動力電池新一輪規模化擴產啟動,物流的柔性升級成為電池企業無法繞開的話題。
目前來看,鋰電行業主要有三大痛點:
1、質量&成本
電芯加工工序對生產環境有較高要求,粉塵、水分等因素會影響電芯的產品一致性;原材料價格的不斷升高,產能快速擴張且勞動強度大,造成招工難、用工成本高;物料在不同工序轉運,人工接觸風險較高,物料報廢造成大量成本損失。
2、效率&安全
前工序卷料重、種類多,上下料對接難度大,機臺上料時需要多個工人同時完成;工藝路線復雜,物料搬運任務難以有效管控,造成產量及節拍損失;地面有碳粉容易打滑,物流通道狹窄,人機混行有安全隱患。
3、物料管理
各工序之間緩存物料多,沒有實時庫存數據,需要人工定期盤點;倉庫按照ERP計劃批量出庫,與產線需求有差異,造成緩存區爆庫;線邊緩存架位置分散,沒有上下架指示,造成產線與所需物料距離較遠。
針對此,極智嘉正在嘗試通過機器人打造各類解決方案。近日,由高工機器人、高工鋰電、高工咨詢聯合主辦的“2021鋰電池智能制造峰會”在智能物流專場上,極智嘉全球供應鏈解決方案總監曹曉剛發表題為“智能機器人助力鋰電制造柔性升級”的演講。
他分析,鋰電行業解決方案包括倉儲和加工兩部分,具體來看,原材料經過一系列的加工形成電芯產品。電芯進入模組車間形成模組,最終組成PACK,即電池包。其間的多項工序為移動機器人提供了用武之地,如前工序中的攪拌、涂布、輥壓、分切等環節粉料搬運、銅鋁箔搬運、卷料搬運;在中段,前工序制好的極卷極片可以通過機器人搬運到卷繞機或者疊片機上,電芯也可以通過機器人搬運到下一個庫存環節。在模組車間的電芯上線、原材料上線、包材上線、模組下線,以及PACK車間的箱體上線、模組上線、原材料上線、PACK下線等都是移動機器人的應用場景。
原材料搬運解決方案
在原材料搬運解決方案中,面臨的場景是原材料立庫出庫搬運至線邊庫、陰陽極粉料配送、陰陽極基材配送、空托盤堆垛,極智嘉提供的解決方案是AMR替代人工叉車搬運,運用的產品包括最大負載1000kg的潛伏頂升機器人M1000R和負載1.4噸的無人叉車F14L,這些SLAM激光導航產品的運行不受地面粉塵影響,不同型號的AMR可以互相安全避讓,因而搬運托盤更精準、更安全。此外,上位系統直接下發任務,搬運系統就近安排空閑的機器人執行任務,由原材料庫向緩存架補料、同時緩存架向投料口送料。
曹曉剛通過視頻進一步展示了無人叉車實際運行的狀況,無人叉車可以對接立庫輸送線,配送產線線邊庫,可以將空托盤自動堆疊回庫,此外無人叉車還具備自動進出電梯、前向及側向、貨叉方向的激光避障等功能。
涂布/輥壓搬運解決方案
在涂布/輥壓搬運解決方案中,面對的場景是拆包間出庫、緩存架存取、涂布上料/下料、輥壓上料/下料、分切上料。極智嘉提供的解決方案是AMR替代叉車及手推料車;搬運系統與MES、上位機進行數據交互,機器人可以自動完成機臺上下料、緩存架存取、工序轉運等一系列任務,物料流轉自動化率可達100%,信息可追溯;雙舉升結構一次搬運就可完成空滿料卷的更換,1臺機器人可以替換4個物流工人(雙班),ROI小于2年。
