摘要
利用圖像處理與機(jī)器視覺技術(shù)開發(fā)了一套安全氣囊檢測系統(tǒng),實(shí)現(xiàn)了對安全氣囊生產(chǎn)過程某一工位處關(guān)鍵尺寸的亞像素測量。介紹了該檢測系統(tǒng)的總體組成和主要工作流程; 分別介紹了該系統(tǒng)的軟硬件設(shè)計(jì); 并選取實(shí)際氣囊對所開發(fā)的檢測系統(tǒng)進(jìn)行了可行性、有效性的驗(yàn)證。通過實(shí)驗(yàn)表明該系統(tǒng)的檢測結(jié)果符合實(shí)際生產(chǎn)的要求。
21 世紀(jì)以來,汽車行業(yè)發(fā)展迅猛。安全氣囊作為汽車的安全輔助工具,它的出現(xiàn)大大降低了死亡率,因而必須確保其尺寸精確,并能正常使用。對安全氣囊傳統(tǒng)的檢 測方法主要是借助千分表、輪廓儀等工具進(jìn)行人工抽檢[1]。然而在長時(shí)間、大批量的工作模式下,工作人員由于身體條件、視覺疲勞等因素,造成產(chǎn)品誤檢率高,極大地 限制了生產(chǎn)效率和產(chǎn)品質(zhì)量。
針對上述情況,開發(fā)了一套基于機(jī)器視覺的安全氣囊檢測系統(tǒng),實(shí)現(xiàn)對安全氣囊關(guān)鍵尺寸的亞像素測量。該系統(tǒng)具有非接觸、實(shí)時(shí)、高精度、高效率的特點(diǎn),可有效降低企業(yè)的人工成本,同時(shí)減少誤檢率和漏檢率,提高企業(yè)的生產(chǎn)效率和經(jīng)濟(jì)效益。
1
視覺檢測系統(tǒng)設(shè)計(jì)
1.1 尺寸測量技術(shù)要求
待檢測對象安全氣囊的實(shí)物圖如圖 1 所示。對氣囊進(jìn)行檢測主要是對其外輪廓尺寸大小和預(yù)縫線間距進(jìn)行測量,具體要求如下: (1)對氣囊外輪廓尺寸進(jìn)行測量,測量誤差范圍為±0.5 mm。 (2) 對預(yù)縫線間距進(jìn)行測量,測量誤差范圍為±0.5mm。 針對以上需求,設(shè)計(jì)并開發(fā)了一套基于機(jī)器視覺的氣囊尺寸檢 測系統(tǒng)。示例中的氣囊外輪廓尺寸為 205.55mm,預(yù)縫線間距為 140.16 mm。
圖 1 待檢測的安全氣囊實(shí)物圖
1.2 系統(tǒng)的工作原理
視覺檢測系統(tǒng)主要由光源、相機(jī)、計(jì)算機(jī)、執(zhí)行機(jī)構(gòu)等部分組合而成[2],如圖 2 所示。其工作原理是: 照明光源發(fā)出平行光照射在檢測工件上,工業(yè)相機(jī)采集圖像,將光信號(hào)轉(zhuǎn)換成圖像數(shù)據(jù)傳送給計(jì)算機(jī),由計(jì)算機(jī)完成圖像處理、分析和計(jì)算等,并將處理結(jié)果以信號(hào)的形式發(fā)送給執(zhí)行機(jī)構(gòu),指導(dǎo)機(jī)器的運(yùn)行。
1.3 系統(tǒng)的結(jié)構(gòu)設(shè)計(jì)
該視覺系統(tǒng)的結(jié)構(gòu)設(shè)計(jì)主要從硬件系統(tǒng)和軟件系統(tǒng)兩方面展開。
圖 2 視覺檢測系統(tǒng)的原理圖
硬件系統(tǒng)包含機(jī)械裝置、圖像采集子系統(tǒng)以及計(jì)算機(jī)等部分,其中圖像采集子系統(tǒng)是整個(gè)硬件系統(tǒng)的核心模塊,由光源、相機(jī)以及照明系統(tǒng)等復(fù)合而成,其任務(wù)是對工件進(jìn)行圖像數(shù)據(jù)采集[3]。對圖像采集子系統(tǒng)的設(shè)計(jì)主要從相機(jī)和光源的選型、光照模式的設(shè)計(jì)等兩個(gè)方面入手。根據(jù)檢測工件的表面屬性和幾何外形,結(jié)合檢測指標(biāo)為外輪廓尺寸和預(yù)縫線間距測量,決定選用 MER- 503- 20GM / C-P 相機(jī),選擇線性 LED 條形光源,以垂直照射的方式進(jìn)行照明,如圖 3( a) 所示。
