小缸徑柴油機通常采用2氣門缸蓋和噴油器非中心布置的形式,以擴展氣道的流通面積。與缸徑相當的采用4氣門、噴油器中心布置的氣缸蓋相比,這種噴油器非中心布置會產生不對稱的氣體流動和燃油分布,從而導致糟糕的熱損失和不太均勻的燃空混合氣。介紹通過改進活塞頂燃燒室的幾何形狀來實現更均勻的氣體流動和燃空混合氣。新方案燃燒室與原有的活塞燃燒室相比,能使燃油消耗減少2.5%,同時還能使氮氧化物排放量減少10%左右。 關鍵詞:燃燒室熱損失淺凹坑高負荷
0前言
為了有助于解決諸如全球變暖和污染等環境問題,以及減輕人們對能源缺乏的憂慮,汽車制造商正面臨著開發出燃油耗更少和有害氣體排放更低的汽車的挑戰。采用高效率柴油機是減少乘用車燃油耗的1種有效途徑。然而,由于柴油機需要采用昂貴的燃油噴射和后處理系統,來滿足更清潔排放的要求,因此,系統的成本是阻礙這種發動機被廣泛應用的因素之一。由于小排量(即小缸徑)柴油機質量相對較輕,易于安裝,因而頗受歡迎。這種發動機有助于實現更高的燃油耗收益。然而,小缸徑柴油機通常采用1個進氣門和1個排氣門的設計,以擴大進氣道的流通面積(即采用2氣門缸蓋設計)和噴油器非中心布置。這種設計會對氣缸內氣體流動和燃油分布產生不利影響,從而使得燃燒的改進更難以實現。此外,小缸徑柴油機較大的氣缸內表面積和容積意味著燃油噴束的貫穿距離相對較大。結果是,燃燒區靠近缸壁,從而導致冷卻損失要比大缸徑柴油機的高(圖1)。
圖1 能量細分比較(平均有效壓力(IMEP)0.4 MPa,氮氧化物(NOx) 0.2 g/(kW·h))
本文介紹的研究旨在開發1種能同時降低冷卻損失和提高小排量柴油機氣缸內混合氣分布均勻性的新燃燒室方案,以幫助改善燃油消耗,且不降低發動機性能。
1 通過擴大燃燒室直徑減少冷卻損失
冷卻損失(熱通量)由以下公式計算
Qw=α·ΔT
式中,α是傳熱系數,ΔT是燃燒氣體與壁面之間的溫度差。這表明冷卻損失隨傳熱系數線性降低,因而可以通過限制近壁面的流速和燃燒氣體與壁面之間的溫度梯度來降低冷卻損失。為了實現上述2個目標,采用了1種大直徑淺凹坑的燃燒室形狀。如圖2所示,該設計減少了燃燒室內的渦流速度和擠流速度。此外,較大的直徑確保了噴油嘴與燃燒室壁之間有適當的距離。保持高溫燃氣近一步遠離壁面也有助于減少與壁面的溫度差。
圖2 燃燒室凹坑邊緣處氣缸內擠流速度和渦流速度的比較(零維模擬)
2 試驗發動機
表1所示為試驗發動機的規格。首先,采用1臺缸徑、行程和氣道渦流比與多缸發動機相同的單缸機,對3種不同燃燒室的燃燒特性進行試驗研究。然后,在1臺多缸發動機上安裝新方案活塞來驗證燃燒效果。圖3所示為多缸發動機的結構布置。這款發動機以目前歐洲汽車采用的豐田汽車公司1.34 L 1ND發動機為基礎。為了進行這些試驗,更改了活塞頂燃燒室的幾何形狀和廢氣再循環(EGR)系統。利用AVL 450噪聲儀測得的氣缸內壓力計算燃燒噪聲,使用AVL 415煙度計測量排氣煙度,由公式(2)~(5)計算能量損失。首先,通過定容度(DCV)計算排氣損失;然后,由燃油化學能減去指示功、排氣損失和未燃損失計算冷卻損失。
表1 發動機主要規格
圖3 多缸發動機示意圖
Qex=Wi·((1-η)η)
η=ηth·DCV
ηth=1-(1-gκ-1)
Qcooling=Qfuet-Wi-Qunburn-Qex
式中,Qex是排氣損失,η是循環效率,ηth是理論效率,ε是壓縮比,κ是比熱比,DCV是定容度,Qcooling是冷卻損失,Qfuel是燃油能量,Wi是指示功,Qunburn是由總碳氫(THC)、CO和煙度排放量計算而得的未燃燒損失。
3 大直徑燃燒室的效果
