減少內燃機的摩擦損失對于降低CO2排放具有重要意義。與轎車發動機不同,商用車發動機目前尚未具備與此密切相關的法規限值,因此未來對用于商用車行駛的CO2排放也應立法加以嚴格限制。正是出于該原因,Mahler公司已建立了一個用于測量商用車發動機運轉工況下的摩擦功率試驗臺。
1 低摩擦降低燃油耗
在轎車柴油機和汽油機上廣泛開展的參數研究已表明,活塞組具有顯著降低摩擦的潛力,因此具有相應的節油潛力。商用車發動機活塞組采取合適的措施也能降低摩擦,這同樣也會體現在燃油耗上,在商用車領域燃油耗對于終端用戶的購買意愿具有決定性的作用,因為燃油耗對于商用車的總運行成本(TCO)具有舉足輕重的意義。下文介紹試驗配置、查明試驗發動機的測試精度以及從廣泛的參數研究中所選擇的結果。
2 試驗配置
借助于測示功圖方法來確定摩擦損失,其中由平均指示壓力與平均有效壓力之差值得到平均摩擦壓力。測示功圖必須具有較高的測量精度,因此需要使用發動機機油、冷卻液和燃油的外部調節設備,此外不僅試驗臺空氣而且發動機進氣都需進行單獨處理。
試驗所用的發動機是一臺排量約13 L的6缸商用車增壓柴油機,其額定功率約為400 kW,扭矩2 500 N·m,冷卻液泵和機油泵由相應的外部設備取代,而燃油泵則仍由內燃機驅動,此外發動機采用一個可自由編程的電控單元運行,從而能實現對發動機的控制。
3 測量和評定方法
活塞組結構變化對發動機平均摩擦壓力的影響將在單參數研究框架中進行試驗。采用實驗設計(DoE)方法來確定平均摩擦壓力的特性曲線場,僅根據21個運行工況點就能建立起用于發動機整個運行范圍的平均摩擦壓力特性曲線場,每個方案采用DoE方法進行3次特性曲線場測量,一個方案的平均摩擦壓力特性曲線場由這三次測量的平均值得到,平均摩擦壓力可根據負荷、轉速和發動機溫度來表示。圖1示范性地示出了評定曲線,左側是兩個比較方案A和B的平均摩擦壓力特性曲線場。為了顯示出參數變化的影響,由這兩個平均摩擦壓力特性曲線場經計算形成數字差值,由此產生的平均摩擦壓力差值特性曲線場示于圖1右側。根據這樣的平均摩擦壓力差值特性曲線場就能得出關于整個運行范圍中平均摩擦壓力差值特性的結論,因而就能顯示出整個運行范圍中每個結構參數的影響。
圖1 平均摩擦壓力差值特性曲線場的形成:
兩個平均摩擦壓力特性曲線場以及由此
計算出的平均摩擦壓力差值特性曲線場
4 測量精度
測示功圖必須具有非常高的測量精度,以便能分辨出平均指示壓力與平均有效壓力之間極小的差異,因此在參數試驗準備階段要進行測量精度的系統試驗,這包括可重復性、可再現性和發動機裝配對可達到的測量精度的影響。
評估測量精度的第一步是評定可重復性,平均摩擦壓力特性曲線場中的21個運行工況點被用于對可重復性進行評判,將每個運行工況點的10個單次測量的平均摩擦壓力的標準偏差作為衡量可重復性的尺度。為此,運行工況點一旦已調節到穩定狀態,在發動機和邊界條件保持恒定不變的情況下即可直接連續進行10次測量,緊接著查明各個運行工況點平均摩擦壓力的標準偏差。從圖2中的藍色曲線可以看到,其是根據運行工況點的不同而變化的,平均摩擦壓力的可重復性平均為±0.0002 MPa。
第二步是評定測量的可再現性,為此同樣也應用平均摩擦壓力特性曲線場中的21個運行工況點來進行評判,將采用DoE方法進行3次特性曲線場測量的平均摩擦壓力的標準偏差作為衡量可再現性的尺度,在3個不同時間段分別進行測試,緊接著查明各個運行工況點的平均摩擦壓力pmr標準偏差,各個運行工況點標準偏差的差異同樣也示于圖2(紅色曲線),平均摩擦壓力的可再現性平均為±0.001 MPa。
圖2 平均摩擦壓力測量精度:可重復性、
可再現性和發動機裝配影響