軟件系統(tǒng)是基于 Window 操作系統(tǒng)平臺(tái),依托 Visual Studio 2013 中 MFC 和開源圖像處理庫 OpenCV2.4.9 設(shè)計(jì)的 UI 界面,主要包括視頻顯示、圖像結(jié)果顯示、識(shí)別與測量及設(shè)備控制等功能模塊,如圖 3( b) 所示。圖中左側(cè)兩個(gè)窗口分別為“視頻顯示窗口”和“圖像結(jié)果顯示窗口”;界面右側(cè)從上到下依次是“串口通信窗口”、“設(shè)備控制窗 口”、“檢測識(shí)別與測量窗口”以及“檢測結(jié)果顯示窗口”。
圖 3 檢測系統(tǒng)的結(jié)構(gòu)設(shè)計(jì)
2
檢測原理與算法實(shí)現(xiàn)
針對氣囊的尺寸測量,采用基于灰度圖像的邊緣特征,通過濾波與增強(qiáng),改善圖像質(zhì)量,銳化邊緣細(xì)節(jié),并通 過亞像素定位技術(shù),提高邊緣定位精度,最后通過對邊緣 的直線擬合和直方圖投影,進(jìn)行尺寸測量,整個(gè)檢測算法 流程如圖 4 所示。
圖 4 氣囊尺寸測量算法流程圖
2.1 圖像濾波
在進(jìn)行圖像采集和數(shù)據(jù)傳輸時(shí),因受到圖像傳感器質(zhì)量、環(huán)境光照等因素的影響,常常會(huì)引入無關(guān)的噪聲,不利于后續(xù)圖像識(shí)別。圖 5 所示為采集圖像的外輪廓和預(yù)縫線區(qū)域的局部圖,可以看出圖像含有大量的噪聲點(diǎn)。
圖 5 原始圖像
在圖像處理中,主要運(yùn)用圖像濾波進(jìn)行噪聲點(diǎn)的去除。目前,常用的濾波方法有高斯濾波、均值濾波和中值 濾波等。采用上述 3 種濾波方法分別對工件圖像進(jìn)行處理,同時(shí)以峰值信噪比( PSNR)[4]作為質(zhì)量評(píng)價(jià)指標(biāo),最終決定采用高斯濾波對圖像進(jìn)行去噪處理。
高斯濾波是一種廣泛使用的線性平滑濾波器,主要思路是對整幅圖像進(jìn)行加權(quán)平均,從而消除噪聲點(diǎn)的影響, 其具體操作是: 通過高斯核的離散化窗口滑窗卷積來實(shí)現(xiàn),高斯核是一個(gè)奇數(shù)的大小高斯模板。
高斯模板中的各個(gè)參數(shù)主要通過二維高斯函數(shù)計(jì)算給出,其具體公式如下:
式中 δ 表示標(biāo)準(zhǔn)差。標(biāo)準(zhǔn)差 δ 越小,表示濾波平滑效果越不明顯。
采用高斯濾波對采集圖像進(jìn)行噪聲點(diǎn)的去除,效果如 圖 6 所示,可以看到噪聲點(diǎn)被平滑處理掉,圖像質(zhì)量得到明顯改善。
圖6 高斯濾波后的圖像
2.2 圖像增強(qiáng)
經(jīng)過高斯濾波之后的圖像,噪聲點(diǎn)被濾除,但是由于引入平均的效果,使得邊緣細(xì)節(jié)變得模糊。為了抵消這種模糊的因素,應(yīng)該增強(qiáng)圖像的對比度。采用 Laplace 算子, 對圖像邊緣進(jìn)行銳化處理。