該項目中運用到的AMR為雙舉升定制型機器人,對接精度可達±1mm,可適配1100~1750mm之間各種尺寸的料軸,可按實際需求定制;具備360°激光避障、高空及低矮障礙物避障、360°防撞觸邊等最高安全性能。
在某國內鋰電池制造企業中已使用了這款產品,客戶的痛點是由于物料重量達3噸,人工搬運困難,容易產生磕碰料廢;上下料對接精度要求高(±1mm);地面掉落碳粉容易滑倒,通道狹窄有安全隱患。
為了解決這一難題,客戶在前工序涂布、輥壓、模切等工序已投入了30臺雙舉升定制型機器人來對接WMS、MES以及上位機,實現全自動化的生產物流過程,通過系統管理庫存,自動盤點、理貨。狀態監控及數據統計,包括效率分析、故障分析等。同時,機器人還可以與立庫、輸送線、電梯、卷簾門等設備智能交互。
總體而言,該項目實現全無人化物料搬運及設備對接,工藝路線靈活可調,節省物流工人120人(雙班),項目整體ROI小于2年。
極卷搬運解決方案
接下來,曹曉剛分享了極卷搬運解決方案,該方案面對的場景包括模切下線、極卷出入庫和卷繞上線。該方案運用的AMR產品為單懸臂定制型機器人,可替代人工推車搬運,可實現360°激光避障,停止精度為±5mm,定位精度達±1mm,懸臂車與卷繞機直接對接完成上料任務。
料箱/料盤搬運解決方案
料箱/料盤搬運解決方案則主要是應對后工序彈匣、Tray盤搬運,以及機臺、輸送線對接和轉運,該方案運用M1000R結合電動輥筒替代手推車搬運,可按照料箱尺寸定制不同的輥筒尺寸,雙排輥筒可以連續取兩箱物料以提高搬運效率。輥筒與輸送線高度保持一致,可直接對接輸送線并取送物料。
模組生產解決方案
曹曉剛進一步介紹了模組生產解決方案,相對來說,模組生產的自動化率較高,潛伏式AMR M1000R可實現原材料上料的無人化配送,在這過程中,揀料工位呼叫機器人搬運空料車作業,隨后機器人按照配料單的配送地址依次在線邊工位停靠,線邊工人取消后機器人行進到下一工位。叉車式AMR F20T/F20MT則可以實現電芯成品上料、包材上料、模組成品下線等的無人化配送。該方案中不同型號的機器人可以互相避讓,保證安全。
極智嘉的系統解決方案向上可以連接企業的MES系統、機臺上位機,向下可以控制機器人進行智能運作,并與數據管理平臺(DMP)和各種外部設備,如提升機、風淋門、卷簾門、緩存架等實現對接。
通過后臺數據的分析,可以對充電效率、機器人運行效率,工廠整體稼動率等進行分析,同時提供單據、任務、物料、機器人等看板,為企業管理人員以及現場操作人員提供更直接化的數據展示。
價值實現
最后,曹曉剛表示,極智嘉的愿景是成為全球領先的人工智能和機器人公司,打造智慧物流的基礎設施和服務網絡,幫助客戶與合作伙伴實現數字化和智慧化的敏捷供應鏈。