考察測量精度的第三步是評定發動機裝配對平均摩擦壓力的影響。為此將經歷3次測量程序,也就是說發動機將完全分解2次,然后用相同的零部件再次裝配好。每個方案特性曲線場要進行3次,因此圖2中(綠色曲線)的標準偏差是以每個運行工況點的9次測量為基礎的,重復考察DoE程序的21個運行工況點,平均摩擦壓力的標準偏差平均為±0.002 MPa。該數值被稱為可信極限,并且必須在評價試驗結果時予以考慮。平均摩擦壓力差值的這種數值必須處于可信極限之外,以便使試驗結果能明確地歸咎于結構設計的變化,而對于處于可信極限之內的試驗結果則需進行附加性的評估,據此至少能得出符合發展趨勢的結論。
除了發動機裝配之外,燃油噴射和燃燒也會影響到平均摩擦壓力,但是在方案測量開始之前的大量試驗研究已使其產生的影響廣為人知。借助于可編程的發動機電控單元,保持表征運行工況點特征的相應參數恒定不變,從而使燃燒對平均摩擦壓力不產生影響。
5 試驗結果
在所進行的單參數試驗研究中,對活塞組眾多的結構設計參數進行了試驗。下文介紹活塞裝配間隙、活塞形狀以及連桿小頭中的活塞銷軸承和刮油環切向力等因素影響的試驗結果。除此之外,還試驗了活塞結構型式對發動機摩擦的影響。
在采用鋁活塞的轎車柴油機上,活塞裝配間隙的降低摩擦顯示出廣闊的應用潛力。仿照這些試驗,在商用車發動機上也試驗了4種不同的裝配間隙。在63 μm間隙(按在涂層上運行計)的基礎上再附加考察31 μm、85 μm和107 μm間隙的效果。圖3左圖中的平均摩擦壓力差值特性曲線場表明,與轎車發動機相比,最小與最大裝配間隙之間的差別較小,因此由此可得出結論:在采用鋼活塞的商用車發動機上活塞裝配間隙對發動機摩擦的影響減小了,而且顯然與負荷和轉速密切相關,其中一個原因可能是氣缸套和活塞的材料特性。試驗發動機具有濕式氣缸套的氣缸體,這就意味著帶有氣缸套的氣缸體曲軸箱與活塞具有相似的熱膨脹系數,因而甚至在全負荷條件下活塞裙部與氣缸壁之間也不會發生完全貼合,因此即使活塞在冷態時的裝配間隙較小,在具有熱機運轉間隙的情況下也不會出現摩擦方面的缺陷,在這種情況下更大的活塞裝配間隙并不會使摩擦進一步降低。
圖3在不同活塞裝配間隙(31~107 μm)
和發動機溫度100 ℃運行時測得的
平均摩擦壓力差值特性曲線場以及
活塞裝配間隙對平均摩擦壓力的影響
圖3右圖示出了活塞裝配間隙對平均摩擦壓力的影響。在熱機運轉時所試驗的活塞裝配間隙之間的平均摩擦壓力差值為0.004 MPa,該數值相對較小,但是能夠看到其與以往試驗的轎車發動機相似的發展趨勢:加大活塞裝配間隙直至某個尺度,按發展趨勢會導致摩擦降低,當然加大活塞裝配間隙超過該尺度后并不會使摩擦進一步降低,在個別情況下甚至會使摩擦又重新增加。
值得注意的是,活塞形狀會影響活塞裙部潤滑油膜的建立,因此應將傳統活塞廓線與所謂的駝峰廓線進行比較。從圖4可以看到這兩種活塞形狀的直接比對情況。設計的目標是要改善活塞裙部的潤滑并促進潤滑環境的建立。圖4中的平均摩擦壓力差值特性曲線場顯示出了傳統和新設計活塞形狀之間的差異,在整個運行特性曲線場中駝峰廓線方案在摩擦方面都顯示出其優勢,但是其與轉速并無明顯關系,而與負荷則密切相關,在高負荷時呈現出降低平均摩擦壓力的最大優勢,可降低0.009 MPa。
圖4 在以不同活塞形狀和發動機溫度100 ℃
運行時測得的平均摩擦壓力差值特性
曲線場(圖中DN=公稱直徑)
由活塞承受的所有力都將經過活塞銷繼續傳遞到連桿和氣缸壁面上。在轎車汽油機上的試驗已證實,連桿小頭中的活塞銷軸承在降低摩擦損失方面能起到重要作用。在現有的情況下已試驗過兩種不同的連桿小頭幾何形狀方案,將小頭具有橫向橢圓度的連桿與小頭具有機油槽的連桿進行比較。圖5中除了連桿小頭孔幾何形狀示意圖之外還示出了相應的平均摩擦壓力差值特性曲線場,其中機油槽比橫向橢圓度大數倍,機油槽方案在整個運行特性曲線場中呈現出較小的摩擦損失,而且無論是與負荷還是與轉速都無明顯的關系。與橫向橢圓度相比,機油槽改善了機油供應和連桿小頭軸承的潤滑,從而獲得了降低摩擦的優勢。