Laplace 算子是一種各向同性的二階微分算子[5],而圖像的邊緣灰度是階躍變化的,在數(shù)學(xué)上表示為其二階導(dǎo)數(shù)過零點(diǎn),故可利用 Laplace 算子對進(jìn)行圖像銳化,可以有效地定位邊緣點(diǎn),并通過加強(qiáng)邊緣的灰度值,使圖像的對 比度增強(qiáng),同時(shí)使邊緣細(xì)節(jié)得到提升。
如圖 7 所示,經(jīng)過 Laplace 算子增強(qiáng)后,可以發(fā)現(xiàn)圖像的對比度得到了提高,預(yù)縫線和外輪邊緣也更加清晰,有利于后續(xù)圖像邊緣的檢測。
圖7 Laplace 圖像增強(qiáng)后的效果
2.3 邊緣檢測
圖像邊緣指的是其周圍像素灰度急劇變化的那些像 素的集合,它主要存在于目標(biāo)、背景與區(qū)域之間,對圖像進(jìn) 行邊緣檢測是圖像識(shí)別的重要步驟[6]。采用亞像素技術(shù) 對像素級(jí)邊緣進(jìn)行精細(xì)再分,提高了圖像的分辨率,具體 實(shí)現(xiàn)過程如下:
(1)粗定位階段,以像素為單位,進(jìn)行傳統(tǒng)的邊緣檢測;
(2)精定位階段,采用圖像處理算法,實(shí)現(xiàn)像素精細(xì)劃分。在粗定位階段,傳統(tǒng)的像素級(jí)邊緣檢測算子主要有:
Roberts 算子、Prewitt 算子、Sobel 算子、Log 算子、Canny 算子等[7]。從定位精度和邊緣細(xì)節(jié)兩方面,對比上述檢測算子的檢測效果,如圖 8 所示,可以發(fā)現(xiàn) Roberts 算子、Prewitt 算子、Sobel 算子檢測結(jié)果相似,能夠準(zhǔn)確定位邊緣,但是邊緣細(xì)節(jié)模糊,而 Canny 算子檢測效果最佳,定位精度高,邊緣連續(xù)性強(qiáng),故在粗定位階段采用 Canny 算子進(jìn)行邊緣檢測。
在精定位階段,采用基于 Zernike 矩的亞像素邊緣檢測算法,并對階躍閾值的選擇進(jìn)行改進(jìn),利用 Otsu 法( 大津法) 確定最佳分割閾值 T 作為階躍閾值,對檢測邊緣進(jìn)行精確定位。
改進(jìn)的 Zernike 矩邊緣檢測算法具體步驟如下。步驟 1: 計(jì)算 Zernike 矩的 Z00、Z11、Z20;
步驟2: 根據(jù)公式( 2) ,計(jì)算出Φ的值;
Φ= tan-1( Im[Z11]/Re[Z11]) ( 2)
步驟3: 利用Zernike 矩的旋轉(zhuǎn)不變性,求得Z'00、Z'11、Z'20;
步驟5: 利用Otsu 法確定最佳分割閾值作為階躍閾值 T; 步驟 6: 取距離閾值 δ,若滿足條件 k ≥T 且 h≤δ,則該像素點(diǎn)即為邊緣點(diǎn)。
通過 Otsu 法確定最佳分割閾值 T = 86,并設(shè)置距離閾值 δ 為一個(gè)像素單位,進(jìn)行亞像素邊緣檢測,如圖 9 所示。可以看出采用改進(jìn)的 Zernike 矩邊緣檢測算法提取的圖像邊緣無毛刺,且連續(xù)性更強(qiáng),為后續(xù)的高精度尺寸測量提供了保證。
圖9 改進(jìn)的Zernike 矩邊緣檢測效果圖
2.4 尺寸測量
通過對氣囊的邊緣圖像進(jìn)行分析,發(fā)現(xiàn)外輪廓具有波 浪形邊緣,而預(yù)縫線邊緣具有明顯的傾斜角度,并且含有 線頭邊緣,對測量產(chǎn)生極大的干擾,針對以上問題,分別提 出了基于直線擬合和直方圖投影的測量算法,檢測效果如 圖 10 所示。
圖 10 氣囊尺寸測量效果圖
1)直線擬合測量算法
對于外輪廓的尺寸測量,其核心步驟在于對輪廓的擬 合,最小二乘法是最常見的直線擬合方法,其具體步驟如下。
步驟 1: 采集圖像上、下邊緣,采用最小二乘法擬合基準(zhǔn)直線 L1 和 L2;