圖4對傳統深凹坑燃燒室和推薦的淺凹坑燃燒室在低負荷(IMEP 260 kPa)時的單缸機測量結果(污染物排放、冷卻損失、氣缸壓力和放熱率曲線)進行了比較。由于冷卻損失降低了8%,淺凹坑燃燒室的指示比油耗比常規燃燒室的低1.2%。這是由于燃燒室凹坑內渦流速度和擠氣速度較低,導致傳熱系數降低而得以實現。圖5比較了高負荷(IMEP 1000 kPa)下的相同結果。與低負荷情況類似,冷卻損失降低了6%,指示比油耗減少了0.9%,然而,煙度增加了0.3 FSN。為了查明煙度排放惡化的原因,通過傳統深凹坑燃燒室和淺凹坑燃燒室的三維計算流體動力學(3D-CFD)計算對氣缸內當量比分布進行了分析。從圖6結果可以清楚地看出,與淺凹坑燃燒室相比,深凹坑燃燒室中初始混合氣的擴散更好,并能通過逆擠流作用排出燃燒室。淺凹坑燃燒室的當量比相對較大是造成上述差異的原因。這是導致淺凹坑燃燒室在高負荷時煙度排放增加的關鍵因素。
圖4 淺凹坑燃燒室的效果(1 800r/min, IMEP 260 kPa, EGR工作,噴射模式2次預噴+主噴,燃燒噪音79±0.2 dB)
圖5 淺凹坑燃燒室的效果(2 000r/min, IMEP1 000 kPa, EGR工作,噴射模式2次預噴+主噴+1次后噴,燃燒噪音88±0.2 dB)
圖6 由STAR-CD計算的氣缸內當量比分布(轉速2000 r/min, IMEP 1000 kPa)
這些結果證實,盡管簡單地采用淺凹坑燃燒室能依靠降低冷卻損失來降低燃油耗,但是它難以同時確保適當的混合氣擴散。
4 通過限制氣流速度促進混合氣擴散
通過限制氣流速度促進混合氣形成的1種減小噴孔直徑并增加噴孔數的方法。然而,在小排量柴油機上采用這種方法會產生因液流速度較低而導致沉積物阻塞噴嘴孔的風險。因此,開發了1種能促進小排量柴油機更好地形成混合氣的不同方法。為了促進混合氣擴散,同時通過限制氣缸內流速降低冷卻損失,設計了新的燃燒室。圖7和圖8所示分別為常規燃燒室和設計燃燒室。新方案燃燒室有1個與無唇口淺凹坑相連的斜坡。燃燒室凹坑從氣缸中心向右偏移,其偏置量與噴油器的偏置量保持一致。斜坡表面相對于燃燒室凹坑向左偏置。這種設計是為了使淺凹坑燃燒室中的富油混合氣快速擴散到燃燒室外部。燃燒室和凹坑中心與斜坡表面彼此偏移,以使它在圖中左邊擠流區的斜度達到最大。與常規的深凹坑燃燒室相比,這具有抑制擠流的作用。它還能使混合氣沿斜坡表面向含有殘余空氣的大容積擠流區擴散,從而增加了空氣利用率。此外,去除燃燒室唇口能減少低負荷時因燃燒室唇口沉積燃油而造成THC排放,因此,假設不會增加THC排放,新方案燃燒室能使壓縮比從16.9下降到16.4。此外,降低壓縮比能使氣缸內氣體密度降低,因而能進一步促進混合氣的擴散。
采用1臺高速照相機從單缸發動機的側面觀測了斜坡對混合氣擴散的影響。圖9為觀測到的結果。在傳統縮口型燃燒室的情況下,燃燒室凹坑中產生發光火焰后,在混合氣燃燒后期會隨著強烈的逆擠流擴散到燃燒室凹坑的外部。這種混合氣狀態會增加冷卻損失,因為強烈的逆擠流會導致較高的氣流速度。相反,在有斜坡的燃燒室中,發光火焰從燃燒開始就沿著斜坡表面擴散到燃燒室凹坑外部。斜坡形狀可以使混合氣在無強烈逆擠流的情況下擴散,這樣就能減少冷卻損失。
圖10是新方案燃燒室在低負荷下(IMEP260 kPa)的污染物排放、燃油耗、冷卻損失、氣缸壓力和放熱率隨時間變化的測量結果。盡管壓縮比較低,但新方案燃燒室減少了未燃THC的排放量。這是因為加大燃燒室直徑和去除唇口能抑制燃油在凹坑內沉積。這樣的設計與簡單的淺凹坑設計相比,在減少冷卻損失方面更為有效。因此,由于冷卻損失減少了23%,該設計能使有效比油耗減少約4-5%。圖11顯示了氣缸內氣體流速的3D-CFD分析結果。傳統縮口形燃燒室會在左側產生圍繞唇口朝向擠流區的強烈逆擠流。與此相反,在新方案燃燒室的這個位置上,較大的斜坡限制了氣體流速。這種氣體流速的減少降低了傳熱系數,進而減少了冷卻損失。
圖7 常規燃燒室形狀
圖8 新方案燃燒室形狀
圖9 燃燒室斜坡的影響(轉速2000r/min,IMEP 1.4 MPa)
圖10 新方案燃燒室的效果(轉速1 800 r/min,IMEP0.26 MPa, EGR工作)
圖11 由STAR-CD計算而得的氣缸內氣體速度分布(轉速1800 r/min,IMEP 0.26 MPa)
