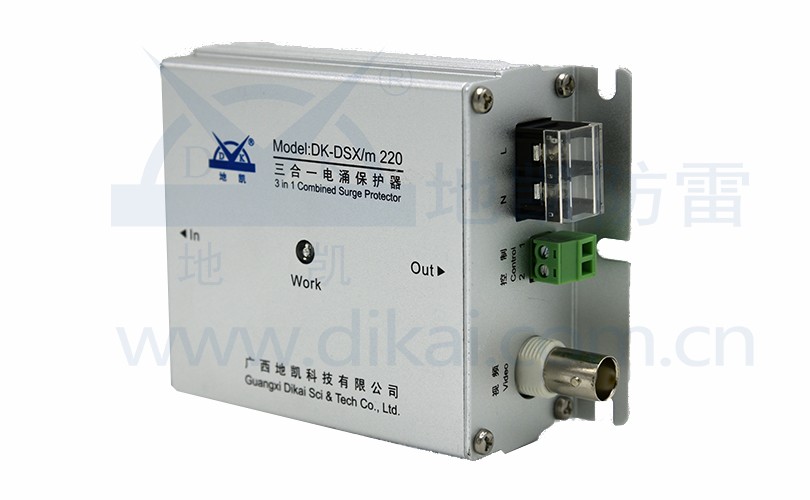
PinFin Cooling Master三合一水道測試系統
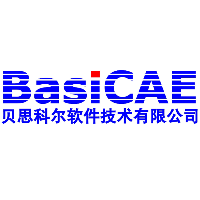
TMDS351 2.5 Gbps三合一DVI/HDMI開關數據表
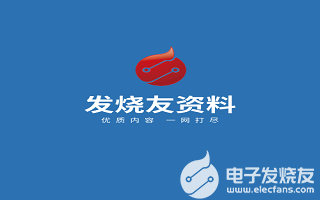
聯想發布三合一觸控芯片LFP131
聯想LFP131三合一觸控芯片首發,開啟人機交互新時代
三合一雷達流量計是一種集成了水位、流速和流量測量功能的技術裝備
WH4530A三合一光距感 接近傳感芯片
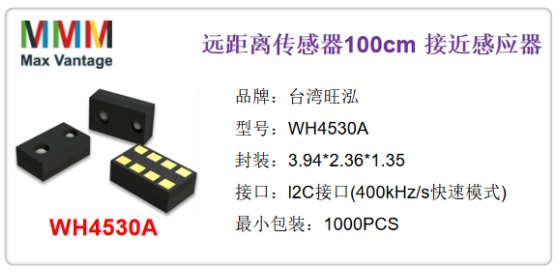
評論