步驟 2: 計(jì)算中心點(diǎn)( x0,y0) ,將上邊緣 x 坐標(biāo)均值作為 x0,根據(jù)直線 L2方程獲取中心點(diǎn)位置;
步驟 3: 利用該中心點(diǎn)的基準(zhǔn)直線 L1的距離,進(jìn)行測距。
2)直方圖投影算法
首先對工件的邊緣圖像進(jìn)行輪廓提取,同時(shí)獲得每個(gè)輪廓的最小外接矩形,再依據(jù)面積和長寬比等幾何特征, 定位預(yù)縫線檢測區(qū)域 R1和 R2,并記錄其左上角頂點(diǎn)坐標(biāo),如圖 10 所示。
對定位出的預(yù)縫線區(qū)域,進(jìn)行直方圖投影,其具體步驟是: 首先遍歷 ROI 區(qū)域 R1和 R2,統(tǒng)計(jì)區(qū)域內(nèi)非 0 值像素的個(gè)數(shù) Ni,以行數(shù)為橫坐標(biāo),Ni 為縱坐標(biāo),繪制直方圖,并記錄直方圖最大值所在位置行數(shù),計(jì)為 I1max 和 I2max,如圖 11 所示。結(jié)合 ROI 區(qū)域的位置坐標(biāo),作差即可求得預(yù)縫線間距。
圖11 預(yù)縫線像素直方圖
3
實(shí)驗(yàn)結(jié)果與分析
對本視覺系統(tǒng)進(jìn)行重復(fù)性測量實(shí)驗(yàn),即將氣囊在相機(jī)視野中任意位置擺放 10 次,采用檢測系統(tǒng)對氣囊進(jìn)行尺寸測量,并計(jì)算其測量均值和標(biāo)準(zhǔn)差,測量結(jié)果如表 1 所示。
通過表 1 可知,外輪廓測量均值為 205.55 mm,其標(biāo)準(zhǔn)偏差為 0.0317 mm,預(yù)縫線間距測量均值為 140.15 mm,標(biāo)準(zhǔn)偏差為 0.023 5 mm,標(biāo)準(zhǔn)偏差均在± 0.05 mm 之間,滿足了生產(chǎn)實(shí)際的精度要求。同時(shí)為了更加直觀體現(xiàn),繪制其檢測結(jié)果折線圖如圖 12 所示。
圖12 零件檢測結(jié)果折線圖
由圖 12 可知雖然該系統(tǒng)測得的數(shù)據(jù)整體比較理想, 測量結(jié)果基本在測量均值附近,但是也有個(gè)別數(shù)據(jù)會(huì)產(chǎn)生波動(dòng),出現(xiàn)這種情況,主要有以下幾個(gè)方面原因:
鏡頭誤差。由于鏡頭制造工藝的限制,使得鏡頭存在畸變,在光學(xué)成像時(shí)產(chǎn)生一定的誤差。
環(huán)境誤差。受到環(huán)境光照的影響,使得被測工件的邊緣亮度和陰影產(chǎn)生變化,這將導(dǎo)致在邊緣提取時(shí)產(chǎn)生 一定的誤差。
算法誤差。對外輪廓進(jìn)行直線擬合時(shí),由于輪廓具有波浪形邊緣,使得擬合出的結(jié)果會(huì)存在一定的誤差。
4
結(jié)論
根據(jù)安全氣囊安全尺寸的檢測要求,開發(fā)了一套視覺檢測系統(tǒng),該系統(tǒng)采用改進(jìn)的Zernike 矩的亞像素邊緣算法,實(shí)現(xiàn)邊緣的精確定位,提高了測量精度。針對工件兩個(gè)不同的測量指標(biāo),分別提出了基于直線擬合的點(diǎn)測距和基于直方圖投影測距的測量方法。在實(shí)例驗(yàn)證下, 檢測精度符合工業(yè)生產(chǎn)要求,有效地提高了生產(chǎn)效率和產(chǎn)品質(zhì)量。
參考文獻(xiàn)
[1] 季瑩. 安全氣囊的技術(shù)現(xiàn)狀與發(fā)展趨勢[J]. 汽車與配件,2012( 10) : 34-37.