圖12所示為高負荷(IMEP1000 kPa)下的結果。采用新方案燃燒室后能使簡單淺凹坑燃燒室的煙度排放得以降低。圖13顯示了該工況下的氣缸內當量比分布的3D-CFD分析結果。在常規的深凹坑燃燒室中,燃油不能擴散到圖左側的擠流區域。另一方面,新方案燃燒室中則能使燃油沿著斜坡擴散到該區域,因而能提高氣缸內空氣的利用率,并能降低煙度。因為它具有與低負荷下相同的減少冷卻損失的效果,所以指示比油耗下降了2%。因此,限制氣體流動速度也有助于減少高負荷下的傳熱系數。
圖12 新方案燃燒室的效果(2000r/min,IMEP 1000 kPa, EGR工作)
圖13 由STAR-CD計算而得的氣缸內當量比分布(轉速2000 r/min,IMEP1.0 MPa)
5 多缸發動機驗證效果
為了驗證新方案燃燒室在單缸發動機上取得的效果,用1臺4缸發動機在部分負荷和全負荷工況下評定了這種新方案燃燒室的性能,發動機的規格和結構布置分別如表1和圖3所示。該發動機在新歐洲行駛循環(NEDC)的8個部分負荷和3個全負荷工況點進行了試驗運行(圖14)。
圖15示出了在NEDC運行范圍內總污染物排放和燃油耗的結果。新方案燃燒室使燃油耗降低了2.5%,NOx排放減少了10%。圖16、圖17和圖18顯示了全負荷工況下的結果。在發動機低轉速區(1200 r/min),新方案使扭矩提高了1 N·m,燃油耗改善了3.7%。這是由于減少了未燃損失,以及冷卻損失而得以實現的。在中等轉速區域(2000 r/min)也同樣實現了扭矩增加1 N·m。不過,在發動機高轉速區(3600 r/min),由于噴射條件與傳統燃燒室的相同而使排氣溫度有所升高,因而輸出功率下降了0.7 kW。這是由于限制氣流速度而導致燃燒持續期延長的緣故。因此,在相同的條件下添加了時間間隔較短的后噴射,它能縮短燃燒持續時間,從而降低排氣溫度,減少排煙。其結果使新方案的功率比傳統燃燒室相比提高了大約1 kW。在常規燃燒室中,不能采用后噴射,因為它會導致較高的煙度排放。新方案燃燒室有后噴與常規燃燒室無后噴產生的差異原因是氣缸內燃油分布的差異(圖13)。在常規燃燒室中,燃燒凹坑中有很多燃油,因此后噴射燃油很容易干擾主噴射,而新方案燃燒室則將燃油散布整個氣缸內。
圖14 試驗運轉的工況點(8個部分負荷和3個全負荷工況點)
圖15 由8個穩態運轉工況點計算而得的NEDC的NOx排放和燃油消耗(車輛整備質量1360 kg)
圖16 新方案燃燒室的效果(轉速1200r/min,全負荷)
圖17 新方案燃燒室的效果(轉速2000r/min,全負荷)
圖18 新方案燃燒室的效果(轉速3600r/min,全負荷)
6 結語
此項研究的目的是減少小缸徑(缸徑73 mm)柴油機的冷卻損失和排氣煙度。試驗測量和3D-CFD分析研究后獲得以下結果:(1)擴大燃燒室的直徑以減少渦流和擠流,降低冷卻損失,并能降低燃油耗1%。然而,這樣做的后果是降低了氣體流速和限制了燃燒室內的混合氣擴散。特別是在高負荷下混合氣擴散會惡化,從而導致較高的煙度。(2)這種活塞頂部無唇口和有斜坡的燃燒室新方案,以及低壓縮比,可以通過限制氣流速度來減少冷卻損失,同時還能通過促進混合氣擴散來減少煙度排放。(3)這種新方案燃燒室已被引入1臺4缸柴油機。試驗表明,這臺發動機在整個NEDC運轉區域內,能使油耗降低2.5%,同時能使NOx排放減少10%。
-
機械
+關注
關注
8文章
1593瀏覽量
40643 -
壓縮
+關注
關注
2文章
102瀏覽量
19390 -
柴油機
+關注
關注
1文章
172瀏覽量
26293 -
燃燒
+關注
關注
0文章
11瀏覽量
12583
發布評論請先 登錄
相關推薦
渦輪增壓中冷柴油機在瞬態工況下的排氣煙度和燃燒特性
6105柴油機連桿及連桿螺栓遷都分析
柴油機預混合燃燒機理的研究
輕型車柴油機燃燒過程的仿真研究
柴油機噴油泵維護“十要”
柴油發電機組常見錯誤操作(二)
柴油發動機排氣管冒藍煙
柴油機噪聲可以分為哪幾種
柴油機預混合燃燒機理的研究
EGR溫度對渦輪增壓柴油機燃燒和排放的影響
船舶柴油機的燃料與燃油噴射與燃燒相關知識詳述
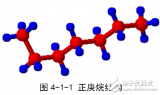
評論