圖5 在以不同幾何形狀連桿小頭和
發動機溫度100 ℃運行時測得的
平均摩擦壓力差值特性曲線場
在歐Ⅵ發動機刮油環切向力水平已較低的基礎上進一步使其降低達50%。圖6中的平均摩擦壓力差值特性曲線場表明了初始狀態刮油環(Ft=34 N)與進一步降低切向力的刮油環(Ft=17 N)之間的差異。降低切向力的刮油環在整個運行特性曲線場中呈現出較小的摩擦特征,其中無法看出其與負荷或轉速存在明顯關系。
圖6 在以不同刮油環切向力和發動機溫度
運行時測得的平均摩擦壓力差值特性曲線場
試驗參數“活塞結構型式”可看成是多個單參數的組合。圖7示出了這兩種不同活塞的圖解比較。與迄今為止使用的Monoweld活塞相比,新設計的Monotile活塞的特點是具有較小的壓縮高度、稍小的活塞裙部表面和較輕的質量。
圖7 在以不同結構型式活塞發動機溫度
100℃運行時測得的平均摩擦壓力
差值特性曲線
從不同結構型式活塞的平均摩擦壓力差值特性曲線場中可以看出,與Monoweld活塞相比,Monotile活塞在整個運行特性曲線場中顯示出其降低摩擦的優勢。平均摩擦壓力差值特性曲線場與負荷無關,但是與轉速存在明顯的關系,在高轉速時呈現出最顯著的特征,最大的平均摩擦壓力差值可達到約0.007 MPa。
由于Monotile活塞的裙部表面稍小,在流體動力學方面獲得了降低摩擦的優勢。基于壓縮高度較小而使用了較長的連桿,這使得活塞裙部側壓力較小,也就降低了活塞裙部的摩擦。
6 結論
圖8示出了各種不同試驗參數在整個運行特性曲線場中各自平均摩擦壓力差值的最大值。顯然,活塞形狀和活塞裝配間隙呈現出對商用車而言較為重要的降低摩擦的潛力,活塞結構型式即其結構剛度也能有效降低發動機摩擦,而在這種考察方式中連桿小頭幾何形狀和刮油環切向力卻呈現出較小的降低摩擦的潛力,但是最終降低摩擦所獲得的節油效果是令人倍感欣慰的,因此借助于行駛循環模擬將在摩擦試驗臺上獲得的試驗結果換算成CO2或燃油耗值。此外,還要制定一種合適的汽車模型,采用3種不同的行駛循環及3種不同的負荷狀況用于計算,從而獲得關于CO2和燃油耗的單獨評價。
圖8整個運行特性曲線場中
的最大平均摩擦壓力差值
圖9示出了各種試驗參數相應的節油效果。與平均摩擦壓力的最大差值相比,這種在行駛循環中考察的節油效果排序發生了明顯的變動。在真實行駛運行中,活塞結構型式呈現出最優越的節油潛力,隨后依次才是刮油環切向力、活塞形狀和連桿小頭形狀,與所考察到的最大值相比活塞裝配間隙的作用明顯較小。節油效果排序不同的原因是其各自平均摩擦壓力差值特性曲線場的特性不同。
圖9 降低摩擦的節油效果及其
3種負荷狀況的平均值
在單參數研究的框架范圍內,未來還將對活塞組其他結構設計措施降低摩擦和燃油耗的潛力進行試驗研究。
-
發動機
+關注
關注
33文章
2517瀏覽量
70314 -
摩擦力
+關注
關注
0文章
9瀏覽量
7269
發布評論請先 登錄
相關推薦
發動機在線信號處理和工作過程控制
[原創]2011中東商用車展/迪拜商用車展/商用車零配件展/商用車
[原創]2011中東商用車展/迪拜商用車展/商用車零配件展/商用車
為生物質氣體燃料發動機開發測量控制系統方案
發動機智能電子控制——汽車車身網絡系統
2019第六屆上海國際商用車、專用車及零部件展覽會
2019第六屆上海國際商用車、專用車及零部件展覽會
模擬發動機的轉速信號設計方案
傳感器對發動機功況的影響
汽車發動機缸壓測試示波器測量
基于單片機的發動機振動速度、位移和加速度測量方法
對于Volkswagen公司商用車用歐6發動機性能分析
汽車發動機特性之汽油機的速度特性分析
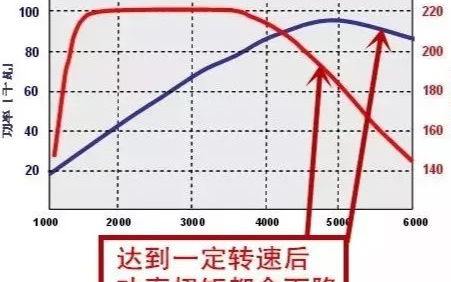
評論