[2] WESLEY E,SNYDER,HARIONG Qi. Machine vision[M]. Camb: Cambridge University Press,2005.
[3] 章煒. 機(jī)器視覺技術(shù)發(fā)展及其工業(yè)應(yīng)用[J]. 紅外技術(shù),2006,27( 2) : 11-16.
[4] 劉國陽. 基于機(jī)器視覺的微小零件尺寸測量技術(shù)研究[D].哈爾濱: 哈爾濱工業(yè)大學(xué),2014.
[5] 周文舉. 基于機(jī)器視覺的在線高速檢測與精確控制研究與應(yīng)用[D]. 上海: 上海大學(xué),2013.
[6] 左敦穩(wěn). 視覺技術(shù)在智能機(jī)械加工中的應(yīng)用研究[J]. 機(jī)械制造與自動(dòng)化,2018,47( 6) : 1-6.
[7] 汪田. 基于機(jī)器視覺的油泵殼體尺寸測量系統(tǒng)[D]. 杭州: 浙江大學(xué),2018.
責(zé)任編輯:xj
原文標(biāo)題:基于機(jī)器視覺的安全氣囊檢測系統(tǒng)研究
文章出處:【微信公眾號(hào):新機(jī)器視覺】歡迎添加關(guān)注!文章轉(zhuǎn)載請注明出處。
-
機(jī)器視覺
+關(guān)注
關(guān)注
162文章
4375瀏覽量
120357 -
安全氣囊
+關(guān)注
關(guān)注
1文章
72瀏覽量
18802 -
亞像素
+關(guān)注
關(guān)注
0文章
4瀏覽量
6716
原文標(biāo)題:基于機(jī)器視覺的安全氣囊檢測系統(tǒng)研究
文章出處:【微信號(hào):vision263com,微信公眾號(hào):新機(jī)器視覺】歡迎添加關(guān)注!文章轉(zhuǎn)載請注明出處。
發(fā)布評(píng)論請先 登錄
相關(guān)推薦
應(yīng)用在汽車控制系統(tǒng)安全氣囊的愛普生可編程晶振SG-8018CG
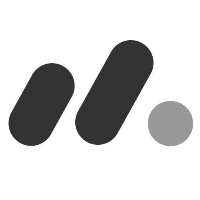
視覺檢測是什么意思?機(jī)器視覺檢測的適用行業(yè)及場景有哪些?
機(jī)器視覺在焊接質(zhì)量檢測中的應(yīng)用
什么是機(jī)器視覺opencv?它有哪些優(yōu)勢?
機(jī)器視覺檢測系統(tǒng)的關(guān)鍵技術(shù)和應(yīng)用場景
圖像檢測與識(shí)別技術(shù)的關(guān)系
基于FPGA EtherCAT的六自由度機(jī)器人視覺伺服控制設(shè)計(jì)
AI視覺檢測系統(tǒng)在多方面實(shí)現(xiàn)技術(shù)創(chuàng)新
山子高科旗下美國ARC持續(xù)創(chuàng)新,安全氣囊技術(shù)引領(lǐng)行業(yè)風(fēng)向標(biāo)
安全氣囊新篇章:美國ARC公司與延鋒汽車達(dá)成戰(zhàn)略合作
機(jī)器視覺中圖像采集卡的功能與應(yīng)用
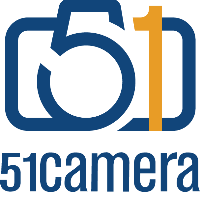
機(jī)器視覺圖像采集卡:關(guān)鍵的圖像處理設(shè)備
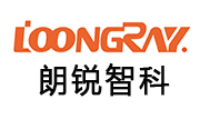
評(píng)論