發展至今,極智嘉已擁有員工超1000人,在南京和鹽城的兩個自有工廠年產能超萬臺,其中2019年首次對外開放的南京智慧工廠,是世界首座使用機器人自動生產自主移動機器人(AMR)的智慧工廠。
目前,極智嘉的專利公開累計超400件,擁有超300家全球大客戶,移動機器人全球部署超10,000臺。其全品類物流機器人系統包括貨架到人系統、貨箱到人系統、訂單到人系統、智能分揀系統、智能搬運系統、智能叉車系統等。
在軟硬件方面,極智嘉關注安全,打造可靠的硬件基礎,如采用CNC高強度合金鋁,其機械零件經過50萬次的嚴格測試,電池防火設計通過日本最嚴認證,Wifi 通過Cisco認證,整機通過CE認證等,同時打造了機器人平臺Matrix、軟件平臺 WES & RMS、算法平臺 HyperX,從而賦能智能倉儲與柔性制造。
在全球服務能力方面,極智嘉可實現線上問題響應時間小于10分鐘,全球服務超20個國家及地區,中英文技術支持7*24小時全天候響應客戶,已建立全球備件中心1個,國內備件倉4個,海外備件中心8個。
“極智嘉致力于為企業創造真正的價值,塑造競爭力,增強反脆弱力。伴隨著鋰電行業產能的不斷擴張,智能機器人則可以助力鋰電行業柔性升級,實現高投資回報率、高可靠性、高敏捷性,為整個供應鏈優化提供最全面的數據驅動智能決策支持,讓企業以‘智’為伴,從容應對市場的風云變幻。”曹曉剛說道。
責任編輯:lq6
-
鋰電池
+關注
關注
260文章
8176瀏覽量
171383 -
動力電池
+關注
關注
113文章
4549瀏覽量
77894 -
機器人
+關注
關注
211文章
28632瀏覽量
208198 -
電芯
+關注
關注
14文章
732瀏覽量
25954
發布評論請先 登錄
相關推薦
【「具身智能機器人系統」閱讀體驗】2.具身智能機器人的基礎模塊
【「具身智能機器人系統」閱讀體驗】2.具身智能機器人大模型
【「具身智能機器人系統」閱讀體驗】1.全書概覽與第一章學習
高工年會 守正創新開新局 助力國產機器人競爭力
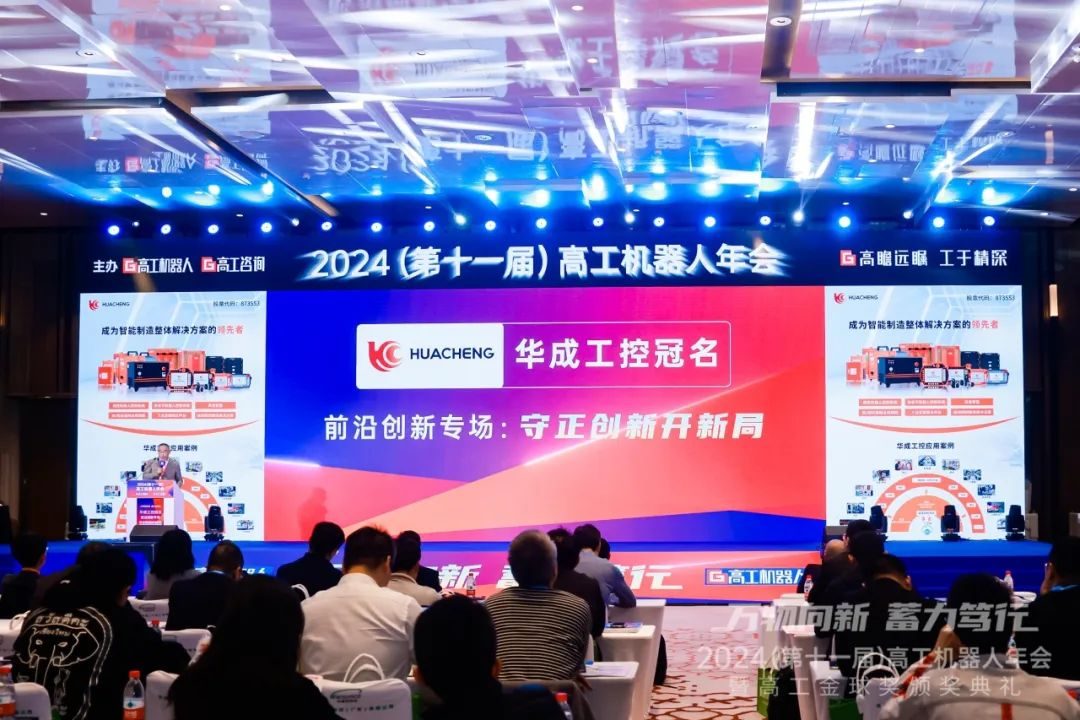
《具身智能機器人系統》第1-6章閱讀心得之具身智能機器人系統背景知識與基礎模塊
使用NVIDIA Jetson打造機器人導盲犬
使用機器學習和NVIDIA Jetson邊緣AI和機器人平臺打造機器人導盲犬
光伏清潔機器人4G之痛,LoRa通訊取而代之?
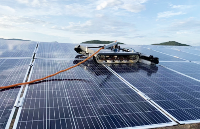
供應 英集芯IP2348,適用于掃地機器人解決方案的鋰電池同步降壓充電芯片
Al大模型機器人
abb機器人home點設置方法
其利天下技術·搭載無刷電機的掃地機器人的前景如何?
工業智能機器人以其卓越的技術和創新能力,正引領著行業的升級與變革
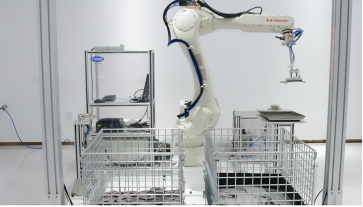
評論